The development of science and technology in the field
Of Electronic Engineering
I . instrumentation and control electronics
1. control of positioning sensor
2. sequence control of actuator (transducer output)
3. control of motor actuator
4. Servo feedback mechanism control
5. Transfer line with a Robotic
6. Sensor detection (control technology)
7. positioning by motor servo feedback
8. Rotating speed motor servo control
9. Process control of water temperature
10. Stepping motor driving technology
11. DC motor servo driving technology
12. Driving of pneumatic chip handling mechanism
13. Play melody by pneumatic driving
14. Drive of Robot Arm mechanism
15. AD / DA conversion program control
16. Air sequence control technique
17. combine mechanism and transmission
18. Triaxial control Robot
19. Complex mechanism and articulated Robot
20. elevator (complex mechanism)
22. Belt Screw positioning control
23 . Rotation angle control
24. Transfer speed control
25. Transfer by the pick and place mechanism
26. transfer by the chip stocker
27. color discriminant and separation on the transfer line
28. Simplified the complex mechanism
29. stepping motor and induction motor count rolling
30. speed control motor measurements
31. Air cylinder measurements
32. sensor control and characteristics
33. Transducer control of input and output systems
II . SIGNAL TRANSFER
1.
Modern communication of visible laser optical
transmission
2.
PWM / PFM transmission of analog measurement
output
3.
PCM signal transmission of analog waveform
4.
Control of digital signal transmission
5.
Personal computer communication
6.
Complex information communication of optical
multi transmission
7.
Remote monitoring and controlling
8.
Conversion of waveform
9.
Modulation and demodulation of PWM and PFM waves
10.
Parallel signal transmission
11.
Analogue and Digital conversion so do D/A
Conversion
12.
Modern
Function in PC communication
13.
Optical communication
14.
Equipment in Optical communication
III .
ELECTRONICS OR PROCESSING COMPONNENT
1.
Semiconductor device
2.
Hall Effect device
3.
Sensor probe and characteristics
4.
Pulse circuit
5.
DC stabilized power source circuit
6.
Active filter circuit
7.
Transistor or diode circuit
8.
Operational Amplifier
9.
Frequency Modulation and demodulation
10.
Amplitude modulation and detection
11.
Power electronic control technology
12.
Relay circuit and good concept
13.
Development Logic circuit
14.
Development Operational Amplifier circuit
15.
Principle of AD / DA conversion
16.
Logic circuit with surface mount technology
17.
Various electronic
circuit and development
18.
Various automatic control instruments
19.
Electronics concept of Magnetic converse Electric or Electric converse Magnetic
20.
Electric Instrumentation
21.
Various Wave form and application to electronics
case study
22.
Electric Power
AND analog automatic
23.
Data acquisition
III .
ELECTRONIC IN PHYSICS
1.
Speed of Light
2.
Measurement of gravitational
3.
Measurement of gravitational acceleration
4.
Wave propagation
5.
Ultrasonic Wave length and phase
6.
Measurement of sound speed
7.
Young’s modulus
8.
Torsional rigidity
9.
Surface tension
10.
Liquid specific heat by cooling method
11.
Gas specific heat
12.
Linier expansion coefficient
13.
Hot air engine
14.
Lens curvature
15.
Light wavelength
16.
Faraday effect
17.
Prism property
18.
Atomic spectrum wavelength
19.
Polarimeter of crystal
20.
Optical device characteristic
21.
Light wavelength strength distribution
22.
Temperature coefficient of metal resistance
23.
Superconductive phenomenon
24.
Electrolytic
25.
LC resonance circuit
26.
Thermo electric power
27.
Electron specific charge
28.
Electric charge Planck’s constant
29.
Radiation track
XXX . XXX How collaborative robots can work alongside humans and offer assistance proactively
With automation accelerating around the world, according to the International Federation of Robotics, one of the fastest growing segments of the industrial robotics market is that associated with collaborative robots.
Growth is being driven by a combination of stronger-than-expected growth in the global economy, faster business cycles, greater variety in customer demand and the scaling up of Industry 4.0 concepts.
One of the leading UK developers of ‘collaborative robotics’ is Ocado Technology, which develops the software and systems that power the online grocery retail platforms of ocado.com and Morrisons, the UK’s fourth largest supermarket chain.
Ocado is involved with a growing number of high-profile research projects, including the SoMa soft manipulation system and the SecondHands technician collaborative robot.
Humanoid robotsWhile the SoMa project is looking to develop smart and generalised solutions and systems capable of picking out thousands of different grocery items safely and reliably, the SecondHands humanoid robotic project is being developed to help engineers fix mechanical faults and even learn on the job.
“The SecondHands project is intended to assist Ocado’s maintenance technicians and crucially, and most excitingly, anticipate the needs of human operatives,” explains Graham Deacon, who heads Ocado’s robotics research team.
“The robot is intended to be completely autonomous and to be able to perform a variety of tasks from fetching tools to holding objects as well as assisting with cleaning and engineering tasks.”
The robot – described as a ‘second pair’ of hands – will be able to assist technicians and, through observation, augment human capabilities.
“It is intended to complete tasks that require levels of precision and physical strength that are not available to humans,” Deacon says.
“The SecondHands project is a European collaboration between Ocado and four EU universities and it would be fair to say that it is one of the most advanced assistive robot projects in the world,” according to Deacon.

European project
Ocado is co-ordinating this European-wide project, funded by the EU to the tune of €7million. The investment forms part of its Horizon2020 initiative to encourage researchers to work more closely with industrial partners.
“While we are co-ordinating and contributing to the research, Ocado will ultimately be the end user and the robots have been designed specifically for our warehouses, or Customer Fulfilment Centres (CFCs).” explains Deacon.
A SecondHands robot prototype was delivered to Ocado’s robotics research lab in late 2017 and, earlier this year, a prototype robot was put through its paces in front of EU officials.
“While there is still plenty of work to do,” concedes Deacon, ”the past few months have provided us with the opportunity to evaluate and then integrate the various research components from the various project partners.”
Those research partners have combined to develop what is described as a real-world solution which has required them to not only take into account the design of a new robotic assistant, but also one that facilitates proactive help, supports a degree of human-robot interaction and the development of advanced perception skills to function in dynamic industrial environments.
Ocado’s research partners include: École Polytechnique Fédérale de Lausanne (EPFL); Karlsruhe Institute of Technology’s (KIT) Interactive Systems Lab (ISL) and its High Performance Humanoid Technologies Lab (H²T); the Sapienza Università di Roma; and University College London (UCL). Various research groups have been focused on computer vision and cognition, human-robot interaction, mechatronics, and perception.
“We want to demonstrate the versatility and productivity that human-robot collaboration can deliver in practice,” explains Deacon.
The research contributions for each of the project partners include:
• EPFL: human-robot physical interaction with bi-manipulation, including action skills learning;
• KIT (H²T): Development of the ARMAR-6 robot, including its entire mechatronics, software operating system and control as well as robot grasping and manipulation skills;
• KIT (ISL): the spoken dialogue management system;
• Sapienza University of Rome: visual scene perception with human action recognition, cognitive decision making, task planning and execution with continuous monitoring; and
• UCL: computer vision techniques for 3D human pose estimation and semantic 3D reconstruction of dynamic scenes.
“Ocado is responsible for the integration of these different functionalities and for the evaluation of the platform,” says Deacon.
While Deacon concedes that while more work needs to be done following the presentation to the EU representatives, it was important that the platform was pulled together.
The SecondHands robot is based on KIT’s next-generation ARMAR robot. “The fact the SecondHands robot has been developed across various sites using different laboratories, tools and facilities, means the project has been complex. But, despite that, everything was ready for January this year.”
As robots evolve from industrial machines performing repetitive tasks in isolated areas of large-scale factories to more complex systems powered by deep neural networks, the SecondHands project has been set the challenging goal of developing, collaborative robots that can interact safely and intelligently with their human counterparts in real-world environments.
“When it comes to maintenance tasks in Ocado’s network of warehouses,” says Deacon, “when something goes wrong with a mechanical component, we want the SecondHands robot to step in and help engineers carry out repairs quickly and safely.
“It should be able to operate in areas deemed too dangerous for humans – examining high-speed conveyors at close quarters, for example, or handling toxic material.”
More importantly, the team expect the robots to track what an engineer is doing, understand the task the engineer is trying to perform and then synthetically understand its own capabilities as a robot to offer assistance proactively.
“SecondHands’ potential for high-level reasoning,” Deacon explains, “is a work of artificial intelligence.”
He explains that software will help the robot construct a vast knowledge base around the tasks it carries out to better understand how they can be applied to problems. “In this sense, the robot will learn on the job,” he concludes.
One of the leading UK developers of ‘collaborative robotics’ is Ocado Technology, which develops the software and systems that power the online grocery retail platforms of ocado.com and Morrisons, the UK’s fourth largest supermarket chain.
Ocado is involved with a growing number of high-profile research projects, including the SoMa soft manipulation system and the SecondHands technician collaborative robot.
Humanoid robotsWhile the SoMa project is looking to develop smart and generalised solutions and systems capable of picking out thousands of different grocery items safely and reliably, the SecondHands humanoid robotic project is being developed to help engineers fix mechanical faults and even learn on the job.
“The SecondHands project is intended to assist Ocado’s maintenance technicians and crucially, and most excitingly, anticipate the needs of human operatives,” explains Graham Deacon, who heads Ocado’s robotics research team.
“The robot is intended to be completely autonomous and to be able to perform a variety of tasks from fetching tools to holding objects as well as assisting with cleaning and engineering tasks.”
The robot – described as a ‘second pair’ of hands – will be able to assist technicians and, through observation, augment human capabilities.
“It is intended to complete tasks that require levels of precision and physical strength that are not available to humans,” Deacon says.
“The SecondHands project is a European collaboration between Ocado and four EU universities and it would be fair to say that it is one of the most advanced assistive robot projects in the world,” according to Deacon.

The SecondHands robot is intended to help technicians in a proactive manner |
Ocado is co-ordinating this European-wide project, funded by the EU to the tune of €7million. The investment forms part of its Horizon2020 initiative to encourage researchers to work more closely with industrial partners.
“While we are co-ordinating and contributing to the research, Ocado will ultimately be the end user and the robots have been designed specifically for our warehouses, or Customer Fulfilment Centres (CFCs).” explains Deacon.
A SecondHands robot prototype was delivered to Ocado’s robotics research lab in late 2017 and, earlier this year, a prototype robot was put through its paces in front of EU officials.
“While there is still plenty of work to do,” concedes Deacon, ”the past few months have provided us with the opportunity to evaluate and then integrate the various research components from the various project partners.”
Those research partners have combined to develop what is described as a real-world solution which has required them to not only take into account the design of a new robotic assistant, but also one that facilitates proactive help, supports a degree of human-robot interaction and the development of advanced perception skills to function in dynamic industrial environments.
Ocado’s research partners include: École Polytechnique Fédérale de Lausanne (EPFL); Karlsruhe Institute of Technology’s (KIT) Interactive Systems Lab (ISL) and its High Performance Humanoid Technologies Lab (H²T); the Sapienza Università di Roma; and University College London (UCL). Various research groups have been focused on computer vision and cognition, human-robot interaction, mechatronics, and perception.
“We want to demonstrate the versatility and productivity that human-robot collaboration can deliver in practice,” explains Deacon.
The research contributions for each of the project partners include:
• EPFL: human-robot physical interaction with bi-manipulation, including action skills learning;
• KIT (H²T): Development of the ARMAR-6 robot, including its entire mechatronics, software operating system and control as well as robot grasping and manipulation skills;
• KIT (ISL): the spoken dialogue management system;
• Sapienza University of Rome: visual scene perception with human action recognition, cognitive decision making, task planning and execution with continuous monitoring; and
• UCL: computer vision techniques for 3D human pose estimation and semantic 3D reconstruction of dynamic scenes.
“Ocado is responsible for the integration of these different functionalities and for the evaluation of the platform,” says Deacon.
While Deacon concedes that while more work needs to be done following the presentation to the EU representatives, it was important that the platform was pulled together.
The SecondHands robot is based on KIT’s next-generation ARMAR robot. “The fact the SecondHands robot has been developed across various sites using different laboratories, tools and facilities, means the project has been complex. But, despite that, everything was ready for January this year.”
"When something goes wrong ... we want the SecondHands robot to step in and help engineers to carry out repairs quickly and safely." |
“When it comes to maintenance tasks in Ocado’s network of warehouses,” says Deacon, “when something goes wrong with a mechanical component, we want the SecondHands robot to step in and help engineers carry out repairs quickly and safely.
“It should be able to operate in areas deemed too dangerous for humans – examining high-speed conveyors at close quarters, for example, or handling toxic material.”
More importantly, the team expect the robots to track what an engineer is doing, understand the task the engineer is trying to perform and then synthetically understand its own capabilities as a robot to offer assistance proactively.
“SecondHands’ potential for high-level reasoning,” Deacon explains, “is a work of artificial intelligence.”
He explains that software will help the robot construct a vast knowledge base around the tasks it carries out to better understand how they can be applied to problems. “In this sense, the robot will learn on the job,” he concludes.
XXX . XXX 4%zero Augmented reality could be a game changer in PCB design
In the future transparent screens could enable AR supported PCB design
Augmented reality is an old technology with new hopes – and could change the face of electronic design.
The markets for augmented and virtual reality (AR/VR) are thriving, with market researcher IDC predicting demand for both will reach $17.8billion in 2018.
While VR is making rapid inroads into the consumer electronics world, AR is poised to have a similar impact in industry – and PCB design is one of the potential beneficiaries, where it could address issues such as fitting electronic packages into unconventional shapes, ensuring circuit connections work properly and reducing the time-consuming process of place and route.
Unlike VR, which fully immerses the user in a digital world, AR sees digital content overlaid onto the existing reality. Virtual objects are oriented so they appear to have real places in the world.
If electronic design could benefit from AR, the question is why hasn’t it been put into practice already?
“People are solving software issues where there is high value,” David Harold, VP marketing and communications at Imagination Technologies, said. “They will pay for the issues they want to be resolved, such as ones that aid protection and health.”
Harold highlighted several areas where he believes AR could be used in the future. The first he labelled ‘procedure’; the idea that a designer could flick between the finished, virtual version of a board and the real-life work-in-progress. He suggested this could help the designer establish what still needs to be done and remind them of the finished article.
The second area is ‘non-distraction’. “People forget how finely detailed some of the work we do is,” he said. “The ability to have a set of virtual instructions in your field of vision, so you don’t have to keep manually turning pages would be very useful.” He described a theoretical system where a user could access a ‘tunnel’ view, in which areas of their vision could be darkened in favour of particular highlighted areas.
He also proposed combining AR with artificial intelligence (AI), offering a scenario in which an AR AI-enabled system could recognise the parts a designer was working on and provide optimisations. This imagined system could suggest alternatives, identify missing elements, offer solutions others have solved and shared previously, as well as search and highlight stress and failure points in a design.
The ability for an AR system to distinguish between necessary and needless motions would also be crucial in electronic design. Real world movement isn’t always logical, so a system would have to be intelligent enough to categorise these, so to avoid delay and error.

“Ultimately,” said Harold, “the technologies being developed in the health and consumer markets will start to trickle through to other industries.”
Heather Macdonald Tait, marketing communications specialist at Ultrahaptics, believes one reason why AR has not been implemented in electronic design is due to the ‘chicken and egg situation’ between software and hardware development. “We need the right tools to develop content,” she explained. “But we also need the hardware to support it and this has affected market acceptance.”
Ultrahaptics’ technology enables haptic feedback in mid-air. Using a speaker array controlled by an FPGA and a microcontroller, ultrasound is emitted at 40kHz. The system controls when each speaker fires, creating an array of pressure points which enables a user to ‘feel’ a virtual object.
“Until we add a mechanism for interacting in a collaborative way,” an Ultrahaptics applications engineer, added, “I don’t think we’re opening up the full potential of AR and VR. We believe we are opening that potential with haptics and it’s up to people using this tool to leverage the technology.”
Altium is also experimenting with ways AR can be used in design. In previous tests, it linked 3D glasses to the 3D PCB editor view in its software, so the designer’s facial position could augment the control of the PCB design workspace. However, it was never carried beyond experimental phase because it was hard to establish any true value or efficiency gains.
“It’ll take time for electronic engineers to think of ways in which AR could help them day-to-day. We’re waiting for some better technology,” Ben Jordan, senior manager product and persona marketing at Altium, said. “It’s like the laser; they didn’t know what to do with it at first and now it’s everywhere.”
While VR is making rapid inroads into the consumer electronics world, AR is poised to have a similar impact in industry – and PCB design is one of the potential beneficiaries, where it could address issues such as fitting electronic packages into unconventional shapes, ensuring circuit connections work properly and reducing the time-consuming process of place and route.
Unlike VR, which fully immerses the user in a digital world, AR sees digital content overlaid onto the existing reality. Virtual objects are oriented so they appear to have real
If electronic design could benefit from AR, the question is why hasn’t it been put into practice already?
“People are solving software issues where there is high value,” David Harold, VP marketing and communications at Imagination Technologies, said. “They will pay for the issues they want to be resolved, such as ones that aid protection and health.”
Harold highlighted several areas where he believes AR could be used in the future. The first he labelled ‘procedure’; the idea that a designer could flick between the finished, virtual version of a board and the real-life work-in-progress. He suggested this could help the designer establish what still needs to be done and remind them of the finished article.
The second area is ‘non-distraction’. “People forget how finely detailed some of the work we do is,” he said. “The ability to have a set of virtual instructions in your field of vision, so you don’t have to keep manually turning pages would be very useful.” He described a theoretical system where a user could access a ‘tunnel’ view, in which areas of their vision could be darkened in favour of particular highlighted areas.
He also proposed combining AR with artificial intelligence (AI), offering a scenario in which an AR AI-enabled system could recognise the parts a designer was working on and provide optimisations. This imagined system could suggest alternatives, identify missing elements, offer solutions others have solved and shared previously, as well as search and highlight stress and failure points in a design.
The ability for an AR system to distinguish between necessary and needless motions would also be crucial in electronic design. Real world movement isn’t always logical, so a system would have to be intelligent enough to categorise these, so to avoid delay and error.

“Ultimately,” said Harold, “the technologies being developed in the health and consumer markets will start to trickle through to other industries.”
Heather Macdonald Tait, marketing communications specialist at Ultrahaptics, believes one reason why AR has not been implemented in electronic design is due to the ‘chicken and egg situation’ between software and hardware development. “We need the right tools to develop content,” she explained. “But we also need the hardware to support it and this has affected market acceptance.”
Above: AR is already being used in an industrial setting for tasks such as fault-finding, but has yet to reach its full potential in PCB design |
“Until we add a mechanism for interacting in a collaborative way,” an Ultrahaptics applications engineer, added, “I don’t think we’re opening up the full potential of AR and VR. We believe we are opening that potential with haptics and it’s up to people using this tool to leverage the technology.”
Altium is also experimenting with ways AR can be used in design. In previous tests, it linked 3D glasses to the 3D PCB editor view in its software, so the designer’s facial position could augment the control of the PCB design workspace. However, it was never carried beyond experimental phase because it was hard to establish any true value or efficiency gains.
“It’ll take time for electronic engineers to think of ways in which AR could help them day-to-day. We’re waiting for some better technology,” Ben Jordan, senior manager product and persona marketing at Altium, said. “It’s like the laser; they didn’t know what to do with it at first and now it’s everywhere.”
the answer could lie in the creation of light emitting touchscreens. He imagines a technology where an image would be projected in front of the user, allowing them to interact through gestures. “One day, we’ll design software into transparent touchscreens and people will be able to hold them over a prototype of a board and plug it in. There will be test applications where designers can verify their work in prototype against the actual design in the software simultaneously.”
He also explored the idea of training and using AR with simulation software. He suggested augmented PCBs could be used in the future to reduce cost and wastage of material used in current training methods, as well as for replicating magnetic and electric fields generated by a product as alternative way to ensure a product would meet regulations
“AR could . “ For example, a product designer may create a clay mockup of the product idea and then the electronics designer may use AR views of that mockup combined with the clusters of parts in the PCB design software in real-time to begin shaping the PCBs and figuring out where some of the bulkier components would fit inside of it, or make alternative part choices to replace them with smaller components.
“Much like the integration of 3D into PCB design would have been in the late 1980s, AR is a solution to problems we probably don’t yet have, . “Today, everyone knows you must have 3D PCB design viewers at a bare minimum for efficient design, but that was not so obvious 20 years ago. As the technology and our design patterns evolve, it will become more apparent,” Jordan ventured.
“ could see that AR will become far more useful for PCB design as 3D MID technology becomes mainstream,” he continued. MIDs – Mechatronic Integrated Devices – are 3D bodies with integrated circuit structures. “With the 3D MIDs, you want to take a plastic or clay mockup of the moulded shape and, with the CAD and an AR camera view, in 3D, superimpose the track routing and component placements.”
“But maybe that isn’t necessary,” he countered. “You could simply bring in the STEP or Parasolid model of the MID design into the editor environment, place the parts and route them. Only time will tell.”
While AR may have a place in electronic design in the future, it seems that progress needs to be made in developing suitable hardware.
XXX . XXX 4%zero null 0 1 2 Enabling the adaptable world
The intelligent connected world needs adaptable accelerated computing. As a result, more engineers are turning to FPGA as a Service providers via the cloud.
The rise of what is being described as the intelligent connected world has brought with it an explosion in data, the growing adoption of artificial intelligence and a move to more heterogeneous computing.
The electronics industry is seeing exponential change and that brings with it certain challenges; in particular, having to address the fact that the speed of innovation is now beginning to outpace silicon design cycles. This brings a growing need for acceleration and a move towards programmable logic and FPGAs.
These devices can provide massive computational throughput with very low latency, which means they can process data at wire speeds and implement complex digital computations, with power and cooling requirements an order of magnitude less than than either CPUs or GPUs.
Earlier in 2018, at a developers’ forum in Frankfurt, Xilinx’s senior director for software and IP, The design teams were increasingly turning to FPGAs when CPU architectures are seen to be failing to meet the demands of increasing workloads.
“As CPU architectures fail to meet demand, so there’s growing interest in heterogeneous computing with accelerators. The breadth of apps being developed is also requiring different architectures. Designers are addressing the need for both higher performance and lower latency and, while we saw a move to multicore architectures to address this, we’re now seeing multicore architecture scaling beginning to flatten.”
With the but : “Whether for video, machine learning or search applications, we have reached a point when specific accelerators can no longer be justified on economic grounds. Why? Because workloads are becoming more diverse and demand is constantly changing.” there’s been a move away from application specific accelerators towards more reconfigurable ones and that trend has played to the strengths of FPGAs and SoCs.
“By using FPGAs, it is possible to provide configurable processor sub-systems and hardware that can be reconfigured dynamically. Their key advantages are that design engineers can build their own custom data flow graph, which can be customized to their own application with its own custom memory hierarchy, which is probably the biggest advantage as it lets you keep data internal to your pipeline
While FPGAs can offer massive computational advantages, programming them has traditionally been be seen as a challenge, despite various application tools being available.
Designers have also been put off using FPGAs as, traditionally, they have needed large investments in dedicated hardware to develop custom designs and hardware prototypes, run large scale simulations and test and debugg hardware accelerated codes.
we conceded the cost of FPGA engineering is an important reason why they haven’t become more mainstream and pointed to the complexity of programming them. Analysts have suggested that FPGA technology has, to a degree, been self-limiting because of the perceived complexity.
In an increasingly data driven world, Intel and Xilinx are developing partner ecosystems and are looking to deliver a much richer development stack so hardware, embedded and application software developers will be able to program FPGAs more easily by using higher level programming options, like C, C++ and OpenCL.
“We are now able to deliver a development stack that designers are increasingly familiar with and which is available on the Cloud via secure cloud services platforms .
The growing role of the Cloud
To increase application processing speeds, hardware acceleration is being helped by Cloud platforms such as Amazon Web Services’ (AWS) FPGA EC2 F1 instances. This new type of compute instance can be used to create hardware accelerations for specific applications.
F1 comes with the tools which will be needed to develop, simulate, debug and compile hardware acceleration code and it includes an FPGA Developer AMI and Hardware Developer Kit.
“Pre-built with FPGA development tools and run time tools to develop and use custom FPGAs for hardware acceleration, our FPGA developer AMI provides users with access to scripts and tools for simulating FPGA designs and compiling code,”
F1 instances include 16nm Xilinx UltraScale Plus FPGAs with each FPGA including local 64Gbit DDR4 ECC protected memory, with a dedicated PCIe x16 connection,” Hutt explained. “The ability to code applications in C, C++, and OpenCL programming languages is possible through the availability of Xilinx’s SDAccel development environment.”
Each FPGA contains 2.5million logic elements and approximately 6800 DSP engines.
we appreciation : “AWS will allow your company to ‘get out of IT’ and focus on providing specialised services where you can add value. It means you can focus on your core business.”
The benefit of using EC2 F1 instances, added, are that it’s a quick way to deploy custom hardware solutions. “Literally with just a few clicks in the platform’s management console,” he claimed.
Because F1 instances can have one or more AFIs associated with them, designers will have much greater speed and agility and be able to run multiple accelerations on the same instance. “It’s also very predictable.
Connected via a dedicated PCI Express fabric, FPGAs can share the same memory space and communicate with each other at up to speeds of 12Gbit/s. The design ensures that only the application’s logic is running on the FPGA while the developers are using it; possible because the PCI Express fabric is isolated from other networks and FPGAs are not shared across instances, users or accounts.
With respect to EC2 F1 instances, Hutt made the point that it is possible to deploy hardware acceleration without having to buy FPGAs or specialised hardware to run them. “That reduces the cost of deploying hardware accelerations for an application dramatically.”
“There’s a tremendous opportunity for FPGAs to shine in a number of areas,” The concluded. “It’s about democratising FPGA development and increasing the number of use cases. The platform is continually evolving and I believe users are turning to F1 because it offers access to thousands of servers in a matter of seconds, which means you can roll out applications quicker, complete your work faster and cut costs.”
XXX . XXX 4%zero null 0 1 2 3 4 EMC basics and practical PCB design tips
The electronics industry is seeing exponential change and that brings with it certain challenges; in particular, having to address the fact that the speed of innovation is now beginning to outpace silicon design cycles. This brings a growing need for acceleration and a move towards programmable logic and FPGAs.
These devices can provide massive computational throughput with very low latency, which means they can process data at wire speeds and implement complex digital computations, with power and cooling requirements an order of magnitude less than than either CPUs or GPUs.
Earlier in 2018, at a developers’ forum in Frankfurt, Xilinx’s senior director for software and IP, The design teams were increasingly turning to FPGAs when CPU architectures are seen to be failing to meet the demands of increasing workloads.
“As CPU architectures fail to meet demand, so there’s growing interest in heterogeneous computing with accelerators. The breadth of apps being developed is also requiring different architectures. Designers are addressing the need for both higher performance and lower latency and, while we saw a move to multicore architectures to address this, we’re now seeing multicore architecture scaling beginning to flatten.”
With the but : “Whether for video, machine learning or search applications, we have reached a point when specific accelerators can no longer be justified on economic grounds. Why? Because workloads are becoming more diverse and demand is constantly changing.” there’s been a move away from application specific accelerators towards more reconfigurable ones and that trend has played to the strengths of FPGAs and SoCs.
“By using FPGAs, it is possible to provide configurable processor sub-systems and hardware that can be reconfigured dynamically. Their key advantages are that design engineers can build their own custom data flow graph, which can be customized to their own application with its own custom memory hierarchy, which is probably the biggest advantage as it lets you keep data internal to your pipeline
While FPGAs can offer massive computational advantages, programming them has traditionally been be seen as a challenge, despite various application tools being available.
Designers have also been put off using FPGAs as, traditionally, they have needed large investments in dedicated hardware to develop custom designs and hardware prototypes, run large scale simulations and test and debugg hardware accelerated codes.
we conceded the cost of FPGA engineering is an important reason why they haven’t become more mainstream and pointed to the complexity of programming them. Analysts have suggested that FPGA technology has, to a degree, been self-limiting because of the perceived complexity.
In an increasingly data driven world, Intel and Xilinx are developing partner ecosystems and are looking to deliver a much richer development stack so hardware, embedded and application software developers will be able to program FPGAs more easily by using higher level programming options, like C, C++ and OpenCL.
“We are now able to deliver a development stack that designers are increasingly familiar with and which is available on the Cloud via secure cloud services platforms .
The growing role of the Cloud
To increase application processing speeds, hardware acceleration is being helped by Cloud platforms such as Amazon Web Services’ (AWS) FPGA EC2 F1 instances. This new type of compute instance can be used to create hardware accelerations for specific applications.
F1 comes with the tools which will be needed to develop, simulate, debug and compile hardware acceleration code and it includes an FPGA Developer AMI and Hardware Developer Kit.
“Pre-built with FPGA development tools and run time tools to develop and use custom FPGAs for hardware acceleration, our FPGA developer AMI provides users with access to scripts and tools for simulating FPGA designs and compiling code,”
F1 instances include 16nm Xilinx UltraScale Plus FPGAs with each FPGA including local 64Gbit DDR4 ECC protected memory, with a dedicated PCIe x16 connection,” Hutt explained. “The ability to code applications in C, C++, and OpenCL programming languages is possible through the availability of Xilinx’s SDAccel development environment.”
Each FPGA contains 2.5million logic elements and approximately 6800 DSP engines.
we appreciation : “AWS will allow your company to ‘get out of IT’ and focus on providing specialised services where you can add value. It means you can focus on your core business.”
The benefit of using EC2 F1 instances, added, are that it’s a quick way to deploy custom hardware solutions. “Literally with just a few clicks in the platform’s management console,” he claimed.
Because F1 instances can have one or more AFIs associated with them, designers will have much greater speed and agility and be able to run multiple accelerations on the same instance. “It’s also very predictable.
Connected via a dedicated PCI Express fabric, FPGAs can share the same memory space and communicate with each other at up to speeds of 12Gbit/s. The design ensures that only the application’s logic is running on the FPGA while the developers are using it; possible because the PCI Express fabric is isolated from other networks and FPGAs are not shared across instances, users or accounts.
With respect to EC2 F1 instances, Hutt made the point that it is possible to deploy hardware acceleration without having to buy FPGAs or specialised hardware to run them. “That reduces the cost of deploying hardware accelerations for an application dramatically.”
“There’s a tremendous opportunity for FPGAs to shine in a number of areas,” The concluded. “It’s about democratising FPGA development and increasing the number of use cases. The platform is continually evolving and I believe users are turning to F1 because it offers access to thousands of servers in a matter of seconds, which means you can roll out applications quicker, complete your work faster and cut costs.”
XXX . XXX 4%zero null 0 1 2 3 4 EMC basics and practical PCB design tips
Differential mode radiation
Though often used as synonyms, Electromagnetic Compatibility (EMC) is really the controlling of radiated and conducted Electromagnetic Interference (EMI); and poor EMC is one of the main reasons for PCB re-designs. Indeed, an estimated 50% of first-run boards fail because they either emit unwanted EM and/or are susceptible to it.
That failure rate, however, is not across all sectors. This is most likely because of stringent regulations in some sectors, such as medical and aerospace, or because the products being developed are to join a product line that has historically been designed with EMC in mind. For instance, mobile phone developers live and breathe wireless connectivity and are well versed in minimising the risk of unwanted radiations .
Those most falling foul of EMC issues are the designers of PCBs intended for white goods - such as toasters, fridges and washing machines – which are joining the plethora of internet-enabled devices connected wirelessly to the IoT. Also, because of the potentially high volumes involved, re-spinning PCBs can introduce product launch delays. Worse still, product recalls could be very damaging to the company’s reputation and finances.
Where’s noise coming from?
There is no shortage of guidance on designing with EMC in mind, and many companies have their own in-house PCB design and EMC rules. Guidance can also come from external sources, such as legislative bodies, IC vendors and customers. However, accepting all guidelines at face value can lead to an over-defensive EMC strategy, and introduce project delays. Rules should be evaluated individually to determine if they apply to the current design.
That said, your basic, common sense rules will always apply. For instance, to supress noise sources on a PCB you should:
• Keep clock frequencies as low as possible and rising edges as slow as possible (within the scope of the requirements spec’);
• Place the clock circuit at the centre of the board unless the clock must also leave the board (in which case place it close to the relevant connector);
• Mount clock crystals flush with the board and ground them;
• Keep clock loop areas as small as possible;
• Locate I/O drivers near to the point at which the signals enter/leave the board; and
• Filter all signals entering the board.
While the above measures will help mitigate against some of the most common EMI issues, every powered PCB will still radiate EM energy. This is because every current produces a magnetic field and every charge causes an electric field. The total radiation will be the sum of signal loop differential-mode radiation, common-mode radiation (both voltage- and current-driven) and radiation produced by the Power Distribution System (PDS).
Looking at these in more detail• Differential mode radiation is caused by transmission line loops, and the signals creating differential currents (see Figure 1). Countermeasures include using shielded layers (Vcc or Ground), placing critical signals on inner layers (also known as striplining), avoiding long parallel runs for signals and, as mentioned above, minimising the loop area and keeping signal rise and fall times as slow as possible.

• Common mode radiation is often the more critical EMC design aspect as the EMI is more ‘visible’ in the far field. It is created from parasitic currents (for example, switching currents or inducted currents by flux couplings) or parasitic voltages (such as crosstalk voltages to active IO-signals). The countermeasures include removing the sources of those parasitic currents and voltages - hence avoiding crosstalk between fast-switching signals – and smarter component placement and routing to avoid flux coupling and wrapping effects.

• As for PDS, it can radiate because the PCB is essentially an LCR resonator, comprising inductive elements (the tracks), capacitance (ground and voltage planes are like the plates of a capacitor) and resistance. Countermeasures for PDS EMI include lowering the board impedance, avoiding inductance and ensuring sufficient decoupling.
In addition, ICs are also a source of EMI and will contribute to the PCB’s EM profile. This must be factored in during IC selection, and chip vendors should be able to provide you with information on the EMI behaviour of the circuits.
Rule checkers and simulations
Many PCB design tools include EMC rule checkers. Checks include looking at the design data geometry for instances where signal crosstalk may occur (because of parallel-routed traces), instances of little or no shielding, and where decoupling may be required.
The rules will incorporate the ‘know-how’ of many EMC engineers. However, it is important to know their origin and how they were implemented by the CAD tool vendor; and you are in your rights to ask to see the vendor’s rule books. The tools should also allow you to highlight PCB areas where EMI suppression and EMC integrity are key – you tell the tool what your priorities are.
But let’s not forget, these are post-layout checks. It is always best to design with EMI and EMC in mind rather than embark on a trial-and-error exercise. Also, you will receive little if any steer on what the EM radiation levels are likely to be.
For a more advanced analysis, simulation is required. As with EMC design rule checkers, the meaningfulness and therefore value of the results will depend on how well the digital representations of the board and its behaviour have been rendered, plus of course how well the variety of EM equations have been implemented as software algorithms. Again, the tool vendors should be able to supply information. You should also take some representative measurements to validate the simulation methodology, and compile metrics to act as the basis for interpreting future results.
There are many numerical 3D EM simulation tools on the market, some of which are dedicated to specific activities such as antenna design. They are well-suited to what-if studies and the optimization of structures. They can model all EMI effects for a given structure, but they do require considerable computation power (memory and CPU time) and tend to cost a lot. In addition, an in-depth understanding of EMI is needed to understand the results, as it can sometimes be difficult to explain using 3D EM results alone the reason for a particular radiation peak, for example.
However, for the types of PCBs used in white goods, we are not seeking to optimize antenna structures or produce a particular RF profile; we simply wish to verify that the board design exhibits good EMC – and a PCB design CAD tool with good EMC rule checkers will suffice.
Designing out EMI
While there is no silver bullet to EMC, good design work should include the identification of parasitic EMI antennas, such as electric and magnetic dipoles. Also, identify the current paths, as current flows in loops and will always look for the path of least resistance. Accordingly, plan for a proper return path (noting that ‘ground’ is not an accepted technical term in EMC engineering) and avoid crossing splits/gaps (even for differential pairs) and return path discontinuities (see Figure 3).

In summary, it’s always best to design with EMC in mind, rather than risk board re-spins, but you must have a clear understanding of which EMC rules will apply to your project. Also, having an EMC analysis capability embedded within the PCB design CAD tool can greatly reduce the risk of EMC compliance failure once the board is manufactured; but make sure the tool’s rule checker is based on well-documented and verified EMC principles and explanations. And never simulate unless a) you trust the simulator and b) you have a feel for what the results will be.
XXX . XXX 4%zero null 0 1 2 3 4 Bringing on bioelectronics
Those most falling foul of EMC issues are the designers of PCBs intended for white goods - such as toasters, fridges and washing machines – which are joining the plethora of internet-enabled devices connected wirelessly to the IoT. Also, because of the potentially high volumes involved, re-spinning PCBs can introduce product launch delays. Worse still, product recalls could be very damaging to the company’s reputation and finances.
Where’s noise coming from?
There is no shortage of guidance on designing with EMC in mind, and many companies have their own in-house PCB design and EMC rules. Guidance can also come from external sources, such as legislative bodies, IC vendors and customers. However, accepting all guidelines at face value can lead to an over-defensive EMC strategy, and introduce project delays. Rules should be evaluated individually to determine if they apply to the current design.
That said, your basic, common sense rules will always apply. For instance, to supress noise sources on a PCB you should:
• Keep clock frequencies as low as possible and rising edges as slow as possible (within the scope of the requirements spec’);
• Place the clock circuit at the centre of the board unless the clock must also leave the board (in which case place it close to the relevant connector);
• Mount clock crystals flush with the board and ground them;
• Keep clock loop areas as small as possible;
• Locate I/O drivers near to the point at which the signals enter/leave the board; and
• Filter all signals entering the board.
While the above measures will help mitigate against some of the most common EMI issues, every powered PCB will still radiate EM energy. This is because every current produces a magnetic field and every charge causes an electric field. The total radiation will be the sum of signal loop differential-mode radiation, common-mode radiation (both voltage- and current-driven) and radiation produced by the Power Distribution System (PDS).
Looking at these in more detail• Differential mode radiation is caused by transmission line loops, and the signals creating differential currents (see Figure 1). Countermeasures include using shielded layers (Vcc or Ground), placing critical signals on inner layers (also known as striplining), avoiding long parallel runs for signals and, as mentioned above, minimising the loop area and keeping signal rise and fall times as slow as possible.

Figure 1: Differential mode radiation |

Figure 2: Common mode radiation |
In addition, ICs are also a source of EMI and will contribute to the PCB’s EM profile. This must be factored in during IC selection, and chip vendors should be able to provide you with information on the EMI behaviour of the circuits.
Rule checkers and simulations
Many PCB design tools include EMC rule checkers. Checks include looking at the design data geometry for instances where signal crosstalk may occur (because of parallel-routed traces), instances of little or no shielding, and where decoupling may be required.
The rules will incorporate the ‘know-how’ of many EMC engineers. However, it is important to know their origin and how they were implemented by the CAD tool vendor; and you are in your rights to ask to see the vendor’s rule books. The tools should also allow you to highlight PCB areas where EMI suppression and EMC integrity are key – you tell the tool what your priorities are.
But let’s not forget, these are post-layout checks. It is always best to design with EMI and EMC in mind rather than embark on a trial-and-error exercise. Also, you will receive little if any steer on what the EM radiation levels are likely to be.
For a more advanced analysis, simulation is required. As with EMC design rule checkers, the meaningfulness and therefore value of the results will depend on how well the digital representations of the board and its behaviour have been rendered, plus of course how well the variety of EM equations have been implemented as software algorithms. Again, the tool vendors should be able to supply information. You should also take some representative measurements to validate the simulation methodology, and compile metrics to act as the basis for interpreting future results.
There are many numerical 3D EM simulation tools on the market, some of which are dedicated to specific activities such as antenna design. They are well-suited to what-if studies and the optimization of structures. They can model all EMI effects for a given structure, but they do require considerable computation power (memory and CPU time) and tend to cost a lot. In addition, an in-depth understanding of EMI is needed to understand the results, as it can sometimes be difficult to explain using 3D EM results alone the reason for a particular radiation peak, for example.
However, for the types of PCBs used in white goods, we are not seeking to optimize antenna structures or produce a particular RF profile; we simply wish to verify that the board design exhibits good EMC – and a PCB design CAD tool with good EMC rule checkers will suffice.
Designing out EMI
While there is no silver bullet to EMC, good design work should include the identification of parasitic EMI antennas, such as electric and magnetic dipoles. Also, identify the current paths, as current flows in loops and will always look for the path of least resistance. Accordingly, plan for a proper return path (noting that ‘ground’ is not an accepted technical term in EMC engineering) and avoid crossing splits/gaps (even for differential pairs) and return path discontinuities (see Figure 3).

Figure 3: In the top diagram, the reference layer changes from the ground plane to the voltage plane for part of the trace. This creates an EMI antenna. Keeping with the same reference plane, as in the bottom diagram, avoids/reduces return path discontinuities. |
XXX . XXX 4%zero null 0 1 2 3 4 Bringing on bioelectronics
aim is to create a soft and flexible conducting polymer.
“Cochlear implants currently have 22 channels of stimulation – a limitation caused by the fact they are made from metals,” “Metal conducts electricity using electrons, while the body uses ions. The material we’re using can conduct electricity using both.
“Metal limits size,” she continued. “You can’t make the device smaller without compromising safety and you can’t push more current through the metal as it could cause unwanted chemical reactions, such as changing the pH in the tissue.”
The polymeric material allows current to be pushed into the body at a ‘faster rate, more efficiently and at a lower voltage’, lowering the risk of electrical changes or degradation significantly.
“This provides better perception of sound for a cochlear implant patient, or allows someone with a bionic eye to see not just with 40 or 60 points of light – which is the current limitation of metal electrodes – but with hundreds and thousands of points of light.”
challenge was to develop a polymer which could be accepted by the body. This involved modifying the properties of conductive polymers to create a soft interface that interacts more readily and reduces the foreign body response .
The bionic eye developed comprises a camera, fitted to sunglasses, connected to a processor that converts the analogue signal into a digital format that is then delivered into the body. The electronic package sits behind the ear under the skin. An electrode lead is inserted into the eyeball, where it can stimulate cells to create a perception of vision. A chip interprets the information received.
The implants are powered via inductive coils; one remains outside the body, with a matching coil inside. When clipped together magnetically, it can be used for data transmission.
“A wireless inductive link powers the implant, sends processed information to it and gets reverse telemetry data on how the device is working inside the body .
“The chip encodes image information from the camera into electrical pulses. The brighter the image spot, the larger the amplitude of the electric pulses. There are 91 electrodes in our array; more electrodes means better visual acuity.” polymeric material will coat the electrodes to make them work more effectively and, potentially, enable devices with more electrodes, something which is not possible with metal electrodes.
“The electronics package (where data transmission and signal generation occurs) is implanted at a distance from the sensory organ (eye or ear), but the interfacing electrode array must be implanted in contact with the cells that require activation and connected to the electronics package via a cable or tracks.”
“The more tracks and channels, the better the patient experience. Once you reach the tissue, you need to be able to stimulate and separate those channels.”
making sure that polymer-based tracks can carry electricity across these lengths is a challenge, hence the development of new polymer chemistries and fabrication techniques.
“Hydrogels are best for interacting with tissue when looking to stimulate them, but the elastomers are needed to create long tracks. The biggest challenge is creating a continuous electrical path that doesn’t break with movement. We’ve achieved that, but need to make it commercially competitive.”
Bioelectronics appears to have a role to play in future medicine and to use bioelectronics to communicate with cells wirelessly . Instead of implanting an electronic device near the nerve tissue and applying a current to modulate cell proteins and stimulate communication .
“By inputting electric fields, we plan on modulating electron transfer, which can then be used to sense and actuate chemical reactions. We’ve demonstrated that cancer cells efflux electrons and metabolize more quickly and grow faster than normal tissues. If you can modulate that external electron flux electrically, we may be able to treat cancer.”
“First, we plan to develop nanotechnology and use conducting nano / micro particles that are functionalized with a bioactive molecule. The cells take up these nanoparticles and when an external electric field is applied, the redox state on the surface of that nanoparticle is changed. When the state of the bioactive molecule changes, it causes a modification in the cell’s metabolism, telling it to kill itself.
“Secondly, we think that, by using wireless electrochemistry to self-assemble conductive wires around brain tumours, you can inhibit cell proliferation, which should theoretically extend the patient’s life.
“Thirdly, we plan on using artificial conductive porins.”
Porins – a type of protein – create channels through cellular membranes large enough to allow ions to pass. “The basis of a lot of electrical talk between cells is from porins opening or closing, depending on the electrical fields,” he continued. “By putting in artificial conductive channels and applying external electric fields, we believe we can modulate the potential that cells see and, therefore, the way they communicate.”
These conductive wires are created by printing electrode systems on a glass substrate. When printing with conductive inks, The project found an electrochemical reaction caused atoms to diffuse into the solution and self-assemble into nanoparticles. These then aligned at the conductive bipolar electrode, which has no physical connection to the circuit, creating conductive wires.
Current bioelectronics therapeutics require standard electronic materials, which need invasive surgery. The project proposes to ‘grow electronic devices potentially in situ and avoid the need for that surgery.’
The Project said there are ‘no current commercial examples of treating cancer in the way we propose’, but it is likely this technology could be developed and applied in the next 10 years.
vision is a wearable device, such as a skin patch, that modulates the electric field and targets the area of disease. To do this, the next step is to develop a device to modulate that electrical behaviour and, therefore, control cell proliferation and communication .

Although bioelectronics appears to have numerous benefits, there isn’t a mass market for the technology as yet. This, the project concludes, is due to a combination of ‘high cost and regulation’. But she remains optimistic, believing that demand and growth for this technology will soon see commercial applications.
XXX . XXX 4%zero null 0 1 2 3 4 5 6 7 8 Mapping the innovation infrastructure

research and innovation infrastructure
National Research and Innovation Infrastructure Roadmap. The roadmap will be one of the first major pieces of work to be completed by UK Research and Innovation (UKRI), the new single funding organisation for research and innovation in the UK established last year and set to become active in April 2018.
The roadmap will play an integral part in furthering R&D opportunities in the UK and will be used to better align them with the UK’s Industrial Strategy. It is intended to identify strengths that can be capitalised on, as well as recognising any gaps in the UK’s extensive research and innovation infrastructure.
“The UKRI was established to bring greater focus to science and research and its commercialisation and to deliver a joined-up approach to interdisciplinary problems,” explained Professor Sir Mark Walport, UKRI’s chief executive designate. “Our aim is to improve collaboration within the research base and ensure that a highly trained and diverse workforce is available to drive the commercialisation of discoveries.”
Speaking at the launch of the roadmap, newly appointed Universities and Science Minister Sam Gyimah said: “Boosting research, development and innovation is at the heart of the Government’s new Industrial Strategy and that is why we are investing an extra £2.3billion in R&D spending in 2021-22.”
The minister highlighted what he saw as the strengths of the UK’s research base. “From RRS Discovery to the UK Biobank and the Diamond Light Source to the UK Data Archive, the UK is world renowned for its scientific abilities.
“Now, for the first time, we will map this infrastructure to enable us to showcase those capabilities around the world and to identify future opportunities.”
Gyimah also point out that: “Nothing of this breadth and scale has ever been attempted in the UK before, but having the skills and expertise to carry out this vitally important work is precisely why UKRI was created.”
Speaking at the launch, Sir Mark said of the roadmap: “One of UKRI’s key tasks is to make sure that the UK’s businesses and researchers are ready and able to seize the opportunity presented by the Industrial Strategy. So I'm very pleased that we are starting the process to map out the UK’s nationally and internationally important research and innovation infrastructure.”
Sir Mark said that the roadmap project would ‘enable us to make sure we are getting the absolute best out the infrastructure we already have, and identify what else we will need in order to stay competitive in the next 10 to 15 years’.
Alongside large scientific facilities and major pieces of equipment, the roadmap will also feature other resources, including collections, archives, scientific data, e-infrastructures such as data and computing systems, and communication networks – things which, together, are considered crucial to maintaining and ensuring the UK’s position in science and innovation.
According to Sir Mark: “UKRI aims to create a long-term research and innovation infrastructure roadmap based on an understanding of existing UK infrastructure, future needs and resulting investment priorities.”
Beyond identifying research and innovation capability priorities, the roadmap will also be used to promote the UK as a global leader in research and innovation.
Structured around key sectors, the preliminary findings of the Roadmap activity will be published in November 2018, with the final report due to appear in Spring 2019.
“The UK does not have an all-encompassing picture of its infrastructure landscape, although there are pockets of understanding,” explained Bryony Butland, Director of the UKRI Infrastructure Roadmap Programme.
According to Butland, it’s a complex and diverse landscape which covers all sorts of disciplines, locations and sectors.
“The roadmap will assess the disciplines covered, as well as the kit and instrumentation that is available. We will be looking at single site, distributed and virtual facilities, as well as different business models.”
Butland made the point that the UK’s participation in international collaborations would also form part of the roadmap. “It’s an important part of landscape that we also want to cover.”
Butland added that the roadmap would be used to establish a cycle for future roadmaps, with the aim of creating a wider picture of facilities and capabilities for a broader audience both in the UK and beyond.
Gyimah conceded that research and innovation in the UK faced ‘real challenges’.
“Despite being in post for just a matter of weeks, I’m well aware – and have received clear messages about – which areas need help and those that are seen as important priorities,” he said.
“We need to invest in both research and innovation and I accept that, despite concerted efforts, business R&D in this country remains low by international standards. Our aim is to raise R&D spend to 2.4% of GDP and it is an important challenge.”
Touching on the impact of Brexit, the minister said he was ‘deeply aware’ of the importance of achieving the best possible deal, post Brexit, one that enabled, supported and deepened the UK’s extensive relationship with the wider scientific community.
"While it is important to have a plan, that plan should not be too rigid. The best plans tend to be dynamic, allowing for change and adaption."
“We need to offer a welcome to the world’s best minds,” he said, noting the UK also needs to train the ‘next generation’ of researchers and innovators. “It’s essential we make the most of the UK’s considerable potential,” he said.
To that end, the map will not only identify nationally important innovation infrastructure, but will also be used by UKRI to raise awareness of the diverse landscape that exists across all regions in order to make research and innovation more efficient and effective.


Royal Society's research snapshot
Alongside the launch of the roadmap, Dr Julie Maxton, executive director of the Royal Society, unveiled a paper presenting a snapshot of the UK’s research infrastructures in 2017.
“The UK’s excellence in science is built on an extensive, dynamic and highly interdisciplinary kaleidoscope of world class research infrastructures,” said Dr Maxton.
“Our research was based on new data from an extensive online and telephone survey of more than 135 UK research infrastructures,” Dr Maxton explained. “This snapshot stems from research we organised and carried out last year. It paints a picture of a wide ranging and very varied infrastructure.”
When it comes to defining research and innovation ‘infrastructure’, the paper included facilities, resources and services used by the research community.
“These resources come in an array of forms and sizes,” explained Dr Maxton.
Amongst the research infrastructure includes are the Medical Research Council Nuclear Magnetic Resonance Centre at the Francis Crick Institute in north London and multi-user facilities, such as the Diamond Light Source. The latter is the UK’s national synchrotron light source, which can harness electrons to produce a very bright light that can be used to research new medicines and advances in engineering and technology.
According to the paper, the research undertaken is varied but, in terms of primary research, the UK’s main focus is on physical science and engineering, biological sciences, health and food, ecosystems and earth science, social science and humanities and energy.
The paper threw up some interesting facts that Dr Maxton said would help to shape the roadmap going forward.
“Our research found that 65% of research infrastructures indicated that multiple disciplines were relevant to their research activities,” said Dr Maxton.
Crucially, a significant amount of activity is commercially focused and engaged with industry.
“Among those surveyed, 84% said there was a commercial component to their research portfolio and more than 90% said they conduct an element of their research with UK businesses,” said Dr Maxton.
With Brexit fast approaching and Gyimah acknowledging the importance of welcoming the best minds to the UK, the Royal Society’s paper found that the UK is a hub for international collaboration, with 69% of those responding to the survey saying they were international in scope. Many respondents acknowledged membership of at least one international partnership.
Users from around the world currently access research infrastructures in the UK. While 56% of users were from the UK, 26% were from the EU and EEA, with 18% from the rest of the world.
Research was carried out by a mixture of internal and external researchers, according to the paper, and highlighted the current open and accessible nature of the UK’s resources.
Introducing the paper, Dr Maxton talked about the importance of chance interactions among the research community that in many cases, ‘lead to new projects and collaborations’.
Gyimah also emphasised the value of collaboration and talked of the importance of working with ‘the best and brightest’ in what he described as a ‘global enterprise’.
“Science is at its best when we collaborate with other countries and welcome researchers to this country,” he said, pointing to recent ‘historic’ agreements with China and the US as the UK looks to establish new relationships outside Europe.
“The UK has reaped huge benefit from Horizon 2020 and Future Framework projects and I’ll be looking to secure a good R&D agreement, despite Brexit,” he asserted.
While research infrastructures are found around the UK, where they are tends to be dictated by factors such as the physical environment; the ability of users to physically access the site and the closeness of certain facilities to others.
At the Harwell Campus, for example, a large number of facilities are co-located, including the Diamond Light Source synchrotron, the ISIS Neutron and Muon source and the Central Laser Facility.
The UK is also home to distributed infrastructure, so while Jodrell Bank may be the headquarters of the Square Kilometre Array, its telescopes are located in other countries.

In terms of location, 38% of the UK’s research infrastucture was in London and the south east, with 10% in the North West and 15% in Scotland. Assets in the West and East Midlands accounted for a further 11%, while the East of England was home to 13% of infrastructure assets.
Employment amongst those organisations approached ranged from 1 to more than 3000; larger facilities included not only full time researchers, but also managers and administrators.
The roadmap is being touted as helping to create the conditions necessary to enable R&D to flourish in the UK and it will certainly have a critical role to play in supporting the work of the UKRI in the years to come.
“Good science not only depends on brain-power,” Gyimah concluded, “but also on the right infrastructure. We need to assess the infrastructure we have if we are to better determine future investment.
“Without the right investment, research and development will suffer. While it is important to have a plan, that plan should not be too rigid. The best plans tend to be dynamic, allowing for change and adaption.”
XXX . XXX 4%zero null 0 1 2 3 4 5 6 7 8 The best way to generate a negative voltage for your system
“Metal limits size,” she continued. “You can’t make the device smaller without compromising safety and you can’t push more current through the metal as it could cause unwanted chemical reactions, such as changing the pH in the tissue.”
The polymeric material allows current to be pushed into the body at a ‘faster rate, more efficiently and at a lower voltage’, lowering the risk of electrical changes or degradation significantly.
“This provides better perception of sound for a cochlear implant patient, or allows someone with a bionic eye to see not just with 40 or 60 points of light – which is the current limitation of metal electrodes – but with hundreds and thousands of points of light.”
challenge was to develop a polymer which could be accepted by the body. This involved modifying the properties of conductive polymers to create a soft interface that interacts more readily and reduces the foreign body response .
The bionic eye developed comprises a camera, fitted to sunglasses, connected to a processor that converts the analogue signal into a digital format that is then delivered into the body. The electronic package sits behind the ear under the skin. An electrode lead is inserted into the eyeball, where it can stimulate cells to create a perception of vision. A chip interprets the information received.
The implants are powered via inductive coils; one remains outside the body, with a matching coil inside. When clipped together magnetically, it can be used for data transmission.
“A wireless inductive link powers the implant, sends processed information to it and gets reverse telemetry data on how the device is working inside the body .
“The chip encodes image information from the camera into electrical pulses. The brighter the image spot, the larger the amplitude of the electric pulses. There are 91 electrodes in our array; more electrodes means better visual acuity.” polymeric material will coat the electrodes to make them work more effectively and, potentially, enable devices with more electrodes, something which is not possible with metal electrodes.
“The electronics package (where data transmission and signal generation occurs) is implanted at a distance from the sensory organ (eye or ear), but the interfacing electrode array must be implanted in contact with the cells that require activation and connected to the electronics package via a cable or tracks.”
“The more tracks and channels, the better the patient experience. Once you reach the tissue, you need to be able to stimulate and separate those channels.”
making sure that polymer-based tracks can carry electricity across these lengths is a challenge, hence the development of new polymer chemistries and fabrication techniques.
“Hydrogels are best for interacting with tissue when looking to stimulate them, but the elastomers are needed to create long tracks. The biggest challenge is creating a continuous electrical path that doesn’t break with movement. We’ve achieved that, but need to make it commercially competitive.”
Bioelectronics appears to have a role to play in future medicine and to use bioelectronics to communicate with cells wirelessly . Instead of implanting an electronic device near the nerve tissue and applying a current to modulate cell proteins and stimulate communication .
“By inputting electric fields, we plan on modulating electron transfer, which can then be used to sense and actuate chemical reactions. We’ve demonstrated that cancer cells efflux electrons and metabolize more quickly and grow faster than normal tissues. If you can modulate that external electron flux electrically, we may be able to treat cancer.”
“First, we plan to develop nanotechnology and use conducting nano / micro particles that are functionalized with a bioactive molecule. The cells take up these nanoparticles and when an external electric field is applied, the redox state on the surface of that nanoparticle is changed. When the state of the bioactive molecule changes, it causes a modification in the cell’s metabolism, telling it to kill itself.
“Secondly, we think that, by using wireless electrochemistry to self-assemble conductive wires around brain tumours, you can inhibit cell proliferation, which should theoretically extend the patient’s life.
“Thirdly, we plan on using artificial conductive porins.”
Porins – a type of protein – create channels through cellular membranes large enough to allow ions to pass. “The basis of a lot of electrical talk between cells is from porins opening or closing, depending on the electrical fields,” he continued. “By putting in artificial conductive channels and applying external electric fields, we believe we can modulate the potential that cells see and, therefore, the way they communicate.”
These conductive wires are created by printing electrode systems on a glass substrate. When printing with conductive inks, The project found an electrochemical reaction caused atoms to diffuse into the solution and self-assemble into nanoparticles. These then aligned at the conductive bipolar electrode, which has no physical connection to the circuit, creating conductive wires.
Current bioelectronics therapeutics require standard electronic materials, which need invasive surgery. The project proposes to ‘grow electronic devices potentially in situ and avoid the need for that surgery.’
The Project said there are ‘no current commercial examples of treating cancer in the way we propose’, but it is likely this technology could be developed and applied in the next 10 years.
vision is a wearable device, such as a skin patch, that modulates the electric field and targets the area of disease. To do this, the next step is to develop a device to modulate that electrical behaviour and, therefore, control cell proliferation and communication .

An experimental set up for the induction of electrochemical microwave wireless growth |
XXX . XXX 4%zero null 0 1 2 3 4 5 6 7 8 Mapping the innovation infrastructure

research and innovation infrastructure
National Research and Innovation Infrastructure Roadmap. The roadmap will be one of the first major pieces of work to be completed by UK Research and Innovation (UKRI), the new single funding organisation for research and innovation in the UK established last year and set to become active in April 2018.
The roadmap will play an integral part in furthering R&D opportunities in the UK and will be used to better align them with the UK’s Industrial Strategy. It is intended to identify strengths that can be capitalised on, as well as recognising any gaps in the UK’s extensive research and innovation infrastructure.
“The UKRI was established to bring greater focus to science and research and its commercialisation and to deliver a joined-up approach to interdisciplinary problems,” explained Professor Sir Mark Walport, UKRI’s chief executive designate. “Our aim is to improve collaboration within the research base and ensure that a highly trained and diverse workforce is available to drive the commercialisation of discoveries.”
Speaking at the launch of the roadmap, newly appointed Universities and Science Minister Sam Gyimah said: “Boosting research, development and innovation is at the heart of the Government’s new Industrial Strategy and that is why we are investing an extra £2.3billion in R&D spending in 2021-22.”
The minister highlighted what he saw as the strengths of the UK’s research base. “From RRS Discovery to the UK Biobank and the Diamond Light Source to the UK Data Archive, the UK is world renowned for its scientific abilities.
“Now, for the first time, we will map this infrastructure to enable us to showcase those capabilities around the world and to identify future opportunities.”
Gyimah also point out that: “Nothing of this breadth and scale has ever been attempted in the UK before, but having the skills and expertise to carry out this vitally important work is precisely why UKRI was created.”
Speaking at the launch, Sir Mark said of the roadmap: “One of UKRI’s key tasks is to make sure that the UK’s businesses and researchers are ready and able to seize the opportunity presented by the Industrial Strategy. So I'm very pleased that we are starting the process to map out the UK’s nationally and internationally important research and innovation infrastructure.”
Sir Mark said that the roadmap project would ‘enable us to make sure we are getting the absolute best out the infrastructure we already have, and identify what else we will need in order to stay competitive in the next 10 to 15 years’.
Alongside large scientific facilities and major pieces of equipment, the roadmap will also feature other resources, including collections, archives, scientific data, e-infrastructures such as data and computing systems, and communication networks – things which, together, are considered crucial to maintaining and ensuring the UK’s position in science and innovation.
According to Sir Mark: “UKRI aims to create a long-term research and innovation infrastructure roadmap based on an understanding of existing UK infrastructure, future needs and resulting investment priorities.”
Beyond identifying research and innovation capability priorities, the roadmap will also be used to promote the UK as a global leader in research and innovation.
Structured around key sectors, the preliminary findings of the Roadmap activity will be published in November 2018, with the final report due to appear in Spring 2019.
“The UK does not have an all-encompassing picture of its infrastructure landscape, although there are pockets of understanding,” explained Bryony Butland, Director of the UKRI Infrastructure Roadmap Programme.
According to Butland, it’s a complex and diverse landscape which covers all sorts of disciplines, locations and sectors.
“The roadmap will assess the disciplines covered, as well as the kit and instrumentation that is available. We will be looking at single site, distributed and virtual facilities, as well as different business models.”
Butland made the point that the UK’s participation in international collaborations would also form part of the roadmap. “It’s an important part of landscape that we also want to cover.”
Butland added that the roadmap would be used to establish a cycle for future roadmaps, with the aim of creating a wider picture of facilities and capabilities for a broader audience both in the UK and beyond.
Gyimah conceded that research and innovation in the UK faced ‘real challenges’.
“Despite being in post for just a matter of weeks, I’m well aware – and have received clear messages about – which areas need help and those that are seen as important priorities,” he said.
“We need to invest in both research and innovation and I accept that, despite concerted efforts, business R&D in this country remains low by international standards. Our aim is to raise R&D spend to 2.4% of GDP and it is an important challenge.”
Touching on the impact of Brexit, the minister said he was ‘deeply aware’ of the importance of achieving the best possible deal, post Brexit, one that enabled, supported and deepened the UK’s extensive relationship with the wider scientific community.
"While it is important to have a plan, that plan should not be too rigid. The best plans tend to be dynamic, allowing for change and adaption."
“We need to offer a welcome to the world’s best minds,” he said, noting the UK also needs to train the ‘next generation’ of researchers and innovators. “It’s essential we make the most of the UK’s considerable potential,” he said.
To that end, the map will not only identify nationally important innovation infrastructure, but will also be used by UKRI to raise awareness of the diverse landscape that exists across all regions in order to make research and innovation more efficient and effective.
Below left: Diamond Light Source is the UK's national synchrotron science facility. Below right: The Francis Crick Institute is researching the science underlying health and disease. |


Royal Society's research snapshot
Alongside the launch of the roadmap, Dr Julie Maxton, executive director of the Royal Society, unveiled a paper presenting a snapshot of the UK’s research infrastructures in 2017.
“The UK’s excellence in science is built on an extensive, dynamic and highly interdisciplinary kaleidoscope of world class research infrastructures,” said Dr Maxton.
“Our research was based on new data from an extensive online and telephone survey of more than 135 UK research infrastructures,” Dr Maxton explained. “This snapshot stems from research we organised and carried out last year. It paints a picture of a wide ranging and very varied infrastructure.”
When it comes to defining research and innovation ‘infrastructure’, the paper included facilities, resources and services used by the research community.
“These resources come in an array of forms and sizes,” explained Dr Maxton.
Amongst the research infrastructure includes are the Medical Research Council Nuclear Magnetic Resonance Centre at the Francis Crick Institute in north London and multi-user facilities, such as the Diamond Light Source. The latter is the UK’s national synchrotron light source, which can harness electrons to produce a very bright light that can be used to research new medicines and advances in engineering and technology.
According to the paper, the research undertaken is varied but, in terms of primary research, the UK’s main focus is on physical science and engineering, biological sciences, health and food, ecosystems and earth science, social science and humanities and energy.
The paper threw up some interesting facts that Dr Maxton said would help to shape the roadmap going forward.
“Our research found that 65% of research infrastructures indicated that multiple disciplines were relevant to their research activities,” said Dr Maxton.
Crucially, a significant amount of activity is commercially focused and engaged with industry.
“Among those surveyed, 84% said there was a commercial component to their research portfolio and more than 90% said they conduct an element of their research with UK businesses,” said Dr Maxton.
With Brexit fast approaching and Gyimah acknowledging the importance of welcoming the best minds to the UK, the Royal Society’s paper found that the UK is a hub for international collaboration, with 69% of those responding to the survey saying they were international in scope. Many respondents acknowledged membership of at least one international partnership.
Users from around the world currently access research infrastructures in the UK. While 56% of users were from the UK, 26% were from the EU and EEA, with 18% from the rest of the world.
Research was carried out by a mixture of internal and external researchers, according to the paper, and highlighted the current open and accessible nature of the UK’s resources.
Introducing the paper, Dr Maxton talked about the importance of chance interactions among the research community that in many cases, ‘lead to new projects and collaborations’.
Gyimah also emphasised the value of collaboration and talked of the importance of working with ‘the best and brightest’ in what he described as a ‘global enterprise’.
“Science is at its best when we collaborate with other countries and welcome researchers to this country,” he said, pointing to recent ‘historic’ agreements with China and the US as the UK looks to establish new relationships outside Europe.
“The UK has reaped huge benefit from Horizon 2020 and Future Framework projects and I’ll be looking to secure a good R&D agreement, despite Brexit,” he asserted.
While research infrastructures are found around the UK, where they are tends to be dictated by factors such as the physical environment; the ability of users to physically access the site and the closeness of certain facilities to others.
At the Harwell Campus, for example, a large number of facilities are co-located, including the Diamond Light Source synchrotron, the ISIS Neutron and Muon source and the Central Laser Facility.
The UK is also home to distributed infrastructure, so while Jodrell Bank may be the headquarters of the Square Kilometre Array, its telescopes are located in other countries.

In terms of location, 38% of the UK’s research infrastucture was in London and the south east, with 10% in the North West and 15% in Scotland. Assets in the West and East Midlands accounted for a further 11%, while the East of England was home to 13% of infrastructure assets.
Employment amongst those organisations approached ranged from 1 to more than 3000; larger facilities included not only full time researchers, but also managers and administrators.
Above: The NPL's Strontium end cap ion trap. |
“Good science not only depends on brain-power,” Gyimah concluded, “but also on the right infrastructure. We need to assess the infrastructure we have if we are to better determine future investment.
“Without the right investment, research and development will suffer. While it is important to have a plan, that plan should not be too rigid. The best plans tend to be dynamic, allowing for change and adaption.”
XXX . XXX 4%zero null 0 1 2 3 4 5 6 7 8 The best way to generate a negative voltage for your system
MC3x063A 1.5-A Peak Boost/Buck/Inverting Switching Regulators datasheet (Rev. N)
Modern active components, such as A/D and D/A converters and operational amplifiers, typically don’t require a negative supply voltage. Op amps in particular are available with rail-to-rail inputs and outputs, and in most cases, input and output voltage can swing to close enough to GND.
However, there are still some cases where a negative voltage is required, including:
There are a number of ways to generate a negative voltage, mainly dependent on the input voltage, output voltage and output current required. Examples include: inverting charge pumps; inverting buck-boost converters; and CUK converters. Each has its advantages and disadvantages.
Inverting charge pumps
Inverting charge pumps, which can be regulated or unregulated, are typically used for output currents of about 100mA. They follow a simple two step conversion principle and only require three capacitors.

Inverting buck-boost converters
For larger output currents, inductive solutions – such as the inverting buck-boost converter – are used. These generate a negative output voltage which can be greater or smaller than the input voltage and provide an advantage over charge pumps.
In the first step, when S1 is closed, an inductor is charged with current. In the second step, S1 is opened and S2 is closed. The current in the inductor continues to flow in the same direction and charges the output negative. Typically, S2 can be implemented as an active switch, but is a diode in most cases.
The output voltage depends on the duty cycle (D). With:
D=Ton/T and ton.Vin=toff.|Vout|
The output voltage is defined as
|Vout|=Vin.[D/(1-D)]
In figure 1, input current only flows when S1 is closed and the output capacitor is only charged when S2 is closed. Therefore, the input and output currents are discontinuous and the peak inductor current is much larger than the average output current. The topology has a low loop bandwidth because a delay in the system’s response sets a limit for the control loop bandwidth. If the system demands higher current, the duty cycle has to be increased, which means a shorter toff. This decreases the amount of current transferred to the output in that switching cycle, so the output voltage drops even further. The control loop therefore needs time until the inductor current in the ton phase rises to the level where there is a higher current in the shorter toff phase delivered to the output. This effect, referred to as right half plane zero, makes the response of the control loop somewhat slow. The loop bandwidth of an inverting buck-boost converter is typically in the order of 10kHz.

CUK converter
A CUK converter combines a boost converter with a step-down converter, with the two stages coupled by a capacitor. This topology requires two inductors or one coupled inductor, but supports continuous input and output current and therefore offers advantages for systems that demand low input and output voltage ripple. The control loop bandwidth, and therefore its speed, is lower than the inverting buck-boost converter.
For applications that require low 1/f noise in frequencies ranging to 100kHz, the CUK or the inverting buck-boost converter are not optimal solutions because their control loop bandwidth is much less than 100kHz. A solution to this issue is the inverting buck converter.
Inverting buck converter
Replacing the input inductor of the CUK converter with a high side switch leads to a new topology; the inverting buck converter. This consists of a charge pump inverter followed by a step-down converter and requires only one inductor. The control loop regulates the output voltage of the step-down converter and, because the charge pump stage is combined with the step-down converter’s power stage, it runs with the inverse of the step-down converter’s duty cycle.
In figure 2, the voltage at CP is switching between VIN and GND while the voltage on SW is between –VIN and GND. As the charge pump stage does not boost the input voltage, the voltage across the internal switches is only VIN, so lower than in the inverting buck-boost or CUK converter. This means more efficient low voltage switches can be used. The output LC of the buck-stage filters the output voltage so output voltage ripple becomes very small.
The TPS63710 offers several advantages over classical topologies, including:
In most converters, the voltage divider to set the output voltage is on the output side between VOUT and GND, which sets a certain gain of the output stage of VOUT / VREF. This increases 1/f noise on the reference voltage. In TPS63710, the gain is 1/0.9, which keeps 1/f noise at nearly the same level as the reference voltage on CCAP.
The TPS63710 accepts inputs ranging from 3.1 to 14V, with an output voltage ranging from -1V to -5.5V. As the TPS63710 uses a buck topology, the input voltage, in absolute value, needs to be larger than the output voltage by a factor of 1/0.7 at least.
Figure 3 shows the schematic of an inverting buck converter optimised for a typical 5V input voltage generating a -1.8V supply at up to 1A. Small size ceramic capacitors used on the input, the CP pin and the output have small electrical series resistance and therefore provide lowest output voltage ripple.
TPS63710 provides the highest efficiency of comparable solutions. The QFN package with thermal pad provides a low thermal resistance to the pcb. This keeps the junction temperature low, even when the device is
Capable of operating in high ambient temperatures, the TPS63710 provides:

XXX . XXX 4%zero null 0 1 2 3 4 5 6 7 8 9 X As small cells are introduced to
4G networks so building efficient
MMIC power amplifiers becomes more important
- high performance/high speed A/D and D/A converters
- gallium nitride power transistor bias
- laser diode bias in optical modules
- LCD bias
There are a number of ways to generate a negative voltage, mainly dependent on the input voltage, output voltage and output current required. Examples include: inverting charge pumps; inverting buck-boost converters; and CUK converters. Each has its advantages and disadvantages.
Inverting charge pumps
Inverting charge pumps, which can be regulated or unregulated, are typically used for output currents of about 100mA. They follow a simple two step conversion principle and only require three capacitors.
- Charge a capacitor from a positive input voltage
- Discharge the capacitor to an output capacitor while reversing the connection, so the positive terminal is connected to the negative and vice versa.

Schematic of an inverting buck-boost converter |
For larger output currents, inductive solutions – such as the inverting buck-boost converter – are used. These generate a negative output voltage which can be greater or smaller than the input voltage and provide an advantage over charge pumps.
In the first step, when S1 is closed, an inductor is charged with current. In the second step, S1 is opened and S2 is closed. The current in the inductor continues to flow in the same direction and charges the output negative. Typically, S2 can be implemented as an active switch, but is a diode in most cases.
The output voltage depends on the duty cycle (D). With:
D=Ton/T and ton.Vin=toff.|Vout|
The output voltage is defined as
|Vout|=Vin.[D/(1-D)]
In figure 1, input current only flows when S1 is closed and the output capacitor is only charged when S2 is closed. Therefore, the input and output currents are discontinuous and the peak inductor current is much larger than the average output current. The topology has a low loop bandwidth because a delay in the system’s response sets a limit for the control loop bandwidth. If the system demands higher current, the duty cycle has to be increased, which means a shorter toff. This decreases the amount of current transferred to the output in that switching cycle, so the output voltage drops even further. The control loop therefore needs time until the inductor current in the ton phase rises to the level where there is a higher current in the shorter toff phase delivered to the output. This effect, referred to as right half plane zero, makes the response of the control loop somewhat slow. The loop bandwidth of an inverting buck-boost converter is typically in the order of 10kHz.

Schematic of an inverting buck converter |
A CUK converter combines a boost converter with a step-down converter, with the two stages coupled by a capacitor. This topology requires two inductors or one coupled inductor, but supports continuous input and output current and therefore offers advantages for systems that demand low input and output voltage ripple. The control loop bandwidth, and therefore its speed, is lower than the inverting buck-boost converter.
For applications that require low 1/f noise in frequencies ranging to 100kHz, the CUK or the inverting buck-boost converter are not optimal solutions because their control loop bandwidth is much less than 100kHz. A solution to this issue is the inverting buck converter.
Inverting buck converter
Replacing the input inductor of the CUK converter with a high side switch leads to a new topology; the inverting buck converter. This consists of a charge pump inverter followed by a step-down converter and requires only one inductor. The control loop regulates the output voltage of the step-down converter and, because the charge pump stage is combined with the step-down converter’s power stage, it runs with the inverse of the step-down converter’s duty cycle.
In figure 2, the voltage at CP is switching between VIN and GND while the voltage on SW is between –VIN and GND. As the charge pump stage does not boost the input voltage, the voltage across the internal switches is only VIN, so lower than in the inverting buck-boost or CUK converter. This means more efficient low voltage switches can be used. The output LC of the buck-stage filters the output voltage so output voltage ripple becomes very small.
The TPS63710 offers several advantages over classical topologies, including:
- a control loop bandwidth of about 100kHz gives fast transient response
- continuous output current for low output voltage ripple
- low gain in the gain stage, so the noise level is not increased after the noise filter by a high gain of the gain stage
- a low 1/f noise reference system
In most converters, the voltage divider to set the output voltage is on the output side between VOUT and GND, which sets a certain gain of the output stage of VOUT / VREF. This increases 1/f noise on the reference voltage. In TPS63710, the gain is 1/0.9, which keeps 1/f noise at nearly the same level as the reference voltage on CCAP.
The TPS63710 accepts inputs ranging from 3.1 to 14V, with an output voltage ranging from -1V to -5.5V. As the TPS63710 uses a buck topology, the input voltage, in absolute value, needs to be larger than the output voltage by a factor of 1/0.7 at least.
Figure 3 shows the schematic of an inverting buck converter optimised for a typical 5V input voltage generating a -1.8V supply at up to 1A. Small size ceramic capacitors used on the input, the CP pin and the output have small electrical series resistance and therefore provide lowest output voltage ripple.
TPS63710 provides the highest efficiency of comparable solutions. The QFN package with thermal pad provides a low thermal resistance to the pcb. This keeps the junction temperature low, even when the device is
Capable of operating in high ambient temperatures, the TPS63710 provides:
- A 1/f noise of ~30mVRMS
- A full power efficiency of more than 86%
- An output voltage ripple of less than 10mVpp

Block diagram of the principle behind the TPS63710 |
XXX . XXX 4%zero null 0 1 2 3 4 5 6 7 8 9 X As small cells are introduced to
4G networks so building efficient
MMIC power amplifiers becomes more important
Figure 1: A three-way Doherty power amplifier architecture
Small cells are being introduced to 4G networks to increase their capacity, particularly in dense urban areas in which macrocells are being overwhelmed with traffic.
As a result the power amplifiers (PAs) for these highly distributed small cells need to be able to meet different design criteria to those for macrocells. They have to be able to handle less power (perhaps 60W peak for a 5W cell), because they transmit over shorter distances than macrocells and they need to be engineered for high efficiency, to keep operating costs down, reliability up, and to enable small, light and low-cost enclosures.
One way to meet these design criteria is to use multi-stage LDMOS MMICs, produced using high-volume silicon manufacturing processes. These devices offer high gain, integrated input and inter-stage matching, and so fit the need for small and low-cost PAs, but, due to their use of integrated passive elements, have tended to suffer from relatively low efficiency compared with alternatives.
One solution, developed by Ampleon, is a semi-integrated three-way 1:2:1 PA architecture that is both small and efficient. It has been successfully used to build a 60W MMIC that operates at 2.14GHz with a gain of 27.4dB and an average power-added efficiency (PAE) of 48.5% at 8dB output back-off. The circuit is 35×35mm2 and, as far as we know, is currently offering the best performance at this frequency and power level for a multi-stage MMIC.
Doherty architecture analysed
This is a basic schematic of a PA built using a three-way Doherty architecture.
One important characteristic of a PA is its efficiency when operating at less than its peak power, which is known as ‘back-off’.
Compact design equations can be used to locate the back-off efficiency peaks 1 and 2, of a DPA as below, where 1 and 2 represent the power capabilities of the peak 1 and peak 2 devices normalised to the main device power capability. The back-off efficiency peaks can then be expressed as:

The load modulation of the main device m can then be expressed as:

This gives high-efficiency points located at -2.50dB ( 1 = 0.75) and -9.54dB ( 2 = 0.33), with m = 2.25 for the (1:2:1) power ratio.
It is possible to simulate the voltage and current profiles of the PA by assuming that its transistors behave as ideal current sources with zero on-state voltage and constant forward trans-conductance, a maximum current limit and a 1V supply. We assume the transistors operate in class-B mode and that all harmonic impedances at the current source are short-circuited.
The equations above, and the simulations shown in Figure 2, say that from an efficiency point of view, the three-way 1:2:1 DPA is better than the 1:2 asymmetric DPA currently used in base stations. The 1:2:1 DPA keeps its efficiency above 67% up to the saturation point, while the efficiency of the 1:2 DPA can dip to 59% before peaking again up to saturation. This means that the 1:2:1 DPA should achieve an average efficiency 6% points higher than that of the 1:2 DPA in the desired 8 to 9dB back-off region.
That’s the theory. What happens in reality? We can calculate the practical power modulation mod of the main device, knowing that m is 2.25 for the 1:2:1 DPA and 3 for the 1:2 DPA. With real devices, which don’t have zero On resistance and zero output RF losses, the actual power modulation of the three-way DPA is lower than theory suggests. This gives us a practical back-off efficiency point real of the 1:2 DPA at -7.8 dB ( real = 0.41). Using a real mod of 1.58 instead of a theoretical 2.25, the practical second back-off efficiency point 2real of the 1:2:1 DPA is located at -8dB.
These calculations show that the efficiency advantage of the 1:2:1 DPA is maintained, and even slightly reinforced, thanks to its extra efficiency peak when operating in back-off. This gives a better average efficiency in the 8 to 9dB back-off region.
A good PA also needs good linearity. One challenge with the 1:2:1 DPA architecture to date has been to build effective practical implementations using passive input splitters. The problem is that, for best efficiency, the current to the main device has to remain saturated and constant from the first back-up point 1 at -6 dB up to the full power condition. This can cause a disruption of the main amplifier load when peak1 reaches voltage saturation at 1. This in turn creates linearity problems that have been experienced demanding modulation schemes such as that used in GSM Multi-Carrier, which need better than -60dBc intermodulation performance.
One way around this is to use independent drive profiling of each amplifier, but this complicates practical implementations so much as to make the approach unaffordable for most base stations.

Practical implementation
Our integrated Doherty (iDPA) implementation replaces the usual Doherty impedance inverter with a π network formed by the drain-to-source parasitic capacitors (CDS_M and CDS_P) of the main and peak transistors, and a series inductor LD connected between them.
We used this approach to build a three-way 1:2:1 DPA by combining using a dual-amplifier device and a single amplifier device in a dual-path package (see Figures 3), to keep the overall size down.

The three-way DPA was built on an industry-standard PCB of 20 mil height and 3.5 dielectric constant.
Figure 3 compares the gain and PAE for the 1:2:1 and 1:2 DPA architectures. The 1:2:1 amplifier achieves a maximum gain of 27.4dB at 2.14GHz and an average PAE of 47.5% at 8dB back-off, when measured using a 20MHz-wide LTE signal with a peak to average ratio of 7.2dB.
The three-way DPA can be linearized at this power level to achieve a -58dBc adjacent channel power ratio, using digital pre-distortion. Comparing the performance of the 1:2:1 DPA implementation with the standalone performance of the 45W 1:2 iDPA MMIC that forms a part of the three-way architecture shows that the three-way configuration offers an improvement in PAE of 3.5% points, at the expense of 2dB gain.
In conclusion this semi-integrated three-way 1:2:1 Doherty architecture integrates a dual-path device with another amplifier in a small package, and achieves class-leading performance in doing so. This shows that DPA MMICs can be used to build efficient, cost-effective small-cell base stations.
++++++++++++++++++++++++++++++++++++++++++++++++++++++++++++++++++++++
ELECTRONICS TECHNOLOGY MODERN AND DEVELOPMENT
++++++++++++++++++++++++++++++++++++++++++++++++++++++++++++++++++++++
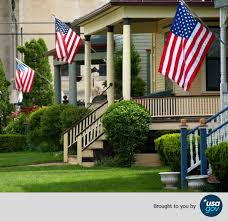
One way to meet these design criteria is to use multi-stage LDMOS MMICs, produced using high-volume silicon manufacturing processes. These devices offer high gain, integrated input and inter-stage matching, and so fit the need for small and low-cost PAs, but, due to their use of integrated passive elements, have tended to suffer from relatively low efficiency compared with alternatives.
One solution, developed by Ampleon, is a semi-integrated three-way 1:2:1 PA architecture that is both small and efficient. It has been successfully used to build a 60W MMIC that operates at 2.14GHz with a gain of 27.4dB and an average power-added efficiency (PAE) of 48.5% at 8dB output back-off. The circuit is 35×35mm2 and, as far as we know, is currently offering the best performance at this frequency and power level for a multi-stage MMIC.
Doherty architecture analysed
This is a basic schematic of a PA built using a three-way Doherty architecture.
One important characteristic of a PA is its efficiency when operating at less than its peak power, which is known as ‘back-off’.
Compact design equations can be used to locate the back-off efficiency peaks 1 and 2, of a DPA as below, where 1 and 2 represent the power capabilities of the peak 1 and peak 2 devices normalised to the main device power capability. The back-off efficiency peaks can then be expressed as:

The load modulation of the main device m can then be expressed as:

This gives high-efficiency points located at -2.50dB ( 1 = 0.75) and -9.54dB ( 2 = 0.33), with m = 2.25 for the (1:2:1) power ratio.
It is possible to simulate the voltage and current profiles of the PA by assuming that its transistors behave as ideal current sources with zero on-state voltage and constant forward trans-conductance, a maximum current limit and a 1V supply. We assume the transistors operate in class-B mode and that all harmonic impedances at the current source are short-circuited.
The equations above, and the simulations shown in Figure 2, say that from an efficiency point of view, the three-way 1:2:1 DPA is better than the 1:2 asymmetric DPA currently used in base stations. The 1:2:1 DPA keeps its efficiency above 67% up to the saturation point, while the efficiency of the 1:2 DPA can dip to 59% before peaking again up to saturation. This means that the 1:2:1 DPA should achieve an average efficiency 6% points higher than that of the 1:2 DPA in the desired 8 to 9dB back-off region.
That’s the theory. What happens in reality? We can calculate the practical power modulation mod of the main device, knowing that m is 2.25 for the 1:2:1 DPA and 3 for the 1:2 DPA. With real devices, which don’t have zero On resistance and zero output RF losses, the actual power modulation of the three-way DPA is lower than theory suggests. This gives us a practical back-off efficiency point real of the 1:2 DPA at -7.8 dB ( real = 0.41). Using a real mod of 1.58 instead of a theoretical 2.25, the practical second back-off efficiency point 2real of the 1:2:1 DPA is located at -8dB.
These calculations show that the efficiency advantage of the 1:2:1 DPA is maintained, and even slightly reinforced, thanks to its extra efficiency peak when operating in back-off. This gives a better average efficiency in the 8 to 9dB back-off region.
A good PA also needs good linearity. One challenge with the 1:2:1 DPA architecture to date has been to build effective practical implementations using passive input splitters. The problem is that, for best efficiency, the current to the main device has to remain saturated and constant from the first back-up point 1 at -6 dB up to the full power condition. This can cause a disruption of the main amplifier load when peak1 reaches voltage saturation at 1. This in turn creates linearity problems that have been experienced demanding modulation schemes such as that used in GSM Multi-Carrier, which need better than -60dBc intermodulation performance.
One way around this is to use independent drive profiling of each amplifier, but this complicates practical implementations so much as to make the approach unaffordable for most base stations.

Figure 2: Simulated fundamental characteristics of the 3-way DPA |
Our integrated Doherty (iDPA) implementation replaces the usual Doherty impedance inverter with a π network formed by the drain-to-source parasitic capacitors (CDS_M and CDS_P) of the main and peak transistors, and a series inductor LD connected between them.
We used this approach to build a three-way 1:2:1 DPA by combining using a dual-amplifier device and a single amplifier device in a dual-path package (see Figures 3), to keep the overall size down.

Figure 3: Comparing the gain and PAE of the 1:2:1 and 1:2 DPAs |
Figure 3 compares the gain and PAE for the 1:2:1 and 1:2 DPA architectures. The 1:2:1 amplifier achieves a maximum gain of 27.4dB at 2.14GHz and an average PAE of 47.5% at 8dB back-off, when measured using a 20MHz-wide LTE signal with a peak to average ratio of 7.2dB.
The three-way DPA can be linearized at this power level to achieve a -58dBc adjacent channel power ratio, using digital pre-distortion. Comparing the performance of the 1:2:1 DPA implementation with the standalone performance of the 45W 1:2 iDPA MMIC that forms a part of the three-way architecture shows that the three-way configuration offers an improvement in PAE of 3.5% points, at the expense of 2dB gain.
In conclusion this semi-integrated three-way 1:2:1 Doherty architecture integrates a dual-path device with another amplifier in a small package, and achieves class-leading performance in doing so. This shows that DPA MMICs can be used to build efficient, cost-effective small-cell base stations.
++++++++++++++++++++++++++++++++++++++++++++++++++++++++++++++++++++++
ELECTRONICS TECHNOLOGY MODERN AND DEVELOPMENT
++++++++++++++++++++++++++++++++++++++++++++++++++++++++++++++++++++++
Tidak ada komentar:
Posting Komentar