X . I
Water Jet Cutter and How It Works

Water jet is a tool used in the process of cold cuts with road spray water pressure and speed to the workpiece surface. To get the right concentration of surface erosion of the objects used nozzle orifice diameter of 0.1 s / d0,4mm. The water pressure is used to reach 400 MPa and supersonic speeds that reached 900 m / s. Distance tip nozzle to the workpiece surface will affect the speed of erosion. This distance is called standoff distance of about 3.2 mm. This type of device diverse, there are using the medium of water ie Water Jet Cutting (WJC) and the Abrasive Water-jet Cutting (AJM), which uses pressurized gas mixes abrasives 0.2 s / d 1,4MPa a speed of about 2,5- 5 , 0 m / s. The gas used can be air dried, nitrogen, carbon dioxide, helium and others. AJM is generally used for finishing work, de burring, trimming, cleaning and so on. Material that can be cut is a polymer.


Water jet parts
Diagram of water jet cutting:
1 - high-pressure water inlet
2 - gem (ruby or diamond)
3 - abrasive (garnet)
4 - mixing tube
5 - guard
6 - water jet cutting
7 - cut materials
High-speed water out of gems creates a vacuum that is interesting abrasive than a rough outline, which is then mixed with water in a mixing tube.
The usefulness of a water jet namely:
Used for cutting glass, metals, non-metallic (wood, rubber, marble, granite), plastic with a thickness of more than 18 inches without forming a used color. Material and ideal speed depends on various factors, including the material, the shape of the part, the water pressure and the type of abrasive. Controlling the speed of the abrasive jet nozzle is essential for efficient and economical engines.
One of the few materials that can not be cut with a water jet is cup upset. Because the hot-tempered glass stress, as soon as you start to cut it, it will disintegrate into tiny fragments as they are designed to do the demolition. Ideal speed motion depends on various factors, including the material, the shape of the part, the water pressure and the type of abrasive.
Because waterjets cut using water and rough, they can work with a variety of materials. This material includes:
* Copper, brass, aluminum* Pre - hardening steels* Mild steel* Exotic materials such as titanium, Inconel and Hastalloy* 304 stainless steel* Brittle materials such as glass, ceramic, quartz, stone* Flammable materials
Water jets also play a large role as one piece in a larger manufacturing process. For example, water jets are often used to machine features into an existing part, or to pre - machine to remove the material before completing another machine precision.
The advantage of using water jets, among others
* Can be used for cutting very precise,* The time needed very quickly* Environmentally friendly, does not produce waste that is damaging to the environment* More economical for water and abrasive materials easily recyclable* Figures are very tight tolerances (relatively small) amount of material removed by the water jet stream is usually about 0.02 "(0.5 mm) wide, which means that very little material will be removed. When you are working with expensive materials (such as titanium) or hazardous materials (such as lead), this can be a significant benefit.* More secure since a leak at a high pressure water system tends to lead to a rapid decrease of pressure to a safe level. The water itself is safe and non-explosive and abrasive garnet too slow and non-toxic.
Losses in the water jets, among others
* The initial cost for the purchase of high water jet, but for the next production process when compared with other equipment is very cheap, and save processing time.* It needs special care and periodically, as water mixed with abrasive material is forced to pass through a very narrow so it took special attention so that the equipment is in good shape.
Characteristics of water jet namely:
1. Using keceatan very high, the flow of abrasive particles (20.000-90.000psi) produced by a water jet intensifier pump2. The workmanship no damage to the workpiece, hot surfaces or pinggiranya3. The angle formed less than 1 degree is used on most cuts, which can be reduced or eliminated altogether by slowing down the cutting process4. Distance nosle and workpiece affect the size guritan5. Used in heat sensitive material, a soft material or a hard material.
The advantages compared to laser water jet:
* Can work with heat sensitive. Water jet cutting of various materials without the necessary changes in the setup. In addition, the heat sensitive materials that can not be done by laser can be cut using a water jet.
* There is no heat-affected zone (haz) or thermal distortion, which can occur with laser. Water jet does not change the material properties.
* Water jet safer. There is no noxious fumes, such as evaporated metal, and there is no risk of fire.
* Better finish the edges. Materials cut by waterjets have smooth surfaces, because of the way abraded material, which makes high-quality results. Materials cut by laser tend to have more rough, scaly edges, which may require additional machining operations to clean up.
The advantage of water jet from the EDM:
It can work with different kinds of materials
Water jet engines can work with non-metallic materials that EDM can not do, such as glass, wood, plastics, and ceramics.
Water jet can penetrate and create his own hole
Some types of EDM, such as wire cut EDM, hole into which the first was made in the material, should be done in a separate process. Water jet can penetrate the material, does not require additional fixturing or machine.
There is no heat-affected zone (haz) with water jets
There is no heat-affected zone ( haz ) or thermal distortion, which can occur with EDM. Water jet does not change the material properties.
The advantage of water jet from the plasma:
The most obvious advantage compared with plasma cutting is that water jets operate at lower temperatures.
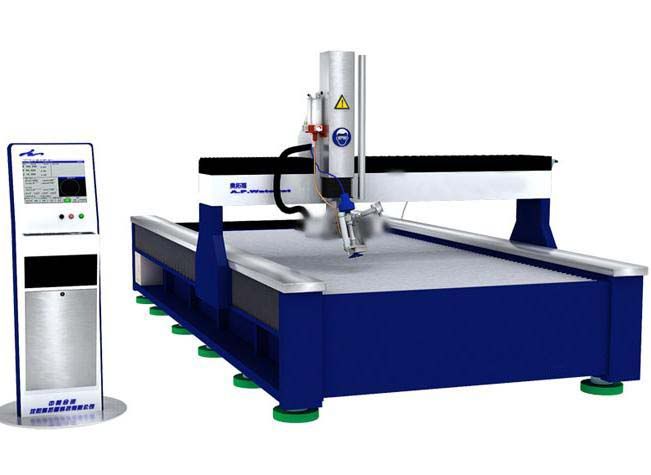
Figure : Water Jet Cutter, Technology Utilizing Water For Metal Cutting
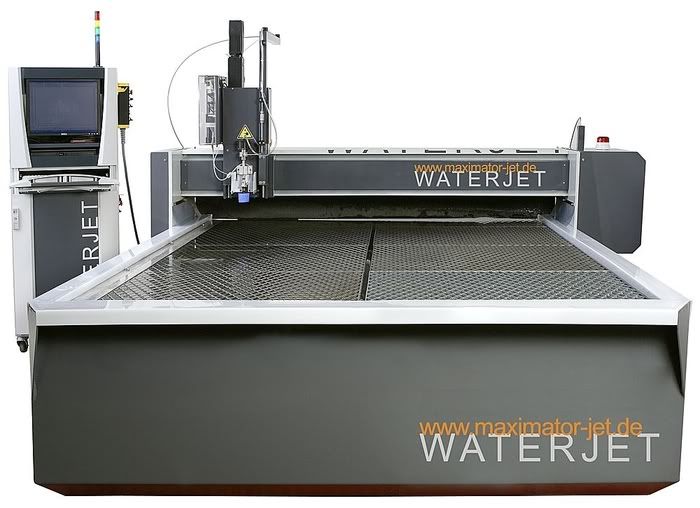
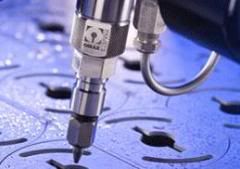
abrasives - water jets are more useful tool for industrial cutting, drilling, and milling, especially for flexible factory automation. Water jet also capable of cutting objects such as: Marble, Granite, Stone, Metal, Plastic, Wood, Stainless steel up though .
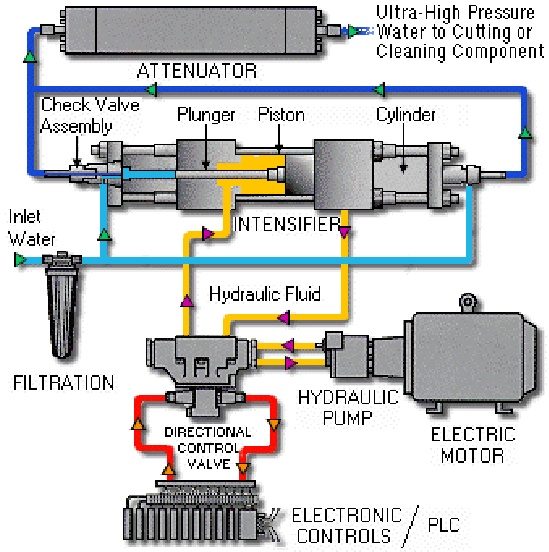

Water jet cutting
To get a smooth flow of water is used the opening of the nozzle with a diameter of about 0.004 to 0.016 in (0.1 to 0.4 mm). In order to obtain the flow with sufficient energy for cutting, used pressure above 60,000 lb / in2 (400 MPa), and a beam reach speeds above 3000 ft / sec. (900m / s). Liquid pressed according to the desired level by using a hydraulic pump. As a cutting fluid is normally used for the polymer solution tends to produce a more unified flow (coherent stream). Liquid flow from the nozzle can be arranged by the size of thin material opening is set smaller in order to produce finer cuts.WJC parameters in the process are:F The distance between the nozzle and the workpiece surface (standoff distance).F The diameter of the nozzle opening,F The water pressure and cutting speed.
The distance between the opening of the nozzle with the workpiece surface should be set as small as possible to avoid splashes of liquid flow. Distance commonly used are 1/8 in (3.2 mm). The size of the nozzle opening affect the accuracy of cutting, a small opening is used for fine cuts on thin material, was to cut thicker materials required emission flow and pressure also increase further. Cutting speeds are often used on the 12 in./min (5 mm / s) up to above 1200 in./min (500 mm / s).

Schematic diagram of a hydrodynamic jet engines.
This intensifier raised fluid pressure nozzles desired to temporarily smooths out the pulse accumulator in the liquid jet. WJC is effectively used to cut narrow grooves in the flat workpieces such as plastics, textiles, composite, tile, carpet, and leather
Abrasive water jet cutting (AWJC)
Air jet engine (WJM) is mainly used to cut and slit porous nonmetallic such as wood, paper, leather, and foam. However, it is not efficient for the working of hard materials. When mixed abrasive water jet, Abrasive Water Jet Machining, new processes and more powerful, realized. Both WJM and AWJM use the principle of pressurizing the water to a very high pressure, and allow the water to escape through a very small hole (orifice).
Air jet engine using light water outlet orifice (or gems) to cut things like diapers and soft candy, but not effective for cutting harder materials. Air inlet pressure is usually between 20,000 and 55,000 pounds per square inch (PSI). This accelerated through a small hole in the "Jewel", which is typically 0.010 "to 0.015" diameter.
This creates a beam of very high water velocity. Abrasive water jet machine that beams use the same water for coarse particles accelerate to speeds fast enough to cut the material is much more difficult. With the help of abrasives, material of any hardness can be cut without delamination, without thermal damage, in the same time, with the cuts were very high and the ability to cut a very large thickness.
WJC used for cutting metal workpieces, it usually must be added the abrasive particles into the jet stream. The abrasive particles are commonly used are aluminum oxide, silicon dioxide, and garnet (silicate mineral). The abrasive particles are added to the water flow of about 0.5 lb / min (0.23 kg / min) after coming out of the nozzle.
AWJC parameters in the process the same as in the WJC, namely:F diameter of the nozzle opening,F water pressure, andF the distance between the nozzle opening and the surface work piece.
The opening of the nozzle diameter ranging between 0.010 in. (0.25 mm) to 0.025 in. (0.63 mm), slightly larger than the WJC. The pressure of the water used is almost the same as the WJC, being the distance between the opening of the nozzle with the workpiece surface is slightly smaller, in order to minimize the effects of splashes cutter, which now contain abrasive particles. The distance of about a quarter and a half of the distance commonly used in the WJC.
Beam abrasive machining (AJM)
Abrasive Jet Machine is the process of disposing of material that use high-speed gas stream containing small abrasive particles as shown in FIG. Here the use of dry gas with a pressure of 25 to 200 lb / in2 (0.2 to 1.4 MPa) is passed through the hole nozzle with a diameter of 0.003 to 0.040 in. (0.075 to 1.0 mm) at speeds of 500 to 1000 ft / min (2.5 to 5.0 m / s). The gas used is dry air, nitrogin, carbon dioxide, and helium. To direct the nozzle to the workpiece is usually done manually by an operator. The distance between the tip of the nozzle to the workpiece surface about 1/8 in. until a few nights. The workplace should be prepared with adequate ventilation to the operator.

Figure : Abrasive jet machining
AJM is generally used for the resolution process such as trimming, cleaning, polishing, and so on. Cutting can be done for a hard and brittle material (for example glass, silicon, mica, and ceramic) were flat and thin. Abrasive that is often used is aluminum oxide (for aluminum and brass), silicon carbide (for stainless steel and ceramic), and grain glasses (for polishing). Very fine grain diameter sizes, ranging from 15 to 40 mm, and to be able to use that size should be uniform.
WJM Cutting EquipmentDiagram of water jet cutter consists of parts such as high-pressure water inlet, gems (ruby or diamond), abrasive (garnet), mixing tube, guards, water jet cutting, cutting material. Pump as a source of pressure and nozzle as beam forming is an essential part in any system with emission cuts. Other equipment such as piping, fittings, and valves. The explanation of the equipment-equipment are as follows:1. PumpEmphasis fluids 1500 and 4000 Mn / m2 is usually done by one of the direct mechanical movement of the small diameter plumper or amplifier (internsifier). Big enough fluid pressure piston air moving large cross-section wherein in step behind moving the small-diameter ram reveals cutting fluid.At this pressure is the main problem to overcome leakage (sealing) due to the high pressure of the ram, while the problem of damage to mechanical components can be restricted by the living elements of the equipment. Some settlement has been found one of them is to provide a high-pressure gasket that can be replaced quickly and with ease to get it. Other alternative conventional fabric back, synthetic rubber gasket can be lubricated by adding oil seluble to 5% to the water being pumped. However, this oil may not match the material being cut and disposal of waste fluid can also make judgment difficult.Ram for movement back and forth (reciprocating ram) can be covered with a closed long sleeve fittings. With the right design and manufacture of precision fluid leakage past the seal clearances may be reduced as low as 2% of the average delivery unit at a pressure of 30KN / cm2. Make a component of hard metal makes the seal has a comparatively long life and is suitable for various types of cutting fluid including pure water.Another method is to use two air seal little leeway on the ram. Ingestion through movement (feeding) in the space between the seal and the oil is very viscous at high pressure, leakage can be reduced, but a small portion of oil will be inevitable exit cutting fluid through the inner seal (innerseal).
Ø How the pump:
Actually, the working principle of abrasive waterjet can be said to be simple and also very complex. The working principle of the simplest is to help drain water pump toward the hole cutter head. Detailed functional descriptions is actually very complex. To generate and keep the output of pressurized water remains in the range of 60,000 psi, required technology is very advanced and complex. At this pressure, a slight error may cause permanent damage to the engine components.
The pump is the heart of a water jet. The pump should be able to produce high-pressure water continuously. In general, the pump consists of two kinds, namely direct pump, and the pump is not directly (intensifier based pump). However, when this type of pump that is more widely used for use in the industrial field is a kind of indirect pump (intensifier based pump), because this type of pump can produce higher water pressure. Therefore, in this paper, we will only discuss the intensifier based pump. Intensifier based pump is a water pump system that can generate high pressure water continuously.
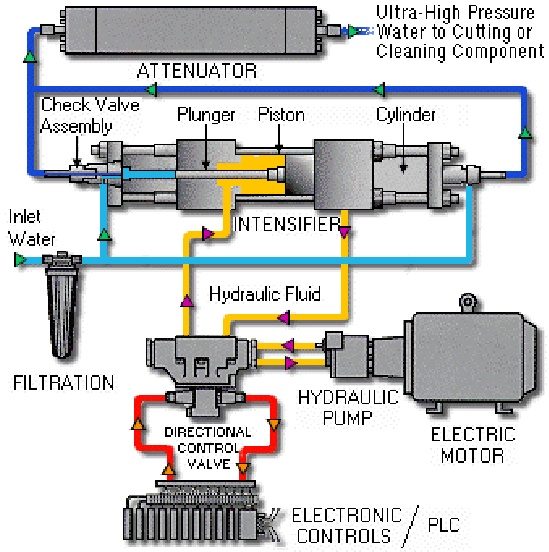
Scheme waterjet cutting system based intensifier pump. The electric motor causes the hydraulic pump circulating the hydraulic fluid in the system that causes the piston plunger along the left and right can move back and forth continuously. At the time of the rod plunger on the left moves to the right, the water from the source is sucked into the pipe container temporarily, while the plunger right, water is pushed out of the pipe container while towards the hole head cutter, and vice versa when the liquid fuida re-circulated, piston rod on the right to move to the left and the siphoning of water from the pipe into the containerwhile, and on the left side of the pump, the water that has been drawn in earlier driven out towards the hole cutter head. So with such a working principle, we can produce a continuous water flow with pressure and speed is very high, reaching 60,000 psi pressure at a speed of 762m / s.
2. Piping (Tubing)High pressure pipe used for delivering fluid from one system to another is a thick-walled components with the ratio between the outside diameter and an inside diameter of at least 5 and sometimes higher than 10. The pipes may be made of stainless steel drill solid walls or walls with steel komposit therein stainless and carbon steel as skin. Pipimg can be used against pda fluid pressure is higher than the yield stress of pipe material through a process known to those on the auto frottaging or self-hooping.
3. Connector Pipe (Tube Fitting)The lines between metal to metal contact is a technique commonly used to get a connecting pipe insulation fluid in a high pressure, which is given by the withdrawal of conical shape into the surrounding cavity (Rounded socket). Conical may be done directly on the pipe or paired conical shape can be used. At higher pressures, conical design which is replaceable The mostly used.4. ValvesValves for high pressure-many is the type of needle (needle type). The main flow through conical shape which is controlled by the tip of a needle remains attached to the stand. Seal gland (Gland Seal) is usually required to reduce leakage along the stem shaft.5. nozzleAqueous nozzle change from a liquid to a high pressure jet at high speed in accordance with the wishes of the designer. For a minimum erosion of the nozzle material must be very hard, on the contrary to provide a smooth contour shape of the material should be resilient and easy to do. The nozzle can be made of sintered diamond or Sappire and can be used for parts mounted on a steel holder which obviously requires voltage and tenacity.Diamond, tungsten carbide and special steel has been used to create a quality nozzle. An exit nozzle with a diameter of 0.05 to 0.35 mm will provide a coherent beam of length until 3-4 cm. Methods to increase the length of the emission is to add to the water cutting as much as 1% polymer material with a chain length (a long chain polymer) as polyethylene- oxide with a molecular weight of 4 billion, which will produce a very high viscosity fluid.
With certain additives such jets would be coherent to achieve long-600x diameter. Past the point of separation (break-up point) some cutting force still allows the concentrated liquid core surrounded by hollow beam.
Characteristics of water jet
Using a high velocity stream of abrasive particles suspended in a stream of Ultra High Pressure Air (30000-90000 psi) which is produced by the water pump intensifier.
Used for machining large array of materials, including heat-sensitive materials, fine or very hard.
It does not produce heat damage to the surface or edge of the work piece.
The nozzles are typically made of sintered boride.
Taper produce less than 1 degree in most of the wounds, which can be reduced or eliminated entirely by slowing the process cut.
Distance of the nozzle from the work piece affects the size of the kerf and material removal rate. Typical range is 0,125
Advantages and disadvantages
Ø Excess water jet
1. Can be used for cutting very precise.
2. The time needed very quickly.
3. Environmentally friendly, does not produce waste that damage the environment.
4. More economical for water and abrasive materials easily recycled.
5. Figures very tight tolerances (relatively small) amount of material removed by water jet of about 0.001 ", which means that very little material will be removed.
6. The cutting process that uses water, causing the process
cutting does not generate heat, so that the materials do not undergo undesirable physical changes, such as expansion or melting around the area to be cut. So that the cutting process can be done well.
7. The cutting process does not produce a chip, flake materials, and garbage other cutting results, so that the cutting process takes place with clean.
8. Because the whole cutting process using only high pressure water, so we do not require replacement of cutting tools on each cutting process. Thus, the cutting process can take place more quickly and effectively.
Ø The drawback of using water jet:
1. The initial cost for the purchase of high water jet, but for the next production process when compared with other equipment is very cheap, and save processing time.
2. It needs special care and periodically, as water mixed with abrasive material is forced to pass through a very narrow so it took special attention so that the equipment is in good shape.
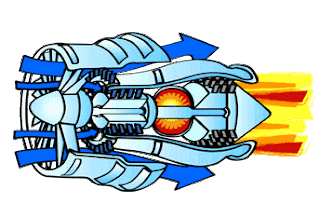

With new review Technology, Water Can Be Used As A Pun Cutting Tool Steels
Understanding Water Jet Cutter
A tool capable of slicing metal or other material that uses a jet of water at high velocity and pressure, or a mixture of water and abrasive. The process is basically the same as water erosion found in nature but very fast and concentrated. This tool is often used in the manufacture or production of spare parts for machines and other devices. This is the preferred method if the material being cut are sensitive to high temperatures generated by other methods. This application can be found in a variety of industries from mining to the space in which is used for operations such as cutting, shaping, carving, and perforation.
History of Water Jet Cutter
water jets be better tools for industrial cutting, drilling, and milling, especially for flexible factory automation. Today the water jet is unmatched in many aspects of cutting and has changed the way many products are manufactured. Many types of water jets that are currently available, including water jet, abrasive water jet, percussive water jets, cavitation jets and hybrid jets.
Principles and Process Works
Cutter is generally associated with the water pump pressure tiinggi level where the water is expelled from the nozzle, cutting through the material by spraying with a high velocity water jet. Additives in the form of suspended grit or other abrasives, such as garnet and aluminum oxide.
There are six main process characteristics for water jet cutting:
Using a high velocity stream of abrasive particles suspended in a stream of Ultra High Pressure Air (30000-90000 psi) which is produced by the water pump intensifier.
Used for machining large array of materials, including heat-sensitive materials, fine or very hard.
It does not produce heat damage to the surface or edge of the work piece.
The nozzles are typically made of sintered boride.
Taper produce less than 1 degree in most of the wounds, which can be reduced or eliminated entirely by slowing the process cut.
Distance of the nozzle from the workpiece affects the size of the kerf and material removal rate. Typical distance is 0.125 ".
X . II
LASER CUTTING
ExplanationWhat is Laser? The acronym LASER stands for Light Amplification Stimulated Emission Radiation.Laser cutting is a technology that uses a laser to cut the material and is usually applied to the manufacturing industry. Laser cutting works by directing a high power laser to cut the material and use the computer to direct it.There are three types of lasers used in laser cutting. CO2 lasers are suitable for cut, make boring, and carve. Neodymium (Nd) is used to make boring where it takes great energy but have the repetition or recurrence is low. While laser neodymium yttrium-aluminum-garnet ( Nd - YAG) is used where very high power needed to make boring and carve. Both CO2 and Nd or Nd - YAG laser can be used for welding
configuration EngineThere are generally three different configurations of the laser cutting machine. Moving materials, hybrid, and the flying optics system. These all refer to how the laser beam moves over the material to be cut or processed. For all this, the axis of motion is usually designated X and Y. If the cutter heads can be controlled, it is designated as the Z-axis.Moving the laser material has a cutter head that does not move, that move is the material to be processed. This method provides a constant distance from the laser generator to the work piece. This machine requires fewer optical, moving the work piece, and the production process at the latest.
Hybrid laser provides a workbench that can move in one axis (generally X-axis) and the cutting head moves on the Y axis This produces a more constant light distribution of the flying machine and can use the optic beam delivery is much simpler. This causes a reduction in force at the time of the distribution system in a flying machine optics.Flying optics laser provides a workbench that is not moving and cutting head moves over the work piece. Cutting the flying optics keeping the work piece remains still during the process and often do not need clamps. Optics flying machine model is the most rapid and has advantages in cutting thin work pieces.The above was written on the system X axis Y to cut flat material. The same discussion applies to engines with five and six-axis, which allows cutting of the work piece in the form and shape of the work piece.
Advantages and disadvantagesThe advantage of laser cutting of mechanical cutting is the work easier and reduce contamination of the work piece. The precision workmanship may be better, because the ability of the laser beam is not reduced during the process. There is also the possibility of reduction in warping the material being cut, because the laser systems have a small heat-affected zone. Some materials are also very difficult or impossible to cut in the traditional way.Laser cutting of metal has advantages over plasma cutting, which became more precise workmanship and use less energy when cutting sheet metal, however, most of the laser cutting machine for metal cutting industry can not thick as that of a plasma cutting machine. Laser cutting machine New operate at a higher power (6000 watts, in contrast with the laser cutting early with power 1500 watt) are approaching plasma machine in their ability to cut thick material, but the capital cost of these machines is much higher than plasma machine cutting.
The main disadvantage of laser cutting is a high power consumption. The efficiency of the laser cutting industry could range from 5% to 15%. Power consumption and efficiency of a particular laser will vary depending on the output power and operating parameters. It will depend on the type of laser and how well the use of laser to work. The amount of power required laser cutting, known as heat input, for a particular job depends on the type of material, thickness, process (reactive / inert) used, and the desired level of cuts.
The amount of heat input required for a variety of materials in various thicknesses using CO2 laser (watt)
The working principle toolLaser cutting can be compared to cutting with a miniature torch is controlled by computer. Laser cutting to the industry designed to concentrate the high amount of energy into a small place. Normally the laser beam cutting diameter of about 0.003 to 0.006 inch when using a laser with a short wavelength. The thermal energy generated by the laser to melt or vaporize material in the workmanship and gas (or mixed) such as oxygen, CO2, nitrogen, or helium is used for removing material evaporates out of the scratches. The light energy is applied directly where it is needed, minimizing heat zona on around the area to be cut.Laser cutting works by directing the output of the high power laser, by computer, at the material to be cut. Material will melt, burn, vaporize, or blown by a jet of gas, leaving the edges with a high quality surface finish.Generating a laser beam is done by stimulating the reinforcing material by electrical discharges or lamps in closed containers. When the reinforcing material is stimulated, internally reflected light by partial mirror, to achieve enough energy to output as a stream of coherent monochromatic light. Mirrors or fiber optics are usually used to direct coherent light into a lens, which focuses light in the work zone. The narrowest part of the focused beam is generally less than 0.0125 inch (0.3175 mm) in diameter.
Process ManufacturingCO2 lasers are used for cutting industrial materials, including mild steel, aluminum, stainless steel, titanium, paper, wax, plastic, wood and fabric. YAG laser is mainly used for cutting and cutting metal and ceramics.Here are some of the machining process of laser cutting:a. Drillingb. cuttingc. grooving
For the manufacturing process, the first process is to make a detailed calculation of the forms, models, sizes, along with a rough picture. Then do the purchase of materials and the manufacturing drawings to CAD or other drawing creation. Then go to the NC machining and can then enter the press room for stamping or forming process. Of NC machining programming reprocessed to 3 & 5 axis laser but previously conducted inspection with CMM programing. Once programming is completed, cutting in using 3 & 5 axis laser cutting machine and then do the inspection and to heat treat by the other party. Then do the finishing coating is carried out also by other parties, and final product inspection for approval and will be shipping. The following flow chart of the above process:
Flow chart laser cutting process
4. Sample calculationTolerances and surface finishingStandard roughness Rz increases with the thickness of the sheet, but decreased with the laser power and cutting speed. When cutting low-carbon steel with a laser power of 800 W, standard roughness Rz is 10 ρm for sheet thickness of 1 mm, 20 ρm for 3 mm, and 25 ρm for 6 mm.
Rz = 12 528 * (S ^ 0.542) / ((P ^ 0528) * (V ^ 0322))
Where:S = thickness of the steel sheet in mm;P = Power dalan kW laser;V = cutting speed in meters per minute
5. Future outlookFor future prospects, laser cutting may be used for the entire process of cutting and forming. Because there has been a laser cutting machine that uses three to five axes to cut work pieces having a shape other than a sheet.
Laser cutting also has the ability to surpass plasma cutting because now been found laser cutting with power four times greater when the initial laser cutting is used. With laser cutting capabilities are almost equal plasma cutting, laser cutting can cut work pieces thick and hard.
In the era of the 2000's, the company that provides services LASER CUTTING LASER CUTTING ENGRAVING or engraving are still extremely rare. MACHINE LASER CUTTING ENGRAVING itself has a variety of types and capabilities vary according to the needs. MACHINE LASER CUTTING ENGRAVING is a technology that uses a machine to CUT and LASER CARVED an object / specific material, but use a computer / Special Software Program to steer.
In 1965, MACHINE LASER CUTTING ENGRAVING first used to drill the diamond. MACHINE LASER CUTTING ENGRAVING created by the Engineering Research Center for Western Electric in 1967. In the early 1970s, laser cutting machine cutters used titanium for aerospace applications.
MACHINE LASER CUTTING ENGRAVING usefulness of this is for the things that are creative, such as Souvenir / Merchandise made of Acrylic (Acrylics), Marble, Glass, Wood, Paper, Rubber Seals, Synthetic Leather and so forth. The types of MACHINE LASER CUTTING ENGRAVING own manufactured according sizes Commonly used in Creative Production Processing the Material / Material. As for the now common use in the Industrial / Business is 40 x 60 cm, 60 x 90 cm, 90 x 120 cm, 90 x 140cm, 130 x 250cm, etc. Along with many kinds of material / material that can be used in MACHINE LASER CUTTING ENGRAVING, then PLASMA / LASER can be adjusted as needed, whether it is only used for scraping / carve / Engraving (ENGRAVING), or to cut / pierce (CUTTING) material so produce pieces according to what you want. Usually for scraping / carve / Engraving (ENGRAVING) takes the Power / PLASMA LASER beam is quite small but it requires a longer time. As for the cut / pierce (CUTTING) takes the Power / PLASMA LASER beam rather large but the time the process is faster than Engraving process.
The ability MACHINE LASER CUTTING ENGRAVING are as follows:
Etching (Marking), laser beam damage the surface of the material, leaving a mark in the form of scratches.
Gravir (Engraving), LASER PLASMA beam scratch the surface of the material with different depths resulting in a form of carving or Image or motif corresponding to Fig what we want ..
Perforate (Perforating / Punching / Cutting), LASER PLASMA rays pierce the material to the shape according to what we wanted.
The advantages of MACHINE LASER CUTTING ENGRAVING LASER PLASMA rays are used as a carving tool / engraving and CUT. The quality of engraving / carving is very nice and detail, as well as have a good artistic value and the process is also very fast.
For LASER CUTTING ENGRAVING MACHINE treatment is to treat Tube Laser Machine, consider cleaning the Optical System Lens, Cleaning the Exhaust Systems, Notice how the replacement and installation of laser tube and Setting Directions Rays and Focus.
MACHINE LASER CUTTING ENGRAVING is still rare used in manufacturing companies, but a lot of demand for objects generated from laser cutting engraving machine is very varied and is able to generate value Outstanding Art and Development of the Infinite.

Laser cutting is a tool used for cutting hard objects such as zinc by using a laser. This one machine being an option many people, especially companies engaged in the industry. Which makes people interested in laser cutting machine because many provide advantages such as, making the job more quickly, the results obtained are nice and tidy, and can cut a variety of complicated patterns. Many advantages are obtained to make people interested in buying a laser cutting machine
type
The type of laser cutting will be selected also important to consider. This is all done so that the machine is sought in accordance with our wishes. There are three types of laser cutting we need to know. What are they ? Here description !!
CO2 lasers, including the type of laser that can be used for cutting, drilling, and sculpt a material. If you want to buy laser cutting is used for cutting, drilling, and chiseling it is strongly recommended to buy the type of CO2 laser alone. Lasers of this type are also included which is pretty good and the price is also quite affordable. In addition, most of this type of choice for the industry.
Neodynium (Nd), a laser machine used to drill using great energy. However, for this one machine requires minimal beats all
Neodymium yttrium-Aluminum-Garnet (Nd-YAG). Machines of this type are used for cutting, drilling, and engraving which requires enormous energy.
For about the usefulness and materials that can be cut from the above three types is the same that can cut materials from leather, wood, aluminum, acrylic, zinc, and so forth. As for the matter of the exact price of each type will be different depending on the type and kind. Most importantly, look for the appropriate type of laser cuting match the desire and finances you have.
X . III
Learning Media Laser cutting
DEFINITIONS LASER JET
Laser (abbreviation of the English language: Light Amplification by Stimulated Emission of Radiation) is a mechanism of a device that emits electromagnetic radiation, usually in the form of light that can not be seen and can be seen with normal eyes, through stimulated emission process. Usually a single laser beam, emits photons in a coherent beam. Lasers can also be said to be the effects of quantum mechanics.The laser system is the most advanced manufacturing technology that is rapidly gaining popularity. Be it in any industry, military, medical, aerospace engineering, automotive, space propulsion or hi-tech manufacturing, processing by laser beam has great benefits and is the best solution to organizational needs and manufacturing equipments as precision laser cutting leads to accuracy and perfection ,
B. PRINCIPLE LASERThe working principle of laser there are four, namely:
1. Laser weldingLaser welding is a process to merge parts of the two components with heat energy. The heat energy in the form of electromagnetic energy, particularly in the form of infrared light.
2. Laser cuttingLaser cutting to the industry designed to concentrate the high amount of energy into a small place. Normally the laser beam cutting diameter of about 0.003 to 0.006 inch when using a laser with a short wavelength. The thermal energy generated by the laser to melt or vaporize material in the workmanship and gas (or mixed) such as oxygen, CO2, nitrogen, or helium is used for removing material evaporates out of the scratches. The light energy is applied directly where it is needed, minimizing heat zone at around the area to be cut.Laser cutting works by directing the output of the high power laser, by computer, at the material to be cut. Material will melt, burn, vaporize, or blown by a jet of gas, leaving the edges with a high quality surface finish.Precision laser cutting is more popular and effective than the traditional cutting process. The reason is obvious, the accuracy of which holds the key to the success of laser precision cutting.The advantages of laser cutting:
1) Flexible and fast but cost-effective mechanism.
2) In a precision laser cutting, the material is not in contact with the cutlery.
3) Precision cutting lasers are used for different types of materials and thicknesses.
3. Laser drillingLaser drilling system providing accurate holes with maximum precision and processing time is very fast. If such does not consider the quality, then drilled a suitable laser is based on the needs of the industry, then that is the solution of manufacturing industry in the long term.
4. Laser engraver
Laser engraving is the practice of using lasers to engrave or mark an object. Lasers operate by focusing a beam of light, or laser, the site refers to an object to cut rather than using a solid object. A computer system with vector graphics software will also be required. Instructions given to the laser cutter through software that deciphers design geometry to numerical C N C machine code. Lasers also can retrieve data from images created with the help of computer-aided design software (CAD). Despite this complexity, very precise carving and clean can be achieved at a high level.There are three main genres of engraving machines:a. The most common is where the X Y table, the work piece (surface) stationary and the laser moves in X and Y direction vector images. Sometimes the work piece moves in the Y axis in the X axis laser
b. A second genre is for cylindrical work piece (or work piece mounted flat around the cylinder) in which the laser effectively across a helical either on / off pulsed laser to produce the desired image on a raster basis.
c. In the third method, both the laser and the work piece is stationary and galvo mirrors move the laser beam on the work piece surface.
C. Advantages and Disadvantages LASERAdvantages of the laser:1. Concentrated on lightIn short, highly concentrated laser beam of light in specific wavelengths. Likewise, as with all laser light can be controlled and redirected using mirrors and lenses. Also a laser, being that the actual light, running at the speed of light.2. Can be used in a variety of intensitiesLaser show up in different intensities, depending on the amount of energy used to create it. Thus, a low power laser is usually used in light shows and for things like gun sights that are very safe to focus on the hand. However, a high-powered laser would quickly cut right through someone's hand.3. Cutting high-poweredOne of the many using high powered lasers is cutting. The reason that the lasers make good cutting tools are many. First, they do not generate dust like other standard cutters, so its great for cutting in sterile, dust-free working environment.4. There is no frictionThe laser also works very well for cutting contoured surfaces that would otherwise be very difficult to cut with a standard cutting device. Laser cutting also does not create friction and require no lubricant. No friction means that no heat is generated that can cause damage to the heat-sensitive thermal cut situation.5. Material lost very littleLaser cutting is also very precise cutter that removes very little material. In many manufacturing situations the laser cutter is a great choice for this reason. Laser cutting has also been developed into surgical instruments that can be inserted into a very small hole to make tacit smooth cutting operations.
Disadvantages laser:1. Irradiation with laser usually can not be done just once but repeatedly. Though the cost for a relatively expensive irradiation.
2. Side effects commonly reported use of lasers is the appearance of heartburn after irradiation. It is caused by exposure to laser light that is absorbed into the body tissue to be converted into thermal energy causing a feeling of heat.
3. The laser action requires certain conditions. For example, in the radiation room should not be contained alcohol. When a laser beam is bounced off, it is impossible to burn objects or parts that contain alcohol.
X . IIII
Working Principle Laser

The word LASER is an acronym for Light Amplification by Stimulated Emission of Radiation, which means the magnification of the intensity of light by stimulated emission. The key word is "magnification" and "stimulated emission" that will become clear later. Today, 30 years after the discovery, said lasers have become everyday vocabulary. Equipment using laser components can be found everywhere, such as price code reader at the supermarket checkout, laser printer, compact - disc player, guides a jet and laser show in a music festival.Laser is a coherent monochromatic light source and very straight. How it works include optics and electronics. Scientists categorize usual in the field of quantum electronics. Actually, the laser is a development of the maser, the letter M here stands for Microwave, means of microwaves. The workings of the maser and the laser is the same, just that they are working on different wavelengths. Lasers work on the spectrum of infrared to ultra violet, while the maser emits electromagnetic waves with wavelengths much longer, about 5 cm, a bit shorter than the TV signal - UHF. Lasers that emit visible light is called laser - optics.
Working Principle LaserLaser produced from the process of relaxation of electrons. At the time of this process, the number of photons will release a bunch of different light flashlight laser emission occurs regularly while the flashlight emission occurs randomly. In the laser emission will generate light having certain wavelengths. different from the flashlight emissions would generate a lot of light with wavelengths. processes that occur are the electrons on the state of the ground state (the valence band) got the status of energy then rises toward the conduction band (excitation) and then the electron back to its initial state (ground state) followed by some of the photons are separated. Then that energy carried large enough it needed a resonator This resonator can be either a lens or a mirror that is often used is that of lenses and mirrors. when inside the resonator then the photons will bounce against the walls of each resonator so it is strong enough to leave the resonator. laser powerful enough to use as cutting tools for instance are a powerful laser CO2 laser is widening its low-level and high-energy picture.
Laser applicationsThere are so many laser applications, such as laser pointer (for presentations), lasers for alignment direction of the shot, cutter or a cutter that has been widely used in the steel industry and electronics, laser hair Removal to remove hair. And there is also a laser for wound healing. While other applications for analysis, for example:1. Spectroscopyis a technique for analyzing an ingredient often used in these applications is the FTIR (Fourier Transform Infra Red) uses an infrared laser for measuring the level of uptake of a substance. then matched to the table so it can be any material contained in until tested.2. Material processing,Usually used for laser cutting which is often used is a CO2 laser.3. Distance MeasurerTo determine the distance of the moon to the earth is done with this method because of the speed of light is already known, by measuring the time lag will be obtained a great distance.4. Laser CoolingLaser cooling utilizing this technique. method of trapping atoms. A method where numbers of atoms are trapped into a box that has been assembled into the electric field and a magnetic field and then irradiating the wavelength-out, then slow them down, and then beam it to cool. This process is known as Bose-Einstein Condensate.
A laser is a device that emits electromagnetic waves pass through a process called spontaneous emission. The term laser is an acronym for light amplification by stimulated emission of radiation. Generally very coherent laser beam, which means that the light emitted does not spread and narrow frequency range (monochromatic light). Laser is a special part of the light source. Most of the light source, emits incoherent, wide frequency spectrum, and phase varies with time and position. Work area laser device is not limited to the visible light spectrum but could also work on a wide frequency range, therefore, the device can be INFA red laser, laser ultra violet, X-ray laser, or a visible laser.
Laser is said to be good if the frequency or wavelength emitted is single. Laser power can be varied ranging from nano watt for trillions watts continuous laser for the laser pulse. Laser is a major component in modern communication systems today. In addition, the laser is also used as a probe for reading a data CD or DVD, as a light source in bar code reader, navigational aids in the military sphere, tools operating in the field of medicine, and many other applications.In general, a laser device consists of a light beam amplifier media (gain medium), pumping energy source (pumping source), and an optical resonator (optical resonator).

Media amplifier is a material that has the properties can increase the intensity of light by means of stimulated emission. While the optical resonator, simply containing an array of mirrors are mounted facing so that the light beam can move back and forth. One mirror is somewhat transparent, so that it can function as an exit point the laser beam (output coupler). Beam of light passing through the media will be strengthened power amplifier. If the surrounding area is a mirror, then the light will move back and forth and passed through the amplifier medium many times. Thus light will undergo strengthening several times. Having gained power, the light can get out past the mirror that is somewhat transparent as a laser beam.

The process of entering the energy as a condition for the occurrence of so-called power amplification with pumping (pumping). Energy pumped can be either an electric current or a beam of light with different wavelengths. To pump energy in the form of light, can be used flash or semiconductor lasers. In addition to the main components of the above, a laser device is usually equipped with some supporting components to produce a sharp laser beam.
Materials reinforcing media may be a gas, liquid, solid, or plasma. Media amplifier absorbs the energy pumped and resulted in a number of electrons excited to a higher energy level. Particles can interact with light in ways absorb or emit photons. Light emission can occur spontaneously or by means of stimulation. When the number of electrons at a level of excitation exceeds the number of electrons in the energy level at the bottom, then the population inversion has occurred. This can result in stimulated emission of more than absorbed. Thus the light has strengthened. If the amplifier medium is placed inside an optical resonator, the light strengthening can occur repeatedly and then produces a laser beam.
Optical cavity is one form of the resonator. Cavity contains a coherent beam that is covered by a reflective surface that allows the light beam moves back and forth through the amplifier medium. The light that moves back and forth within the cavity may experience a loss of power (loss) caused by the absorption or diffraction. If the reinforcement in the media is greater than the power loss in the resonator, the laser power will increase exponentially. In any event stimulated emission, number of particles will move from the excited energy level to the ground state, this will reduce the capacity of the amplifier medium. To restore it to the condition stimulated, must be pumped back with a certain energy. The amount of energy pumped must consider the threshold of media amplifier and power loss within the cavity. If the power is pumped too small, then the resulting emissions would not be enough to offset the loss of power due to absorption within the cavity. Conversely, if the energy pumped too large, then the media will accelerate the degradation of the amplifier so that shorten the life of the user. Therefore, the necessary optimization of the energy pumped minium limit (lasing threshold), so that the laser beam generated significant with a long service life.
Laser can operate in continuous mode (continuous wave) with constant output amplitude or in the form of pulses. Laser pulses can be generated by using Q-switching, mode locked (mode locking) or gain switching. Lasers in the form of pulses can generate enormous power. In continuous operation mode, the laser beam is generated relatively constant over time. The process generated from a population inversion takes place continuously using a stable source of energy pumping. While in pulse operation mode, the laser beam is generated vary with time back and forth with the mode on and off. Laser pulses are usually created with the aim to produce enormous power laser radiation with a short time.

Working Principle Laser
Laser produced from the process of relaxation of electrons. At the time of this process, the number of photons will release a bunch of different light flashlight laser emission occurs regularly while the flashlight emission occurs randomly. In the laser emission will generate light having certain wavelengths. different from the flashlight emissions would generate a lot of light with wavelengths. processes that occur are the electrons on the state of the ground state (the valence band) got the status of energy then rises toward the conduction band (excitation) and then the electron back to its initial state (ground state) followed by some of the photons are separated. Then that energy carried large enough it needed a resonator This resonator can be either a lens or a mirror that is often used is that of lenses and mirrors. when inside the resonator then the photons will bounce against the walls of each resonator so it is strong enough to leave the resonator. laser powerful enough to use as cutting tools for instance are a powerful laser CO2 laser is pelebaranya level low and high energy picture.
Laser applications
There are so many laser applications, such as laser pointer (for presentations), lasers for alignment direction of the shot, cutter or a cutter that has been widely used in the steel industry and electronics, laser hair Removal to remove hair. And there is also a laser for wound healing. While other applications for analysis, for example:
spectroscopyis a technique for analyzing an ingredient often used in these applications is the FTIR (Fourier Transform Infra Red) uses an infrared laser for measuring the level of uptake of a substance. then matched to the table so it can be any material contained in until tested.
material processing,Usually used for laser cutting which is often used is a CO2 laser.
hodo meterTo determine the distance of the moon to the earth is done with this method because of the speed of light is already known, by measuring the time lag will be obtained a great distance.
laser CoolingLaser cooling utilizing this technique. method of trapping atoms. A method where numbers of atoms are trapped into a box that has been assembled into the electric field and a magnetic field and then irradiating the wavelength-out, then slow them down, and then beam it to cool. This process is known as Bose-Einstein Condensate.

Figure Laser Cutting Machine



Values High Aesthetic laser cutting
Application of products that emphasizes a high aesthetic value, such as for the interior design and customer end-products, will appreciate the smooth and shiny pieces that do not require edge finishing work is expensive and time consuming. Because the laser cutting process does not use pressure apart from Assist-gas, the material used can be flexible on the thinnest metal sheets, until the thickest though.
Accurate dimensions according to the design and the impact of low surface oxidation also ensures advanced workmanship such as folding, welding and coating can be done much more easily than with laser technology.
X . IIIII
how to create a simple laser cutter
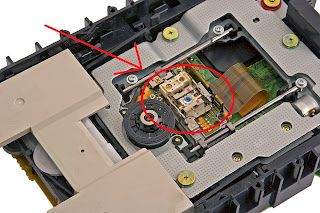
For this work you are required to master the skill of electronics and soldering techniques are good, or accompanied by people who master it. The execution can not be done in a hurry because it takes patience to disassemble a used DVD hardware unused small parts.
Before uninstalling you should need to know the supporting components that we need later on, what are its components:
1-Adjustable Voltage Regulator LM317T
1- 100 ohm potentiometer
2- 10 ohm resistors
1- 1N4001 Rectifier Diode
1- 47uf 35v Capacitor
1- PCB Board
1- tin solder
1- Soldering Iron
1- Power Switch (advised that there is a push button on)
1- 12x30mm Aixiz laser housing
2- Spools of wire (Red and Black)
Screwdriver
6V power supply
digital multimeter
step I .
step II .
Once separated the outer cover, the time issued its innards component slowly
step III
step IIII
step IIIII
Then the raft as shown in the circuit below
Once we assemble all of you can put a homemade laser into small squares as you like, this complete reference laser manufacture can see in the blog making of this DVD laser. In addition, we will provide some animation that I managed to create just how devastating the effects of this laser beam.
Unlike the laser beam from the mini dvd etched, blue laser light is very strong maximum power 5000mW as to burn any material that way.

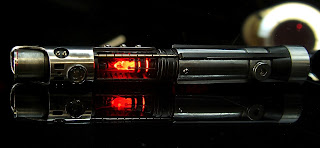
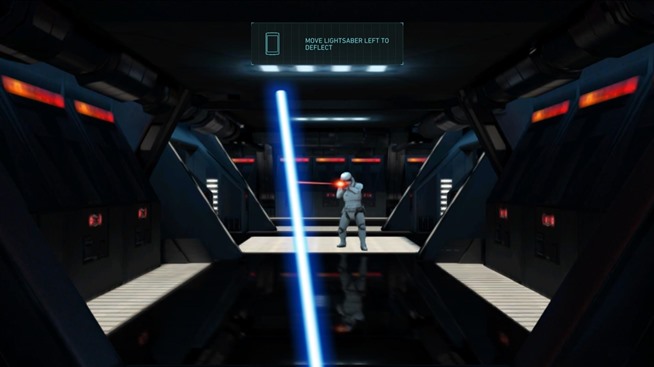
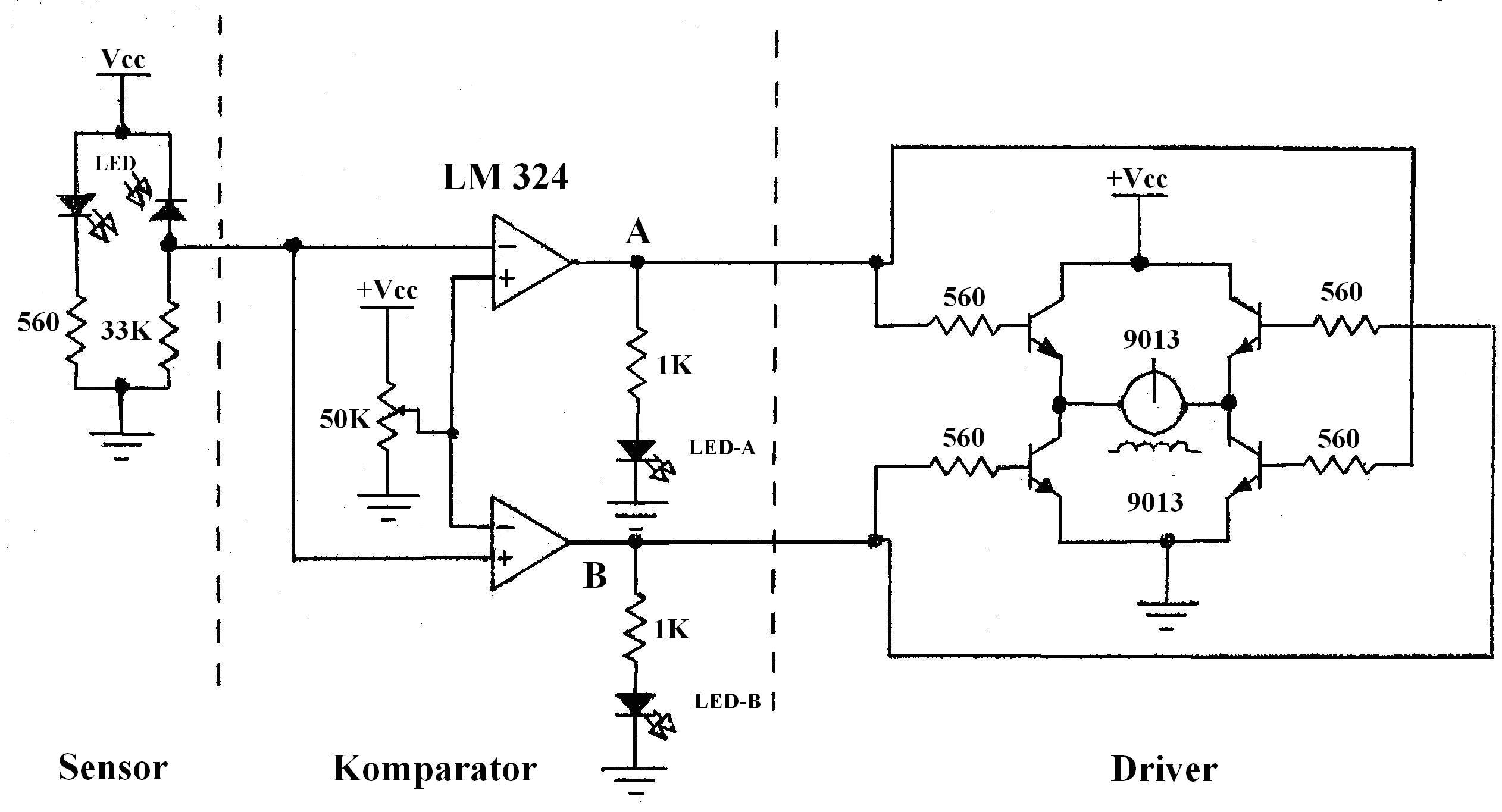
Figure Simple circuit movers
This blog is very interesting and worth spending time on reading.
BalasHapusLaser Cutting Stainless Steel Sheet
Nice information shared here.... Thank you.
BalasHapusWater jet Coimbatore
Great post.I'm glad to see people are still interested of Article.Thank you for an interesting read........
BalasHapuslaser line generator