TRANSDUCER I / O AND O / I
A transducer is a device that converts one form of energy or disturbance into another. In electronics, transducers convert alternating or direct electric current into sound, light, heat, radio waves, or other forms. Transducers also convert sound, light, heat, radio waves, or other energy forms into alternating or direct electric current.
Common examples of electrical and electronic transducers include buzzers, speakers, microphones, piezoelectric crystals, light-emitting and infrared-emitting diodes, photocells, radio antennas, and many other devices.
the input transducer is called the sensor and also the output transducer called the actuator in the science of robotic electronics is indispensable transducer as a suply energy for the robot in order to work in a multi-dimensional environment both earth and divergent convergent environments .
transducers that work robotically should work efficiently and effectively to program the input transducers and transducers out in a state of program signal calm but not the threshold time .
einstein's relativity review which says that the earth always revolves on its axis but we on earth do not feel it but if we are in the movement of light then we will feel that the earth rotates on its axis so energy collaborate with other energy into an energy needed by future robots to follow the logic of work einstein is still valid in the pockets of a triple paved vacuum LJBUSAF XI XA PIN PING HUNG .
"What is a robot?"
ROBOT is a Machine Which can SENSE, PLAN, ACT
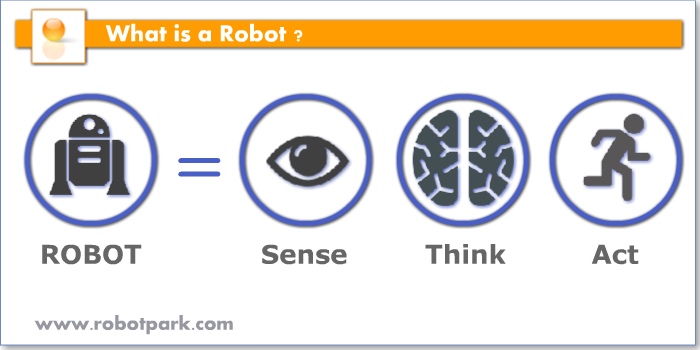
What is a Robot
As far as the exact definition of a robot is concerned, you’d be hard pressed to find one that is widely accepted. You see, not every machine that you come across could be called a Robot. My iPhone, albeit it’s amazing, is in no way a robot. The same could be said about the Laptops, Vacuum cleaners, Washing machines, you name it. For a machine to fall in the category of robots,and to be the answer of "What is a Robot?" question, it should have following features in its repertoire.
1) SENSE
Robots should be able to sense to interact with their environment, Robots use different kinds of sensors. These could be light sensors, temperature sensors, pressure sensors, proximity sensors, and distance sensors. The last thing you want for a robot is to repeatedly crash into the furniture.The sensors of a robot are the main units that avoid it crashing the furniture in that sense.
2) PLAN
Robots are supposed to show some kind of intelligence, like solving complex problems, having social interactions or the ability to learn virtually anything. They accomplish all of this through Artificial Intelligence. Artificial intelligence allows a robot to assess its status and generate a plan according to this assessment to act. If your machine lacks significant AI, it probably isn’t a robot.
3) ACT
For a robot to interact with its environment, they should act besides sensing. Acting has a wide meaning when it is for robots and it can be seen in different forms. Acting is not just moving around for a robot. For a robot acting is the ability to manipulate its environment in any way. Acting is not just a robot's changing its position or manipulation of an object, it is also changing the temperature or humidity of a room.
What is a ROBOT, What is NOT
There is no one simple definition of what is a robot. There are lots of different kinds of machines, some of them is called a robot, some of them not. Joseph Engelberger, once remarked: "I can't define a robot, but I know one when I see one."

The line between Robots and machines sometimes is not clear. If a machine can control its arms or other parts of its body, and especially if it is anthropomorphic or zoomorphic (like a Humanoid), it would be called a robot. Lets check some examples:
-a Cnc Machine is very occasionally called as a robot, but an industrial arm is always characterized as a robot.
-An Autonomous Wheeled or Tracked thing, such as (Dagu Rower 5) , is nearly always named as a robot.
-A Computer Controller Car, like Google Car, can be named as a robot as it can sense,think and act.
On the other hand, only being anthropomorphic is not enough for something to be called a robot. A robot has to Sense,Think and Act. A human body shaped mechanical object would not be a robot. So we can say the physical appearance of a machine is not enough to name it as a robot.
What is Robotics
After the definition “robot”, the next term should be “robotics”. Robotics is the science and study of designing, building and utilizing robots. So, if you’re planning to build an automata from scratch or you’re using a ready-made robot, you’re essentially working in the field of robotics. And these are exciting times to be in this field where lots of intriguing discoveries are being made and tons of new information is being contributed to human knowledge.
The word Robotics, used to describe this field of study, was coined by the science fiction writer Isaac Asimov. He defined the "Three Laws of Robotics" which is mentioned in a movie called iRobot.
All Types Of Robots - By Locomotion
What are Types of Robots? Here are the types of robots by locomotion systems. We will examine these types in detail. Please Click on the image for a larger picture.
1.Stationary Robots
Stationary robots are robots those work without chaning their positions. Referring the robot as “stationary” does not mean that the robot actually is not moving. What “stationary” means is the base of the robot does not move during operation.
These kind of robots generally manipulate their environment by controlling the position and orientation of an end-effector. Stationary robot category includes robotic arms, catesian robots, cylinderical robots, spherical robots, SCARA robots and parallel robots.
1.1 Cartesian/Gantry Robots
1.2 Cylindrical Robots
1.3 Spherical Robots
1.4 SCARA Robots
1.5 Robotic Arms - (Articulated Robots )
1.6 Parallel Robots
2.Wheleed Robots
Wheeled robots are robots which change their positions with the help of their wheels. Wheeled motion for a robot can be achieved easily in mechanical terms and its cost is pretty low. Additionally control of wheeled movement is generally easier.
These reasons make wheeled robots one of the most frequently seen robots. Single wheeled robots, mobile ball robots, two-wheeled robots, three-wheeled robots, four-wheeled robots, multi-wheeled robots and tracked robots are examples of wheeled robots.
2.1 Single Wheel (Ball) Robots
2.2 Two-Wheeled Robots
2.3 Three Wheeled Robots
2.4.Four Wheeled Robots
2.5.Multi Wheeled Robots
2.6.Tracked Robots
3. Legged Robots
Legged robots are mobile robots, similar to wheeled robots, but their locomotion methods are more sophisticated and complicated compared to their wheeled counterparts. As their name suggests they use their legs to control their locomotion and they perform much better than wheeled robots on uneven terrain.
Despite the cost and complexity of production is high for these robots their advantages on uneven terrain makes these robots indispensable for most applications. One-legged robots, two-legged robots, three-legged robots, four-legged robots, six-legged robots and multi-legged robots are examples of this robot class.
3.1.One Legged Robots
3.2.Two Legged – Bipedal Robots (Humanoids)
3.3.Three Legged – Tripedal Robots
3.4.Four Legged – Quadrupedal Robots
3.5.Six Legged Robots (6 Legged Hexapod)
3.6 Robots With Many Legs
4.Swimming Robots – Robot Fish
Swimming robots are robots which move underwater. These robots are generally inspired by fish and they use their fin-like actuators to maneuver in water.
5.Flying Robots
Flying robots are robots that float and maneuver on air using their plane-like or bird/insect-like wings, propellers or balloons. Examples of these robots are airplane robots, bird/insect inspired wing flapping robots, proppeller based multicopters and balloon roobots.
6.Rolling Robotic Balls (Mobile Spherical Robots)
7.Swarm Robots
Swarm robots are robotic systems which consist of multiple small robots. These robots structurally does not create a single united robot, but operates as their robot modules operate cooperatively. Although similar to modular robotic systems, elements of swarm robots have much less functionality and herd configurations does not create new robots.
8.Modular Robots
Similar to swarm robots, modular robotic systems also have multiple robots in their configurations. Modules of these systems are more functional compared to a robotic herd. For example a single module of a modular robotic system can have self-mobility and it can operate alone. The power of modular robotics comes from its versatility in its configurations. Modules of a modular robotic system can create very different configurations and the robots created this way can have very distinct abilities.
9.Micro Robots
By definiton micro robots term is used to specify both robots that have dimensions on micrometer scale and robots that can operate on micrometer resolution. Therefore both possibly very big stationary robots that can manipulate their environment on a micrometer scale and small robots that are actually measured by micrometers are called micro motors.
10.Nano Robots
Similar to micro robots nano robots also defined a bit vaguely. The term nano robot both defines very small robots which have nano meter scaled dimensions and robots those can manipulate their environment with a nano meter scale resolution regardless of their actual sizes.
11.Soft Elastic Robots
Soft/elastic robots, are new introductions to robotics. These robots are generally bio-inspired. Most applications are inspired from squids or inchworms both structurally and functionally.
13.Snake Robots
14.Crawler Robots
15.Hybrid Robots
CARTESIAN and GANTRY Robots
A cartesian coordinate robot (also called linear robot) is an industrial robot whose three principal axes of control are linear (i.e. they move in a straight line rather than rotate) and are at right angles to each other.The three sliding joints correspond to moving the wrist up-down,in-out,back-forth. Among other advantages, this mechanical arrangement simplifies the Robot control arm solution.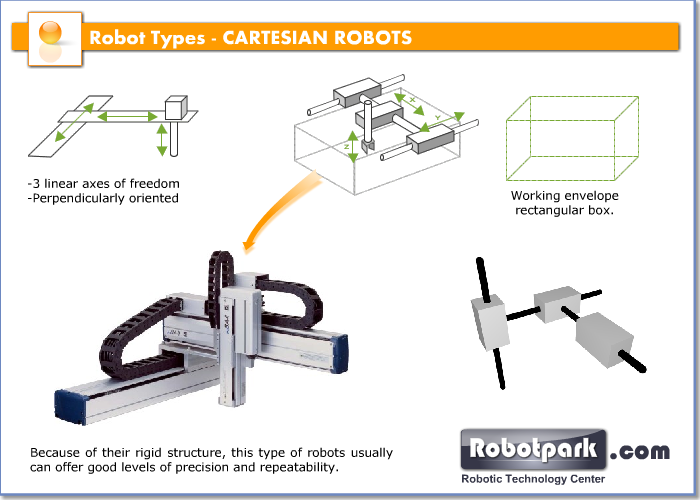
Cartesian coordinate robots with the horizontal member supported at both ends are sometimes called Gantry Robots. They are often quite large.

A popular application for this type of robot is a computer numerical control machine (CNC machine). The simplest application is used in milling and drawing machines where a pen or router translates across an x-y plane while a tool is raised and lowered onto a surface to create a precise design.
SPHERICAL ROBOTS
Spherical Coordinate RobotsA spherical robot is a robot with two rotary joints and one prismatic joint; in other words, two rotary axes and one linear axis. Spherical robots have an arm which forms a spherical coordinate system.
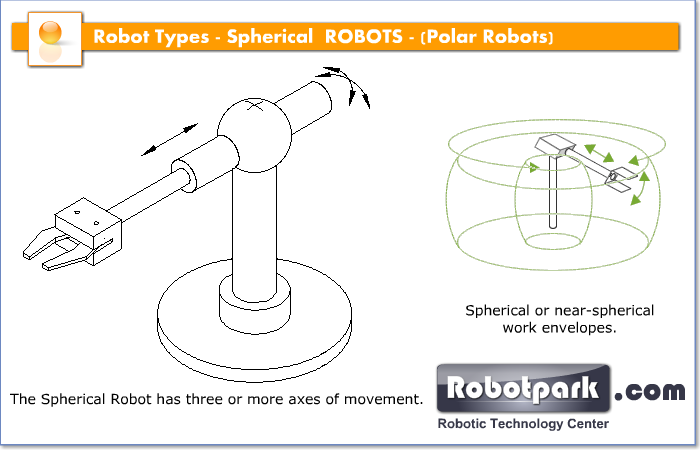
Spherical Coordinate System:
In mathematics, a spherical coordinate system is a coordinate system for three-dimensional space where the position of a point is specified by three numbers: the radial distance of that point from a fixed origin, its polar angle measured from a fixed zenith direction, and the azimuth angle of its orthogonal projection on a reference plane that passes through the origin and is orthogonal to the zenith, measured from a fixed reference direction on that plane.
The radial distance is also called the radius or radial coordinate. The polar angle may be called colatitude, zenith angle, normal angle, or inclination angle.
SCARA ROBOTS
The SCARA acronym stands for Selective Compliant Assembly Robot Armor Selective Compliant Articulated Robot Arm.
In 1981, Sankyo Seiki, Pentel and NEC presented a completely new concept for assembly robots. The robot was developed under the guidance of Hiroshi Makino, a professor at the University of Yamanashi. The robot was called Selective Compliance Assembly Robot Arm, SCARA. Its arm was rigid in the Z-axis and pliable in the XY-axes, which allowed it to adapt to holes in the XY-axes.

By virtue of the SCARA’s parallel-axis joint layout, the arm is slightly compliant in the X-Y direction but rigid in the ‘Z’ direction, hence the term: Selective Compliant. This is advantageous for many types of assembly operations, i.e., inserting a round pin in a round hole without binding.
The second attribute of the SCARA is the jointed two-link arm layout similar to our human arms, hence the often-used term, Articulated. This feature allows the arm to extend into confined areas and then retract or “fold up” out of the way. This is advantageous for transferring parts from one cell to another or for loading/ unloading process stations that are enclosed.
SCARA’s are generally faster and cleaner than comparable Cartesian robot systems. Their single pedestal mount requires a small footprint and provides an easy, unhindered form of mounting. On the other hand, SCARA’s can be more expensive than comparable Cartesian systems and the controlling software requires inverse kinematics for linear interpolated moves. This software typically comes with the SCARA though and is usually transparent to the end-
Robotic Arms – Articulated Robots
An articulated robot is a robot with rotary joints (e.g. a legged robot or an industrial robot). Articulated robots can range from simple two-jointed structures to systems with 10 or more interacting joints. They are powered by a variety of means, including electric motors.
Some types of robots, such as robotic arms, can be articulated or non-articulated.
Terms & Definitions of Robotic Arms
Articulated Robot: An articulated robot is one which uses rotary joints to access its work space. Usually the joints are arranged in a “chain”, so that one joint supports another further in the chain.Continuous Path: A control scheme whereby the inputs or commands specify every point along a desired path of motion. The path is controlled by the coordinated motion of the manipulator joints.
Degrees Of Freedom (DOF): The number of independent motions in which the end effector can move, defined by the number of axes of motion of the manipulator.
Gripper: A device for grasping or holding, attached to the free end of the last manipulator link; also called the robot’s hand or end-effector.
Payload: The maximum payload is the amount of weight carried by the robot manipulator at reduced speed while maintaining rated precision. Nominal payload is measured at maximum speed while maintaining rated precision. These ratings are highly dependent on the size and shape of the payload.
Pick And Place Cycle: Pick and place Cycle is the time, in seconds, to execute the following motion sequence:
Step 1: Move down one inch,
Step 2: grasp a rated payload;
Step 3: move up one inch;
Step 4: move across twelve inches;
Step 5: move down one inch;
Step 6: ungrasp; move up one inch;
Step7: and return to start location.
Reach: The maximum horizontal distance from the center of the robot base to the end of its wrist.
Accuracy: The difference between the point that a robot is trying to achieve and the actual resultant position. Absolute accuracy is the difference between a point instructed by the robot control system and the point actually achieved by the manipulator arm, while repeatability is the cycle-to-cycle variation of the manipulator arm when aimed at the same point.
Repeatability: The ability of a system or mechanism to repeat the same motion or achieve the same points when presented with the same control signals. The cycle-to-cycle error of a system when trying to perform a specific task
Resolution: The smallest increment of motion or distance that can be detected or controlled by the control system of a mechanism. The resolution of any joint is a function of encoder pulses per revolution and drive ratio, and dependent on the distance between the tool center point and the joint axis.
Robot Program: A robot communication program for personal computers. Provides terminal emulation and utility functions. This program can record all of the user memory, and some of the system memory to disk files.
Maximum Speed: The compounded maximum speed of the tip of a robot moving at full extension with all joints moving simultaneously in complimentary directions. This speed is the theoretical maximum and should under no circumstances be used to estimate cycle time for a particular application. A better measure of real world speed is the standard twelve inch pick and place cycle time. For critical applications, the best indicator of achievable cycle time is a physical simulation.
Servo Controlled: Controlled by a driving signal which is determined by the error between the mechanism’s present position and the desired output position.
Via Point: A point through which the robot’s tool should pass without stopping; via points are programmed in order to move beyond obstacles or to bring the arm into a lower inertia posture for part of the motion.
Work Envelope: A three-dimensional shape that defines the boundaries that the robot manipulator can reach; also known as reach envelope.
PARALLEL ROBOTS
A parallel manipulator is a mechanical system that uses several computer-controlled serial chains to support a single platform, or end-effector. Perhaps, the best known parallel manipulator is formed from six linear actuators that support a movable base for devices such as flight simulators.
Also known as parallel robots, these systems are articulated robots that use similar mechanisms for the movement of either the robot on its base, or one or more manipulator arms. Their ‘parallel’ distinction, as opposed to a serial manipulator, is that the end effector (or ‘hand’) of this linkage (or ‘arm’) is connected to its base by a number of (usually three or six) separate and independent linkages working in parallel. ‘Parallel’ is used here in the topological sense, rather than the geometrical; these linkages act together, but it is not implied that they are aligned as parallel lines.
‘Parallel” is used here in the topological sense, rather than the geometrical; these linkages act together, but it is not implied that they are aligned as parallel lines.
Design features
A parallel manipulator is designed so that each chain is usually short, simple and can thus be rigid against unwanted movement, compared to a serial manipulator. Errors in one chain’s positioning are averaged in conjunction with the others, rather than being cumulative. Each actuator must still move within its own degree of freedom, as for a serial robot; however in the parallel robot the off-axis flexibility of a joint is also constrained by the effect of the other chains. It is this closed-loop stiffness that makes the overall parallel manipulator stiff relative to its components, unlike the serial chain that becomes progressively less rigid with more components.This mutual stiffening also permits simple construction: Stewart platform hexapods chains use prismatic joint linear actuators between any-axis universal
This mutual stiffening also permits simple construction: Stewart platform hexapods chains use prismatic joint linear actuators between any-axis universal ball joints. The ball joints are passive: simply free to move, without actuators or brakes; their position is constrained solely by the other chains. Delta robots have base-mounted rotary actuators that move a light, stiff, parallelogram arm. The effector is mounted between the tips of three of these arms and again, it may be mounted with simple ball-joints. Static representation of a parallel robot is often akin to that of a pin-jointed truss: the links and their actuators feel only tension or compression, without any bending or torque, which again reduces the effects of any flexibility to off-axis forces.
A further advantage of the parallel manipulator is that the heavy actuators may often be centrally mounted on a single base platform, the movement of the arm taking place through struts and joints alone. This reduction in mass along the arm permits a lighter arm construction, thus lighter actuators and faster movements. This centralisation of mass also reduces the robot’s overall moment of inertia, which may be an advantage for a mobile or walking robot.
All these features result in manipulators with a wide range of motion capability. As their speed of action is often constrained by their rigidity rather than sheer power, they can be fast-acting, in comparison to serial manipulators.
Comparison to Serial Manipulators
Most robot applications require rigidity. Serial robots may achieve this by using high-quality rotary joints that permit movement in one axis but are rigid against movement outside this. Any joint permitting movement must also have this movement under deliberate control by an actuator. A movement requiring several axes thus requires a number of such joints. Unwanted flexibility or sloppiness in one joint causes a similar sloppiness in the arm: there is no opportunity to brace one joint’s movement against another. Their inevitable hysteresis and off-axis flexibility accumulates along the arm’s kinematic chain; a precision arm is a compromise between precision, complexity and cost of these joints.
A major drawback of parallel manipulators, in comparison to serial manipulators, is their limited workspace, because the legs can collide and, in addition (for the hexapod) each leg has five passive joints that each have their own mechanical limits. Another drawback of parallel robots is that they lose stiffness in singular positions completely (The robot gains finite or infinite degrees of freedom which are uncontrolable; it becomes shaky or mobile). This means that the Jacobian matrix, which is the mapping from joint space to Euclidian space, becomes singular (the rank decreases from six).
Applications
Major industrial applications of these devices are:
-Flight Simulators
-Automobile Simulators
-in work processes
-Photonics / Optical Fiber Alignment
They also become more popular:
-in high speed, high-accuracy positioning with limited workspace, such as in assembly of PCBs
-as micro manipulators mounted on the end effector of larger but slower serial manipulators
-as high speed/high-precision milling machines
Parallel robots are usually more limited in the workspace; for instance, they generally cannot reach around obstacles. The calculations involved in performing a desired manipulation (forward kinematics) are also usually more difficult and can lead to multiple solutions.
SINGLE WHEEL (Ball) Robots
One wheeled robots are extremely difficult to keep balanced due to the single point of contact with the ground.Multi-wheel statically-stable mobile robots tall enough to interact meaningfully with people must have low centers of gravity, wide bases of support, and low accelerations to avoid tipping over. These conditions resent a number of performance limitations.
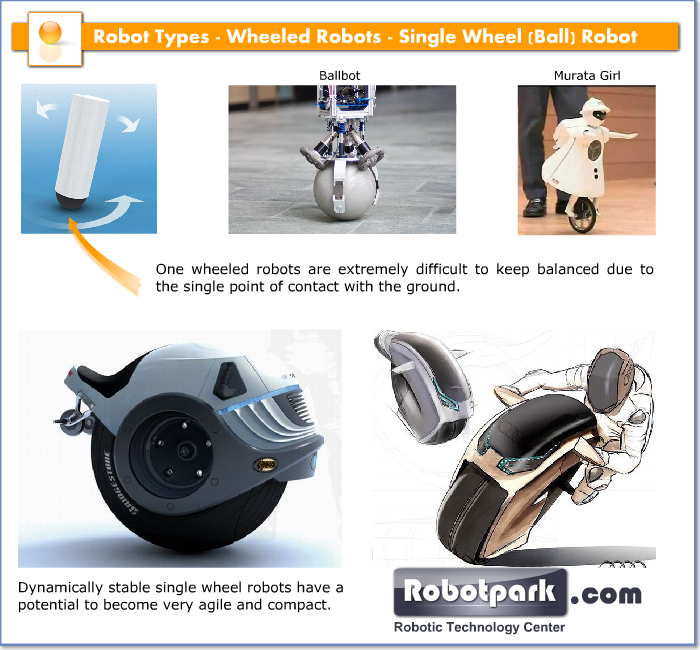
Accordingly, we are developing an inverse of this type of mobile robot that is the height, width, and weight of a person, having a high center of gravity, that balances dynamically on a single spherical wheel. Unlike balancing 2-wheel platforms which must turn before driving in some direction, the single-wheel robot can move directly in any direction. We present the overall design, actuator mechanism based on an inverse mouse-ball drive, control system, and initial results including dynamic balancing, station keeping, and point-to-point motion.
A significant, but frequently overlooked problem is that statically-stable one wheeled mobile robots can easily become dynamically unstable.
-If the center of gravity is too high,
-or the robot accelerates/decelerates too rapidly,
-or is on a sloping surface,
-the machine can tip over.
A robot must be tall enough to be able to interact with people and the human environment at a reasonable height. On the other hand, it must be skinny enough to easily make its way around without bumping into things or getting into peoples’ way.
TWO WHEELED Robots
Like one wheeled (or Ball) Robots also two wheeled robots are harder to balance than other types because they must keep moving to maintain upright. The center of gravity of the robot body is kept below the axle, usually this is accomplished by mounting the batteries below the body.
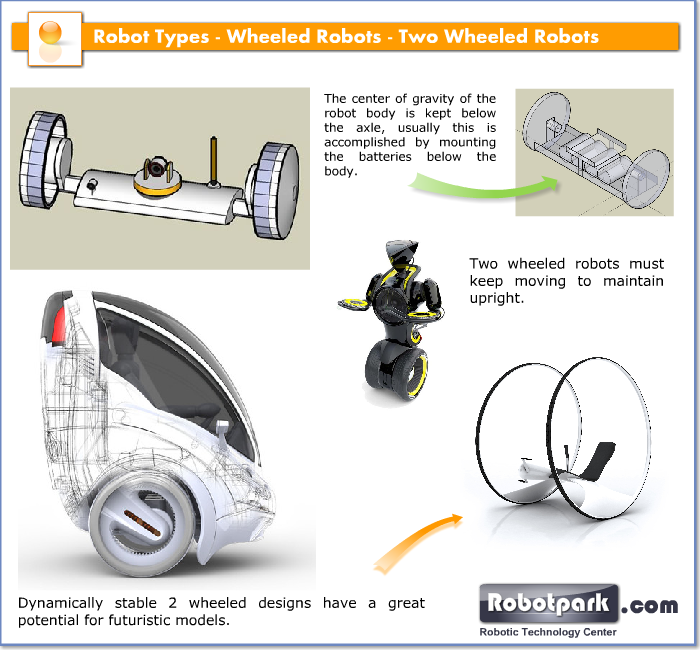
They can have their wheels parallel to each other, these vehicles are called dicycles, or one wheel in front of the other, tandemly placed wheels.
Two wheeled robots must keep moving to remain upright and they can do this by driving in the direction the robot is falling. To balance, the base of the robot must stay with under its center of gravity. For a robot that has the left and right wheels, it needs at least two sensors. A tilt sensor that is used to determine tilt angle and wheel encoders which keep track of the position of the platform of the robot.
Three Wheeled Robots
3-Wheeled Robots may be of two types:
1-Differentially steered (2 powered wheels with an additional free rotating wheel to keep the body in balance)2-Two wheels powered by a single source and a powered steering for the third wheel.
In the case of differentially steered wheels,the robot direction may be changed by varying the relative rate of rotation of the two separately driven wheels. If both the wheels are driven in the same direction and speed, the robot will go straight. Otherwise, depending on the speed of rotation and its direction, the center of rotation may fall anywhere in the line joining the two wheels.

The center of gravity in this type of robot has to lay inside the triangle formed by the wheels. If too heavy of a mass is mounted to the side of the free rotating wheel, the robot will tip over.
4 WHEELED ROBOTS
While talking about 4 Wheeled Robots, we have different types of drives.-2 Powered + 2 Free Rotating Wheels
-2-By-2 Povered Wheels (Tank-Like Drive)
-Car-Like Steering

2 Powered, 2 Free Rotating Wheels:
Same as the Differentially steered 3Wheeled Robots above but with 2 free rotating wheels for extra balance. More stable than the three wheeled robots since the center of gravity has to remain inside the rectangle formed by the four wheels instead of a triangle. This leaves a larger useful space. Still it’s advisable to keep the center of gravity to the middle of the rectangle as this is the most stable configuration, especially when taking sharp turns or moving over a non-level surface.2-By-2 Powered Wheels (Tank-Like Drive) :
This kind of robot uses 2 pairs of powered wheels. Each pair (connected by a line) turn in the same direction. The tricky part of this kind of propulsion is getting all the wheels to turn with the same speed. If the wheels in a pair aren’t running with the same speed, the slower one will slip (inefficient). If the pairs don’t run at the same speed the robot won’t be able to drive straight. A good design will have to incorporate some form of car-like steering.Car-like steering :
This method allows the robot to turn in the same way a car does. This is a far harder method to build and makes dead reckoning much harder as well. This system does have an advantage over previous methods when your robot is powered by a combustion engine: It only needs one motor (and a servo for steering of course). The previous methods would require either 2 motors or a very complicated gearbox, since they require 2 output axles with independent speed and direction of rotationMULTI WHEELED Robots
Especially when more powered wheels are used the design becomes much more complex as each of the wheels have to turn with the same speed when the robot has to move forwards. Differences in speed between the left and right wheels in differentially steered robots cause the robot to move to the side instead of in a straight line. Difference in speed between wheel on the same side cause slipping of the slowest wheel.
Sometimes an extra free rotating wheel with odometry is added to the robot. This measures more accurately how the robot moves. Odometry on the powered wheels excludes slip and other movements and thus could be erroneous.
The Mars Rovers (Sojourner, Spirit, Opportunity) are six wheeled robots that navigate across Martian terrain after landing. They are used to examine territory, interesting landmarks and make observations about the surface of Mars. They have a suspension system which keeps all six wheels in contact with the surface, and helps them traverse slopes ans sandy terrain.
TRACKED Robots
A tracked vehicle (also called: track-type tractor, tractor crawler, or track-laying vehicle) is a vehicle that runs on continuous tracks instead of wheels.Tracked vehicles include construction vehicles, military armored vehicles and unmanned ground vehicles.
The principal design advantages of tracked over wheeled vehicles are that they are in contact with a larger surface area than would generally be the case with a wheeled vehicle, and as a result exert a much lower force per unit area on the ground being traversed than a conventional wheeled vehicle of the same weight. This makes them suitable for use on soft, low friction and uneven ground such as mud, ice and snow. The principal disadvantage is that tracks are a more complex mechanism than a wheel, and relatively prone to failure modes such as snapped or derailed tracks.

Continuous tracks, also called tank treads or caterpillar tracks, are a system of vehicle propulsion in which a continuous band of treads is driven by two or more wheels. This band is typically made of modular steel plates in the case of military vehicles, or rubber reinforced with steel wires in the case of lighter agricultural or construction vehicles. The large surface area of the tracks distributes the weight of the vehicle better than steel or rubber tires on an equivalent vehicle, enabling a continuous tracked vehicle to traverse soft ground with less likelihood of becoming stuck due to sinking.
The prominent treads of the metal plates are both hard-wearing and damage resistant, especially in comparison to rubber tires. The aggressive treads of the tracks provide good traction in soft surfaces but can damage paved surfaces. Special tracks that incorporate rubber pads can be installed for use on paved surfaces to prevent the damage that can be caused by all-metal tracks.
Continuous tracks can be traced back as far as 1770 and today are commonly used on a variety of vehicles including
-bulldozers,
-excavators,
-tanks, and
-tractors,
but can be found on any vehicle used in an application that can benefit from the added traction, low ground pressure and durability inherent in continuous track propulsion systems.
ONE LEGGED Robots
1980 and 1993 there was a lot of research in making one legged robots at the Massachusetts Institute of Technology (MIT). The MIT lab turned out a series of “MIT hoppers” that could balance themselves and traverse a path. The biggest challenge with the hoppers was that they could not stand still; they needed to continue hopping in order to maintain their balance. Researchers were able to build a 3-D One-Leg Hopper that “hopped in place, traveled at a specific rate, followed simple paths, and maintained balance when disturbed.”They also constructed a hopper named Uniroo that used an actuated tail to maintain its balance.
The Monopod is a planar, single legged robot. The Monopod’s distiguishing feature is its use of an articulated, rather than a telescoping leg found in previous robots. Additionally, the leg terminates in a leaf spring unlike the air springs of the other running robots. The Monopod was used to investigate the use of articulated legs that use rotary joints. Ultimately, the Monopod ran at a maximum speed of 2.3 m/s(5.1 mph) averaged over 16 m.
Articulated legs offer mechanical advantages, such as lower moment of inertia, less unsprung mass, larger range of motion, greater compactness, better ruggedness, and ease of construction. However, articulated legs also have added kinematic complexity and coupling between degrees of freedom. This coupling is evident from the fact that displacements of the two joints do not in general cause orthogonal displacements of the toe or hip.
We believe that articulated legs, those that use rotary joints, can be designed to be stronger, lighter, faster, and more reliable than the telescoping legs used on previous running machines. One hurdle is to incorporate the elastic storage elements vital to good dynamic behavior, without making the leg too difficult to control. The tests we have done show that it performs quite well as part of a planar hopping machine, though its asymmetry and high natural frequency pose new locomotion control problems.
TWO LEGGED – BIPEDAL Robots (Humanoid)
Two legged robots have probably seen the most development dollars since humanoid robots have been envisioned since the very beginning of the field. Much of the development in passive dynamic walking has been done in this area. The design of a bipedal passive dynamic walker begins with the concept of a wheel with spokes. If the wheel is divided into sections, and all but two removed, we have what appears to be a set of legs. When the mass is properly distributed, the legs each act as inverted pendulums and the robots “rolls” through its steps.
Further complexity can be added to the model by using knee joints to shorten the legs (allowing one to swing past the other without touching the ground) and ankle joints that can provide a “spring” to the step to add lost energy back into the system.

There are several robots that have used these concepts to achieve firsts in the field of robotics. “RunBot,” developed in Germany and Scotland, broke the speed record per size for a robot in April 2006 by walking at 3.5 leg-lengths per second.The Cornell Ranger, while not truly passive, is passive inspired and one of many robots that has more than two legs but is still classified as bipedal. When viewed from the side, Ranger appears to have only two legs, but it actually has four legs. These four legs act in pairs of two, qualifying it as bipedal but providing better lateral stability. On April 3, 2008 Ranger walked 9.07 kilometers without stopping, an unofficial record at that time (it has since been surpassed, according to the Cornell team, by Boston Dynamic’s Big Dog).
One of the most successful companies at building bipedal robots over the years has been Honda. Their most recent model, ASIMO, is one of the few bipedal robots that appears humanoid, can climb stairs, and carries its own power supply. ASIMO can also change its gait in real time using Honda’s i-WALK technology. This allows ASIMO to continuously change speeds and direction. The robot can walk up stairs and run up to four miles per hour.
THREE LEGGED – Tripedal Robots
Three legged robots are not very common, especially since they have no biological counterparts. However, researchers at Virginia Tech’s RoMeLa lab have developed a three legged robot STriDER that uses a “revolutionary” passive dynamic walking technique.STriDER is short for Self-excited Tripedal Dynamic Experimental Robot. STriDER sways until it can lift one leg, and using the other two as an A-frame, swing it in between the other two “stance” legs moving forward at a sixty degree angle. This patent pending “tripedal gait” is extremely energy efficient and requires minimal control. It also allows STriDER to easily change directions by changing the sequence of its steps.

Strider on Action
Four Legged – Quadrupedal Robots
A system on four legs is another walking scheme found readily in nature. Four legged robots have the advantage of being statically stable when not moving, but require dynamic walking control. There are many different ways for a four legged robot to walk including alternating pairs and opposite pairs as in six legged robots. However these techniques now cease to be statically stable and thus require dynamic control.
Boston Dynamics has developed a four legged robot for DARPA (Defense Advanced Research Projects Agency) called “Big Dog,” that they claim is “the most advanced quadruped robot on earth.” Big Dog can run at four miles per hour, climb thirty five degree slopes, and carry 340 pounds. But the most impressive feature is its dynamic walking: Big Dog can recover from slipping and even being pushed. Its behavior is such that it approaches the infamous “uncanny valley” .
Six Legged Robots (Hexapods)
A hexapod robot is a mechanical vehicle that walks on six legs. Since a robot can be statically stable on three or more legs, a hexapod robot has a great deal of flexibility in how it can move. If legs become disabled, the robot may still be able to walk. Furthermore, not all of the robot’s legs are needed for stability; other legs are free to reach new foot placements or manipulate a payload.
Many hexapod robots are biologically inspired by Hexapoda locomotion. Hexapods may be used to test biological theories about insect locomotion, motor control, and neurobiology.
Hexapod designs vary in leg arrangement. Insect-inspired robots are typically laterally symmetric, such as the RiSE robot at Carnegie Mellon. A radially symmetric hexapod is ATHLETE (All-Terrain Hex-Legged Extra-Terrestrial Explorer) robot at JPL. Typically, individual legs range from two to six degrees of freedom. Hexapod feet are typically pointed, but can also be tipped with adhesive material to help climb walls or wheels so the robot can drive quickly when the ground is flat.
ROBOTS With MANY LEGS
ROBOTS With MANY LEGS
SWIMMING Robots – Robot FISHES
There are different types of swimming robots (or Robot Fishes). Here we examined some of these:
PacX Wave Glider
Also known as Papa Mau, swam all the way from San Francisco to Queensland, Australia, a distance of 9,000 nautical miles (16,668 kilometers). After more than a year in the water, a swimming robot has set a new world record for the longest distance traveled by an autonomous vehicle.The company behind the project, US-based Liquid Robotics, used Papa Mau to gather “unprecedented amounts of high-resolution ocean data never before available over these vast distances or time-frames” to help scientists learn more about the condition and ecosystem of the Pacific.
During its journey, the swimming robot weathered gale force storms, fended off the attention of sharks and navigated its way around the Great Barrier Reef before finally arriving in Queensland this week.
PacX comprises two main sections
-the top part has a surfboard-like appearance which helps stabilize the robot,
-the bottom section is made up of a number of fins and a keel.
There’s no fuel consumption involved as PacX is designed to convert wave energy into forward thrust.
Liquid Robotics still has another three robots at sea – one is heading for Australia while the other two are on their way to Japan.
Festo Fish
Most remarkable has to have been the fish, which swam round large tanks on the Festo stand under radio control, spitting bubbles at passers by. As well as demonstrating the capabilities of the company’s Fluidic Muscles and robotic controls, it looks to be well capable of underwater surveillance, monitoring and robotic tasks, and points a way forward for Biomimetics as a way to design future underwater vehicles.Swimming Swumanoid’ Robot
Japanese researchers are building a human-like robotic swimmer that could help athletes swim faster, or at least wear speedier swimsuits. Among other things, the Swumanoid will give researchers insight into the propulsive force created by a swimmer’s hands, which is difficult to gauge with sensors on an actual human.The robot is modeled after a competitive swimmer, built to half scale. Waterproof motors reproduce swimming motions. It currently swims about three times slower than the current 100-meter freestyle record-holder, Brazilian Cesar Cielo. Nakashima said the robot will find use in sports research. It might also serve as a rescue robot. Given other developments on the robot lifeguard front, it’s beginning to look like a favorite summer job is about to be automated.
FLYING ROBOTS
It is not easy to group Flying Robots into sub groups. As Flying robots use various kinds of technologies we will group these robots by their flying system.For now we have defined the following types (Other Types will be added soon)
-Air Baloon Robots: These type of Flying robots use an air baloon to float in the sky.
-Robots with Rotary Wings: Robots which fly like a Helicopter (Quadrocopters)
-Wing Flapping Robots: These robots fly like a bird with the help of their wings.
-Airplane Robots: Robots which fly like an airplane
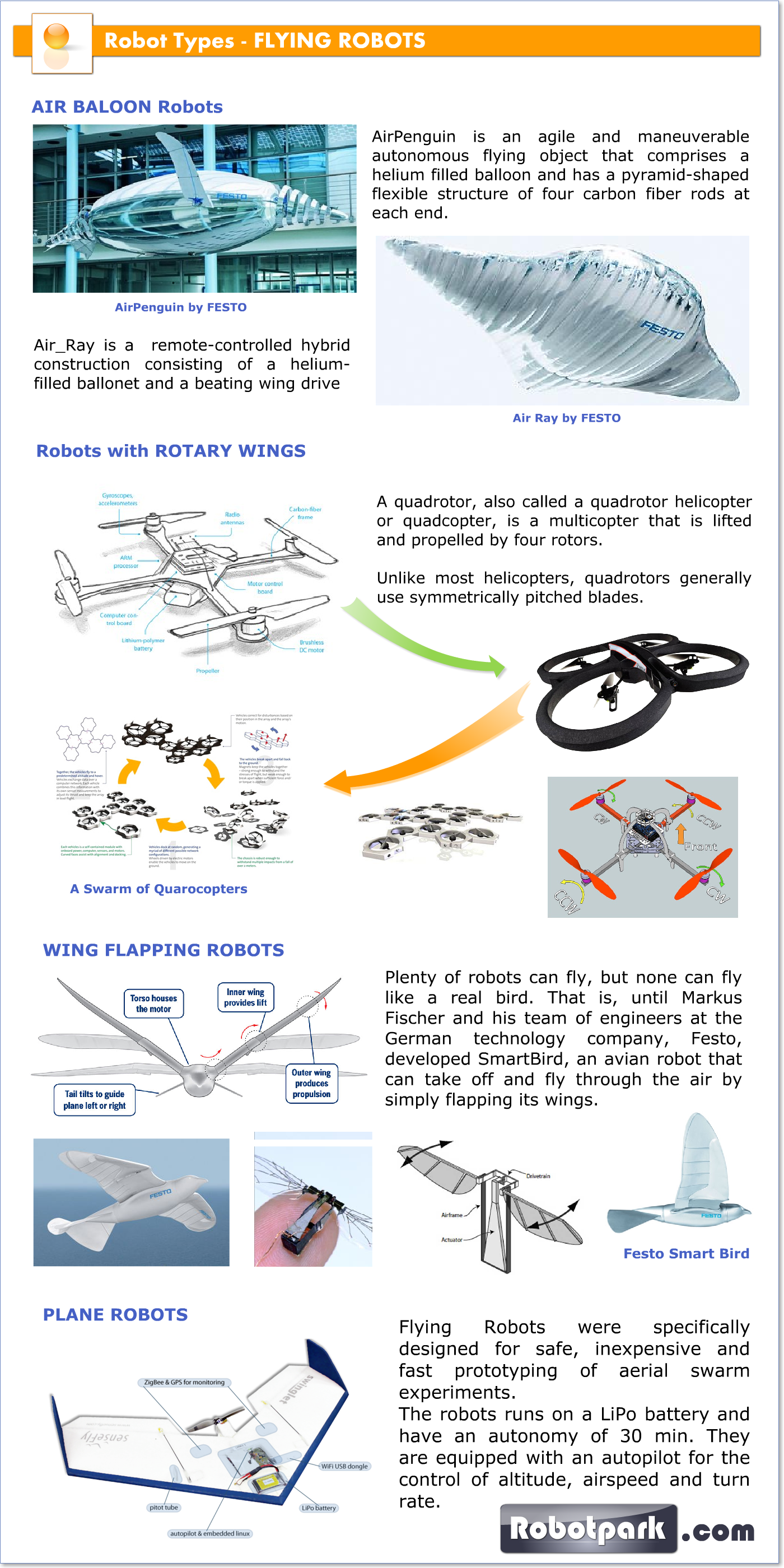
AIR BALOON ROBOTS:
AirPenguin – Autonomous Flying Robot
AirPenguin is an agile and maneuverable autonomous flying object that comprises a helium filled balloon and has a pyramid-shaped flexible structure of four carbon fiber rods at each end.
Not only is this but the AirPenguins also flaps wings as the birds do. This is made possible via new type of wing span that can produce forward or reverse thrust and 3D Fin Ray structure. Wings are controlled by two actuators wherein flapping actuator helps up and down movements and a further unit that displaces the wing struts to alter the pressure point of the wings.
Also, there is a rotational actuator for the two flapping wings, directing thrust upwards or downwards, thus making the AirPenguins rise or descend accordingly.
Air Ray
Air_ray, modelled on the manta ray, is a remote-controlled hybrid construction consisting of a helium-filled ballonet and a beating wing drive. Its lightweight design enables it to “swim” in the sea of air using the lift from the helium in a similar way to the manta ray in water.
Propulsion is achieved by a beating wing drive. The servo drive-controlled wing, which can move up and down, utilises the Fin Ray Effect® and is based on alternate pulling and pushing flanks connected via frames. When pressure is exerted on one edge, the geometrical structure automatically curves against the direction of the influencing force. A servo drive pulls the two flanks alternately in longitudinal direction, thus moving the wing up and down.
-ROBOTS WITH ROTARY WINGS
Quadrotor, Quadcopter,Quadrocopter
A quadrotor, also called a quadrotor helicopter or quadcopter, is a multicopter that is lifted and propelled by four rotors. Quadrotors are classified as rotorcraft, as opposed to fixed-wing aircraft, because their lift is generated by a set of revolving narrow-chord airfoils. Unlike most helicopters, quadrotors generally use symmetrically pitched blades; these can be adjusted as a group, a property known as ‘collective’, but not individually based upon the blade’s position in the rotor disc, which is called ‘cyclic’ (see helicopter). Control of vehicle motion is achieved by altering the pitch and/or rotation rate of one or more rotor discs, thereby changing its torque load and thrust/lift characteristics.
Swarm of Quadrocopters
A team at the Swiss Institute of Technology in Zurich has developed intelligent robots that can dock with each other and fly in a swarm.
The Distributed Flight Array robots locate each other using infrared and then lock together magnetically to create a sophisticated multi-propeller flight system.
Each hexagonal quadrocoptor robot, built of low-density expanded polypropylene (EPP) foam, has its own fixed-pitch mini-propeller and sensors. They are powered by a 50W brushless DC motor with an off-the-shelf electronic speed controller which produces more than three Newtons of thrust.
Embedded in the chassis is a lithium-ion polymer battery that is capable of powering both the motors and the electronics for up to five minutes of flight.
The units can take off and land vertically and fly independently, but erratically. Small wheels let them crawl around on the ground to locate each other.
Once they’ve hooked up, though, they become capable of more efficient flight, communicating information from their altitude sensors via infrared to make flight more even by controlling roll and pitch.
If one fails, the others can compensate. And when they land, the robots can simply detach from each other and crawl away.
The developers are continuing to work on the system, with plans for larger-scale driving and flying experiments. “The goal is to have many modules assemble at random, fly to a predetermined altitude, hover, break apart, fall back down, and repeat the cycle,” says the team.
WING FLAPPING ROBOTS
Festo Smart Bird
Plenty of robots can fly, but none can fly like a real bird. That is, until Markus Fischer and his team of engineers at the German technology company, Festo, developed SmartBird, an avian robot that can take off and fly through the air by simply flapping its wings.
SmartBird was inspired by the herring gull, Larus argentatus. It is a bit larger than this gull species, with a two-metre wingspan and a carbon-fiber “skeleton” that weighs 450 grams. Like live birds, SmartBird’s “torso” can flex, providing directional control and is radio-controlled and monitored from afar.
As you would expect, the wings move up and down, generating lift, but the wings also twist and flex in flight like those of a real bird. This torsion keeps the wing’s leading edge pointed upwards during the upward stroke, so that the wing adopts a positive angle of attack. This smooth sequence of wing movements generates thrust.
AIRPLANE ROBOTS
Smawnet Project
The SMAVNET project aims at developing swarms of flying robots that can be deployed in disaster areas to rapidly create communication networks for rescuers. Flying robots are interesting for such applications because they are fast, can easily overcome difficult terrain, and benefit from line-of-sight communication.
From a software perspective, controllers allow flying robots to work together. For swarming, robots react to wireless communication with neighboring robots or rescuers (communication-based behaviors). Using communication as a sensor is interesting because most flying robots are generally equipped with off-the-shelf radio modules that are low-cost, light-weight and relatively long-range. Furthermore, this strategy alleviates the need for position which is required for all existing aerial swarm algorithms and typically requires using sensors that depend on the environment (GPS, cameras) or are expensive and heavy (lasers, radars).
MOBILE SPHERICAL BALL ROBOTS

Morphex Project
Morphex is a Mobile Ball robot but actually it is a Hexapod. When legs come together the robot forms a sphere which can roll. Morphex locomotion system is different from other robot types.
Other Robot Technologies
Plant inspectors usually employ indirect methods to monitor buried pipework, such as running an electric current through them to identify corroded sections or using ultrasound technology to look for cracks because direct monitoring would require digging up the pipes to visually inspect them, which is a costly and time-intensive operation.
Researchers at the Massachusetts Institute of Technology (MIT) are now developing small, egg-shaped robots that will be able to navigate their way around underground pipe networks checking for cracks and corrosion. Equipped with cameras, the robots would be able to transmit images in real-time.
The researchers have devised a network of special Y-shaped valves that can be created using 3D printing across the surface of the device. By closing certain valves, thereby channelling jets of water through others, the spherical robots can be propelled in a particular direction.
Originally it had been planned that the robots would use their onboard cameras to take and store images of the interior of the pipes. The devices would then be retrieved and the images examined. However, Asada and his team now intend to equip the devices with wireless underwater communications, using laser optics to transmit images in real-time across distances of up to 100 metres. They are also working on an “eyeball” mechanism that would enable the camera to pan and tilt while the robot is stationary. To achieve this, the researchers have installed a two-axis pivoting support system that enables them to change the device’s centre of gravity.
SWARM ROBOTS – Swarm Robotics
Swarm Robotics is a new approach to the coordination of multirobot systems which consist of large numbers of mostly simple physical robots. It is supposed that a desired collective behavior emerges from the interactions between the robots and interactions of robots with the environment. This approach emerged on the field ofartificial swarm intelligence, as well as the biological studies of insects, ants and other fields in nature, where swarm behaviour occurs.
The research of swarm robotics is to study the design of robots, their physical body and their controlling behaviors. It is inspired but not limited by the emergent behavior observed in social insects, called swarm intelligence. Relatively simple individual rules can produce a large set of complex swarm behaviors. A key-component is the communication between the members of the group that build a system of constant feedback. The swarm behavior involves constant change of individuals in cooperation with others, as well as the behavior of the whole group.
Unlike distributed robotic systems in general, swarm robotics emphasizes a large number of robots, and promotes scalability, for instance by using only local communication. That local communication for example can be achieved by wirelesstransmission systems, like radio frequency or infrared.
Video tracking is an essential tool for systematically studying swarm-behavior, even though other tracking methods are available. Recently Bristol robotics laboratory developed an ultrasonic position tracking system for swarm research purposes. Further research is needed to find methodologies that allow the design and reliable prediction of swarm behavior when only the features of the individual swarm members are given.
What is a “Swarm”?
As robots become more and more useful, multiple robots working together on a single task will become commonplace. Many of the most useful applications of robots are particularly well-suited to this “swarm” approach. Groups of robots can perform these tasks more efficiently, and can perform them in fundamentally different ways than robots working individually. However, swarms of robots are difficult to program and coordinate.
Applications of Robot Swarms
There are many applications for swarms of robots. Multiple vacuum cleaner robots might need to share maps of areas where they’ve previously cleaned. A swarm of mars rovers might need to disperse throughout the environment to locate promising areas, while maintaining communications with each other. Robots used for earthquake rescue might come in three flavors: thousands of cockroach-sized scouts to infiltrate the debris and locate survivors, a few dozen rat-sized structural engineers to get near the scene and solve the “pick-up-sticks” problem of getting the rubble off, and a few brontosaurus-sized heavy-lifters to carry out the rescue plan.
In all these applications, individual robots must work independently, only communicating with other nearby robots. It is either too expensive (robot vacuums need to be very cheap), too far (it takes 15 minutes for messages to get to Mars), or impossible (radio control signals cannot penetrate into earthquake ruble) to control all of the robots from a centralized location. However, a distributed control system can let robots interact with other nearby robots, cooperating amongst themselves to accomplish their mission.
The Future
Robots are going to be an important part of the future. Once robots are useful, groups of robots are the next step, and will have tremendous potential to benefit mankind. Software designed to run on large groups of robots is the key needed to unlock this potential.
MODULAR Robots
Self-Reconfiguring Modular RobotsModular self-reconfiguring robotic systems or self-reconfigurable modular robots are autonomous kinematic machines with variable morphology. Beyond conventional actuation, sensing and control typically found in fixed-morphology robots, self-reconfiguring robots are also able to deliberately change their own shape by rearranging the connectivity of their parts, in order to adapt to new circumstances, perform new tasks, or recover from damage.
For example, a robot made of such components could assume a worm-like shape to move through a narrow pipe, reassemble into something with spider-like legs to cross uneven terrain, then form a third arbitrary object (like a ball or wheel that can spin itself) to move quickly over a fairly flat terrain; it can also be used for making “fixed” objects, such as walls, shelters, or buildings.

In some cases this involves each module having 2 or more connectors for connecting several together. They can contain electronics, sensors, computer processors, memory, and power supplies; they can also contain actuators that are used for manipulating their location in the environment and in relation with each other. A feature found in some cases is the ability of the modules to automatically connect and disconnect themselves to and from each other, and to form into many objects or perform many tasks moving or manipulating the environment.
By saying “self-reconfiguring” or “self-reconfigurable” it means that the mechanism or device is capable of utilizing its own system of control such as with actuators or stochastic means to change its overall structural shape. Having the quality of being “modular” in “self-reconfiguring modular robotics” is to say that the same module or set of modules can be added to or removed from the system, as opposed to being generically “modularized” in the broader sense. The underlying intent is to have an indefinite number of identical modules, or a finite and relatively small set of identical modules, in a mesh or matrix structure of self-reconfigurable modules.
Structure and Control
Modular robots are usually composed of multiple building blocks of a relatively small repertoire, with uniform docking interfaces that allow transfer of mechanical forces and moments, electrical power and communication throughout the robot. The modular building blocks usually consist of some primary structural actuated unit, and potentially additional specialized units such as grippers, feet, wheels, cameras, payload and energy storage and generation.
A Taxonomy of Architectures
Modular self-reconfiguring robotic systems can be generally classified into several architectural groups by the geometric arrangement of their unit (lattice vs. chain). Several systems exhibit hybrid properties.
• Lattice Architecture have their units connecting their docking interfaces at points into virtual cells of some regular grid. This network of docking points can be compared to atoms in a crystal and the grid to the lattice of that crystal. Usually few units are sufficient to accomplish a reconfiguration step. Lattice architectures allows a simpler mechanical design and a simpler computational representation and reconfiguration planning that can be more easily scaled to complex systems.
• Chain Architecture do not use a virtual network of docking points for their units. The units are able to reach any point in the space and are therefore more versatile, but a chain of many units may be necessary to reach a point making it usually more difficult to accomplish a reconfiguration step. Such systems are also more computationally difficult to represent and analyze.
• Hybrid Architecture takes advantages of both previous architectures. Control and mechanism are designed for lattice reconfiguration but also allow to reach any point in the space.
Modular robotic system are also generally classified depending on the DESIGN OF THE MODULES
• Homogeneous Modular Robot Systems have many modules of the same design forming a structure suitable to perform the required task. An advantage over other systems is that they are simple to scale in size (and possibly function), by adding more units. A commonly described disadvantage is limits to functionality – these systems often require more modules to achieve a given function, than heterogeneous systems.
• Heterogeneous Modular Robot Systems have different modules, each of which do specialized functions, forming a structure suitable to perform a task. An advantage is compactness, and the versatility to design and add units to perform any task. A commonly described disadvantage is an increase in complexity of design, manufacturing, and simulation methods.
Other modular robotic systems exist which are not self-reconfigurable, and thus do not formally belong to this family of robots though they may have similar appearance. For example, self-assembling systems may be composed of multiple modules but cannot dynamically control their target shape. Similarly, tensegrity robotics may be composed of multiple interchangeable modules but cannot self-reconfigure.
Motivation and Inspiration
There are two key motivations for designing modular self-reconfiguring robotic systems.
• Functional Advantage: Self reconfiguring robotic systems are potentially more robust and more adaptivethan conventional systems. The reconfiguration ability allows a robot or a group of robots to disassemble and reassemble machines to form new morphologies that are better suitable for new tasks, such as changing from a legged robot to a snake robot and then to a rolling robot. Since robot parts are interchangeable (within a robot and between different robots), machines can also replace faulty parts autonomously, leading to self-repair.
• Economic Advantage: Self reconfiguring robotic systems can potentially lower overall robot cost by making a range of complex machines out of a single (or relatively few) types of mass-produced modules.
Both these advantages have not yet been fully realized. A modular robot is likely to be inferior in performance to any single custom robot tailored for a specific task. However, the advantage of modular robotics is only apparent when considering multiple tasks that would normally require a set of different robots.
The added degrees of freedom make modular robots more versatile in their potential capabilities, but also incur a performance tradeoff and increased mechanical and computational complexities.
-The quest for self-reconfiguring robotic structures is to some extent inspired by envisioned applications such as long-term space missions, that require long-term self-sustaining robotic ecology that can handle unforeseen situations and may require self repair.
-A second source of inspiration are biological systems that are self-constructed out of a relatively small repertoire of lower-level building blocks (cells or amino acids, depending on scale of interest). This architecture underlies biological systems’ ability to physically adapt, grow, heal, and even self replicate – capabilities that would be desirable in many engineered systems.
Quantitative Accomplishment
• The robot with most active modules has 56 units <polybot centipede, PARC>
• The smallest actuated modular unit has a size of 12 mm <smart pebble, MIT>
• The largest actuated modular unit (by volume) has the size of 8 m^3 <(GHFC)giant helium filled catoms, CMU>
• The strongest actuation modules are able to lift 5 identical horizontally cantilevered units.<PolyBot g1v5, PARC>
• The fastest modular robot can move at 23 unit-sizes/second.<CKbot, dynamic rolling, ISER’06>
• The largest simulated system contained many 100,000′s of units.
Nano Robots
Nanobots, Nanoids, Nanites, NanoMachines, Nanomites
Nanorobotics is the emerging technology field creating machines or robots whose components are at or close to the scale of a nanometer (0,000000001 Meters – 10−9 Meters).More specifically, nanorobotics refers to the nanotechnology engineering discipline of designing and building nanorobots, with devices ranging in size from0.1–10 micrometers and constructed of nanoscale or molecular components. The names-nanobots,
-nanoids,
-nanites,
-nanomachines or
-nanomites
have also been used to describe these devices currently under research and development.
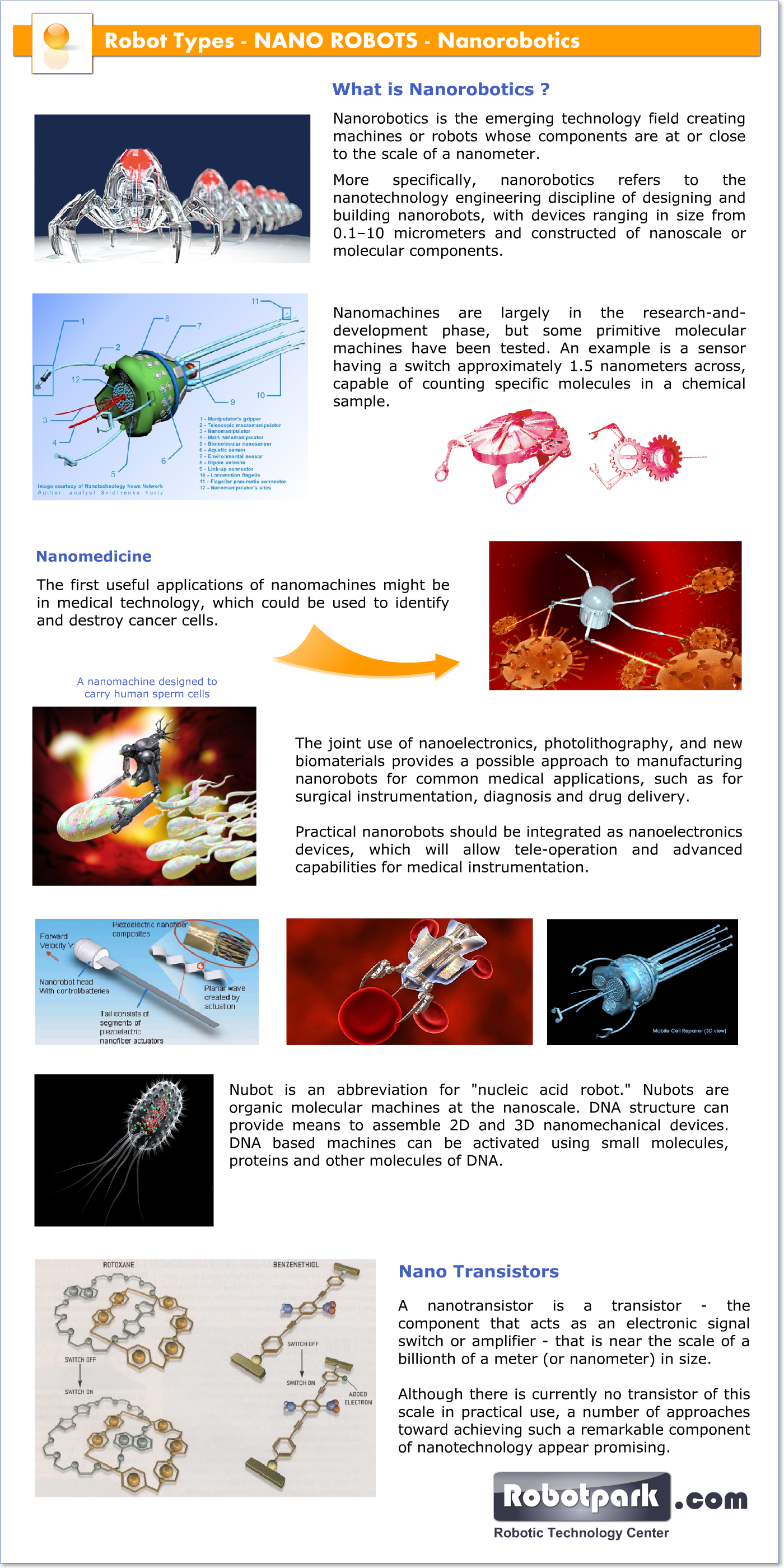
Nanomachines are largely in the research-and-development phase, but some primitive molecular machines have been tested. An example is a sensor having a switch approximately 1.5 nanometers across, capable of counting specific molecules in a chemical sample. The first useful applications of nanomachines might be in medical technology, which could be used to identify and destroy cancer cells.
Another potential application is the detection of toxic chemicals, and the measurement of their concentrations, in the environment. Rice University has demonstrated a single-molecule car developed by a chemical process and including buckyballs for wheels. It is actuated by controlling the environmental temperature and by positioning ascanning tunneling microscope tip.
Another definition: is a robot that allows precision interactions with nanoscale objects, or can manipulate with nanoscale resolution. Such devices are more related to microscopy or scanning probe microscopy, instead of the description of nanorobots asmolecular machine. Following the microscopy definition even a large apparatus such as an atomic force microscope can be considered a nanorobotic instrument when configured to perform nanomanipulation. For this perspective, macroscale robots or microrobots that can move with nanoscale precision can also be considered nanorobots.
Nanorobotics Theory
Since nanorobots would be microscopic in size, it would probably be necessary for very large numbers of them to work together to perform microscopic and macroscopic tasks. These nanorobot swarms, both those incapable of replication (as in utility fog) and those capable of unconstrained replication in the natural environment (as in grey goo and its less common variants), are found in many science fiction stories, such as the Borg nanoprobes in Star Trek and The Outer Limits episodeThe New Breed.
Some proponents of nanorobotics, in reaction to the grey goo scare scenarios that they earlier helped to propagate, hold the view that nanorobots capable of replication outside of a restricted factory environment do not form a necessary part of a purported productive nanotechnology, and that the process of self-replication, if it were ever to be developed, could be made inherently safe. They further assert that their current plans for developing and using molecular manufacturing do not in fact include free-foraging replicators.
The most detailed theoretical discussion of nanorobotics, including specific design issues such as sensing, power communication, navigation, manipulation, locomotion, and onboard computation, has been presented in the medical context of nanomedicine by Robert Freitas. Some of these discussions remain at the level of unbuildable generality and do not approach the level of detailed engineering.
Biochip
The joint use of nanoelectronics, photolithography, and new biomaterials provides a possible approach to manufacturing nanorobots for common medical applications, such as for surgical instrumentation, diagnosis and drug delivery. This method for manufacturing on nanotechnology scale is currently in use in the electronics industry.So, practical nanorobots should be integrated as nanoelectronics devices, which will allow tele-operation and advanced capabilities for medical instrumentation.
Nubots
Nubot is an abbreviation for “nucleic acid robot.” Nubots are organic molecular machines at the nanoscale. DNA structure can provide means to assemble 2D and 3D nanomechanical devices. DNA based machines can be activated using small molecules, proteins and other molecules of DNA. Biological circuit gates based on DNA materials have been engineered as molecular machines to allow in-vitro drug delivery for targeted health problems.Such material based systems would work most closely to smart biomaterial drug system delivery,while not allowing precise in vivo teleoperation of such engineered prototypes.
Positional Nanoassembly
Nanofactory Collaboration, founded by Robert Freitas and Ralph Merkle in 2000 and involving 23 researchers from 10 organizations and 4 countries, focuses on developing a practical research agenda specifically aimed at developing positionally-controlled diamond mechanosynthesisand a diamondoid nanofactory that would have the capability of building diamondoid medical nanorobots.
Bacteria-Based
This approach proposes the use of biological microorganisms, like the bacterium Escherichia coli. Thus the model uses a flagellum for propulsion purposes. Electromagnetic fields normally control the motion of this kind of biological integrated device.
Open technology
A document with a proposal on nanobiotech development using open technology approaches has been addressed to the United Nations General Assembly. According to the document sent to the UN, in the same way that Open Source has in recent years accelerated the development ofcomputer systems, a similar approach should benefit the society at large and accelerate nanorobotics development. The use of nanobiotechnology should be established as a human heritage for the coming generations, and developed as an open technology based on ethical practices forpeaceful purposes. Open technology is stated as a fundamental key for such an aim.
Soft Elastic Robots
Harvard researchers have blended organic chemistry, soft materials science, and robotics to create a soft robot inspired by animals like squid and worms.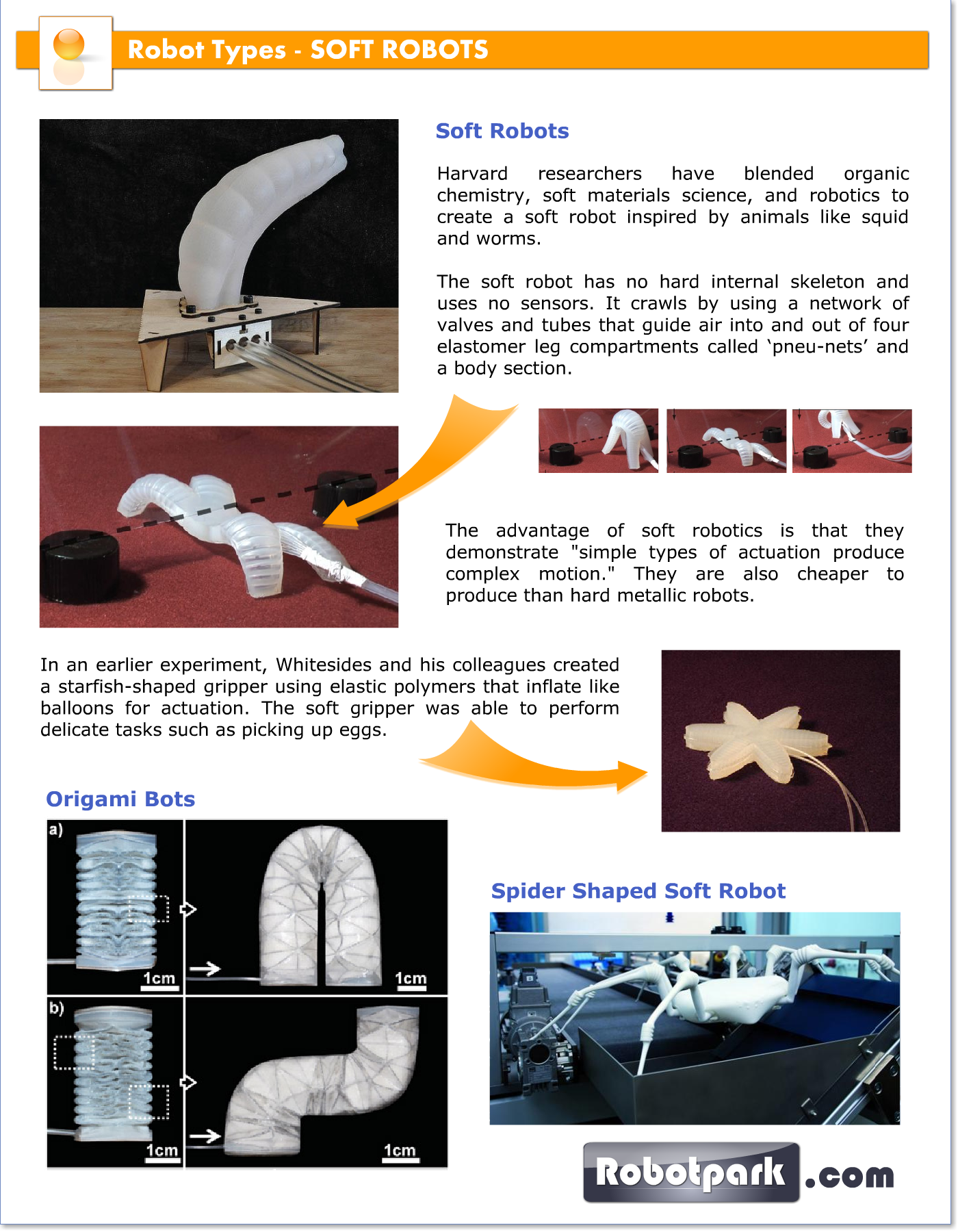
The soft robot has no hard internal skeleton and uses no sensors. It crawls by using a network of valves and tubes that guide air into and out of four elastomer leg compartments called ‘pneu-nets’ and a body section.
The pneumatically actuated robot can navigate obstacles using one of several gaits–walking, crawling, and slithering–and it can deflate to pass through tiny little gaps.
In an earlier experiment, Whitesides and his colleagues created a starfish-shaped gripper using elastic polymers that inflate like balloons for actuation. The soft gripper was able to perform delicate tasks such as picking up eggs.
Soft robots can’t yet handle heavy loads or conduct electricity, but the researchers believe that eventually they may be able to by incorporating the right materials.
Robotic MECHANISMS – 51003

Basics of Robotic MECHANISMS
INTRODUCTION : Machines & Mechanisms
Complex machines from internal combustion engines to helicopters and machine tools contain many mechanisms. However, it might not be as obvious that mechanisms can be found in consumer goods from toys and cameras to computer drives and printers.In fact, many common hand tools such as scissors, screwdrivers, wrenches, jacks, and hammers are actually true mechanisms. Moreover, the hands and feet, arms, legs, and jaws of humans qualify as functioning mechanisms as do the paws and legs, flippers, wings, and tails of animals.
There is a difference between a machine and a mechanism: All machines transform energy to do work, but only some mechanisms are capable of performing work. The term machinery means an assembly that includes both machines and mechanisms.

Fig. 1: Cross section of a cylinder of an internal combustion engine showing piston reciprocation (a), and the skeleton outline of the linkage mechanism that moves the piston (b).
Figure 1a illustrates a cross section of a machine—an internal combustion engine. The assembly of the piston, connecting rod, and crankshaft is a mechanism, termed a slider-crank mechanism. The basic schematic drawing of that mechanism, Fig. 1b, called a skeleton outline, shows only its fundamental structure without the technical details explaining how it is constructed.
Basics of Robotics Mechanisms
-Inclined Plane-Pulley Systems
-Screw Systems
-Levers
-Linkages – Simple Planar Linkages
-Physical Principles – Efficiency of Machines & Mechanical Advantage
Robotic MECHANISMS – INCLINED PLANE
An inclined plane is a flat supporting surface tilted at an angle, with one end higher than the other, used as an aid for raising or lowering a load. The inclined plane is one of the six classical simple machines defined by Renaissance scientists. Inclined planes are widely used to move heavy loads over vertical obstacles; examples vary from a ramp used to load goods into a truck, to a person walking up a pedestrian ramp, to an automobile or railroad train climbing a grade.
Moving an object up an inclined plane requires less force than lifting it straight up, at a cost of an increase in the distance moved. The mechanical advantage of an inclined plane, the factor by which the force is reduced, is equal to the ratio of the length of the sloped surface to the height it spans. Due to conservation of energy, the same amount of mechanical energy (work) is required to lift a given object by a given vertical distance, disregarding losses from friction, but the inclined plane allows the same work to be done with a smaller force exerted over a greater distance.
The angle of friction, also sometimes called the angle of repose,is the maximum angle at which a load can rest motionless on an inclined plane due to friction, without sliding down. This angle is equal to the arctangent of the coefficient of static friction μs between the surfaces.

For example, if a weight W of 1000 lb is to be raised vertically through a height BC of 3 ft without using an inclined plane, a force F of 1000 lb must be exerted over that height. However, with an inclined plane, the weight is moved over the longer distance of 8 ft, but a force F of only 3/8 of 1000 or 375 lb would be required because the weight is moved through a longer distance. To determine the mechanical advantage of the inclined plane, the following formula is used:
F = W sin θ
sin θ = height h / lenght l
where height h = 3 ft, length l = 8 ft , sin θ = 0,375, and weight W = 1000lb
F= 1000 x 0,375
F = 375 lb
Mechanical advantage MA = load / effort = W / F = 1000 / 375 = 2,7
F = W sin θ
sin θ = height h / lenght l
where height h = 3 ft, length l = 8 ft , sin θ = 0,375, and weight W = 1000lb
F= 1000 x 0,375
F = 375 lb
Mechanical advantage MA = load / effort = W / F = 1000 / 375 = 2,7
Moving an object up an inclined plane requires less force than lifting it straight up, at a cost of an increase in the distance moved. The mechanical advantage of an inclined plane, the factor by which the force is reduced, is equal to the ratio of the length of the sloped surface to the height it spans. Due to conservation of energy, the same amount of mechanical energy (work) is required to lift a given object by a given vertical distance, disregarding losses from friction, but the inclined plane allows the same work to be done with a smaller force exerted over a greater distance.
The angle of friction, also sometimes called the angle of repose,is the maximum angle at which a load can rest motionless on an inclined plane due to friction, without sliding down. This angle is equal to the arctangent of the coefficient of static friction μs between the surfaces.
Inclined Plane Example
The inclined plane, shown in Fig. , has an incline length l (AB) = 8 ft and a height h (BC) = 3 ft. The inclined plane permits a smaller force to raise a given weight than if it were lifted directly from the ground.
For example, if a weight W of 1000 lb is to be raised vertically through a height BC of 3 ft without using an inclined plane, a force F of 1000 lb must be exerted over that height. However, with an inclined plane, the weight is moved over the longer distance of 8 ft, but a force F of only 3/8 of 1000 or 375 lb would be required because the weight is moved through a longer distance. To determine the mechanical advantage of the inclined plane, the following formula is used:
F = W sin θ
sin θ = height h / lenght l
where height h = 3 ft, length l = 8 ft , sin θ = 0,375, and weight W = 1000lb
F= 1000 x 0,375
F = 375 lb
Mechanical advantage MA = load / effort = W / F = 1000 / 375 = 2,7
Frictionless Inclined Plane
If there is no friction between the object being moved and the plane, the device is called an ideal inclined plane. This condition might be approached if the object is rolling, like a barrel, or supported on wheels or casters. Due to conservation of energy, for a frictionless inclined plane the work done on the load lifting it, Wout, is equal to the work done by the input force, WinF = W sin θ
sin θ = height h / lenght l
where height h = 3 ft, length l = 8 ft , sin θ = 0,375, and weight W = 1000lb
F= 1000 x 0,375
F = 375 lb
Mechanical advantage MA = load / effort = W / F = 1000 / 375 = 2,7
Frictionless Inclined Plane
If there is no friction between the object being moved and the plane, the device is called an ideal inclined plane. This condition might be approached if the object is rolling, like a barrel, or supported on wheels or casters. Due to conservation of energy, for a frictionless inclined plane the work done on the load lifting it, Wout, is equal to the work done by the input force, Win
Robotic MECHANISMS – PULLEY SYSTEMS
A pulley is a wheel on an axle that is designed to support movement of a cable or belt along its circumference. Pulleys are used in a variety of ways to lift loads, apply forces, and to transmit power. A pulley is also called a sheave or drum and may have a groove between two flanges around its circumference. The drive element of a pulley system can be a rope, cable, belt, or chain that runs over the pulley inside the groove.

The common principle of all screws is that a rotating helix can cause linear motion.
Mechanisms are often required to move a large load with a small effort. For example, a car jack allows an ordinary human to lift a car which may weigh as much as 6000 lb, while the person only exerts a force equivalent to 20 or 30 lb.
Biomechanics of the Body – Levers

EVANS STRAIGHT LINE
Diametral Pitch of Spur Gears (DP)

Hero of Alexandria identified the pulley as one of six simple machines used to lift weights. Pulleys are assembled to form a block and tackle in order to provide mechanical advantage to apply large forces. Pulleys are also assembled as part ofbelt and chain drives in order to transmit power from one rotating shaft to another.
Example of a Pulley System
In the typical pulley system, shown in Fig. 3a, each block contains two pulleys or sheaves within a frame or shell. The upper block is fixed and the lower block is attached to the load and moves with it. A cable fastened at the end of the upper block passes around four pulleys before being returned to the operator or other power source.
Figure b shows the pulleys separated for clarity. To raise the load through a height h, each of the sections of the cable A, B, C, and D must be moved to a distance equal to h.
The operator or other power source must exert a force F through a distance s = 4h so that the velocity ratio of s to h is 4.
Therefore, the theoretical mechanical advantage of the system shown is 4, corresponding to the four cables supporting the load W. The theoretical mechanical advantage TA for any pulley system similar to that shown equals the number of parallel cables that support the load.
Robotic MECHANISMS – SCREW SYSTEMS
What is a Screw Mechanism ?
The common principle of all screws is that a rotating helix can cause linear motion.
A screw is a mechanism that converts rotational motion to linear motion, and a torque (rotational force) to a linear force. It is one of the six classical simple machines. The most common form consists of a cylindrical shaft with helical grooves or ridges called threads around the outside. The screw passes through a hole in another object or medium, with threads on the inside of the hole that mesh with the screw’s threads. When the shaft of the screw is rotated relative to the stationary threads, the screw moves along its axis relative to the medium surrounding it; for example rotating a wood screw forces it into wood.
In screw mechanisms, either the screw shaft can rotate through a threaded hole in a stationary object, or a threaded collar such as a nut can rotate around a stationary screw shaft. Geometrically, a screw can be viewed as a narrow inclined plane wrapped around a cylinder.
Other mechanisms that use the same principle, also called screws, don’t necessarily have a shaft or threads. For example, a corkscrew is a helix-shaped rod with a sharp point, and an Archimedes’ screw is a water pump that uses a rotating helical chamber to move water uphill. The common principle of all screws is that a rotating helix can cause linear motion.
A screw can amplify force; a small rotational force (torque) on the shaft can exert a large axial force on a load. The smaller the pitch, the distance between the screw’s threads, the greater the mechanical advantage, the ratio of output to input force. Screws are widely used in threaded fasteners to hold objects together, and in devices such as screw tops for containers, vises, screw jacks and screw presses.

Screw Type – JACK
Mechanisms are often required to move a large load with a small effort. For example, a car jack allows an ordinary human to lift a car which may weigh as much as 6000 lb, while the person only exerts a force equivalent to 20 or 30 lb.
The screw jack, shown in Fig. is a practical application of the inclined plane because a screw is considered to be an inclined plane wrapped around cylinder. A force F must be exerted at the end of a length of horizontal bar l to turn the screw to raise the load (weight W) of 1000 lb. The 5-ft bar must be moved through a complete turn or a circle of length s 2 l to advance the load a distance h of 1.0 in. or 0.08 ft equal to the pitch p of the screw. The pitch of the screw is the distance advanced in a complete turn.
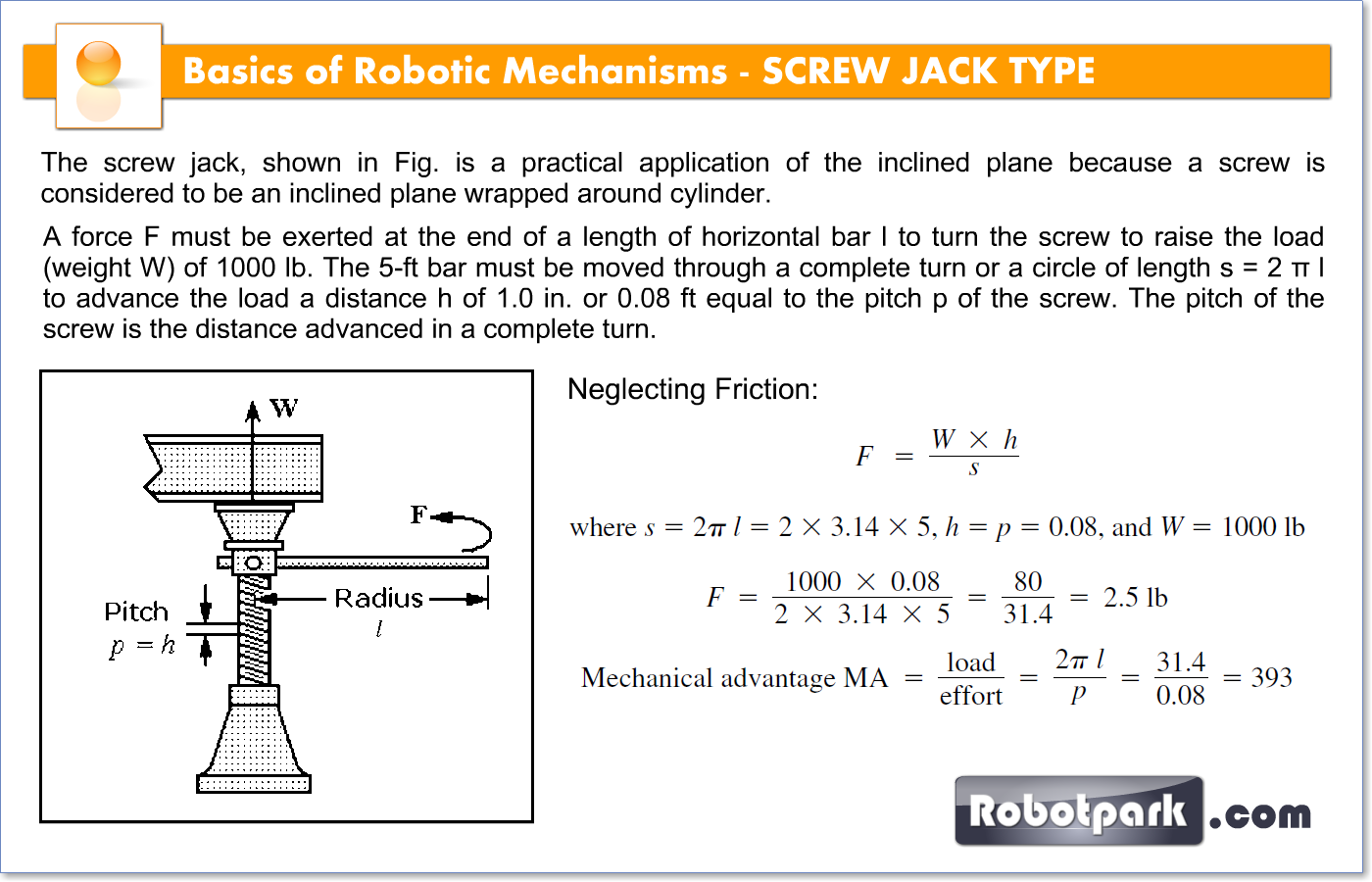
Advantages
An advantage of jackscrews over some other types of jack is that they are self-locking, which means when the rotational force on the screw is removed, it will remain motionless where it was left and will not rotate backwards, regardless of how much load it is supporting. This makes them inherently safer than hydraulic jacks, for example, which will move backwards under load if the force on the hydraulic actuator is accidentally released.
Mechanical Advantage
The mechanical advantage of a screw jack, the ratio of the force the jack exerts on the load to the input force on the lever, ignoring friction, is
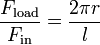
where ;
is the force the jack exerts on the load
i s the rotational force exerted on the handle of the jack
is the length of the jack handle, from the screw axis to where the force is applied
is the lead of the screw.
However, most screw jacks have large amounts of friction which increase the input force necessary, so the actual mechanical advantage is often only 30% to 50% of this figure.
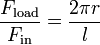




Torque Form
The rotational force applied to the screw is actually a torque
. Because of this, the input force required to turn a screw depends on how far from the shaft it is applied; the farther from the shaft, the less force is needed to turn it. The force on a screw is not usually applied at the rim as assumed above. It is often applied by some form of lever; for example a bolt is turned by a wrench. The mechanical advantage in this case can be calculated by using the length of the lever arm for r in the above equation. This extraneous factor r can be removed from the above equation by writing it in terms of torque:



Actual Mechanical Advantage and Efficiency
Because of the large area of sliding contact between the moving and stationary threads, screws typically have large frictional energy losses. Even well-lubricated jack screws have efficiencies of only 15% – 20%, the rest of the work applied in turning them is lost to friction. When friction is included, the mechanical advantage is no longer equal to the distance ratio but also depends on the screw’s efficiency. From conservation of energy, the work Win done on the screw by the input force turning it is equal to the sum of the work done moving the load Wout, and the work dissipated as heat by friction Wfric in the screw

The efficiency η is a dimensionless number between 0 and 1 defined as the ratio of output work to input work


Work is defined as the force multiplied by the distance moved, so
and
and therefore


or in terms of torque :
So the mechanical advantage of an actual screw is reduced from what it would be in an ideal, frictionless screw by the efficiency
. Because of their low efficiency, in powered machinery screws are not often used as linkages to transfer large amounts of power (except in lead screws) but are more often used in positioners that operate intermittently.










Robotic MECHANISMS – LEVERS
What is a Lever ? Types of Levers…
Levers are the simplest of mechanisms; there is evidence that Stone Age humans used levers to extend their reach or power; they made them from logs or branches to move heavy loads such as rocks. It has also been reported that primates and certain birds use twigs or sticks to extend their reach and act as tools to assist them in obtaining food.
A lever is a rigid beam that can rotate about a fixed point along its length called the fulcrum. Physical effort applied to one end of the beam will move a load at the other end. The act of moving the fulcrum of a long beam nearer to the load permits a large load to be lifted with minimal effort. This is another way to obtain mechanical advantage.
The three classes of lever are illustrated in Fig. Each is capable of providing a different level of mechanical advantage. These levers are called Class 1, Class 2, and Class 3. The differences in the classes are determined by:
-Class 1 – Position along the length of the lever where the effort is applied
-Class 2 -Position along the length of the lever where the load is applied
-Class 3 -Position along the length of the lever where the fulcrum or pivot point is located
CLASS 1 LEVER, the most common, has its fulcrum located at or about the middle with effort exerted at one end and load positioned at the opposite end, both on the same side of the lever.
Examples of Class 1 levers are playground seesaw, crowbar, scissors, claw hammer, and balancing scales.
CLASS 2 LEVER, has its fulcrum at one end; effort is exerted at the opposite end, and the opposing load is positioned at or near the middle.
Examples of Class 2 levers are wheelbarrow, simple bottle openers, nutcracker, and foot pump for inflating air mattresses and inflatable boats.
CLASS 3 LEVER, also has its fulcrum on one end; load is exerted at the opposite end, and the opposing effort is exerted on or about the middle.
Examples of Class 3 levers are shovel and fishing rod where the hand is the fulcrum, tweezers, and human and animal arms and legs.
-Class 2 -Position along the length of the lever where the load is applied
-Class 3 -Position along the length of the lever where the fulcrum or pivot point is located
Examples of Class 1 levers are playground seesaw, crowbar, scissors, claw hammer, and balancing scales.
Examples of Class 2 levers are wheelbarrow, simple bottle openers, nutcracker, and foot pump for inflating air mattresses and inflatable boats.
Examples of Class 3 levers are shovel and fishing rod where the hand is the fulcrum, tweezers, and human and animal arms and legs.
Law of the Lever
The lever is a movable bar that pivots on a fulcrum attached to a fixed point. The lever operates by applying forces at different distances from the fulcrum, or pivot.
Assuming the lever does not dissipate or store energy, the power into the lever must equal the power out of the lever. As the lever rotates around the fulcrum, points farther from this pivot move faster than points closer to the pivot. Therefore a force applied to a point farther from the pivot must be less than the force located at a point closer in, because power is the product of force and velocity.
If a and b are distances from the fulcrum to points A and B and let the force FA applied to A is the input and the force FB applied at B is the output, the ratio of the velocities of points A and B is given by a/b, so we have the ratio of the output force to the input force, or mechanical advantage, is given by

This is the law of the lever, which was proven by Archimedes using geometric reasoning. It shows that if the distance a from the fulcrum to where the input force is applied (point A) is greater than the distance b from fulcrum to where the output force is applied (point B), then the lever amplifies the input force. On the other hand, if the distance a from the fulcrum to the input force is less than the distance b from the fulcrum to the output force, then the lever reduces the input force.

Winches, Windlasses, and Capstans
Winches, windlasses, and capstans are machines that convert rotary motion into linear motion, usually with some mechanical advantage. These machines are essentially Class 1 levers: effort is applied to a lever or crank, the fulcrum is the center of the drum, and the load is applied to the rope, chain, or cable.
Manually operated windlasses and capstans, mechanically the same, were originally used on sailing ships to raise and lower anchors. Operated by one or more levers by one or more sailors, both had barrels or drums on which rope or chain was wound. In the past, windlasses were distinguished from capstans; windlasses had horizontal drums and capstans had vertical drums. The modern term winch is now the generic name for any manual or poweroperated drum for hauling a load with cable, chain, or rope. The manually operated winch, shown in Fig., is widely used today on sailboats for raising and trimming sails, and sometimes for weighing anchors.
Ignoring friction, the mechanical advantage of all of these machines is approximately the length of the crank divided by the diameter of the drum. In the winch example shown, when the left end of the line is held under tension and the handle or crank is turned clockwise, a force is applied to the line entering on the right; it is attached to the load to perform such useful work as raising or tensioning sails.
Biomechanics of the Body – Levers

Biomechanics: the study of the mechanics as it relates to the functional and anatomical analysis of the human body.
-Statics: involves all forces acting on the body being in balance, resulting in the body being in equilibrium.
-Dynamics: involves the study of systems in motion while unbalanced due to unequal forces acting on the body.
Kinesiology: Meaning of Kinesiology is the study of movement.
Kinesis: “To move”
-ology: “to study:
-Dynamics: involves the study of systems in motion while unbalanced due to unequal forces acting on the body.
-ology: “to study:
Robotic Mechanisms – Four Bar Linkages
What are Complex Linkages ? Four Bar Linkages ?
In addition to changing the motions of objects or forces, more complex linkages have been designed to perform many specialized functions: These include;
-drawing or tracing straight lines;
-moving objects or tools faster in a retraction stroke than in an extension stroke;
-and converting rotating motion into linear motion and vice versa.
The simplest specialized linkages are four-bar linkages. These linkages have been versatile enough to be applied in many different applications. Four-bar linkages actually have only three moving links but they have one fixed link and four pin joints or pivots. A useful mechanism must have at least four links but closed-loop assemblies of three links are useful elements in structures. Because any linkage with at least one fixed link is a mechanism, both the parallel-motion and push-pull linkages mentioned earlier are technically machines.
-drawing or tracing straight lines;
-moving objects or tools faster in a retraction stroke than in an extension stroke;
-and converting rotating motion into linear motion and vice versa.
Four Bar Linkages – Hoekens Linkage
The Hoekens linkage is a four-bar mechanism that converts rotational motion to approximate straight-line motion with approximate constant velocity. The precise design trades off straightness, lack of acceleration, and what proportion of the driving rotation is spent in the linear portion of the full curve.

Mechanisms – Linkages – Pantograph Mechanism
A pantograph is a mechanical linkage connected in a manner based on parallelograms so that the movement of one pen, in tracing an image, produces identical movements in a second pen. If a line drawing is traced by the first point, an identical, enlarged, or miniaturized copy will be drawn by a pen fixed to the other.
Because of their effectiveness at translating motion in a controlled fashion, pantographs have come to be used as a type of motion guide for objects large and small. A common example of the use of a pantograph assembly as mechanical guide frame is the extension arm of an adjustable wall-mounted mirror.
What is a Pantograph ?
Pantograph is a geometrical instrument used in drawing offices for reproducing given geometrical figures or plane areas of any shape, on an enlarged or reduced scale. It is also used for guiding cutting tools. Its mechanism is utilised as an indicator rig for reproducing the displacement of cross-head of a reciprocating engine which, in effect, gives the position of displacement.
Robot Arm – 4 Bar Linkage End Effector, Robot Gripper
EVANS STRAIGHT LINE
A mechanism that produces a straight-line (or nearly so) output motion from an input element that rotates, oscillates, or moves in a straight line. Common machine elements, such as linkages, gears, and cams, are often used in ingenious ways to produce the required controlled motion. The more elegant designs use the properties of special points on one of the links of a four-bar linkage.
Four-Bar linkages that generate approximate straight lines are not new. In 1784 James Watt applied the concept to the vertical-cylinder beam engine. By selecting the appropriate link lengths, the designer can easily develop a mechanism with a high-quality approximate straight line.
Contemporary kinematicians have contributed to more comprehensive studies of the properties of the mechanisms that generate approximate straight lines. The work not only describes the various classical mechanisms, but also provides design information on the quality (the amount of deviation from a straight line) and the length of the straight-line output.
A mechanism that produces a straight-line (or nearly so) output motion from an input element that rotates, oscillates, or moves in a straight line. Common machine elements, such as linkages, gears, and cams, are often used in ingenious ways to produce the required controlled motion. The more elegant designs use the properties of special points on one of the links of a four-bar linkage.
Four-Bar linkages that generate approximate straight lines are not new. In 1784 James Watt applied the concept to the vertical-cylinder beam engine. By selecting the appropriate link lengths, the designer can easily develop a mechanism with a high-quality approximate straight line.
Contemporary kinematicians have contributed to more comprehensive studies of the properties of the mechanisms that generate approximate straight lines. The work not only describes the various classical mechanisms, but also provides design information on the quality (the amount of deviation from a straight line) and the length of the straight-line output.
Straight Line Generator – Lipkin Linkage
The Peaucellier–Lipkin linkage (or Peaucellier–Lipkin cell, or Peaucellier–Lipkin Inversor), invented in 1864, was the first planar linkage capable of transforming rotary motion into perfect straight-line motion, and vice versa. It is named after Charles-Nicolas Peaucellier (1832–1913), a French army officer, and Yom Tov Lipman Lipkin, a Lithuanian Jew and son of the famed Rabbi Israel Salanter.
Until this invention, no planar method existed of producing straight motion without reference guideways, making the linkage especially important as a machine component and for manufacturing. In particular, a piston head needs to keep a good seal with the shaft in order to retain the driving (or driven) medium. The Peaucellier linkage was important in the development of the steam engine.
The mathematics of the Peaucellier–Lipkin linkage is directly related to the inversion of a circle.
Tchebicheff’s straight-line generator, (Chebyshev linkage) can also describe a horizontal line. The Chebyshev linkage is a mechanical linkage that converts rotational motion to approximate straight-line motion.
It was invented by the 19th century mathematician Pafnuty Chebyshev who studied theoretical problems in kinematic mechanisms. One of the problems was the construction of a linkage that converts a rotary motion into an approximate straight line motion. This was also studied by James Watt in his improvements to the steam engine.
The Chebyshev approximate straight line mechanism is also a four bar linkage mechanism that is both historically important and also of practical importance. After the invention of steam engine and straight line mechanism by Watt a range of straight line mechanisms were designed. Chebyshev’s mechanism is the first mechanism to be designed after Watt’s linkage by a Russian Mathematician Pafnuty Chebyshev. This mechanism was invariable used for linear guidance of the piston and valves.
Like the Watt’s Linkage Chebyshev’s straight line mechanism is simple in construction. It is a double rocker and the mid point of the coupler is the point tracing the approximate linear path. Chebyshev’s mechanism has two critical advantages over Watt’s linkage, viz, a very long segment of the path of the coupler midpoint is approximately linear and both fixed points of the linkage are on the same side of the linear path, which in case of Watt’s linkage are on opposite sides. The required proportions of the length of members of the linkage are a = 1, b = 2.5 and c = 2.
Watts Straight Line
Watt’s straight-line generator, can describe a short vertical straight line. Equal length links AB and CD are hinged at A and D, respectively. The midpoint E of connecting link BC traces a figure eight pattern over the full mechanism excursion, but a straight line is traced in part of the excursion because point E diverges to the left at the top of the stroke and to the right at the bottom of the stroke. This linkage was used by Scottish instrument maker, James Watt, in a steam-driven beam pump in about 1769, and it was a prominent mechanism in early steam-powered machines.
Watt’s linkage consists of a chain of three rods, two longer and equal length ones on the outside ends of the chain, connected by a short rod in the middle. The outer endpoints of the long rods are fixed in place relative to each other, and otherwise the three rods are free to pivot around the joints where they meet. Thus, counting the fixed-length connection between the outer endpoints as another bar, Watt’s linkage is an example of a four-bar linkage.
Link ratios are: L1 = L3. Point P is in the middle of L2
In this example: L1=4, L2=2, L3=4, P= in the middle of L2
Complex Linkage Mechanisms – Wing Flapping
Complex Linkage Mechanisms – Theo Jansen Mechanism
Theo Jansen (born 1948) is a Dutch artist. In 1990, he began what he is known for today: building large mechanisms out of PVC that are able to move on their own, known asStrandbeest.
His animated works are a fusion of art and engineering; in a car company (BMW) television commercial Jansen says: “The walls between art and engineering exist only in our minds.” He strives to equip his creations with their own artificial intelligence so they can avoid obstacles by changing course when one is detected, such as the sea itself.
ROBOTICS > Linkage – DRAFTING MECHANISM – 51023

Linkage – DRAFTING MECHANISM
A drafting machine is a very useful tool in technical drawing, consisting of a pair of scales mounted to form a right angle on an articulated protractor head that allows an angular rotation.
The protractor head (two scales and protractor mechanism) is able to move freely across the surface of the drawing board, sliding on two guides directly or indirectly anchored to the drawing board. These guides, which act separately, ensure the movement of the set in the horizontal or vertical direction of the drawing board, and can be locked independently of each other.
A drafting machine is a very useful tool in technical drawing, consisting of a pair of scales mounted to form a right angle on an articulated protractor head that allows an angular rotation.
The protractor head (two scales and protractor mechanism) is able to move freely across the surface of the drawing board, sliding on two guides directly or indirectly anchored to the drawing board. These guides, which act separately, ensure the movement of the set in the horizontal or vertical direction of the drawing board, and can be locked independently of each other.
Rotary Linear Linkages – SLIDER CRANK Mechanism
A crank is an arm attached at right angles to a rotating shaft by which reciprocating motion is imparted to or received from the shaft. It is used to convert circular motion into reciprocating motion, or vice-versa. The arm may be a bent portion of the shaft, or a separate arm or disk attached to it. Attached to the end of the crank by a pivot is a rod, usually called a connecting rod. The end of the rod attached to the crank moves in a circular motion, while the other end is usually constrained to move in a linear sliding motion.
The term often refers to a human-powered crank which is used to manually turn an axle, as in a bicycle crankset or a brace and bit drill. In this case a person’s arm or leg serves as the connecting rod, applying reciprocating force to the crank. There is usually a bar perpendicular to the other end of the arm, often with a freely rotatable handle orpedal attached.

ALTERNATIVE DESIGNS
1- Slider-crank mechanism having a pause at the end of stroke.
The tooth number of internal gear is 3 times of the one of satellite gear. The short crank’s length is half of the long crank’s one. One axle of the connecting rod draws a deltoid that consists of 3 nearly round curves. The length of the connecting rod is equal the radius of the curve.
2-Slider-Crank Mechanism with added double crank 2
The slider’s stroke length is nearly 4 times of the red crank length.
Rotary Linear Linkages – SCOTH-YOKE Mechanism
The Scotch yoke is a mechanism for converting the linear motion of a slider into rotational motion or vice-versa. The piston or other reciprocating part is directly coupled to a sliding yoke with a slot that engages a pin on the rotating part. The shape of the motion of the piston is a pure sine wave over time given a constant rotational speed.
Scotch-yoke mechanism, pictured in Fig. functions in a manner similar to that of the simple crank mechanism except that its linear output motion is sinusoidal. As wheel A, the driver, rotates, the pin or roller bearing at its periphery exerts torque within the closed yoke B; this causes the attached sliding bar to reciprocate, tracing a sinusoidal waveform. Part a shows the sliding bar when the roller is at 270°, and part b shows the sliding bar when the roller is at 0°.

Applications
This mechanism is most commonly used in control valve actuators in high pressure oil and gas pipelines. Although not a common metalworking machine nowadays, crude shapers can use a Scotch yoke. Almost all those use a Whitworth linkage, which gives a slow speed forward cutting stroke and a faster return. It has been used in various internal combustion engines, such as the Bourke engine, SyTech engine, and many hot air engines and steam engines .
GENEVA WHEEL
The Geneva drive or Maltese cross is a gear mechanism that translates a continuous rotation into an intermittent rotary motion. The rotating drive wheel has a pin that reaches into a slot of the driven wheel advancing it by one step. The drive wheel also has a raised circular blocking disc that locks the driven wheel in position between steps.
The name derives from the device’s earliest application in mechanical watches, Switzerland and Geneva being an important center of watchmaking.The Geneva drive is also commonly called a Maltese cross mechanism due to the visual resemblance when the driven wheel has four spokes. They are used in watches and for the main reason of being made small and can withstand mechanical stress.
In the most common arrangement, the driven wheel has four slots and thus advances for each rotation of the drive wheel by one step of 90°. If the driven wheel has n slots, it advances by 360°/n per full rotation of the drive wheel.
DESIGN ALTERNATIVES -Internal Geneva Drive 1
An internal Geneva drive is a variant on the design. The axis of the drive wheel of the internal drive can have a bearing only on one side. The angle by which the drive wheel has to rotate to effect one step rotation of the driven wheel is always smaller than 180° in an external Geneva drive and always greater than 180° in an internal one, where the switch time is therefore greater than the time the driven wheel stands still.
The external form is the more common, as it can be built smaller and can withstand higher mechanical stresses.
The ratio of dwell period to motion period is 1/3. Angle of each rotation of the driven shaft is 90 degrees.
DESIGN ALTERNATIVES – Inverted Geneva Mechanism
Inspired by mechanism #169 from 1800 Mechanical Movements, Devices and Appliances by Gardner D. Hiscox.
Republication by Dover Press, 2007. Simulation created in Autodesk Inventor 2012 Professional.
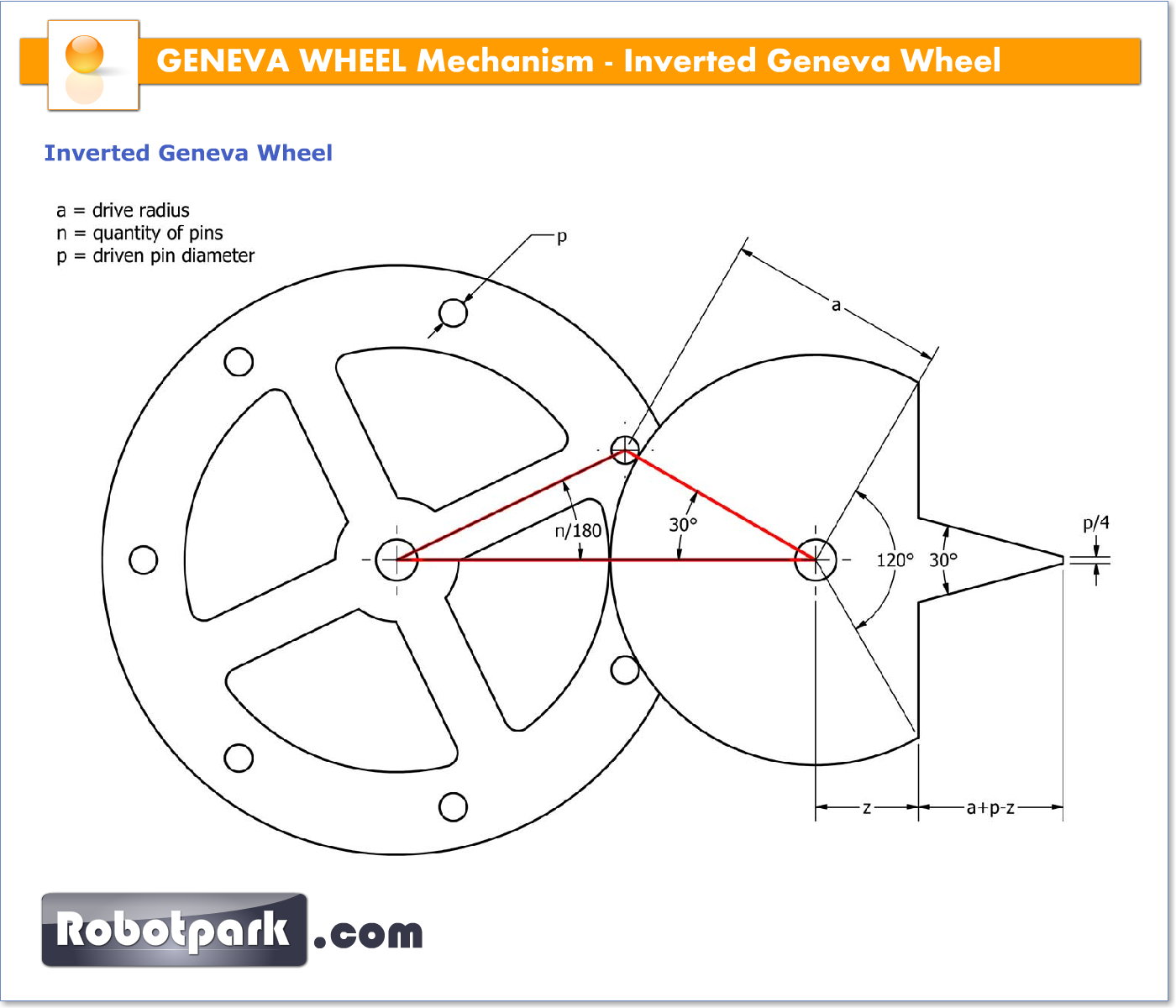
Specialized Mechanisms – WHITWORTH QUICK RETURN
The Whitworth quick return mechanism converts rotary motion into reciprocating motion, but unlike the crank and slider, the forward reciprocating motion is at a different rate than the backward stroke. At the bottom of the drive arm, the peg only has to move through a few degrees to sweep the arm from left to right, but it takes the remainder of the revolution to bring the arm back. This mechanism is most commonly seen as the drive for a shaping machine.
Robotic Mechanisms – ALL TYPES of GEARS
All gears can be classified as either external gears or internal or annual gears:
• External Gears have teeth on the outside surface of the disk or wheel.
• Internal or Annual Gears have teeth on the inside surface of a ring or cylinder.
An external gear is one with the teeth formed on the outer surface of a cylinder or cone. Conversely, an internal gear is one with the teeth formed on the inner surface of a cylinder or cone.

• Internal or Annual Gears have teeth on the inside surface of a ring or cylinder.
ALL TYPES OF GEARS
A- SPUR GEARS: are cylindrical external gears with teeth that are cut straight across the edge of the disk or wheel parallel to the axis of rotation. The spur gears shown in Fig A. are the simplest gears. They normally translate rotating motion between two parallel shafts. An internal or annual gear, is a variation of the spur gear except that its teeth are cut on the inside of a ring or flanged wheel rather than on the outside.
Robotic Mechanisms – SPUR GEARS
Spur gears or straight-cut gears are the simplest type of gear. They consist of a cylinder or disk with the teeth projecting radially, and although they are not straight-sided in form, the edge of each tooth is straight and aligned parallel to the axis of rotation. These gears can be meshed together correctly only if they are fitted to parallel shafts.
Spur Gears are Used to Control Power Transmission in These Ways
1. Changing the direction through which power is transmitted (i.e. parallel, right angles, rotating, linear etc.)
2. Changing the amount of force or torque
3. Changing RPM
Spur Gears, are cogged wheels whose cogs or teeth project radially and stand parallel to the axis.
1. Changing the direction through which power is transmitted (i.e. parallel, right angles, rotating, linear etc.)
2. Changing the amount of force or torque
3. Changing RPM
TECHNICAL DETAILS of SPUR GEARS
Diametral Pitch of Spur Gears (DP)
The Diametral Pitch describes the gear tooth size. The Diametral Pitch is expressed as the number of teeth per inch of Pitch Diameter. Larger gears have fewer teeth per inch of Diametral Pitch. Another way of saying this; Gear teeth size varies inversely with Diametral Pitch.

Pitch Diameter of Spur Gears (D)
The Pitch Diameter refers to the diameter of the pitch circle. If the gear pitch is known then the Pitch Diameter is easily calculated using the following formula;
P = N/P
PD = Pitch Diameter, N = Number of teeth on the gear, P = Diametral Pitch (Gear Size)
PD = N/P = 36 /24 = 1,5″
The Pitch Diameter is used to generate the Pitch Circle.
The Pitch Circle
The pitch circle is the geometrical starting point for designing gears and gear trains. Gear trains refer to systems of two or more meshing gears. The pitch circle is an imaginary circle that contacts the pitch circle of any other gear with which it is in mesh. The pitch circle centers are used to ensure accurate center-to-center spacing of meshing gears.
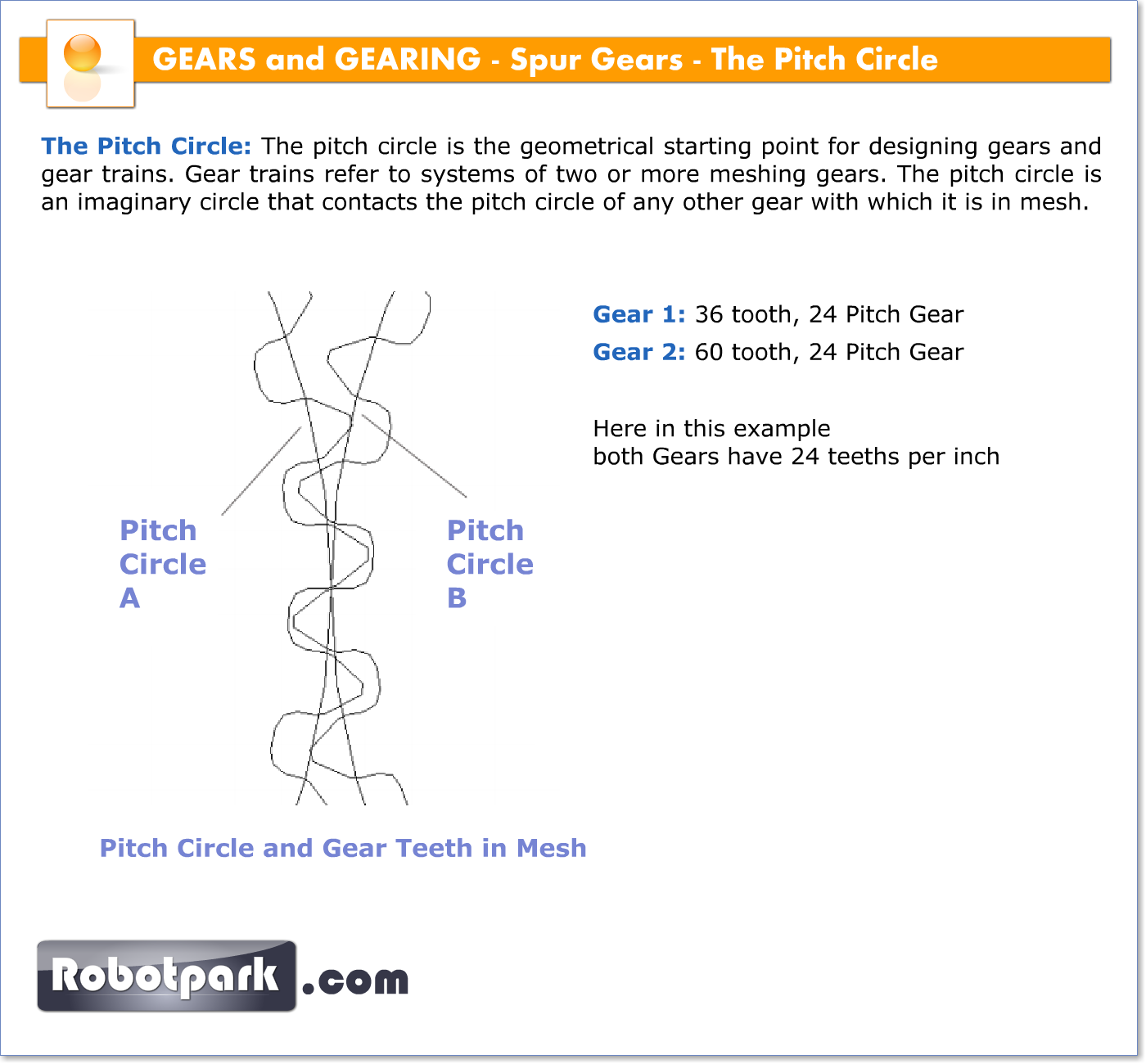
GEAR TERMS
Addendum (A): The addendum refers to the distance from the top of the tooth to the Pitch circle.
Dedendum (B): The Dedendum refers to the distance from the Pitch circle to the root circle.
Clearance (C) : Refers to the radial distance between the top and bottom of gears in mesh. Some machinists and mechanics refer to clearance as “play” or the degree of looseness between mating parts.
Whole Depth (WD) : Refers to the distance from the top of the tooth to the bottom of the tooth.
Pressure Angle (PA) (Choose either 14.5 or 20 degrees) : The pressure angle figures into the geometry or form of the gear tooth. It refers to the angle through which forces are transmitted between meshing gears. 14.5-degree tooth forms were the original “standard” gear design. While they are still widely available, the 20-degree PA gear tooth forms have wider bases and can transmit greater loads. Note: 14.5-degree PA tooth forms will not mesh with 20-degree PA teeth. Be certain to verify the Pressure angle of the gears you use.
Center Distance : The center distance of 2 spur gears is the distance from the center shaft of one spur gear to the center shaft of the other.
Spur Gear Calculations – Formulas
This is a chart of formulas used in calculating spur gear information based on standard gearing practices.
The spur gear formulas here are based on the “Diametral Pitch system (DP).
These formulas can be used with Circular Pitch and Module systems by first converting them to the Diametral Pitch
To convert a Circular Pitch (CP) to DP – Divide 3.1416 by the circular pitch
To convert the Module (Mod) to DP - Divide the 25.4 by the module
The spur gear formulas here are based on the “Diametral Pitch system (DP).
These formulas can be used with Circular Pitch and Module systems by first converting them to the Diametral Pitch
To convert the Module (Mod) to DP - Divide the 25.4 by the module
Diametral Pitch | The circular pitch | Divide 3.1416 by the circular pitch |
Pd = 3.1416 / CP
|
Diametral Pitch |
| Divide the number of teeth by the pitch diameter |
Pd = N / D
|
Diametral Pitch |
| Divide number of teeth + 2 by the outside diameter |
Pd = (N+2) / OD
|
Diametral Pitch |
| Divide the base pitch by the cosine of the pressure angle then divide by 3.1416 |
Pd = (BP / Cos PA) / 3.1416
|
Pitch Diameter |
| Divide the number of teeth by the diametral pitch |
D = N / Pd
|
Pitch Diameter |
| Divide the product of the outside diameter + number of teeth by the number of teeth + 2 |
D = (OD x N) / (N+2)
|
Pitch Diameter |
| Subtract 2 divided by the diametral pitch from the outside diameter |
D = OD – (2/ Pd)
|
Pitch Diameter |
| Multiply addendum by the number of teeth |
D = A x N
|
Pitch Diameter |
| Divide the base diameter by the cosine of the pressure angle |
D = BD / (Cos Pa)
|
Outside Diameter |
| Divide number of teeth + 2 by the diametral pitch |
OD = (N+2) / Pd
|
Outside Diameter |
| Two divided by the diametral pitch plus pitch diameter |
OD = (2 / Pd) + D
|
Outside Diameter |
| Number of teeth + 2, divided by the quotient of number of teeth divided by the pitch diameter |
OD = (N+2) / (N / D)
|
Outside Diameter |
| Multiply the number of teeth + 2 by the addendum |
OD = (N + 2) x A
|
Number Of Teeth |
| Multiply the pitch diameter by the diametral pitch |
N = D x Pd
|
Number Of Teeth |
| Multiply the outside diameter by the diametral pitch and subtract 2 |
N = (OD x Pd) – 2
|
Thickness Of Tooth |
| Divide 1.5708 by the diametral pitch |
t = 1.5708 / Pd
|
Addendum |
| Divide 1 by the diametral pitch |
a = 1 / Pd
|
Dedendum |
| Divide 1.157 (or 1.25) by the diametral pitch |
b = 1.157 / Pd
|
Working Depth |
| Divide 2 by the diametral pitch |
hk = 2 / Pd
|
Whole Depth |
| Divide 2.157 (or 2.25) by the diametral pitch |
ht = 2.157 / Pd
|
Clearance |
| Divide .157 (or .250) by the diametral pitch |
c = .157 / Pd
|
Clearance |
| Divide thickness of tooth at the pitchline by 10 |
c = t / 10
|
Operating Diametral Pitch |
| Add the number of teeth in both gears and divide by 2 then divide by the center distance |
PdO = ((n1 + n2)/2) / C
|
Center Distance |
| Add the number of teeth in both gears and divide by 2 then divide by the normal diametral pitch |
C = ((n1 + n2)/2) / Pnd
|
Operating Center Distance |
| Add the number of teeth in both gears and divide by 2 then divide by the operating diametral pitch |
Co = ((n1 + n2)/2) / Pod
|
Base Diameter |
| Multiply the pitch diameter by the cosine of the pressure angle |
Db = PD x (cos PA)
|
Pressure Angle |
| Divide the base diameter by the pitch diameter |
cosPA = Db / D
|
Pressure Angle |
| Divide Pi by the diametral pitch, then divide by the base pitch |
cosPA = (3.1416 / Pd) / Pb
|
Base Pitch |
| Divide the diametral pitch by Pi, then multiply by the cosine of the pressure angle |
Pb = (Pd / 3.1416) x (cos PA)
|
BalasHapusI am glad to find amazing information from the blog. Thanks for sharing the information. Hydraulic Power Pack Manufacturers in India | Hydraulic Cylinder Manufacturers in India