

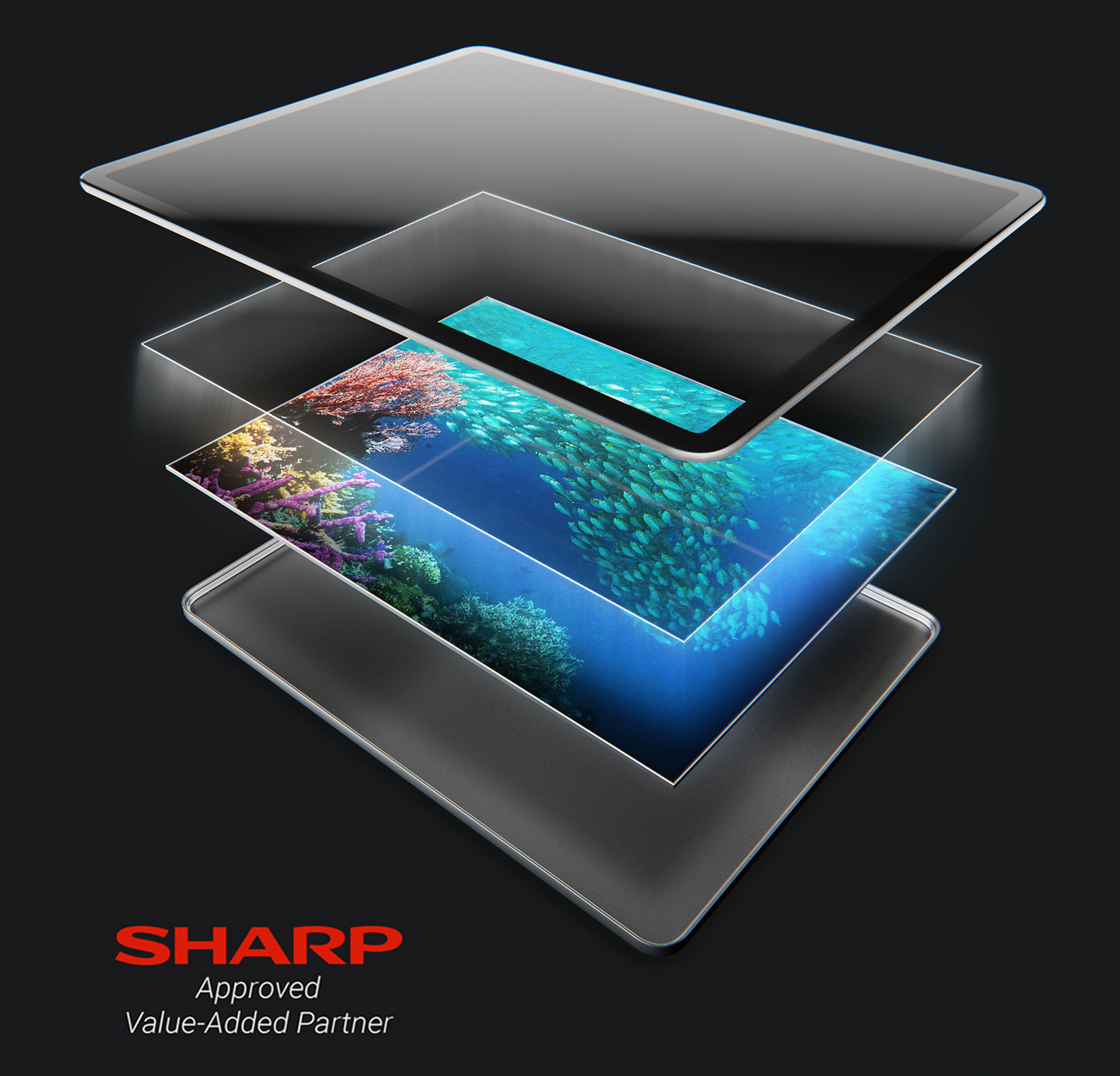
XO__XO How To design LED Display ?
LED-based signage and matrix displays are bringing new dimensions of versatility and eye-pleasing visual effects to a growing number of outdoor and indoor applications. Recent advances in LED technology have even made it difficult to distinguish still images on their high-quality displays from traditional printed or painted billboards. In this tutorial, Texas Instruments takes a detailed look at the essential technical principles of LED display systems and the engineering considerations required to design them using arrays of discrete LED lamps.
LED driving basics
First we will compare the various LED driving circuitries to determine the best method.
Connecting a voltage source
It is well known that an LED lamp (or diode) starts turning ON with enough forward voltage (VF). When ON its forward current emits light. From this basic knowledge, one can come up with the first option in Figure 1a but it will not work. Because an LED current is an exponential function of its voltage bias (equation 1), light intensity from the LED lamp is very sensitive to the voltage. In most cases the high current condition turns the normally long-lived LED into a very expensive flash bulb.
Here’s why Figure 1a will not work. In equation 1, IS, RS is a constant, depending on the LED product, and whether VT is the thermal voltage. Assuming a series resistance RS is ideal and zero, only 0.1V of VF change makes 47 times difference in ILED.
For example, a target LED current value 20 mA jumps up to 1A with only 0.1V difference of its bias current. Even taking into account a realistic RS value, a real LED device still shows 10 to 20 times difference with a 0.1V bias difference.

Figure 1 Comparing three LED driver circuits
Voltage source with current limit resistor
Now let’s examine Figure 1b. A current limit resistor RLIMIT is added to protect an LED lamp. Because of the limit resistor, the lamp does not blow up. Still, it is not great at controlling LED light intensity in video display applications. An LED curve and a load curve by RLIMIT determine its LED current value. As shown in red or blue annotations, this LED and resistor has variations of forward voltage and resistance from manufacturing errors. These error factors change the LED current (green) at non-negligible levels.
Constant current source
Figure 1c employs a constant current circuitry instead of resistors. This constant current driver circuit regulates an LED current directly at the target value. The LED conducts a certain value, no matter how much VF variation the LED lamp has from its manufacturing process. Because the light intensity of an LED lamp is strongly tied to charges crossing its PN junction, this constant current driver method is ideal to get uniform light output from LED lamps.
Furthermore, it is well known that an integrated circuit (IC) provides good matching circuit pairs. This is another benefit of selecting a constant-current method. Figure 2 shows a basic output stage structure of LED drivers. Many LED driver ICs in the market have a reference current setting terminal IREF, and this reference current is constant-current-mirrored to its output terminals.

Figure 2 A basic LED driver IC output configuration
Figure 2 illustrates the results of this discussion, a basic output circuitry configuration of LED drivers.
Driving in color
Thus far, we have been able to determine how to drive an individual LED lamp. The next step is to achieve full color light output for video display systems. By combining varying shades of light’s three primary colors, red, green and blue (RGB), any color can be generated. A familiar example is a color selection tool on a personal computer (PC).
Gray scale control by digital or analog
A PC's operating system blends three colors in 256 steps (8 binary bits each) or more to display a full color pixel. For the LED display system, the same concept of step color intensity control is needed. The goal is to achieve step control, or gray scale control in LED driver design.
Your first decision should be whether to use digital or analog control. As explained earlier, the total charge count crossing a PN junction determines light intensity, so both digital and analog methods can control the light intensity. Figure 3 illustrates 50 percent gray scale control in digital and analog methods. In a total 256-step example, this 50 percent indicates a 128 gray scale target.

Figure 3 Fifty percent intensity control in digital and analog
LED current and color change
At this point, the effects of current change on the wavelength value of LED light output needs to be considered. A changing wavelength means changing color to the human eye. Figure 4 shows a green color LED lamp example. Usually, 510 nm widely represents green in the industry. Thus, most LED lamp manufacturers design a lamp to have 510 nm at maximum-rated current of LED lamp products. In Figure 4, the wavelength reaches 510 nm as the LED current rises. The best way to get green color is to always drive a lamp as close to its maximum rated current as possible. This explains why using digital control is better than analog control.
Another benefit of choosing digital control is the ease of implementing the control on LED driver ICs as a digital circuit block. For a gray scale control over a 256 step range, digital control costs less than analog control.

Figure 4 A green LED current vs. wavelength example
This ON/OFF digital control is known as a pulse-width modulation (PWM) control, or PWM dimming. Now PWM control switches are added to Figure 2.
How to form a matrix or 2D image
RGB LED lamps are tiled to form a 2-dimensional (2D) image.
Structure of display systems

Figure 5 LED display system consists of module / panel / display
RGB LED lamps are arranged to form a square-shaped base structure, or module. It usually consists of one PCB with a pixel array of 16×16 to 64×64, depending on applications. Multiple modules are combined to form a mechanical and system structure, or panel. LED display system vendors usually provide panels. Each panel has a mechanical frame to hold multiple modules. It contains one or more control units to provide a power distribution, data interface and processor. At a display system building site, such as stadium screens or road side billboards, multiple panels are installed to form a final display. At the construction site, all the data and power cables from each panel are routed to central control units.
Pixel pitch
One LED display system comprises a huge number of LED lamps and a large power supply. Optimizing LED lamp density is a key item to consider when designing a system. This density of LED lamps is discussed as a distance of each pixel, or pixel pitch. If the pixel pitch is too tight, it won’t improve image output quality once it is finer than the human eye can detect, and adds to the cost. The human eye can distinguish two individual light sources when these two points form 1/60 of one arc degree (= one minute of arc).

Figure 6 The ability of the human eye to detect resolution
Figure 6 illustrates how the human eye distinguishes pixel pitch DPP1 is calculated in equation 3 where L is a viewing distance.
In best practice, DPP1 is considered overkill in that roughly three times of DPP1 is good enough for a good quality video system. DPP is the guideline in equation 4.
An easy way to remember equation 4 is this:
Required Pixel Pitch in millimeter (mm) = "Viewing distance in meter"(m)
For example, a system with a viewing distance of 5 m requires 5 mm of pixel pitch to achieve good resolution. Another visual example is shown in Figure 7, which illustrates how too low of a pixel pitch degrades the output image quality. The 12.5 mm pixel pitch image (top) looks rough, and is not discernable at close distance. However, the image starts to make sense when viewing it at arm’s length, which is similar to viewing the 5 mm pixel-pitch image (bottom). This is a good example of the relationship between the viewing distance and pixel pitch.

Figure 7 Comparison between different pixel pitch and viewing distance
Static drive and time multiplexing drive
From Figure 2, the cathode side of LED lamps is driven by LED driver ICs common in today’s market. Here, drive circuitry for the anode side of LED lamps is reviewed. With the benefit of employing constant-current drive at the cathode side, the anode side is expected to supply just enough voltage. Still, an important decision is needed: how to drive the anode side!
Figure 8 compares static and time-multiplexing anode drive systems. The static anode drive configuration is very straightforward: one LED driver IC drives one LED. When designing a system with a huge number of pixels, the static anode drive requires a huge number of LED driver ICs. In contrast, the time-multiplexing anode drive system uses fewer LED driver ICs by sharing one IC with multiple LED lamps. A tradeoff with the time-multiplexing drive is that output LED light intensity is reduced due to time-sharing.
In outdoor display systems, very strong LED output is required to overcome the brightness of the sun in order to deliver the image to the human eye. In such outdoor systems, the static anode drive is preferable. On the other hand, in indoor systems, the time-multiplexing anode drive is a good method to reduce system building cost.
Since time-multiplexing has become the most commonly-used technique in today's applications, we'll use it for the applications we discuss in the remainder of this document.


Figure 8 Static and time-multiplexing anode drive
How to create movie/video images
Earlier we discussed how to display a still image. If we keep changing that still image, we can turn it into a movie or video.
Frame rate/frame refresh rate
Old analog TV systems used to show 24 different still images in one second, for a frame rate of 24. When an analog TV camera views another analog TV screen, it creates a zebra mix comprising video images and black bands (Figure 9). This is caused by the synchronized TV camera and TV screen scanning rate. The same problem occurs when a camera taking a shot of an LED screen uses the time-multiplexing anode drive. Examples include a TV camera capturing an image of a concert stage with an LED display enlarging a performer on the back wall, or a TV camera viewing a stadium score/display panel at a sport event. To avoid this issue, LED displays today need to operate faster than camera systems, especially in a professional use LED display market.

To meet this faster operation requirement, many LED display systems repeatedly show the same image within one frame period, known as the frame refresh rate. Figure 10 shows the relationship of the frame rate and refresh rate. There are only two frame images: A and B. Each frame repeats “image x” twice. Thus, this example is "Frame Refresh Rate" = 2 ×"Frame Rate".

Figure 10 Frame rate and frame refresh rate
In a common LED display system, a frame rate is in the range of 50 Hz to 120 Hz, and a frame refresh rate is in the range of 50 Hz to 2 kHz.
ON/OFF control driver or PWM control driver
To meet system requirements of frame rate and refresh rates, a decision needs to be made between two ways to implement the logic circuit. First is the ON/OFF control driver, and the second is the PWM control driver.
Figure 11a shows a system with an ON/OFF control IC, which has an ON/OFF register that corresponds with each bit to its output. A logic high of the register bit turns ON the corresponding output; a logic low turns it OFF.
Figure 11b shows a system with a PWM control IC, which has a gray scale reference clock input terminal that references the clock counter. Plus the IC has a set of registers that hold gray scale logic code. PWM comparators compare and generate PWM output patterns from the counter and gray scale (GS) register.
For both types of driver ICs, two operations are performed in parallel:
- The constant current driver block drives its LED lamp array based on inputs from the current display cycle data.
- Meanwhile, the data for the next display cycle is received into the shift register.


Figure 11 LED display with ON/OFF control IC and with PWM control IC
Summary
Beginning with a driver circuit for a single LED lamp, a complete LED driver IC structure is derived by reviewing details of the LED lamp physical characteristics; physical layout and structure of display system; and static and time-multiplexing control.
in parts 2 addresses data transfer between an image processing controller and LED driver ICs with examples provided. LED display driver IC-related features and topics will also be examined.
LED signage and matrix displays are an integral part of the 21st century landscape. Their quality is becoming so good that it's becoming increasingly difficult to distinguish LED images from traditional billboards.
Part 1 of this three-part series addressed the technical and engineering steps necessary to design an LED display system from individual LED lamps. In Part 2 we'll visit the remaining necessary steps to complete the LED system. This will lay the groundwork for Part 3 which will introduce several important features becoming commonly available on advanced LED display driver ICs, as well as tips on how to make best use of them.
How to transfer display data
To begin, let’s review how data is transferred between the image processing controller and the LED driver ICs. Table 1 lists the design specifications of the example application we'll be working with in Part 2.
Table 1 Example specifications.

System with ON/OFF driver IC
In a basic ON/OFF driver IC system, such as the example in Figure 1 (Originally Figure 11a in Part 1), an image processing controller must generate a pulse-width modulation (PWM) pattern map on its memory.

Figure 1 LED display with ON/OFF control IC
This pattern map consists of an ON/OFF status (bit) of each output managed by this controller per each gray scale PWM clock (Figure 2a). The ON and OFF patterns of OUTN and OUTM are rendered for one entire frame period (5 ms), plus a few more clocks. Once the controller finishes rendering the memory map, the controller sends out the resulting pattern of logic-H and logic-L, (along with each red line) to the ON/OFF control of the LED drivers’ shift register.
For this system, the data transfer rate fDATA(ON/OFF) is expressed in equation 1.
The parameters in Table 1, fDATA(ON/OFF), are calculated as 105 MHz. For large outdoor display systems, delivering 105 MHz logic signal on its PCB is neither practical nor realistic. Most LED driver ICs cannot receive 105 MHz logic inputs anyway. In Table 1, the ON/OFF control driver cannot meet the target specification. A realistic frame refresh rate (FRR) needs to be downgraded to 50 Hz. The result is fDATA(ON/OFF) = 26 MHz.

Figure 2 PWM data timing chart for ON/OFF and PWM drivers.
PWM driver IC system
In the PWM driver system used in Part 1, there are two logic signal speeds (or frequency parameters) to consider. The first is a gray scale reference clock frequency fGSCLK(PWM):
Using the parameters in Table 1, fGSCLK(PWM) is calculated as 819 kHz, which is easy to achieve.
The second is a data transfer frequency fDATA(PWM):
The second is a data transfer frequency fDATA(PWM):
Based on Table 1, fDATA(PWM) is calculated as 26 MHz. Note that a PWM control driver IC can repeat the same image data without resending gray scale data and the frame rate (FR) used in equation 3, which is unlike using FRR in equation 1. Figure 2b shows a simplified diagram of how PWM control driver ICs can reduce the data transfer rate.
ON/OFF versus PWM control drivers
There are pros and cons when choosing between ON/OFF and PWM control drivers. The choice depends on your display system’s needs. A generic comparison is listed in Table 2.
Table 2 ON/OFF versus PWM control ICs


So far, a PWM control driver might look to be a better choice. Before you decide, however, let’s consider an important benefit of the ON/OFF control driver. The image processing controller has the flexibility to generate PWM patterns for all outputs by its software. For example, the controller can achieve a unique spread-spectrum PWM pattern to avoid potential electromagnetic interference (EMI), or a special gamma-correction.
Driver ICs improve video image
Now, let’s review the various LED driver IC functions.
Dot correction
Because of various error factors, an LED display must be calibrated in order to present a uniform brightness profile across each of its LEDs. Figure 3a represents a non-calibrated display showing the entire white image data. The inconsistencies may be due to one or more possible error factors such as, but not limited to:
- Current-to-light conversion efficiency difference of each LED lamp
- Forward voltage difference of each LED lamp
- Driving current error of LED driver ICs
- Error of reference current setting resistor connected to LED driver ICs
- Light output loss caused by physical dimension error of LED lamps
A dot correction (DC) function has the ability to adjust driving current of individual output terminals by referring to several bits of digital data. Thus, a dot correction is like a set of current-output digital-to-analog converters (DACs). An example of a dot-corrected calibrated display is shown in Figure 3b.

Figure 3 Examples of un-calibrated image (right) and dot correction (left).
The schematic in Figure 4 depicts a circuit element which implements the dot correction function using DCx signals (highlighted in red text).

Figure 4 LED display with PWM control IC including dot correction and brightness control.
In Part 1, we confirmed that the LED current change shifts its output light wavelength (color). Because the dot correction function adjusts output current amplitude, a calibration attempt with a dot correction causes another smaller color shift. A best practice is to utilize visual inspection equipment which can digitize output color from a RGB lamp. Now, all lamps can be set to have the same target digitized value.
Brightness control
Brightness control (BC) is a similar function to dot correction adjusting output current amplitude. However the brightness control changes all IC outputs simultaneously.
Brightness control is an effective way to adjust whole display brightness. As with adjusting the brightness on your notebook PC, it depends on the ambient brightness. For example, an outdoor display system in bright daylight needs the highest light output to overcome the bright sunlight. However, the same outdoor system doesn’t need near as much light output at night.

Figure 5 Example of brightness control.
Figure 5 shows how brightness settings can change the same image, depending on ambient brightness. Figure 5a is in a bright room while Figure 5b is in a dark room – but they both look the same to the human eye. Note: The BC signals which implement the brightness control function illustrated here are shown in the previous schematic (Figure 4), highlighted with green text.
Part 3 explores some of the issues which affect the image quality and reliability of LED displays, and the technologies and design techniques used to deal with them.
Part 1 of this three-part series introduced the technical and engineering steps necessary to design an LED display system from individual LED lamps. Part 2 provided the remaining steps needed to implement a basic LED display. In the third and concluding installment of this tutorial, we'll explore some of the issues which affect the image quality and reliability of LED displays. We'll also become acquainted with the technologies and design techniques commonly used to deal with them.
Anti-ghosting/ghost-canceling/pre-charge FETs
Ghosting, spike noise, or phantom noise are unwanted lighting effects caused by Anode gate "float" which can occur in time-multiplexed LED driver. Since LED lamps (PN junction of diodes) have relatively high levels of capacitance, their residual charge can keep triggering capacitive charge transfers between the floating nodes. And every time there's forward electron flow through a PN junction
The situation where this phenomenon is most is a diagonal line image. Figure 1b shows an example of so-called "ghosting" caused by anode float. Modern LED driver ICs, such as the TLC59283, employ so-called "pre-charge FET" circuits which eliminate these ghosting effects (Figure 1a). As explained earlier, the root cause of ghosting is stray charges on the LED's anode which forward-bias its PN junction and cause it to light at unwanted times. These pre-charge FETs are designed to insure the LED lamps remain reverse-biased and unlit except when the driver circuit is actually on.

Figure 1 Pre-charge FETs (right) and the ghosting (left).
Blank bands, black bands and Enhanced spectrum PWM
LED display designers face several other challenges as they strive to produce ever-larger products which deliver the pest-possible image quality. One of the biggest issues is eliminating the blank bands which can occur when capturing the image of an LED display on a camera. As we discussed in Part 1 of this series, this is caused by "slow-synching" between the display and the camera. This can be avoided by using a faster frame refresh rate (FRR). Unfortunately, larger displays require faster FRRs. As a result, it becomes increasingly difficult to achieve an FRR that's sufficiently high to avoid slow-synching effects as display size increases.
Another issue is black bands which appear when a camera captures a display image image at the moment some of its LEDs are OFF. This can be avoided by keeping the LED lamps ON during a camera scan period but, as the following example will show, that's not always possible.
Black bands become a more significant problem as PWM control LED ICs grow to control larger, higher-quality displays where the length of their PWM operation cycle time grows longer. For example, the latest 16-bit PWM control with a 25 MHz reference clock requires 2.6 ms = 216 bit / 25 MHz, which is a frame refresh rate of 381 Hz. Here, a gray scale code of 128 for a total of 216 clock cycles generates 5.1 us (= 128 / 25 MHz) of ON time, and 2.6 ms minus 5.1 us of OFF time. The camera captures LED lamps in the OFF state during this 2.6 ms period.
Black-banding can be mitigated using a technique called enhanced-spectrum PWM (ES-PWM), a method for PWM generation which divides one long PWM cycle into shorter sub-PWM cycles. In the above example, if 128 clocks of the ON period are divided into 16 periods of 8 clocks each, creating an effective FRR of 6 kHz (= 381 Hz x 16). At 6 kHz, the refresh rate is high enough to avoid black bands with most cameras.
An original PWM code cannot always be equally divided. In this situation, the ES PWM function splits one ON period into rounded integers. For instance, to divide a gray scale code of 100 into 16 pieces, the ES-PWM circuit generates twelve of 6 clocks and four of 7 clocks to maintain a total gray scale of 100 (= 6 clock x 12 + 7 clock x 4).
Detecting LED open, LED short, & output leakage conditions
Many LED display systems are controlled remotely, making it difficult for an operator to detect any failures. Because the human eye is sensitive to a faulty lamp that remains constantly ON or OFF, the failure of even a few lamps can degrade the quality of a viewer's video experience. As a result, many displays implement ways to detect open and shorted LEDs, as well as output leakage conditions which can cause LEDs to malfunction.
An LED open detector (LOD) function monitors LED lamps for open-circuit failures. Under normal circumstances, a driver IC’s constant-current output terminal stays at the head room voltage required by the constant-current circuit. When the constant-current circuit's LED fails and becomes an open circuit, the constant-current circuit drives its output terminal to almost zero voltage. The LOD function detects these telltale voltage changes and generates an error signal.
Similarly, an LED short detection (LSD) monitors the LED lamp for conditions which indicate the LED, and/or its driver are short-circuited to its anode's supply voltage. When the LED fails in a shorted mode, its output terminal reverts from its normal bias state to the full voltage applied to the anode. The LSD function distinguishes this voltage difference and generates an alarm signal.
An output leakage detection (OLD) differs slightly from the first two safety functions. It's designed to detect conditions which arise when an LED is forced into its ON state due to debris forming a conduction path from an output terminal to the ground. When this occurs, the LED is turned ON – no matter what the output of its constant current-circuit driver happens to be. The OLD element produces a small amount of current at its output terminal node which it uses detect any leakage path by monitoring the terminal voltage.
Low gray scale enhancement
The human eye has more sensitivity to darker light sources than brighter lights. In other words, it recognizes which of two dark light sources emits more photons. However, when the human eye is saturated with bright light from two different sources, it cannot distinguish the difference.
For handling video image, low gray scale data requires more attention. Here a technique like gamma correction is widely used. As for LED display systems, software programming can implement a gamma correction function with both ON/OFF and PWM control drivers.
Recent LED drivers, like the , integrates more proactive improvements on low gray scale handling. A common problem is that red LED lamps are stronger than green and blue with dark white image output, even though red, green and blue all have the same low gray scale data. This occurs because red LED lamps can turn ON longer than green and blue lamps due to its lower forward voltage. A low gray scale enhancement (LGSE) function can correct this difference inside the IC. Figure 2a has no correction while 2b has been corrected.

Figure 2 Two examples of low gray scale enhancement with both showing dark white image data.
Regarding this low gray scale concern, LED current PWM pulses need very sharp turn-ON and turn-OFF times, or rise and fall times, TR and TF. If TR and TF are slow, low gray scale problems can get worse.
"First line" issues and integrated SRAM
As mentioned earlier, ES-PWM control speeds up FFR. By using ES-PWM with the time-multiplexing anode control, the first line of time-multiplexing gets darker. Figure 6a has two lines that appear to be more reddish than the others (very top and middle). All other lines look to be more white. This first line issue is caused when the green and blue lamps are not fully turned ON.
A solution to the root cause of the first line issue can be found by integrating static RAM (SRAM) bits to store gray scale PWM codes for the entire frame, thus avoiding data transfer time lag. For example, the integrates 48 k bits of SRAM on-chip for up to 32 times of multiplexing.
Design tips for display systems and driver ICs
Inrush current control
In general, an LED display system handles huge amounts of current. For example, eight pieces of 48-output LED driver ICs controls 25 mA each. The total current is 9.6A. The biggest problem with an LED display system is that this 9.6A of current keeps turning ON and OFF at very high frequency with fast TR and TF.
Many LED driver ICs come with noise reduction features such as delay between each output. Because a system handles 10 MHz order of digital signal on its PCB, noise management is an important design factor early into the project.
Thermal error flag/pre-thermal warning
As stated, an LED display system handles huge amounts of current – which translates into huge amounts of heat. This excessive heat can cause thermal shutdown and unexpectedly stop LEDs from working. It is a major issue when the entire display stops working, but viewers might think that the system is simply turned OFF. However, in most cases, only a partial module stops working and viewers can see that something is wrong (Figure 3). Because of this, many LED driver ICs do not come with a thermal shutdown function. Instead, they come with a thermal error flag (TEF) or pre-thermal warning flag (PWF) function.

Figure 3 LED display with some modules inoperative.
These flags are generated by a circuit similar to thermal shutdown detectors. Instead of stopping an IC when temperatures get hot, hot temperature condition flags are sent to an image processing controller. Upon receipt of a flag, the controller cools down the system by reducing screen brightness, showing darker images, or simply stops the system for a moment.
48-output driver
PCB layouts can be nightmarish on a typical LED display module design. We compare system concept sketches utilizing one 48-output driver (Figure 4a) and three 16-output drivers (Figure 4b). Both diagrams are a 16 x 16 RGB matrix, which equals 768 LED lamps. It is clear that a 48-output driver like the can simplify your PCB design.
(a) 
(b)
Figure 4 PCB layout comparison between 48- and 16-output drivers.

(b)

Figure 4 PCB layout comparison between 48- and 16-output drivers.
With the numerical example specification, key points in IC data transfer calculations are reviewed as a final step of the LED display system building, which is a continuation of the discussion started in Part 1. We also visited how various LED display driver features improve video output quality, plus we examined some tips for making system design easier and more efficient.
TLC59283 (ACTIVE)
16 Channel Constant Current LED Driver with Pre-Charge FET

Parametrics Compare all products in Signage & Large Display LED Driver
Features |
Analog Dimming Steps |
Data Transfer Rate (Typ) (MHz) |
Ch to Ch Accuracy (Typ) (+/- %) |
Rating |
Operating Temperature Range (C) |
Pin/Package |
LED Displays
What is an LED Display?
An LED display, or light emitting diode display, is a flat panel display that uses light emitting diodes as the video display. An LED display panel can be either a small display or part of a larger display. LED diodes are used in order to make up an LED display. LED displays are also used in billboards and store signs. An LED panel consists of several LEDs, whereas an LED display consists of several LED panels. LEDs used in order to make up LED displays offer several advantages in comparison to other light emitting sources. A light emitting diode is made up of a semiconductor chip which is surrounded by a transparent plastic case. The plastic case allows the light to pass through it. The emission of different colors including ultraviolet and infrared light depends on the semiconductor material which is used in the diode.
Types of LED Displays
There are many different kinds of LED Displays. At Electronics we stock many of the most common types categorized by display type, digit/alpha/matrix size, color, common pin value, packaging type and number of digits/alpha/matrix/bars. The parametric filters on our website can help refine your search results depending on the required specifications.
The most common types for display type are light bar, seven segment and dot matrix. We also carry many other different types of display. Digit/Alpha/Matrix Size can range from 0.03 in to 0.40 in, with the most common sizes being 0.2 in, 0.3 in and 0.4 in.
LED Displays
LED Electronics has a full selection of programmable LED displays from several LED display chip manufacturers that can be used for devices such as an LED display screen, LED display sign, LED display panel, LED backlit display, LED display lighting, outdoor LED display, LED digital display, LED display board or any other LED display chip for lighting or programming. Simply choose from the LED display technical attributes below and your search results will quickly be narrowed in order to match your specific LED display application needs.
If you have a preferred brand, we deal with several manufacturers such as Avago Technologies, Everlight, Kingbright, Lumex or Lite-On, among others. You can easily refine your LED display product search results by clicking your preferred LED display brand below from our list of manufacturers.
Applications for LED Displays:
LED displays are often found outdoors in billboards and store signs. They can also be found in destination signs on public transportation vehicles or as part of transparent glass area. LED panels can either be used for lighting or for general illumination, task lighting or stage lighting. LED displays can be found in sports stadiums, public squares, train stations, airports, highways, commercial plazas, subways, parks, shopping centers, on tall buildings and for corporate image promotion and advertising. Due to the far viewing distances in sports venues, the high brightness of LED displays can meet this special requirement and ensure that viewers get clear images.
Choosing the Right LED Display:
When you are looking for the right LED displays, with the parametric search, you can filter the results by various attributes: by Color (Green, Red, Yellow, Green/Red/Yellow,…), Common Pin Value (Anode, Cathode, Anode/Cathode,…) and Number of Digits/Alpha/Matrix/Bars (from 1 to 8) to name a few. You will be able to find the right programmable LED display chip from several manufacturers that can be used for an LED display screen, LED display lighting, outdoor LED display, LED digital display, LED display sign, LED display board, LED display panel, LED backlit display or any other LED display chip for programming or lighting.
LED Displays in Production Ready Packaging or R&D Quantities
If the quantity of LED displays that you require is less than a full reel, we offer customers many of our programmable LED display products in tube, tray or individual quantities that will help you avoid unneeded surplus.
In addition, Future Electronics offers clients a unique bonded inventory program that is designed to eliminate potential problems that could arise from an unpredictable supply of products containing raw metals and products with long or erratic lead times.
LED Displays By:
LED Displays by Primary Attributes:
By Display Type
By Number of Digits/Alpha/Matrix/Bars
By Digit/Alpha/Matrix Size
By Common Pin Value
Featured LED Display Products
Manufacturer | Part Number | Description |
---|---|---|
Avago Technologies | HDSP-U101 | HDSP Series Single Digit Seven Segment Red 0.31" Common Anode Display |
Avago Technologies | HDSP-5621 | HDSP Series Dual Digit Seven Segment Green 0.56" Common Anode Display |
Avago Technologies | HLMP-2450 | Yellow 19.05 x 3.81 mm 38 mcd 2.1 V LED Light Bar Panel Mount |
Avago Technologies | HLMP-2300-EF000 | Red 8.89 x 3.81 mm 23 mcd 2 V LED Light Bar Panel Mount |
Everlight | HLMP2855 | Green 8.89 x 8.89 mm 50/75 mcd 2.2 V Dual In Line 4 LED Light Bar |
Everlight | MV57164 | MV57164 Series 630 nm 10 Segment High Efficiency Red Bargraph Display - DIP-20 |
Everlight | MAN6940 | Dual Digit Seven Segment High Efficiency Red 0.56" Common Cathode Display |
Everlight | F416SYGWA/S530-E3 | Yellow Green Four Digit Seven Segment 0.4 inch Common Anode Display |
Kingbright | DC56-11EWA | Dual Digit Seven Segment High Efficiency Red 0.56" Common Cathode Display |
Kingbright | SC36-11GWA | Single Digit Seven Segment Green 0.36" Common Cathode Right Hand Decimal Display |
Kingbright | SC56-11GWA | Single Digit Seven Segment Green 0.56" Common Cathode Display |
Kingbright | WP1043ID | Red 3.65 x 6.15 mm 100° Tinted Diffused 10 mcd 2 V Single Chip LED Light Bar |
Kingbright | TA20-11SRWA | Single Character Dot Matrix Super Bright Red 2" Common Anode Display |
Kingbright | SA36-11SRWA | Single Digit Seven Segment Super Bright Red 0.36" Common Anode Display |
Kingbright | BA56-12GWA | Three Digit Seven Segment Green 0.56" Common Anode Display |
Lite-On | LTP-3862G | Dual Digit Green 0.3" Sixteen Segment Right Hand Alphanumeric LED Display |
Lite-On | LTS-3361JS | Single Digit Yellow 0.3" 7 Segment Common Cathode Right Hand Decimal Display |
Lite-On | LTS-3867KD-J | Single Digit Red 0.315 " Seven Segment Common Anode Right Hand Decimal Display |
Lite-On | LTS-3361JD | Single Digit Red 0.3 " Seven Segment Common Cathode Right Hand Decimal Display |
Lite-On | LTC-4727JR | Four Digit Seven Segment Super Red 0.4" Common Cathode Display |
Lumex | SSB-LX2350SIW | Four Chip Red 0.15" Through Hole Diffused Rectangular Light Bar |
Lumex | LDS-M512RI-RA | Single Digit Seven Segment Green 0.56" Common Anode Through Hole LED Display |
Lumex | LDT-N2804RI | Three Digit Seven Segment Red 0.28" Common Cathode Through Hole LED Display |
Lumex | LDS-A816RI | Single Digit Seven Segment Red 0.8" Common Anode Through Hole LED Display |
+++++++++++++++++++++++++++++++++++++++++++++++++++++++++++++++++++++++++ e- Make Pictures and Graphics on the e- MICON ![]() ![]() ++++++++++++++++++++++++++++++++++++++++++++++++++ |
Amazing. Click more for led display - https://www.lexastream.com/
BalasHapus