16 duty cycle for car
( Mobile system sevice output ( Servo ) )
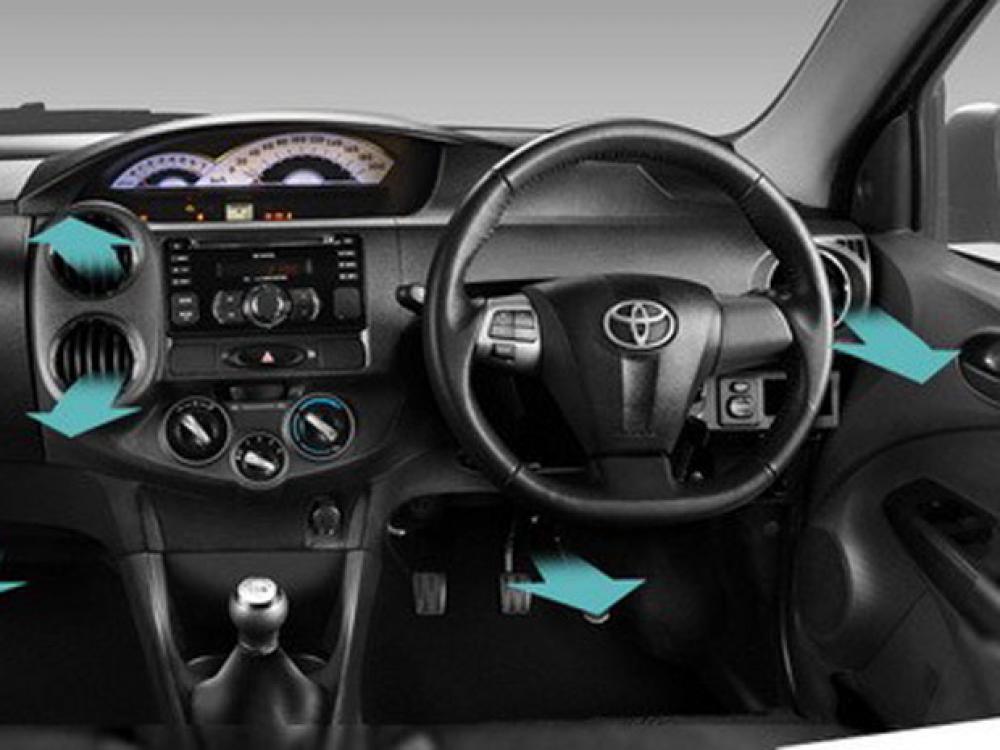
1. Tires and tooling tools (90 degrees)
2. Machine (45 degrees)
3. Lubrication system (22.5 degrees)
4. Cooling system (0 degrees)
5. Combustion system (360 degrees)
6. carburetor (337,5 degrees)
7. ignition system (315 degrees)
8. electric installation on car system (292,5 degrees)
9. steering system (270 degrees)
10. Accu and generator (247,5 degrees)
11. Dynamo stater (225 degrees)
12. Coupling and acceleration (202.5 degrees)
13. ax ace (180 degrees)
14. car frames and springs (157.5 degrees)
15. Bolt / nut (135 degrees)
16. brakes (112.5 degrees)
X . I
Machine

While driving, never cross your mind questions like, what drives your car engine? Or how does a car engine work?
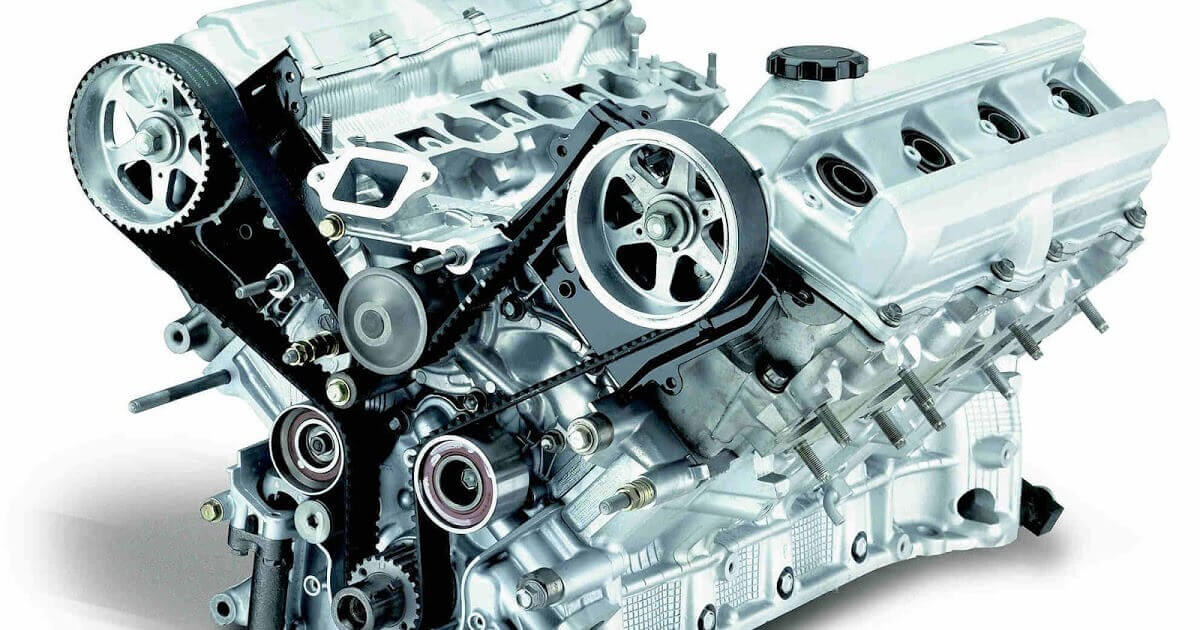
Looks a simple car engine
Internal Combustion Engine
Before talking further about the car engine and how it works, it feels less afdol if you have not talked about one important part of the engine, the internal combustion engine. As the name implies, this is where the combustion process occurs between fuel and air which will create the power used to drive the piston. This is the key movement that exists in the series of car engines.
Anatomy of a Car Machine
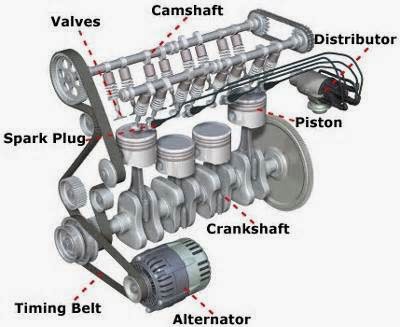
When looking at a car engine, there appear to be some components that seem quite complicated. But in general, the car engine consists of several main components that work together. These components have a big part in driving the vehicle. For more details, let's find out one by one.1. Machine BlockThis is the foundation of a machine and one of the keys to how a car engine works. Generally this engine block is made of aluminum material. However, iron materials are sometimes still used by some manufacturers. This engine block is often associated with cylinder block because its shape is indeed a tube. Starting from here also mentions the four-cylinder engine, V6 or V8 engine appears. Cylinder block engine is also a place of piston movement. Therefore, the more the number of cylinders in a machine, the more power it can generate.2. Combustion chamberThis is where the meeting of fuel, air, pressure and electrical energy that then creates a small explosion that drives the piston. This component also serves as a shelter for several other components such as pistons, cylinders and cylinder heads.3. Cylinder HeadThe cylinder head is usually located on the top side of the engine cylinder. This component also has a very important role in the combustion process.4. PistonThe piston has a shape like a tin that moves up and down, creating a movement that has a big hand in running the car. On the upper side of the piston, there are 3 or 4 cast grooves. In this path there is a piston ring made of iron and consists of two types of rings, compression rings and oil rings.5. Crankshaft / CrankshaftWhen the piston moves up and down, crankshaft or crankshaft is then tasked to convert the movement to be able to move the car. In this component there is also a lobe balancing that is useful to keep the engine from damage when the crankshaft rotates.6. CamshaftYou could say this is the brain of the machine. Camshaft works together with the crankshaft to ensure the engine valve opens and closes its place in time to produce the best performance. This component also has important controls on the intake and outtake valves. On some V-shaped machines, there are sometimes 2 camshafts on each cylinder. That's why the performance of the engine is also much more optimal than ordinary machines.7. Timing SystemHow to work the car is also not separated from the timing system. This component is the place to coordinate between crankshaft and camshaft. If both components are out of sync, then the machine will not work properly.In addition to the 7 components mentioned earlier, there are still some other components that also have a very important role such as engine valves, rocker arms, pushrods and fuel injectors. Each component has its own function and role. And with mutual cooperation, mobilpun machine can work well.
How Car Machine Works
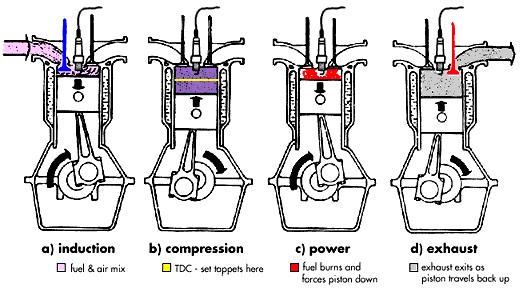
Now we know the outline of the main components in a car engine. Next we can begin to go further, knowing how to work the real car engine. In the process, car engine work is divided into 4 activities that include intake, compression, power and exhaust. For a more complete explanation, the following elaboration.1. IntakeIn the intake process, the piston will be pulled by the crankshaft to the bottom side toward the inside of the cylinder. As long as the car moves, this crankshaft will also continue to move. Valves contained in the engine will also open to allow air and fuel to enter and mix in the cylinder.2. CompressionThe inlet valve is then closed, the piston moves to squeeze or compress the mixture between air and fuel, making it more flammable. As the piston moves to the upper side of the cylinder, at that moment also the burning plug is also burned.3. PowerThe sparks result from this compression process then produce a small explosion and make the burning fuel produce hot gas that push the piston to the bottom side. The energy released in the process will be the energy used to drive the crankshaft.4. ExhaustThe outer channel valve will then open and the crankshaft continues to rotate, pushing the piston back toward the cylinder. At this stage the combustion gas will be discharged through the exhaust.
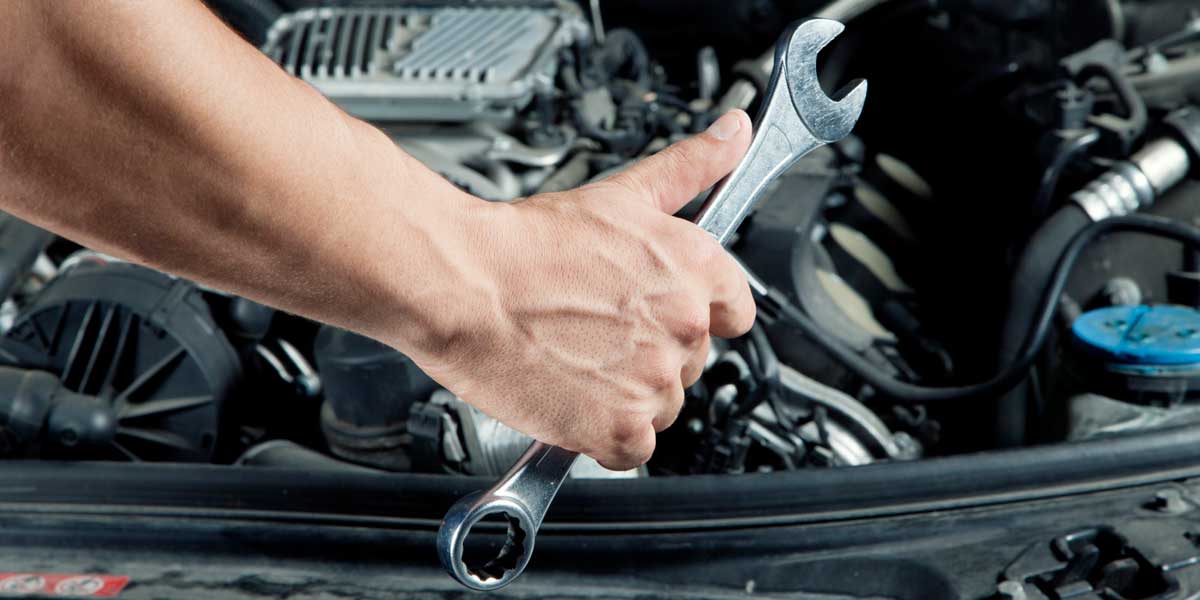
Car maintenance.
Preheat the machine before use. Before starting to drive, always make sure to heat the engine first. The duration of time heating the car varies according to the type of car itself. But in general, 10 minutes is the standard time to heat the machine. When heating the engine, do not step on the accelerator. Let the machine heat without coercion.
Oil change periodically. Changing the car oil should be done every 3000 km or 5000 km. Try not to change oil late. In addition, choose the type of oil that suits your vehicle.
Clean the carburizing filer. Filters are dirty can be very disturbing performance of the car engine, especially when about to turn it on. You can use a toothbrush to clean the carburizing filters. When cleaning this section, do not use a compressor or hairdryer. This can actually damage the carburizing filter layer.
Drive your vehicle. When the old car is not in use, the machine will be crusted for long. To remove the crust you can do it by stepping on the accelerator more deeply. Thus, the crust will come out of the exhaust and the workings of the car engine will return as before.
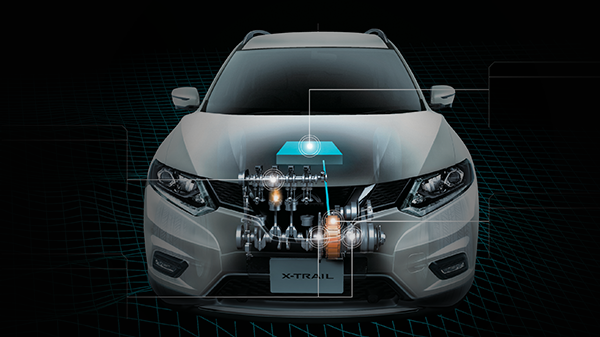
X . II
LUBRICATION SYSTEM
The lubrication system of an automobile is mostly used for collecting, cleaning, cooling and re circulating oil in the engine of vehicle
Lubrication lubrication system plays an important role in the design and operation of all automotive engines.
ANNOUNCEMENT SYSTEM1. Lubrication systemLubricants play an important role in the design and operation of all automotive engines. The age and service provided by the car depends on the attention we give to the lubrication. In combustion engines, lubrication is even more difficult than in other machines, because here there is heat especially around the piston and cylinder, as a result leadakan in spaceburning. The main purpose of lubrication of any mechanical equipment is to eliminate friction, wear and loss of power. Other goals of lubrication in combustion engines are:1. Absorb and move heat.2. As the baffle hole between the piston and cylinder so that the pressure does not leak from the combustion chamber.3. As a cushion to muffle the noisy sound of moving parts.In the lubrication system there are several kinds of complementary systems for good lubrication in a vehicle.
Working principle of lubrication system:The oil is lifted from the oil tub (charter), by a straw, from the oil pump driven by the rotation of the wheels operated by the rotation of the crankshaft, through the suction pipe.From the oil pump, it is channeled through a dividing pipe, then flowed to a cooling medium in the form of a circular pipe supporting one half (1½) circle with finned wall to expand the pipe surface so that the cooling process is more smoothly from the surrounding air or in the form of an oil radiator or without both systems Such cooling, depending on the capacity of the diesel.In the latter case, the oil is only supplied to a short tube (y pass). From this oil impurities that may carry, both from outside and circulation within the machine itself. Lubrication System on Rosker Arm from the valve, obtained through camp shaft, tappel and push rod directly through the rosker arm (Rocker Arm Bearing) baud arm then drip out for a moment to accommodate the tub per valve; Through the gap between the push rod and push rod protective pipe, the oil flows into the bahah toward the charter tub. For lubrication there are metal-metal and also cylinder walls, oil is channeled through capillary tubes contained in the wall of the charter (crank case), also entered into a pipe similar to the crank case)
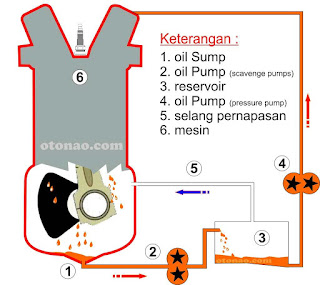
Reduces frictionMotorcycle engine consists of several components, there are components that are stationary and some are moving. Movement of components with each other will cause friction, and friction will reduce energy, cause wear, produce dirt and heat. To reduce friction then between the parts rubbing oil coated oil (oil film).As a silencerPistons, piston rods and crankshaft are the engine parts accepting fluctuating force, so when receiving a large compressive force it may cause a violent collision and cause noisy noise. Lubrication serves to coat between parts and dampen the impact that occurred so that the engine noise is smoother.As anti corrosionThe lubricating system serves to coat the metal with oil, thus preventing direct contact between the metal with air or water and the formation of rust can be avoided.Ë Important parts of the car that require lubrication are:A) cylinder and piston wallB) crankshaft bearings and drive rodsC) our shaft bearingsD) valve mechanismE) shaft penF) the fanG) pumpH) ignition mechanism
X . II
Cooling system
Cooling system in a vehicle engine is a system that serves to keep the engine temperature in ideal conditions. The internal combustion engine (or outside) performs the combustion process to generate energy and with the engine mechanism converted to power. Non-mechanized machines with perfect efficiency, burning heat is not all converted into energy, partially wasted through the drainage and partially absorbed by material around the combustion chamber. High efficiency machines have the ability to convert combustion heat into energy converted into mechanical movement, with only a small part of the wasted heat. Machines are always developed to achieve the highest efficiency, but also consider the economic, durability, safety and environmentally friendly factors.
The cooling system serves to keep engine heat temperature stable and cool .The continuous combustion process in the engine resulted in the machine in very high temperature conditions. Extremely high temperatures will result in uneconomical engine design, most machines are also in an environment not too far away with humans thereby lowering the safety factor. Very low temperatures are also not very profitable in the process of working the machine. The cooling system is used to keep the engine temperature at its ideal working temperature.The principle of cooling is to release the engine heat to the air, the type directly released into the air is called air cooling (water cooling), the type using a fluid as an intermediate is called water cooling .
Air coolingCylinder engine with cooling finsA fully closed IC engine cooling systemOpen IC engine cooling systemSemiclosed IC engine cooling system

Cylinder engine with cooling fins
In this system, the engine heat is immediately released into the air. Machines with air cooling systems have a design on the engine cylinder with cooling fins. This cooling fins to expand the tangent field between the engine with the air so that the heat release can take place more quickly. Some are equipped with fans (eletrical or mechanical fans) to drain air through cooling fins, others without fan.AdvantagesThis type has advantages:
Engine design is more concise.
Overall engine weight is lighter than the water cooling type.
Easy maintenance.This type has its drawbacks, there should be adjustment for use in cold or hot areas especially large capacity machines.This type is widely applied to aircraft engines, mostly motorcycles, old type cars and some of the latest type of cars. Almost all small capacity machines use this type, such as lawn mowers, generator sets under 10 Kva, chain saw, and so on.Cooling water



This system uses the water medium as an intermediary to release heat into the air.Main componentThe main components in this system are:
Radiator, serves to release heat.
Channels in the form of pipes (tubes) or hose rubber (hose).
Pump, serves for water circulation in the system.
Thermostat, serves to close or open the circulation path.
Fan, serves to assist the release of heat on the radiator.This system is very commonly used in cars, whereas motorcycles rarely use this typeThe cooling system of a motorcycle generally uses an air fin fin as a cooling on the engine. Although on new type motorcycles or large vehicles are already using fluid-cooled systems, in contrast to car-cooling systems that use water.Another coolerEngine oil in crankshaft crankcase, in addition to functioning for inner engine lubricants also participates in the engine cooling process.
X . III
ignition / Combustion Engine and system count rolling ( controll )


An ignition system generates a spark or heats an electrode to a high temperature to ignite a fuel-air mixture in spark ignition internal combustion engines oil-fired and gas-fired boilers, rocket engines, etc. The widest application for spark ignition internal combustion engines is in petrol road vehicles: cars (autos), four-by-fours (SUVs), motorcycles, pickups, vans, trucks, and buses.
Compression ignition Diesel engines ignite the fuel-air mixture by the heat of compression and do not need a spark. They usually have glowplugs that preheat the combustion chamber to allow starting in cold weather. Other engines may use a flame, or a heated tube, for ignition. While this was common for very early engines it is now rare.
Switchable systems
Switchable magneto ignition circuit, with starting battery.
To provide high voltage for the spark from the low voltage batteries, a 'tickler' was used, which was essentially a larger version of the once widespread electric buzzer. With this apparatus, the direct current passes through an electromagnetic coil which pulls open a pair of contact points, interrupting the current; the magnetic field collapses, the spring-loaded points close again, the circuit is reestablished, and the cycle repeats rapidly. The rapidly collapsing magnetic field, however, induces a high voltage across the coil which can only relieve itself by arcing across the contact points; while in the case of the buzzer this is a problem as it causes the points to oxidize and/or weld together, in the case of the ignition system this becomes the source of the high voltage to operate the spark plugs.
In this mode of operation, the coil would "buzz" continuously, producing a constant train of sparks. The entire apparatus was known as the 'Model T spark coil' (in contrast to the modern ignition coil which is only the actual coil component of the system). Long after the demise of the Model T as transportation they remained a popular self-contained source of high voltage for electrical home experimenters, appearing in articles in magazines such as Popular Mechanics and projects for school science fairs as late as the early 1960s. In the UK these devices were commonly known as trembler coils and were popular in cars pre-1910, and also in commercial vehicles with large engines until around 1925 to ease starting.
The Model T (built into the flywheel) differed from modern implementations by not providing high voltage directly at the output; the maximum voltage produced was about 30 volts, and therefore also had to be run through the spark coil to provide high enough voltage for ignition, as described above, although the coil would not "buzz" continuously in this case, only going through one cycle per spark. In either case, the low voltage was switched to the appropriate spark plug by the 'timer' mounted on the front of the engine. This performed the equivalent function to the modern distributor, although by directing the low voltage, not the high voltage as for the distributor. The timing of the spark was adjustable by rotating this mechanism through a lever mounted on the steering column. As the precise timing of the spark depends on both the 'timer' and the trembler contacts within the coil, this is less consistent than the breaker points of the later distributor. However, for the low speed and the low compression of such early engines, this imprecise timing was acceptable.
Battery and coil-operated ignition
With the universal adoption of electrical starting for automobiles, and the availability of a large battery to provide a constant source of electricity, magneto systems were abandoned for systems which interrupted current at battery voltage, using an ignition coil (a transformer) to step the voltage up to the needs of the ignition, and a distributor to route the ensuing pulse to the correct spark plug at the correct time.The first reliable battery operated ignition was developed by the Dayton Engineering Laboratories Co. (Delco) and introduced in the 1910 Cadillac. This ignition was developed by Charles Kettering and was a wonder in its day. It consisted of a single coil, points (the switch), a capacitor and a distributor set up to allocate the spark from the ignition coil timed to the correct cylinder.
The points allow the coil magnetic field to build. When the points open by a cam arrangement, the magnetic field collapses inducing an EMF in the primary that is much larger than the battery voltage and the transformer action produces a large output voltage (20 kV or greater) from the secondary.
The capacitor forms a parallel resonant circuit with the ignition coil. During resonance, energy is repeatedly transferred to the secondary side until the energy is exhausted. The capacitor also minimises arcing at the contacts at the point of opening. This reduces contact burning and maximizes point life. The Kettering system became the primary ignition system for many years in the automotive industry due to its lower cost, and relative simplicity.
Modern ignition systems
The ignition system is typically controlled by a key operated Ignition switch.Mechanically timed ignition
Top of distributor cap with wires and terminals
Rotor contacts inside distributor cap
The system is powered by a lead-acid battery, which is charged by the car's electrical system using a dynamo or alternator. The engine operates contact breaker points, which interrupt the current to an induction coil (known as the ignition coil).
The ignition coil consists of two transformer windings — the primary and secondary. These windings share a common magnetic core. An alternating current in the primary induces an alternating magnetic field in the core and hence an alternating current in the secondary. The ignition coil's secondary has more turns than the primary. This is a step-up transformer, which produces a high voltage from the secondary winding. The primary winding is connected to the battery (usually through a current-limiting ballast resistor). Inside the ignition coil one end of each winding is connected together. This common point is taken to the capacitor/contact breaker junction. The other end of the secondary is connected to the rotor. The distributor cap sequences the high voltage to the respective spark plug.
Ignition circuit diagram for mechanically timed ignition
As the engine turns, the cam inside the distributor rotates. The points ride on the cam so that as a piston reaches the top of the engine's compression cycle, the cam causes the breaker points to open. This breaks the primary winding's circuit and abruptly stops the current through the breaker points. Without the steady current through the points, the magnetic field generated in the coil immediately collapses. This severe rate of change of magnetic flux induces a high voltage in the coil's secondary windings.
At the same time, current exits the coil's primary winding and begins to charge up the capacitor (condenser) that lies across the open breaker points. This capacitor and the coil’s primary windings form an oscillating LC circuit. This LC circuit produces a damped, oscillating current which bounces energy between the capacitor’s electric field and the ignition coil’s magnetic field. The oscillating current in the coil’s primary produces an oscillating magnetic field in the coil. This extends the high voltage pulse at the output of the secondary windings. This continues beyond the time of the initial field collapse pulse. The oscillation continues until the circuit’s energy is consumed.
The ignition coil's high voltage output is directed to the distributor cap. A turning rotor, located on top of the breaker cam within the distributor cap, sequentially directs the output of the secondary winding to the spark plugs. The high voltage from the coil's secondary (typically 20,000 to 50,000 volts) causes a spark to form across the gap of the spark plug. This, in turn, ignites the compressed air-fuel mixture within the engine. It is the creation of this spark which consumes the energy that was stored in the ignition coil’s magnetic field.
The flat twin cylinder 1948 Citroën 2CV used one double ended coil without a distributor, and just contact breakers, in a wasted spark system.
Some two-cylinder motorcycles and motor scooters had two contact points feeding twin coils each connected directly to one of the two sparking plugs without a distributor; e.g. the BSA Thunderbolt and Triumph Tigress.
High performance engines with eight or more cylinders that operate at high r.p.m. (such as those used in motor racing) demand both a higher rate of spark and a higher spark energy than the simple ignition circuit can provide. This problem is overcome by using either of these adaptations:
- Two complete sets of coils, breakers and condensers can be provided - one set for each half of the engine, which is typically arranged in V-8 or V-12 configuration. Although the two ignition system halves are electrically independent, they typically share a single distributor which in this case contains two breakers driven by the rotating cam, and a rotor with two isolated conducting planes for the two high voltage inputs.
- A single breaker driven by a cam and a return spring is limited in spark rate by the onset of contact bounce or float at high rpm. This limit can be overcome by substituting for the breaker a pair of breakers that are connected electrically in series but spaced on opposite sides of the cam so they are driven out of phase. Each breaker then switches at half the rate of a single breaker and the "dwell" time for current buildup in the coil is maximized since it is shared between the breakers. The Lamborghini V-8 engine has both these adaptations and therefore uses two ignition coils and a single distributor that contains 4 contact breakers.
However it is necessary to check periodically the maximum opening gap of the breaker(s), using a feeler gauge, since this mechanical adjustment affects the "dwell" time during which the coil charges, and breakers should be re-dressed or replaced when they have become pitted by electric arcing. This system was used almost universally until the late 1970s, when electronic ignition systems started to appear.
Electronic ignition
The disadvantage of the mechanical system is the use of breaker points to interrupt the low-voltage high-current through the primary winding of the coil; the points are subject to mechanical wear where they ride the cam to open and shut, as well as oxidation and burning at the contact surfaces from the constant sparking. They require regular adjustment to compensate for wear, and the opening of the contact breakers, which is responsible for spark timing, is subject to mechanical variations.In addition, the spark voltage is also dependent on contact effectiveness, and poor sparking can lead to lower engine efficiency. A mechanical contact breaker system cannot control an average ignition current of more than about 3 A while still giving a reasonable service life, and this may limit the power of the spark and ultimate engine speed.
Example of a basic electronic ignition system.
The first electronic ignition (a cold cathode type) was tested in 1948 by Delco-Remy, while Lucas introduced a transistorized ignition in 1955, which was used on BRM and Coventry Climax Formula One engines in 1962. The aftermarket began offering EI that year, with both the AutoLite Electric Transistor 201 and Tung-Sol EI-4 (thyratron capacitive discharge) being available. Pontiac became the first automaker to offer an optional EI, the breakerless magnetic pulse-triggered Delcotronic, on some 1963 models; it was also available on some Corvettes. The first commercially available all solid-state (SCR) capacitive discharge ignition was manufactured by Hyland Electronics in Canada also in 1963. Ford fitted a Lucas system on the Lotus 25s entered at Indianapolis the next year, ran a fleet test in 1964, and began offering optional EI on some models in 1965. Beginning in 1958, Earl W. Meyer at Chrysler worked on EI, continuing until 1961 and resulting in use of EI on the company's NASCAR hemis in 1963 and 1964.
Prest-O-Lite's CD-65, which relied on capacitance discharge (CD), appeared in 1965, and had "an unprecedented 50,000 mile warranty."(This differs from the non-CD Prest-O-Lite system introduced on AMC products in 1972, and made standard equipment for the 1975 model year.) A similar CD unit was available from Delco in 1966, which was optional on Oldsmobile, Pontiac, and GMC vehicles in the 1967 model year. Also in 1967, Motorola debuted their breakerless CD system. The most famous aftermarket electronic ignition which debuted in 1965, was the Delta Mark 10 capacitive discharge ignition, which was sold assembled or as a kit.
The Fiat Dino is the first production car to come standard with EI in 1968, followed by the Jaguar XJ Series 1[9] in 1971, Chrysler (after a 1971 trial) in 1973 and by Ford and GM in 1975.
In 1967, Prest-O-Lite made a "Black Box" ignition amplifier, intended to take the load off of the distributor's breaker points during high r.p.m. runs, which was used by Dodge and Plymouth on their factory Super Stock Coronet and Belvedere drag racers. This amplifier was installed on the interior side of the cars' firewall, and had a duct which provided outside air to cool the unit. The rest of the system (distributor and spark plugs) remains as for the mechanical system. The lack of moving parts compared with the mechanical system leads to greater reliability and longer service intervals.
Chrysler introduced breakerless ignition in mid-1971 as an option for its 340 V8 and the 426 Street Hemi. For the 1972 model year, the system became standard on its high-performance engines (the 340 cu in (5.6 l) and the four-barrel carburetor-equipped 400 hp (298 kW) 400 cu in (7 l)) and was an option on its 318 cu in (5.2 l), 360 cu in (5.9 l), two-barrel 400 cu in (6.6 l), and low-performance 440 cu in (7.2 l) . Breakerless ignition was standardised across the model range for 1973.
For older cars, it is usually possible to retrofit an EI system in place of the mechanical one. In some cases, a modern distributor will fit into the older engine with no other modifications, like the H.E.I. distributor made by General Motors, the Hot-Spark electronic ignition conversion kit, and the Chrysler breakerless system.
Coil pack from Honda (one of six).
Digital electronic ignitions
At the turn of the 21st century digital electronic ignition modules became available for small engines on such applications as chainsaws, string trimmers, leaf blowers, and lawn mowers. This was made possible by low cost, high speed, and small footprint microcontrollers. Digital electronic ignition modules can be designed as either capacitor discharge ignition (CDI) or inductive discharge ignition (IDI) systems. Capacitive discharge digital ignitions store charged energy for the spark in a capacitor within the module that can be released to the spark plug at virtually any time throughout the engine cycle via a control signal from the microprocessor. This allows for greater timing flexibility, and engine performance; especially when designed hand-in-hand with the engine carburetor.Engine management
In an Engine Management System (EMS), electronics control fuel delivery and ignition timing. Primary sensors on the system are crankshaft angle (crankshaft or Top Dead Center (TDC) position), airflow into the engine and throttle position. The circuitry determines which cylinder needs fuel and how much, opens the requisite injector to deliver it, then causes a spark at the right moment to burn it. Early EMS systems used an analogue computer to accomplish this, but as embedded systems dropped in price and became fast enough to keep up with the changing inputs at high revolutions, digital systems started to appear.Some designs using an EMS retain the original ignition coil, distributor and high-tension leads found on cars throughout history. Other systems dispense with the distributor altogether and have individual coils mounted directly atop each spark plug. This removes the need for both distributor and high-tension leads, which reduces maintenance and increases long-term reliability.
Modern EMSs read in data from various sensors about the crankshaft position, intake manifold temperature, intake manifold pressure (or intake air volume), throttle position, fuel mixture via the oxygen sensor, detonation via a knock sensor, and exhaust gas temperature sensors. The EMS then uses the collected data to precisely determine how much fuel to deliver and when and how far to advance the ignition timing. With electronic ignition systems, individual cylinders[citation needed] can have their own individual timing so that timing can be as aggressive as possible per cylinder without fuel detonation. As a result, sophisticated electronic ignition systems can be both more fuel efficient, and produce better performance over their counterparts.
Turbine, jet and rocket engines
Gas turbine engines, including jet engines, have a CDI system using one or more ignitor plugs, which are only used at startup or in case the combustor(s) flame goes out.Rocket engine ignition systems are especially critical. If prompt ignition does not occur, the combustion chamber can fill with excess fuel and oxidiser and significant overpressure can occur (a "hard start") or even an explosion. Rockets often employ pyrotechnic devices that place flames across the face of the injector plate, or, alternatively, hypergolic propellants that ignite spontaneously on contact with each other. The latter types of engines do away with ignition systems entirely and cannot experience hard starts, but the propellants are highly toxic and corrosive.
X . IIII
CARBURETOR
A carburetor (American English) or carburettor (British English; see spelling differences) is a device that blends air and fuel for an internal combustion engine in the proper ratio for combustion. It is sometimes colloquially shortened to carb in North America or carby in Australia. To carburate or carburet (and thus carburation or carburetion, respectively) is to blend the air and fuel or to equip (an engine) with a carburetor for that purpose.
Carburetors have largely been supplanted in the automotive and, to a lesser extent, aviation industries by fuel injection. They are still common on small engines for lawn mowers, rototillers and other equipment.

Etymology
The word carburetor comes from the French carbure meaning "carbide". Carburer means to combine with carbon (compare also carburizing). In fuel chemistry, the term has the more specific meaning of increasing the carbon (and therefore energy) content of a fluid by mixing it with a volatile hydrocarbon.Principles
The carburetor works on Bernoulli's principle: the faster air moves, the lower its static pressure, and the higher its dynamic pressure. The throttle (accelerator) linkage does not directly control the flow of liquid fuel. Instead, it actuates carburetor mechanisms which meter the flow of air being pulled into the engine. The speed of this flow, and therefore its pressure, determines the amount of fuel drawn into the airstream.When carburetors are used in aircraft with piston engines, special designs and features are needed to prevent fuel starvation during inverted flight. Later engines used an early form of fuel injection known as a pressure carburetor.
Most production carbureted engines, as opposed to fuel-injected, have a single carburetor and a matching intake manifold that divides and transports the air fuel mixture to the intake valves, though some engines (like motorcycle engines) use multiple carburetors on split heads. Multiple carburetor engines were also common enhancements for modifying engines in the USA from the 1950s to mid-1960s, as well as during the following decade of high-performance muscle cars, fueling different chambers of the engine's intake manifold.
Older engines used updraft carburetors, where the air enters from below the carburetor and exits through the top. This had the advantage of never flooding the engine, as any liquid fuel droplets would fall out of the carburetor instead of into the intake manifold; it also lent itself to use of an oil bath air cleaner, where a pool of oil below a mesh element below the carburetor is sucked up into the mesh and the air is drawn through the oil-covered mesh; this was an effective system in a time when paper air filters did not exist.
Beginning in the late 1930s, downdraft carburetors were the most popular type for automotive use in the United States. In Europe, the sidedraft carburetors replaced downdraft as free space in the engine bay decreased and the use of the SU-type carburetor (and similar units from other manufacturers) increased. Some small propeller-driven aircraft engines still use the updraft carburetor design.
Outboard motor carburetors are typically sidedraft, because they must be stacked one on top of the other in order to feed the cylinders in a vertically oriented cylinder block.
1979 Evinrude Type I marine sidedraft carburetor
Operation
- Fixed-Venturi
- in which the varying air velocity in the Venturi alters the fuel flow; this architecture is employed in most carburetors found on cars.
- Variable-Venturi
- in which the fuel jet opening is varied by the slide (which simultaneously alters air flow). In "constant depression" carburetors, this is done by a vacuum operated piston connected to a tapered needle which slides inside the fuel jet. A simpler version exists, most commonly found on small motorcycles and dirt bikes, where the slide and needle is directly controlled by the throttle position. The most common variable Venturi (constant depression) type carburetor is the sidedraft SU carburetor and similar models from Hitachi, Zenith-Stromberg and other makers. The UK location of the SU and Zenith-Stromberg companies helped these carburetors rise to a position of domination in the UK car market, though such carburetors were also very widely used on Volvos and other non-UK makes. Other similar designs have been used on some European and a few Japanese automobiles. These carburetors are also referred to as "constant velocity" or "constant vacuum" carburetors. An interesting variation was Ford's VV (Variable Venturi) carburetor, which was essentially a fixed Venturi carburetor with one side of the Venturi hinged and movable to give a narrow throat at low rpm and a wider throat at high rpm. This was designed to provide good mixing and airflow over a range of engine speeds, though the VV carburetor proved problematic in service.
A high performance 4-barrel carburetor
- Measure the airflow of the engine
- Deliver the correct amount of fuel to keep the fuel/air mixture in the proper range (adjusting for factors such as temperature)
- Mix the two finely and evenly
- Cold start
- Hot start
- Idling or slow-running
- Acceleration
- High speed / high power at full throttle
- Cruising at part throttle (light load)
To function correctly under all these conditions, most carburetors contain a complex set of mechanisms to support several different operating modes, called circuits.
Basics
Cross-sectional schematic of a downdraft carburetor
Fuel is introduced into the air stream through small holes at the narrowest part of the Venturi and at other places where pressure will be lowered when not running on full throttle. Fuel flow is adjusted by means of precisely calibrated orifices, referred to as jets, in the fuel path.
Off-idle circuit
As the throttle is opened up slightly from the fully closed position, the throttle plate uncovers additional fuel delivery holes behind the throttle plate where there is a low pressure area created by the throttle plate/Valve blocking air flow; these allow more fuel to flow as well as compensating for the reduced vacuum that occurs when the throttle is opened, thus smoothing the transition to metering fuel flow through the regular open throttle circuit.Main open-throttle circuit
As the throttle is progressively opened, the manifold vacuum is lessened since there is less restriction on the airflow, reducing the flow through the idle and off-idle circuits. This is where the Venturi shape of the carburetor throat comes into play, due to Bernoulli's principle (i.e., as the velocity increases, pressure falls). The Venturi raises the air velocity, and this high speed and thus low pressure sucks fuel into the airstream through a nozzle or nozzles located in the center of the Venturi. Sometimes one or more additional booster Venturis are placed coaxially within the primary Venturi to increase the effect.As the throttle is closed, the airflow through the Venturi drops until the lowered pressure is insufficient to maintain this fuel flow, and the idle circuit takes over again, as described above.
Bernoulli's principle, which is a function of the velocity of the fluid, is a dominant effect for large openings and large flow rates, but since fluid flow at small scales and low speeds (low Reynolds number) is dominated by viscosity, Bernoulli's principle is ineffective at idle or slow running and in the very small carburetors of the smallest model engines. Small model engines have flow restrictions ahead of the jets to reduce the pressure enough to suck the fuel into the air flow. Similarly the idle and slow running jets of large carburetors are placed after the throttle valve where the pressure is reduced partly by viscous drag, rather than by Bernoulli's principle. The most common rich mixture device for starting cold engines was the choke, which works on the same principle.
Power valve
For open throttle operation a richer mixture will produce more power, prevent pre-ignition detonation, and keep the engine cooler. This is usually addressed with a spring-loaded "power valve", which is held shut by engine vacuum. As the throttle opens up, the vacuum decreases and the spring opens the valve to let more fuel into the main circuit. On two-stroke engines, the operation of the power valve is the reverse of normal — it is normally "on" and at a set rpm it is turned "off". It is activated at high rpm to extend the engine's rev range, capitalizing on a two-stroke's tendency to rev higher momentarily when the mixture is lean.Alternative to employing a power valve, the carburetor may utilize a metering rod or step-up rod system to enrich the fuel mixture under high-demand conditions. Such systems were originated by Carter Carburetor in the 1950s for the primary two Venturis of their four barrel carburetors, and step-up rods were widely used on most 1-, 2-, and 4-barrel Carter carburetors through the end of production in the 1980s. The step-up rods are tapered at the bottom end, which extends into the main metering jets. The tops of the rods are connected to a vacuum piston or a mechanical linkage which lifts the rods out of the main jets when the throttle is opened (mechanical linkage) or when manifold vacuum drops (vacuum piston). When the step-up rod is lowered into the main jet, it restricts the fuel flow. When the step-up rod is raised out of the jet, more fuel can flow through it. In this manner, the amount of fuel delivered is tailored to the transient demands of the engine. Some 4-barrel carburetors use metering rods only on the primary two Venturis, but some use them on both primary and secondary circuits, as in the Rochester Quadrajet.
Accelerator pump
Liquid gasoline, being denser than air, is slower than air to react to a force applied to it. When the throttle is rapidly opened, airflow through the carburetor increases immediately, faster than the fuel flow rate can increase. This transient oversupply of air causes a lean mixture, which makes the engine misfire (or "stumble")—an effect opposite to that which was demanded by opening the throttle. This is remedied by the use of a small piston or diaphragm pump which, when actuated by the throttle linkage, forces a small amount of gasoline through a jet into the carburetor throat. This extra shot of fuel counteracts the transient lean condition on throttle tip-in. Most accelerator pumps are adjustable for volume or duration by some means. Eventually, the seals around the moving parts of the pump wear such that pump output is reduced; this reduction of the accelerator pump shot causes stumbling under acceleration until the seals on the pump are renewed.The accelerator pump is also used to prime the engine with fuel prior to a cold start. Excessive priming, like an improperly adjusted choke, can cause flooding. This is when too much fuel and not enough air are present to support combustion. For this reason, most carburetors are equipped with an unloader mechanism: The accelerator is held at wide open throttle while the engine is cranked, the unloader holds the choke open and admits extra air, and eventually the excess fuel is cleared out and the engine starts.
Choke
When the engine is cold, fuel vaporizes less readily and tends to condense on the walls of the intake manifold, starving the cylinders of fuel and making the engine difficult to start; thus, a richer mixture (more fuel to air) is required to start and run the engine until it warms up. A richer mixture is also easier to ignite.To provide the extra fuel, a choke is typically used; this is a device that restricts the flow of air at the entrance to the carburetor, before the venturi. With this restriction in place, extra vacuum is developed in the carburetor barrel, which pulls extra fuel through the main metering system to supplement the fuel being pulled from the idle and off-idle circuits. This provides the rich mixture required to sustain operation at low engine temperatures.
In addition, the choke can be connected to a cam (the fast idle cam) or other such device which prevents the throttle plate from closing fully while the choke is in operation. This causes the engine to idle at a higher speed. Fast idle serves as a way to help the engine warm up quickly, and give a more stable idle while cold by increasing airflow throughout the intake system which helps to better atomize the cold fuel.
In older carbureted cars, the choke was controlled manually by a Bowden cable and pull-knob on the dashboard. Forgetting to reset this once started and warm meant that the choke was used for too long, wasting fuel and increasing HC emissions. To reduce these emissions, later cars (from around 1980, depending on market) began to have this automatically controlled by a thermostat employing a bimetallic spring, heated by the engine coolant. A choke unloader is a linkage arrangement that forces the choke open against its spring when the vehicle's accelerator is moved to the end of its travel. This provision allows a "flooded" engine to be cleared out so that it will start.
The 'choke' for constant-depression carburettors such as the SU or Stromberg does not use a choke valve in the air circuit but instead has a mixture enrichment circuit to increase fuel flow by opening the metering jet further or by opening an additional fuel jet or 'enrichment'. Typically used on small engines, notably motorcycles, enrichments work by opening a secondary fuel circuit below the throttle valves. This circuit works exactly like the idle circuit, and when engaged it simply supplies extra fuel when the throttle is closed.
Classic British motorcycles, with side-draft slide-throttle carburetors, used another type of "cold start device", called a "tickler". This is simply a spring-loaded rod that, when depressed, manually pushes the float down and allows excess fuel to fill the float bowl and flood the intake tract. If the "tickler" is held down too long it also floods the outside of the carburetor and the crankcase below, and is therefore a fire hazard.
Other elements
The interactions between each circuit may also be affected by various mechanical or air pressure connections and also by temperature sensitive and electrical components. These are introduced for reasons such as response, fuel efficiency or automobile emissions control. Various air bleeds (often chosen from a precisely calibrated range, similarly to the jets) allow air into various portions of the fuel passages to enhance fuel delivery and vaporization. Extra refinements may be included in the carburetor/manifold combination, such as some form of heating to aid fuel vaporization such as an early fuel evaporator.Fuel supply
Float chamber
Holley "Visi-Flo" model #1904 carburetors from the 1950s, factory equipped with transparent glass bowls.
The fuel stored in the chamber (bowl) can be a problem in hot climates. If the engine is shut off while hot, the temperature of the fuel will increase, sometimes boiling ("percolation"). This can result in flooding and difficult or impossible restarts while the engine is still warm, a phenomenon known as "heat soak". Heat deflectors and insulating gaskets attempt to minimize this effect. The Carter Thermo-Quad carburetor has float chambers manufactured of insulating plastic (phenolic), said to keep the fuel 20 degrees Fahrenheit (11 degrees Celsius) cooler.
Usually, special vent tubes allow atmospheric pressure to be maintained in the float chamber as the fuel level changes; these tubes usually extend into the carburetor throat. Placement of these vent tubes is critical to prevent fuel from sloshing out of them into the carburetor, and sometimes they are modified with longer tubing. Note that this leaves the fuel at atmospheric pressure, and therefore it cannot travel into a throat which has been pressurized by a supercharger mounted upstream; in such cases, the entire carburetor must be contained in an airtight pressurized box to operate. This is not necessary in installations where the carburetor is mounted upstream of the supercharger, which is for this reason the more frequent system. However, this results in the supercharger being filled with compressed fuel/air mixture, with a strong tendency to explode should the engine backfire; this type of explosion is frequently seen in drag races, which for safety reasons now incorporate pressure releasing blow-off plates on the intake manifold, breakaway bolts holding the supercharger to the manifold, and shrapnel-catching ballistic blankets made from nylon or kevlar surrounding the superchargers.
Diaphragm chamber
If the engine must be operated in any orientation (for example a chain saw or a model airplane), a float chamber is not suitable. Instead, a diaphragm chamber is used. A flexible diaphragm forms one side of the fuel chamber and is arranged so that as fuel is drawn out into the engine, the diaphragm is forced inward by ambient air pressure. The diaphragm is connected to the needle valve and as it moves inward it opens the needle valve to admit more fuel, thus replenishing the fuel as it is consumed. As fuel is replenished the diaphragm moves out due to fuel pressure and a small spring, closing the needle valve. A balanced state is reached which creates a steady fuel reservoir level, which remains constant in any orientation.Multiple carburetor barrels
Holley model #2280 2-barrel carburetor
Colombo Type 125 "Testa Rossa" engine in a 1961 Ferrari 250TR Spider with six Weber two-barrel carburetors inducting air through 12 air horns; one individually adjustable barrel for each cylinder.
The first four-barrel carburetors, with two primary bores and two secondary bores, were the Carter WCFB and identical Rochester 4GC simultaneously introduced on the 1952 Cadillacs, Oldsmobiles and Buick Roadmaster. Oldsmobile referred the new carburetor as the “Quadri-Jet” (original spelling) while Buick called it the “Airpower”.
The spread-bore four-barrel carburetor, first released by Rochester in the 1965 model year as the "Quadrajet" has a much greater spread between the sizes of the primary and secondary throttle bores. The primaries in such a carburetor are quite small relative to conventional four-barrel practice, while the secondaries are quite large. The small primaries aid low-speed fuel economy and driveability, while the large secondaries permit maximum performance when it is called for. To tailor airflow through the secondary Venturis, each of the secondary throats has an air valve at the top. This is configured much like a choke plate, and is lightly spring-loaded into the closed position. The air valve opens progressively in response to engine speed and throttle opening, gradually allowing more air to flow through the secondary side of the carburetor. Typically, the air valve is linked to metering rods which are raised as the air valve opens, thereby adjusting secondary fuel flow.
Multiple carburetors can be mounted on a single engine, often with progressive linkages; two four-barrel carburetors (often referred to as "dual-quads") were frequently seen on high performance American V8s, and multiple two barrel carburetors are often now seen on very high performance engines. Large numbers of small carburetors have also been used (see photo), though this configuration can limit the maximum air flow through the engine due to the lack of a common plenum; with individual intake tracts, not all cylinders are drawing air at once as the engine's crankshaft rotates.
Carburetor adjustment
The fuel and air mixture is too rich when it has an excess of fuel, and too lean when there is not enough. The mixture is adjusted by one or more needle valves on an automotive carburetor, or a pilot-operated lever on piston-engined aircraft (since the mixture changes with air density and therefore altitude). Independent of air density the (stoichiometric) air to gasoline ratio is 14.7:1, meaning that for each mass unit of gasoline, 14.7 mass units of air are required. There are different stoichiometric ratios for other types of fuel.Ways to check carburetor mixture adjustment include: measuring the carbon monoxide, hydrocarbon, and oxygen content of the exhaust using a gas analyzer, or directly viewing the color of the flame in the combustion chamber through a special glass-bodied spark plug sold under the name "Colortune"; the flame color of stoichiometric burning is described as a "Bunsen blue", turning to yellow if the mixture is rich and whitish-blue if too lean. Another method, widely used in aviation, is to measure the exhaust gas temperature, which is close to maximum for an optimally adjusted mixture and drops off steeply when the mixture is either too rich or too lean.
The mixture can also be judged by removing and scrutinizing the spark plugs. Black, dry, sooty plugs indicate a mixture too rich; white or light gray plugs indicate a lean mixture. A proper mixture is indicated by brownish-gray/straw-coloured plugs.
On high-performance two-stroke engines, the fuel mixture can also be judged by observing piston wash. Piston wash is the color and amount of carbon buildup on the top (dome) of the piston. Lean engines will have a piston dome covered in black carbon, and rich engines will have a clean piston dome that appears new and free of carbon buildup. This is often the opposite of intuition. Commonly, an ideal mixture will be somewhere in-between the two, with clean dome areas near the transfer ports but some carbon in the center of the dome.
When tuning two-strokes It is important to operate the engine at the rpm and throttle input that it will most often be operated at. This will typically be wide-open or close to wide-open throttle. Lower RPM and idle can operate rich/lean and sway readings, due to the design of carburetors to operate well at high air-speed through the Venturi and sacrifice low air-speed performance.
Where multiple carburetors are used the mechanical linkage of their throttles must be properly synchronized for smooth engine running and consistent fuel/air mixtures to each cylinder.
Feedback carburetors
In the 1980s, many American-market vehicles used "feedback" carburetors that dynamically adjusted the fuel/air mixture in response to signals from an exhaust gas oxygen sensor to provide a stoichiometric ratio to enable the optimal function of the catalytic converter. Feedback carburetors were mainly used because they were less expensive than fuel injection systems; they worked well enough to meet 1980s emissions requirements and were based on existing carburetor designs. Frequently, feedback carburetors were used in lower trim versions of a car (whereas higher specification versions were equipped with fuel injection). However, their complexity compared to both non-feedback carburetors and to fuel injection made them problematic and difficult to service. Eventually falling hardware prices and tighter emissions standards caused fuel injection to supplant carburetors in new-vehicle production.Catalytic carburetors
Constant vacuum carburetors
Constant vacuum carburetors, also called variable choke carburetors and constant velocity carburetors, are carburetors where the throttle cable was connected directly to the throttle cable plate. Pulling the cord caused raw gasoline to enter the carburetor, creating a large emission of hyrdocarbons.Vaporizers
A cutaway view of the intake of the original Fordson tractor (including the intake manifold, vaporizer, carburetor, and fuel lines).
How a fuel pump works
A circulating fuel system
This fuel system has both supply and return pipes along
which petrol circulates continuously; the carburettor draws off whatever
it needs. Single-pipe systems are more usual.
In the fuel-injection system, used on some engines, the petrol and air are mixed in the inlet manifold.
A fuel pump draws petrol out of the tank through a pipe to the carburettor.
Keeping the petrol tank safe
For safety, the petrol tank is placed at the opposite end of the car from the engine.Inside the tank, a float works an electrical sender unit that transmits current to the fuel gauge, signalling how much petrol is in the tank.
The tank has an air vent - usually a pipe or a small hole in the filler cap to allow air in as the tank empties. Some of the latest systems have a carbon filter, so that fuel fumes do not escape.
How a mechanical pump works
Mechanical fuel pump
In a mechanical pump the actuating lever moves up and down
constantly, but pulls the diaphragm down only as needed to refill the
pump chamber. The return spring pushes the diaphragm up to deliver
petrol to the carburettor.
The other end of the lever, which is linked loosely to a rubber diaphragm forming the floor of a chamber in the pump, goes down and pulls the diaphragm with it.
As the revolving cam turns further, so that it no longer presses on the lever, the lever is moved back by a return spring, relaxing its pull on the diaphragm.
The loosely linked lever does not push the diaphragm up, but there is a return spring that pushes against it.
The diaphragm can move up only by expelling petrol from the chamber. The petrol cannot go back through the first one-way valve, so it goes out through another one leading to the carburettor.
The carburettor admits petrol only as it needs it, through the needle valve in its float chamber
While the carburettor is full and the needle valve is
closed, no petrol leaves the pump. The diaphragm stays down, and the
lever idles up and down.
When the carburettor accepts more petrol, the return spring
pushes the diaphragm up and, by taking up the slack in the loose
linkage, brings it back into contact with the lever, which again pulls
it down to refill the pump chamber.
How an electric pump works
Electric fuel pump
An electric pump has a similar diaphragm mechanism; it is
worked by a rod that is drawn into a solenoid switch until it opens a
set of contacts to turn off the current.
At the end of its travel the iron rod forces apart a set of contacts, breaking the current to the electromagnet and relaxing the pull on the diaphragm.
When the diaphragm return spring raises the diaphragm, it also pulls the rod away from the contacts; they then close so that the solenoid pulls the rod and diaphragm down again.
Circulating petrol continuously
Most mechanical and electrical systems pump fuel only when the carburettor needs it. An alternative system has a complete circuit of pipes, from the tank to the carburettor and back again. The pump sends petrol continuously round this circuit, from which the carburettor draws petrol as it needs it.Filtering petrol and air
Both petrol and air are filtered before passing into the carburettor.The petrol filter may be a replaceable paper one inside a plastic housing in the fuel line. A pump may include a wire or plastic gauze filter, and sometimes a bowl to catch sediment.
The air cleaner is a box fitted over the carburettor air intake, usually containing a replaceable paper-filter element.
Some older cars are fitted with an oil-soaked wire-gauze element, which needs washing from time to time in petrol or paraffin, and re-oiling.
X . IIIII
electric installation on car system
How car electrical systems work
The electrical system of a car is a closed circuit with an independent power source the battery. It operates on a small fraction of the power of a household circuit.A typical electrical system
Apart from the main charging, starting and ignition
circuits, there are other circuits that power lights, electric motors,
the sensors and gauges of electrical instruments, heating elements,
magnetically operated locks, the radio and so on.
All Circuits are opened and closed either by switches or by relays - remote switches operated by electromagnets.
All Circuits are opened and closed either by switches or by relays - remote switches operated by electromagnets.
Earth-return system
In a negative (-) earth-return system, the current flows
from the positive (+) terminal to the component being operated. The
component is earthed to the car body, which is earthed to the negative
(-) terminal of the battery.
The strength of the current is measured in amperes (amps); the pressure that drives it round the circuit is called voltage (volts). Modern cars have a 12 volt battery. Its capacity is measured in amp/hours. A 56 amp/hour battery should be able to deliver a current of 1 amp for 56 hours, or 2 amps for 28 hours.
If the battery voltage drops, less current flows, and eventually there is not enough to make the components work.
Current, voltage and resistance
The extent to which a wire resists the flow of current is called resistance, and is measured in ohms.Thin wires conduct less easily than thick ones, because there is less room for the electrons to travel through.
The energy needed to push current through a resistance is transformed into heat. This can be useful, for example in the very thin filament of a light bulb, which glows white hot.
However, a component with a high current consumption must not be connected using wires which are too thin, or the wires will overheat, blow a fuse, or burn out.
All the electrical units of measurement are interrelated: a pressure of 1 volt causes a current of 1 amp to flow through a resistance of 1 ohm. Volts divided by ohms equal amps. For example, a light bulb with a resistance of 3 ohms, in a 12 volt system, consumes 4 amps.
This means it must be connected using wires thick enough to carry 4 amps comfortably.
Often the power consumption of a component will be stated in watts, which are found by multiplying amps and volts. The lamp in the example consumes 48 watts.
Positive and negative polarity
Electricity flows from a battery in one direction only, and some components work only if the flow through them is in the correct direction.This acceptance of a one-way flow is called polarity. On most cars the negative () battery terminal is earthed and the positive (+) one feeds the electrical system.
This is called a negative earth system, and when buying an electrical accessory a radio, for example check that it is of a type suitable for your car's system. Fitting a radio with the incorrect polarity will damage the set, but most car radios have an external switch for setting the polarity to suit that of the car. Switch to the correct setting before fitting.
Short circuits and fuses
If the wrong-sized wire is used, or if a wire becomes broken or disconnected, this can cause an accidental short circuit which bypasses the resistance of the component. The current in the wire may become dangerously high and melt the wire or cause a fire.
The fuse box is often located in a cluster of components, as illustrated here. The box is shown with the cover off.
The most common type of fuse is a short length of thin wire enclosed in a heatproof casing often glass.
The size of the fuse wire is the thinnest that can carry the normal current of the circuit without overheating, and it is rated in amps.
The sudden surge of high current in a short circuit makes the fuse wire melt, or 'blow', breaking the circuit.
When this happens, see if there is a short circuit or a disconnection, then install a new fuse of the correct amperage rating .
There are many fuses, each protecting a small group of components, so that one blown fuse does not shut down the whole system. Many of the fuses are grouped together in a fuse box, but there may also be line fuses in the wiring.
Series and parallel circuits
A headlamp bulb, for example, is designed to have a degree of resistance so that it consumes a certain current to glow normally.
But there are at least two headlamps in the circuit. If they were connected in series, electric current would have to go through one headlamp to get to the other.
The current would encounter the resistance twice, and the double resistance would halve the current, so that the bulbs would glow only feebly.
Connecting the bulbs in parallel means that electricity goes through each bulb only once.
Some components must be connected in series. For example, the sender in the fuel tank varies its resistance according to the amount of fuel in the tank, and 'sends' a small electrical current to the fuel gauge.
The two components are connected in series so that the varying resistance in the sender will affect the position of the needle on the gauge.
Ancillary circuits
Most are wired through the ignition switch, so that they work only when the ignition is switched on.
This prevents you accidentally leaving something switched on which might cause the battery to go flat.
The side and tail lights, however, which you may need to leave on when the car is parked, are always wired independently of the ignition switch.
When fitting extra accessories, such as a rear window heater which consumes a heavy current, always wire it through the ignition switch.
Some ancillary components can be operated without the ignition turned on by turning the switch to the 'auxiliary' position. A radio is usually wired through this switch, so that it can be played with the engine off.
Wires and printed circuits
The instrument connections to this printed circuit are removed by squeezing the integral catches on each end.
A complex network of wires runs through the car. To avoid confusion, each wire is colour coded (but only within the car: there is no national or international system of colour-coding).
Most car handbooks and service manuals include a wiring diagram which can be difficult to follow.
The colour-coding, however, is a useful guide to tracing wiring.
Where wires run side-by-side they are bound together in a bundle, in a plastic or fabric sheath, to keep them tidy and less difficult to fit.
This bundle of wires stretches over the length of the car, with single wires or small groups of wires emerging where necessary, and is called the wiring loom.
Modern cars often need room for many wires in confined spaces. Some manufacturers now use printed circuits instead of bundles of wires, particularly at the rear of the instrument panel.
Printed circuits are plastic sheets on which copper tracks have been 'printed'. Components are plugged directly into the tracks.
A few modern cars have flexible printed circuits. The copper tracks are printed in ribbons of flexible plastic, which replace the whole wiring system.
X . IIIIIII
steering system
Checking power-assisted steering
Checking power-steering fluid
If the reservoir has a dipstick on the cap, clean the dipstick, replace it and then remove again to read the level.
The cap on a centre-spindle reservoir is held by a wingnut. The level marking is on the side of the reservoir.
If not, the level may be up to the top of a circular filter plate fitted to the centre spindle; look in the car handbook to find whether this is the hot or cold level.
On a centre-spindle reservoir, the whole lid is removed by unscrewing a wingnut.
Alternatively, there may be a dipstick on the bottom of the cap. Remove the cap, wipe the stick with a lint-free rag, screw back fully and remove again to read the level.
How to bleed power steering
Put on the handbrake and keep the car in neutral gear; if the car is an automatic, put it in Park before starting the engine.Run the engine until it reaches normal working temperature. Leave it idling.
Turn the steering from lock to lock several times to heat the fluid. Switch off the engine.
Jack up the front of the car with both wheels just off the ground. Turn the steering from lock to lock three times.
Check the fluid level, topping up if necessary. Start the engine.
Slowly turn the wheels from lock to lock three times. Check the fluid level again, and top up if necessary. Note the exact level when you have done this. Replace the reservoir cap and switch off.
Lower the car and restart the engine. Turn the steering from lock to lock five times, then centre it exactly. Switch off, and look in the reservoir.
There should be no bubbling or frothing. The fluid level should not have risen by more than a small amount.
If the fluid is bubbling or has risen much, repeat the whole process from the start.
Finally re-examine the complete system for leaks. If there is still a problem, have the system checked by a garage.
Checking steering-rack security
ACCU and GeneratorTesting a dynamo and checking output
The dynamo is a simple direct-current generator with two output terminals.
If you suspect a fault in the dynamo, check all the connections to it with a circuit tester.
Check also that the dynamo actually turns when the engine is running, and that the drive belt is adjusted to its correct tension, and is not slipping .
Checking output with a voltmeter or tester
Checking dynamo output
Connect the positive lead of the voltmeter to the D terminal, and the negative lead to earth.
The instructions are for a car with a negative (-) earth system. For a positive (+) earth system, read negative for positive, and positive for negative.
Connect a voltmeter across the battery terminals while the engine is running. Have a helper rev the engine up from idling speed.
The battery voltage should rise, or the tester lamp (or headlamps) should brighten.
If it does not, and if checks on connections and the drive belt have been satisfactory, switch off the engine and disconnect the two cables from the endplate of the dynamo.
The terminals are usually marked D and F. They are of different sizes, but label them if necessary, to avoid confusion.
Connect the positive lead of the voltmeter to the D terminal and the negative lead to earth. The meter should read about 14 volts (or the 12 volt bulb should shine brightly). If so, the dynamo is working.
Testing the cables
Testing dynamo cables
Start the engine and allow it to idle at not more than 1,000 rpm. Connect the positive lead from the voltmeter to the cable disconnected from the D terminal at the control box to see if it is sound.
Then do the same with the cable from the F terminal at the control box.
If the cables are sound, and if the dynamo is charging as previously checked, the meter should read about 14 volts and any fault must be in the control box.
Checking a low charge rate or failure to charge
Testing the D terminal without the cable link between D and F should result in a low reading.
Start the engine and have your helper run it up to 2,000 rpm (medium speed).
If the car is not fitted with a tachometer (rev counter), 2,000 rpm is about the speed of the engine when the car is travelling at 30 mph in top gear.
Reconnect the voltmeter between the D terminal and earth.
If the voltage reading is 2 to 4 volts - enough to light a torch bulb but not a 12 volt car bulb in a circuit tester the fault is in the field coil or the brushes.
If there is no voltage the fault is in the armature or the output brushes.
In either case, check the brushes and commutator .
Checking the batteries
Tools you might need
Topping up a battery
The fluid level in other batteries should be checked at least once a month and topped up if it drops below the correct level - just above the tops of the battery plates.
Never top up with tap water, which contains minerals which may damage the battery. Use distilled or otherwise purified water, or a proprietary topping-up fluid.
Do not use a naked flame when checking the battery. The fluid inside - called the electrolyte - can give off explosive gas, especially soon after the battery has been charged.
The electrolyte is a mixture of sulphuric acid and purified water, and is corrosive and dangerous. Do not allow any to splash on to your skin or your clothing.
If you are splashed, wash the affected skin area immediately. If it goes in your eye, wash thoroughly in running water and call a doctor.
If electrolyte splashes on to your car, hose it off immediately.
A drop in the battery fluid level is caused - provided that there are no leaks - by evaporation of the water in the electrolyte mixture.
Once the level falls below the tops of the battery plates, the cell concerned starts to lose efficiency.
If the cell is left for some time with the plates exposed, it can be damaged. That in turn will ruin the battery, which needs all its cells functioning to retain its full electrical charge and deliver power. The battery must be replaced.
How quickly the electrolyte evaporates depends a great deal on two factors: the under-bonnet temperature (if the battery is located there); and whether the generator is overcharging the battery.
Generally, the higher the temperature the more frequently a battery may need topping up. In most cases, the monthly check is enough - but check more often in hot weather, or if the level is well down at the monthly check. Battery cases rarely leak. If more than the usual amount of topping up suddenly becomes necessary, look for the cause.
If a charging-system fault is overcharging the battery, you may find damp patches around the cell caps and even droplets of electrolyte on the battery top .
How to top up a battery
Remove the cell caps or trough cover and fill each cell to the level marked on the battery case. If there is no mark, fill until the electrolyte just covers the battery plates, which you can see through the filler holes.Apart from distilled or otherwise purified water, proprietary topping-up fluids are available from garages, accessory shops and sometimes chemists. Buy them only in sealed containers, to be sure that they are not contaminated.
As an alternative, water from a de-frosted refrigerator can be used, but it must be kept in a clean glass jar or bottle.
Always keep the battery top clean - wipe it before removing the cell caps or trough cover, when dirt is liable to fall into the cells.
The cell caps or cover have ventilating holes to allow the escape of gases when the battery is being charged. Make sure these holes are clear.
After topping up, wipe away any water spilled on the top of the battery.
Using a hydrometer
Using a hydrometer
Squeeze the hydrometer bulb, put the nozzle into the cell
and release the bulb. Remove the hydrometer and read the state of charge
when the float has settled. Squeeze the bulb to replace the
electrolyte.
The figure for electrolyte in a fully charged battery is between 1.270 and 1.290 - meaning that it is 1.270 times heavier than water.
However, as the battery loses charge, the specific gravity drops to 1.130 or lower.
The instrument for measuring specific gravity is a hydrometer, which contains a weighted float. The float is marked with a graduated scale, usually reading from 1.10 to 1.30.
Insert the syringe into a cell, then squeeze and release the bulb to draw up a sample of electrolyte - enough to raise the float but not enough to make it touch the bulb.
Read off the graduation mark which is level with the surface of the electrolyte.
The state of charge can be gauged from how much the figure is below 1.290. A reading of, say, 1.200 would show the battery to be about half charged.
The float may be graded red, yellow and green to show low, half or full charge. Some hydrometers have three small balls of different weights instead of a float. The number of balls that float to the top of the sample indicate the state of charge.
After taking the reading, squeeze the bulb to return the electrolyte to its cell, and test the other cells in turn. All should give similar readings within about 0.04 of each other - any greater variation indicates a defective cell, and the battery must be replaced.
The best time for testing is after the battery has been charged or the car run for about 30 minutes. Switch off the engine and lights.
Using a car battery charger
Frequent short trips, with constant stopping and starting, make your battery work very hard, especially in winter when heater, headlights, heated windows and wipers may be working most of the time.
Eventually, because more current is being drained from the battery than the alternator can put back, the battery will not have enough power left to turn the starter motor. A battery in that state of discharge is said to be flat.
A flat battery can be avoided if you have a battery charger - a relatively cheap, but worthwhile accessory.
It uses mains current to replace the battery's lost charge through positive and negative leads that clip to the corresponding battery posts.
How to charge a battery
A basic charger usually charges at around 2 amps - and so needs 24 hours to deliver the 48 amps needed to fully charge a flat, 48 amp hour battery.
But there is a wide range of chargers with different charge rates on the market - from 2 to 10 amps. The higher the charge output, the faster a flat battery is recharged. Fast charging, however, is undesirable as it can buckle the battery plates.
The loads imposed on your battery may be gauged from the amount of current used by the various electrical components: headlights take about 8 to 10 amps, a heated rear window about the same.
Theoretically, a fully charged battery, without taking in current from the generator, should work the starter for about ten minutes, or the headlights for eight hours, and a heated rear window for 12 hours. As the battery nears full discharge, the lights gradually grow dimmer and finally go out altogether.
There are also causes other than short trips and cold weather which can affect the state of your battery. Failure is more common on cars equipped with a dynamo rather than an alternator, because the alternator produces more electricity and charges better at low engine speeds
The answer in all these cases is frequent testing with a hydrometer to see how much capacity is left in the battery, and using a battery charger to top up its charge when necessary.
Connecting a battery charger
Some batteries have a one-piece cell-cap cover fitting in a central trough.
If there is a power point handy, the battery can be left in the car, so long as the charge rate is only 3 or 4 amps.
However, if the car has an alternator, disconnect the battery terminals beforehand: otherwise some alternators - generally the older type - can be damaged.
If separate cell caps are fitted, remove them for ventilation. Leave a trough cover on, unless the charging rate is high. Clamp the positive (+) lead from the charger, usually coloured red, to the positive battery post. Clamp the negative (-) lead, usually black, to the negative terminal.
Plug the charger into the mains and switch on. The indicator light or gauge (ammeter) will show that the battery is being charged.
The gauge may show a high charging rate at first, but this drops gradually as the battery becomes charged.
If it was very flat, charging is likely to take a long time; check periodically with a hydrometer, while continuing the charge.
In the final stages, the cells bubble and give off gas. If any of them begin gassing before others, or do so more violently, the battery is probably defective and should be checked by a garage or battery specialist.
Unplug before disconnecting
After charging, always switch off at the mains and unplug the charger before removing its terminal clips - otherwise the clips may spark as you take them off and ignite gas given off during charging.Make sure also that no electrical circuits are switched on in the car when you reconnect the battery - a spark may occur as you replace the second battery terminal and ignite battery gas.
Types of car battery charger
A basic home battery charger incorporates a transformer and rectifier, to change the mains 110/220 volt alternating current to 12 volt direct current, and allows the mains supply to provide a charging current at a rate determined by the state of the battery.In the case of a battery in good condition, the rate of charge may be around 3 to 6 amps with a normal home charger.
A battery at the end of its useful life may not accept any recharging, and will not, in any case, hold a charge.
Some chargers are fitted with a high and low (Hi-Lo) switch to give a choice of two charging rates - typically 3 or 6 amps - in case you want to give the battery a short overnight boost at 6 amps rather than a longer charge at 3 amps.
Many have a charge indicator which may be a warning light, or a gauge showing the charge rate in amps.
Note that the mains lead on all chargers should be fused. If it is not, use a three-pin fused plug. As an extra precaution, fit a line fuse cable lead to the battery.
Tidak ada komentar:
Posting Komentar