the input transducer and the electrochemical output transducer as the direct response of the electronic switch
A sensor is a device which can quantitatively measure a certain physical quantity. A transducer is a device which converts one physical quantity to another from of physical quantity, e.g., acceleration to voltage or voltage to pressure. Therefore, a transducer can be a sensor when it is used to measure a certain physical quantity. But the transducer can also be an actuator when the (electrical) input is converted to, for example, force. So a transducer is more general than a sensor.
Since there are six different kinds of signals—mechanical, thermal, magnetic, electric, chemical and radiation (corpuscular and electromagnetic, including light)—any device converting signals of one kind to signals of a different kind is a transducer. The resulting signals can be of any useful physical form. Devices offering an electric output are called sensors. Most measurement systems use electric signals, and hence rely on sensors.
The distinction between input-transducer (physical signal/electric signal) and output-transducer (electric signal/display or actuation) is seldom used at present. Nowadays, input transducers are termed sensors, or detectors for radiation, and output transducers are termed actuators or effectors. Sensors are intended to acquire information. Actuators are designed mainly for power conversion.”
the development of a new category of motion sensors including linear and angular accelerometers and seismometers based on molecular electronic transducer (MET) technology. This technology utilizes a liquid not only as an inertial mass, but also as one of the main elements in the conversion of mechanical motion into electric current. The amplification process is similar to that in a vacuum triode. Therefore, it is possible to achieve signal amplification close to 108. Motion sensors demonstrating wide frequency and dynamic range and sensitivity that are one to two orders of magnitude better than MEMS devices of the same size have been developed. . Motion sensors, including accelerometers and gyroscopes, provide measurement of movement in at least six degrees of freedom. The simplest way to do motion sensing is with a solid-state mass-spring system, creating a damped simple harmonic oscillator. The movement of the solid-state proof mass can be measured with respect to displacement, velocity, or acceleration by suitable mechanical-electrical transducers. Efforts to miniaturize linear accelerometers and gyroscopes for inertial systems are mostly concentrated around Micro-Electro-Mechanical Systems (MEMS) technology. Similarly, in terms of design, fabrication, and readout, accelerometers and gyroscopes are the current leaders in commercially successful MEMS technology. Among a variety of transduction mechanisms underlying solid-state MEMS motion sensors, the most successful types are based on capacitive transduction due to the simplicity of the sensor element itself, no need for exotic materials, low power consumption, and good stability with respect to temperature. Although capacitive transducers have a characteristic nonlinear capacitance vs. displacement response, feedback is commonly used to convert the signal to a linear output. MEMS motion sensors in combination with other sensors, such as compass, pressure sensor, and GPS, have created a consumer electronics sensing package that works as the intelligent interface for users to interact with their electronics and, further on, with external environments, and have reasonable performance with low cost CMOS-compatible silicon microfabrication technology. However, in addition to high-volume consumer electronics markets requiring low-to-medium performance motion sensors, there are huge markets for high-performance motion sensing devices, with applications designed for military inertial navigation/guidance, high-resolution seismic sensing and high-g sensors. The key requirements for these high-performance applications include small size, wide bandwidth, low noise floor, low cross-axis sensitivity, low drift, wide dynamic range, high shock survivability, and low power consumption. There has been plenty of work done along the direction of scaling down the device size while maintaining low noise, high sensitivity and high resolution using MEMS techniques . However, the design and fabrication of these solid-state MEMS devices are complicated, which can result in low reliability, low reproducibility, and high cost. More importantly, they have yet to prove satisfactory for specific applications, especially in low frequency seismic sensing, because of the inherent limitation of the working mechanism of the solid-state mass-spring system. For some applications they also have limited successes due to their fragility to high shocks.
where the term “Molecular Electronic Transducer” was introduced to describe such a device The advantages of MET motion sensors include their small size, lack of fragile moving parts (thus high shock tolerance), high sensitivity and low noise especially at low frequencies, and independence of the response on installation angle.
As opposed to a solid inertial mass, a molecular electronic transducer (MET) is sensitive to the movement of a liquid electrolyte relative to fixed electrodes. METs are part of a third class of fundamental electronic devices, characterized by charge transfer via ions in solution—hence the name “Solion”. This is in contrast to solid-state electronics (charge transfer by electron/hole pairs in a solid conductor or semiconductor) and vacuum tubes (charge transfer by free electrons in an ionized gas or vaccum). Solion technology was first developed in the 1950s by US-Navy sponsored research. Early applications of Solion devices were for detection of low-frequency acoustic waves, either in the form of an infrasonic microphone or limited-band seismometer ,
XXX . XXX Output Transducers
A device which can convert information from one physical form to another.
Electrical systems are only able to respond to voltage and current signals in the electrical domain: amplitude, frequency, phase and time constant.
A transducer may generate an electrical signal by varying one of the following: voltage, current, resistance, capacitance, self-inductance, mutual inductance. The most fundamental transducers respond to temperature, electromagnetic radiation intensity, force, displacement or chemical concentration. If coupled to the time domain these devices can be used to measure any physical or chemical quantity.The output transducer transfers signals out of the electrical domain and into the domain that can be perceived by one of the five human senses. A substantial amount of power is usually required to transfer information out of the electrical domain.
An output transducer can:
- Produce sound with a speaker or buzzer.
- Produce light with LED or lamp.
- Produce movement with an electric motor or a solenoid.
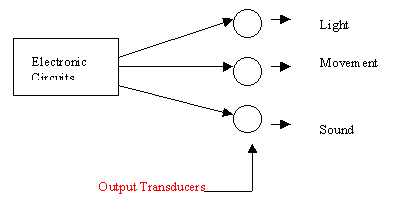
- Types of Output Transducers
- Produce "information"
e.g. meter, oscilloscope à "Low" Power < 1W - Produce "Action"
e.g. valves à "High" Power > 1W
- Produce "information"
- Controlling Power
- Types of Loads
- Resistive- e.g. heater, light bulbs
- Inductive (& probably resistive as well)- e.g. solenoids, motors.
- have to worry about back EMFs.
- Types of Control
- ON/ OFF
- Proportional
- Trade offs
Consider:
For proportional control, need to be able to dissipate as much power in control as in load! Therefore, not efficient.
Can turn ON/OFF quickly to approximate proportional. This can produce noise, especially with inductive loads. - Devices for control
- Relay:
- can be DC or AC, relatively slow, high current
- need diode across coil - Solid State Relay:
- uses logic levels in, convenient usually DC only, faster, < 1 - Power BJT:
- DC, fast
- need base resistor
- Beta (DC) gives possible gain typical Beta approximately 100
- Darlington transistors: typical Beta approximately 10000 - Power MosFET:
- DC, fast: You can put current through one way
- E Type: enhancement mode only
Vgs > Vth to switch "on" (Io > 0)
- D Type: depletion mode (& also enhancement)
Vgs < Voff to turn off (Io = 0)
- Voltage devices: need very little gate current. - SCR (1 way) or TRIAC (2 way :2 SCR's back to back)
- switching AC
- turn on when a gate pulse is received
- turn off when current = 0
- 2 ways to operate:- Burst Mode - turn "on" for n out of m cycles. Slower e.g. heater
- Delay & Trigger Mode - noisy e.g. light
- Solid state switch is a slightly modified SCR
- Rules for Control
- isolate - Actuators
- solenoid: usually "pull" type
- stepper mode
Current Device: current going in the base matters
- Types of Loads
Burst mode - turn on at zero crossing, slow rate but smooth, used for electric heaters
Delayed Trigger - turn on during cycle, fast rate and starts up high at instant turn on, used for lights
Application of power-control circuit
Switching circuits
Circuits designed to respond to nonlinear waveforms, such as square waves are referred to as switching circuits. These switches are commonly used as drivers in switching applications. A driver is a circuit used to couple a low-current circuit output to a relatively high current device, such as an LED.
The BJT as a Switch
A bipolar junction transistor (BJT) is a current-controlled device, the base current controls the amount of collector current. It can be used as a switch by driving the component back and forth between saturation and cutoff. A basic transistor switching circuit is shown in figure (a). The way this is accomplished is easy to see if you refer to the dc load line shown in figure (b).
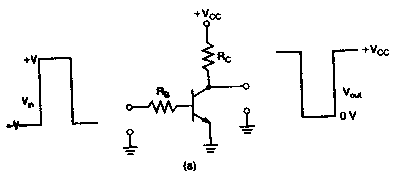
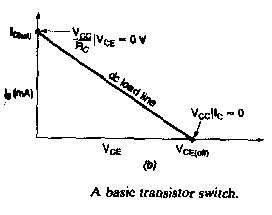
when the input to the transistor is –V, the emitter-base junction of the transistor is biased off. When the transistor is biased off, the following condition exist:
Vce =Vcc (ideal) and Ic =0 (ideal)
As figure 2 (a) shows, these conditions are the same as those caused by an open switch.
When the input to the transistor is at +V, the transistor will saturate. This assumes, of course, that the input current is sufficient to cause saturation. When the transistor saturates, the following condition exists:
Vce=0V(ideal) and Ic=Vcc/Rc (ideal)
As Figure 2 (b) shows, these conditions are the same as those caused by a closed switch.
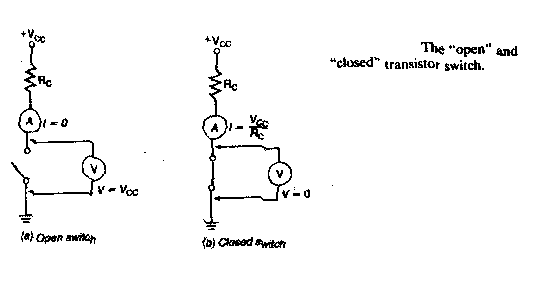
The high input voltage, +Vin must ensure that the transistor saturates, In a practical transistor switch , this is accomplished by two thing:
- + Vin is usually equal to +Vcc
- Rb is made small enough so that the calculated value of Ib>>Ic
Vin=IbRb+Vbe
For practical output values for a BJT switch, the output will never actually be 0V
The JEFT as a switch
The junction field effect transistor(JEFT) is a type of FET(a voltage-controlled device in which the voltage terminal controls the amount of current through the device) that operate reverse-biased junction to control current in a channel.
The basic JEFT switch differs from the BJT switch in several aspects:
- The JEFT switch has a much higher input impedance
- A negative input square wave to an n-channel is used to produce a positive output pulse.
Certain calculation or signal-processing chores can be performed in the machine and then used to control external circuits. The simplest forms of external are on-off switches that are controlled by a single bit of a computer output port. More complex control applications use devices such as a amplifiers, DACs, and so forth.
Fig1-1 shows connecting the relay to the computer. Control over the relay is maintained by using 1 bit of the computer output port, in this case B0. Since only one bit is used, the other 7 bits are available for other applications, which may be displays, other relays, or certain other devices.
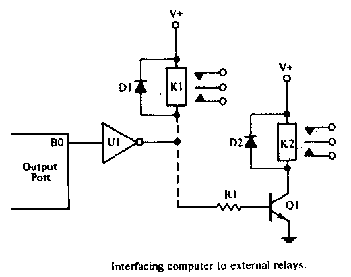
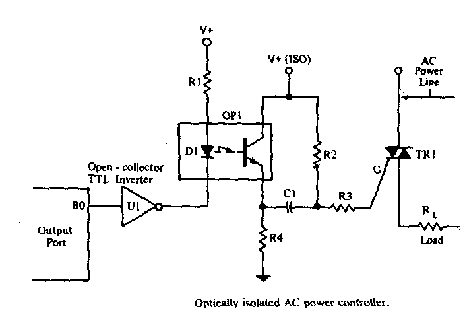
for interfacing the microcomputer with display devices as an oscilloscope or a strip chart paper record is shown in Fig 1-2. There are instances when these devices are the most appropriate means display, so we will want to provide some means to convert binary data analog voltages for the oscilloscope or recorder.
Simple Application
Model
Taking into the audio scene, for a speaker, we have the input energy to be electrical, the loudspeaker as the transducer, which has the output energy of sound.
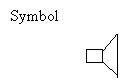
As stated from above, a loudspeaker is a transducer that converts electrical energy from an audio amplifier into mechanical vibrations of the air. That is it produces sound. This device is sometimes known as a dynamic loudspeaker or simply a speaker. The basic construction of a speaker is shown below.
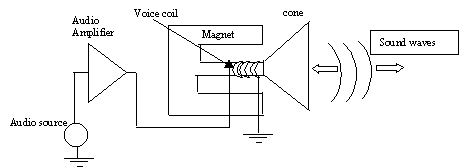
When electrical energy at audio frequencies, is applied to the voice coil, the magnetic field developed as a result, drives the cone in sympathy with the audio waveform.
The movement of the cone, backwards and forwards, produces a sound wave of which is a replica of the original electrical signal.
Loudspeakers have many uses including radios, sound systems and alarms.
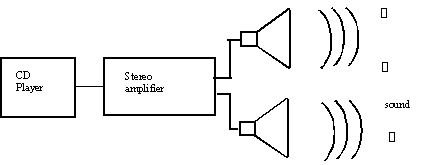
Types of transducer
- Electrochemical Transducers
Molecular electric transducers
Fuel cell
Battery
- Electroacoustic
Microphone
Hydrophone
3.Elctromagnetic
Magnetic cartridge
Generator
4.Electrostatic
Electrometer
5.Electromechanical transducer
Generator
Motor
Strain Gauge
Galvanometer
6.Other types of transducer
Photoelectric - light energy to electrical energy or vice versa
Thermoelectric - heat energy to electrical energy or vice versa
Industrial and municipal wastewater must be treated to the specified standards before discharged into a sewer or watercourse. These standards are determined not only to protect the sewerage infrastructure and workers maintaining the sewerage system, but also to prevent adverse effects on treatment processes at the downstream sewage treatment works and protect aquatic life. As water pollution acts become more and more strict, it is important to monitor multiple parameters of effluent conveniently during the treatment and before discharge. Therefore, it is necessary to develop an instrument to measure these parameters conveniently and efficiently.
Current available instrumentations are capable of measuring pH value of aqueous solutions, oxidation/reduction potential (ORP), free ion concentrations of some anions and metallic ions, conductivity, the concentration of dissolved oxygen (DO) and temperature. However, only a common instrument can measure some of these parameters among the standards of environmental pollution control acts at present. It is inconvenient to measure all parameters of effluent by many separate instruments, and hence it is important to develop one integrated instrument for more parameters. Many electrochemical measurements are affected by environmental temperature, and the results should be corrected to compensate the effect of temperature after measurement. In fact, some of electrochemical sensors have temperature compensation functions and they are duplicated if the functions are integrated instrument for more parameters. In addition, most of conventional electrochemical instruments are composed of the same components, such as liquid crystal display (LCD), keypad, and digital output port. It is necessary to integrate these similar or same functional parts into a system and save the cost.
We designed and fabricated an integrated transducer to determine multiple parameters, which include pH, oxidation/reduction potential, temperature, conductivity, dissolved oxygen, the concentrations of some of anions and metallic ions. The transducer is composed of multiple input ports for standard commercial sensors, microprocessor for energetic data treatment, liquid crystal display for easily operation and directly result representation, keypad for input and digital output port for communication with personal computer. The transducer provides powerful functions, including flexible calibration strategy, optimized display mode, intelligent internal compensation, and wide measurement range.
Fig below illustrates the front of an integrated transducer 1 for environmental multi-parameter monitoring according to one embodiment of the present invention. The case 2 of the transducer covers the exterior of the meter except for a panel containing the keypad 3, liquid crystal display 23, a series of jacks for standard commercial probes and the accessories. The keypad includes sixteen keys, eleven of which are number keys, and others are function keys. The transducer has eight jacks (4 to 11) for pH, ORP and ion selective electrodes, and three jacks (12 to 14) for temperature probes, and one jack 15 for DO electrode through the top of the case. The transducer has one jack 16 for conductivity electrode, and three jacks (17 to 19) for the working, reference and counter electrodes of anodic stripping voltammetry (ASV) for the monitoring of metallic ions such as some of heavy metals through the right side of the case. The transducer has a digital output port 20 to communicate with the computer under the protocol of RS232 in the right side of the case, and an on/off button 21 to switch on and off the power of the transducer in the front panel of the case, and a contrast knob 22 to adjust the display contrast of the LCD in the front panel of the case.

Schematic diagram of the integrated transducer
Fig.below is a schematic diagram of the functional components of the transducer. The pH or ORP or ion selective electrodes (ISE) are connected via the jacks (4 to 11) to the transducer. The analog voltage input 24 (actually 8 channels) of pH or ORP or ISE is connected to an analog amplifier circuit 25 to a strobing circuit 55. The temperature probe is connected via the jacks (12 to 14) to the transducer. The analog input 27 (actually 3 channels) of temperature probe is connected to an analog amplifier circuit 28 to a strobing circuit 55. The DO electrode is connected via the jack 15 to the transducer. The analog current input 32, which is produced by DO electrode under the polarizing voltage signal 31 of the polarizing voltage circuit 30, is connected to current to voltage circuit 33 to convert to voltage signal 34, and then the voltage signal 34 is connected to an analog amplifier circuit 35 to a strobing circuit 55. The conductivity electrode is connected via the jack 16 to the transducer. The analog current input 39, which is produced by conductivity electrode under the alternating voltage 38 of the oscillation generator circuit 37, is connected to current to voltage circuit 40 to convert to voltage signal 41, and then the voltage signal 41 is connected to an analog amplifier circuit 44 to the strobing circuit 55. The amplification gain of analog amplifier circuit 44 is controlled by the signal 43 of the controllable gain 42, which receives control signal 61 from the microprocessor 59. The working electrode, reference electrode and counter electrode of ASV to measure the concentration of metallic ions are connected via the jacks (17 to 19) to the transducer. The analog current input 48, which is produced by the electrodes under the deposition and stripping voltage 47 of the circuit 46, is connected to current to voltage circuit 49 to convert to voltage signal 50, and then the voltage signal 50 is connected to an analog amplifier circuit 53 to the strobing circuit 55.The deposition and stripping voltage circuit 46 receive control signal 63 from the microprocessor 59. The amplification gain of analog amplifier circuit 53 can be controlled by the signal 52 of the controllable gain 51, which receives control signal 62 from the microprocessor 59.
The voltage inputs (26, 29, 36, 45 and 54) connected to the strobing circuit 55, are transferred to A/D converter 57, which converts analog input 56 into a digital signal 58 one by one in proper order. The digital signal 58 is an input into microprocessor 59, contained on a circuit board within the case 2 of the transducer 1. Keypad input 66 represents the connection of the various keys of keypad 3 to the microprocessor 59. Output 65 from microprocessor 59 to display 23 is representative of various control lines that connect microprocessor 59 to the individual liquid crystal display elements of the components of display 23. Output 64 from microprocessor 59 is representative of various control lines that connect microprocessor 59 to the serial communication port of the computer under the communication protocol RS232.
Fig below illustrates in schematic form of the microprocessor 59, its major logic elements and the connecting elements. The two types of inputs to the microprocessor 59 are the digitized input 58 (shown as coming from A/D Converter 57 in Fig. 2) and the keypad input 66 (shown as coming from keypad 3 in Fig. 2). The five types of outputs from the microprocessor 59 are the display outputs 65 to LCD 23, the serial digital output 64 to RS232 serial communication port 20, the channel selector output 60 which controls the strobing circuit 55 to determines whether A/D Converter 57 is connected to pH/ORP/ISE jacks (4 to 11) or to temperature jacks (12 to 14) or to DO jack (15) or to conductivity jack 16 or to heavy metal jacks (17 to 19), the gain select outputs (61 and 62) which control the gains of the amplifiers (44 and 53), and the deposition and stripping voltage output 63 which control the deposition and stripping voltage 46 of anodic stripping voltammetry.

Schematic form of the microprocessor 59
The two types of inputs and five types of outputs connect through the I/O interface 67 to the arithmetic logic unit (ALU) 71 of microprocessor 59. Additional inputs to ALU 71 are timer circuits 70 used for indicating increments at which ALU performs certain functions. The microprocessor 59 also contains read only memory (ROM) 69 in which various program routines and constants are permanently stored and called up by ALU in a controlled fashion. Random access memory (RAM) 68 contains various values obtained by ALU 71 from I/O 67 or from computations on those values, on stored values already in RAM 68, on values from ROM 69 or on values from a variety of sources.
The integrated electrochemical transducer can measure the multiple parameters of the solution, such as pH, ORP, temperature, conductivity, DO, concentration of some anions and metallic ions. When the transducer is turned on, all the parameters will display in the LCD, and the operator press the key to select the parameters to be measured.


The front view and reae view of the integrated
transducer integrated with power supply and accessories
Tidak ada komentar:
Posting Komentar