
Cut Out ( regulator / Auto timer ) circuit
XXX . XXX How it Works - the Cut-out
/GettyImages-169792718-56a104e53df78cafdaa7eab1.jpg)
The charging system of the Austin Seven primarily consists of a dynamo to produce an electric current and a battery in which to store the charge. In between these two is an automatic switch, known as a Cut-out. Without the cut-out, the battery would be charged whenever the dynamo is rotated sufficiently fast by the engine, but would be rapidly discharged by trying to operate the dynamo as a motor when the engine revs are not high enough – particularly when the engine is stationary. Note that the ignition switch does NOT disconnect the dynamo from the battery; it only disconnects the ignition circuit itself, (plus a few auxiliary devices such as stop lights). The ignition switch is therefore not relevant to the cut out operation or charging circuit.
There have been a number of variants during the period over which the cars were manufactured. However, they all have the same function and all have very similar operation. Each Cut-out has a set of spring loaded contacts mounted on a mechanical rocker, known as an armature, plus two electromagnets which are arranged so as to pull and push on this armature. One electromagnet is connected between the dynamo output terminal “D” and earth, (the “shunt” winding”), and the other, (the “series” winding) is connected in series with the battery usually marked “A” and the cut-out contacts. Note that, depending on cut-out type, these windings may be on separate bobbins or combined on one bobbin. Irrespective of type, the shunt winding is composed of many turns of thin wire, whilst the series winding is very few turns of substantially thicker wire.
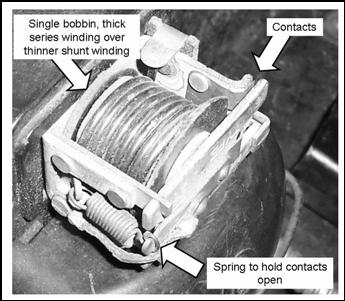
Example cut-out circuit
With the engine stationary, it is necessary for the battery to be disconnected from the dynamo, to prevent the “motor” action described above. Hence, the contacts must be open. This is the resting state of the cut-out.
As the engine is started and the revs increased, the dynamo output voltage will rise. This output voltage appears across the shunt winding, making it act as an electromagnet. As the series winding has one end connected to an open contact, it plays no part at this stage. Eventually, (at fast tickover), the dynamo voltage will reach a value that would be high enough to prevent current flowing from the battery to the dynamo, but would allow current to flow from the dynamo to the battery – the normal charging method. The shunt winding is arranged so that when the dynamo output voltage reaches this value, it produces a sufficiently strong magnetic field to pull on the armature overcoming the spring force and close the contacts. The battery is now being charged. For 6V systems, this should occur at approximately 6.5V; for 12V, this occurs at 13.5V. As soon as the contacts are closed, the shunt winding is now also connected across the battery. This gives a latching action as the battery now also supplies current for the shunt winding. In this state, the contacts would still be pulled shut until the battery voltage dropped to a low level irrespective of the dynamo output, as the electromagnet is now being operated by the battery.
Consequently, it is necessary to counteract this force so that the spring can pull the contacts apart to disconnect the battery. This is the function of the second or “series” winding.
The Series winding produces a force on the armature which is proportional to the current flowing either to or from the battery, and which changes direction with the direction of current flow. When the battery is being charged, the force acts to add to the pulling force from the shunt winding, causing the contacts to be held firmly shut. However, when the dynamo output falls so that there is a current from the battery to the dynamo, the force is now in the opposite direction and opposes that of the shunt winding. When the force from the series winding equals that of the shunt, then the armature is released for the spring to open the contacts.
If the engine is stopped at this point, the battery is safely disconnected from the dynamo. If the revs rise, the force from the shunt winding will close the contacts again.
This can be seen in operation from the behaviour of the ammeter. With all other electrical loads off, (note that the ammeter measures all current flow from the battery, not just that to the dynamo), and the engine running at a fast tickover, the ammeter will settle in the charging side of the scale. When the revs are allowed to drop, the ammeter will move to the discharge side and then suddenly fall back nearer to zero. This sudden fall back occurs when the series winding has sufficient current flowing in the discharge direction to counteract the closing force from the shunt winding and the contacts are opened. The charging warning light will operate at the same time. No current flows to the dynamo; the remaining discharge shown is actually the current required by the ignition circuit.
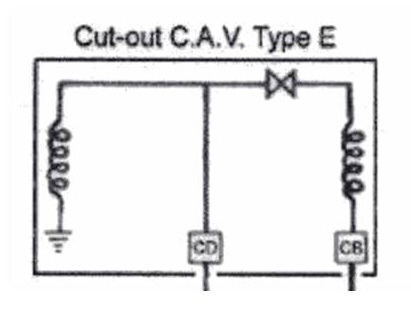

Type E 1922-1923
Type CF1 1924-1931
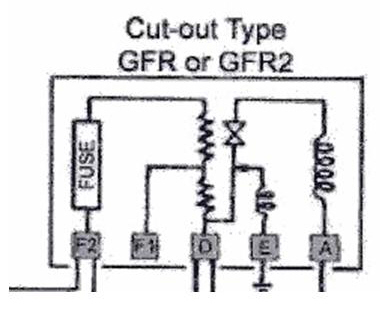

Type CF3 1931-1933
Type GFR or GFR2
1934-1937
This article, written by Geoff Hardman, originally appeared in CA7C Seven Focus in Nov 2006 pp6-8.
XXX . XXX 4 zero How Voltage Regulators Work
Voltage Regulators
As you may recall from last month's article on the function of generators in your classic car, there is no means of internally controlling the output of one. In other words, the faster it spins the more voltage goes into the car's electrical system. If this weren't controlled the generator would damage the battery and burn out the car's lights. Also, if the generator weren't cut out from the car's circuitry when not running, the battery would discharge through its case.

That's where the REGULATOR (commonly called the Voltage Regulator, but that's only one component of the system) comes in. Regulators have seen many design improvements over the decades, but the most commonly used electro-mechanical regulator is the three-control units in one box type. Let's look at how these things work...
Cutout Relay
Sometimes called the circuit breaker, this device is a magnetic "make-and-break" switch. It connects the generator to the battery (and therefore the rest of the car) circuit when the generator's voltage builds up to the desired value. It disconnects the generator when it slows down or stops.
The relay has an iron core that is magnetized to pull down a hinged armature. When the armature is pulled down a set of contact points closes and the circuit is completed. When the magnetic field is broken (like when the generator slows down or stops) a spring pulls the armature up, breaking the contact points.

An obvious failure mode is the contact points. As they open and close, a slight spark is generated, eventually eroding the material on the points until they either "weld" themselves together or become so high in resistance that they won't conduct current when closed. In the first case the battery would discharge through the generator overnight and in the second there would be no charging to the system.
Voltage Regulator
Another iron core-operated set of contact points is utilized to regulate maximum and minimum voltage at all times. This circuit also has a shunt circuit (a shunt re-directs electrical flow) going to ground through a resistor and placed just ahead (electrically) of the points. When the points are closed the field circuit takes the "easy" route to ground but when the points are open the field circuit must pass through the resistor to get to ground.
The field coil on the generator is connected to one of the voltage regulator contact points. The other point leads directly to ground.
When the generator is operating (battery low or a number of devices running) its voltage may stay below that for which the control is set. Since the flow of current will be too weak to pull the armature down the generator field will go to ground through the points. However, if the system is fully charged the generator voltage will increase until it reaches the maximum limit and current flow through the shunt coil will be high enough to pull the armature down and separate the points.
This cycle is repeated over and over in real time. The points open and close about 50 to 200 times per second, maintaining a constant voltage in the system.
Current Regulator
Even though the generator's voltage is controlled it is possible for its current to run too high. This would overheat the generator, so a current regulator is incorporated to prevent premature failure.
Similar in appearance to the voltage regulator's iron core, the current regulator's core is wound with a few turns of heavy wire and connected in series with the generator's armature.

In operation, current flow increases to the predetermined setting of the unit. At this time, current flow through the heavy wire windings will cause the core to draw the armature down, opening the current regulator points. In order to complete the circuit the field circuit must pass through a resistor. This lowers current output, points close, output increases, points open, output down, points close, and so on. The points, therefore, vibrate open and closed much as the voltage regulator's points do, many times every second.
Good and Bad News
Because they are mechanical, voltage regulators are easy to troubleshoot. If you study the function of each of the three parts and how they interrelate, it becomes obvious which part is malfunctioning, depending upon symptoms. That means anyone who understands how everything works can easily troubleshoot problems. That's the good news.
The bad news is that the point gaps and spring pressures determine the voltage/current limits and they are exceedingly hard to adjust. Sometimes it can be done on the car using a voltmeter, but generally it is best to replace the entire regulator assembly when a certain part of it fails. Factory assembly of regulators required relatively sophisticated measurement instruments. Adjusting them by "feel" is a matter of luck, and frequently can result in damage.
Overall, the good news is that regulators are inexpensive and relatively easy to find. Replacement is always a good idea.
What about Alternator Regulators?
The same type of regulator was originally incorporated into alternator-fitted cars and they work in much the same way. However, since some cars used ammeters no current regulator was needed. Therefore, a "single unit" regulator was used to turn on the alternator's stator windings. It was just a regulator without a current regulator section.
It wasn't long thereafter that the automobile companies converted to transistor voltage regulators. Utilizing Zener diodes, transistors, resistors, a capacitor and a thermistor, these regulators maintain proper voltage and current flow throughout the system. Their circuitry operates as fast as 2,000 times per second and they are tremendously reliable. On the other hand, these regulators aren't easy to repair. They are designed to be thrown away and replaced.
Many "solid state" regulators are mounted inside the alternator and are not serviceable other than the ability to set the voltage limits. That's okay, because they work very well for long periods of time. To check their operation, just measure the battery voltage while the engine is off, then when it's running. You should see something between 13 and 15 volts when running. No change in voltage means either the regulator or alternator isn't working, while higher voltage means the regulator isn't properly "regulating."
What about Converting from Generators to Alternators?
Well, that's a double-sided question. We believe such conversions should be done if additional electrical devices have been installed during restoration or major updating of the car. Air conditioning, electric cooling fans, etc. eat up lots of current that can't be easily handled by old generators. Alternators provide three times the current and weigh much less than their old counterparts.
On the other hand, converting to an alternator will affect the car's "period" appearance. It's a personal choice, of course, but one worth considering. We'll be doing an article on a conversion very soon.
XXX . XXX 4 zero null How Automotive Relays and Fuses Work
We've gone through basic theory and major components over the last several articles, so by now you should be fairly comfortable with overall circuitry. Now, we'll cover just a few more common devices and then draw a simple circuit and follow an electron through it. Ready?
Relays:
This was touched-on before but it's worth special attention. Remember that certain devices require considerable current (amps) and that, in turn, require thicker wire. High current devices require big, heavy switches to handle the current. Unfortunately, these would be ugly and expensive, so engineers use relays.
A relay consists of a small coil of wire around a central iron core. When the actuating switch energizes the coil this core moves heavy-duty contacts together, thus allowing high current to be passed to the device. That's how a small switch can control a high-current device.
You already know the starter solenoid is a high-current relay. Other devices that typically utilize relays are the horns, power antenna, air conditioning compressor, power seats, power windows, engine cooling fans, and power tops. Sometimes, headlights and accessory driving lights use them too. It's important to know this because many electrical failures occur in the relays themselves!
Automotive Fuses:
Almost everything in a car is wired through a fuse. Fuses are designed to fail when too much current is drawn through the device. This prevents heating of the wires and subsequent melting of the insulation, followed usually by fire!
Fuses are simple in design. Inside a fuse is a soft wire with a specific cross-sectional thickness. This dimension dictates how many amps can be carried before the wire melts. Too many amps and the fuse fails, saving the rest of the circuit from damage. Pretty neat, huh?
Most of any car's fuses are located in the fuse panel, but some are in-line. In-line fuses are found under the dash and in the engine compartment.
Fusible Links, another kind of fuse, are used in many cars and are almost always found in the wiring harness in the engine compartment. These are molded, single-purpose links in the wire which are designed to melt under extreme conditions (usually a crash which might crush wires together, causing a huge short circuit). Your car's schematic will show their use and location.
Let's look at a fairly typical horn circuit and see how various components are put together to form a working system:

Horn Relay Diagram
Notice that battery voltage travels through a high current wire (red) through the relay to the horn and also through a smaller wire (blue) through the ignition switch to the relay's low-current coil. The first thing you should be aware of is that the horn circuit is always "hot" or "live" when the ignition switch is turned on and all that's needed is a path to ground.
That path is completed when you push in the horn button. When the button is pushed the ground connection is made, energizing the relay's coil "A". The coil's iron core (in this particular design) pulls down arm, connecting high-current contacts "B". High current then flows from the battery to the horn (the horn is connected to ground because it's mounted to the chassis of the car). See how it works?
Actually, one thing is missing from this circuit. There has to be a fuse somewhere in the circuit! The high-current wire from the battery might go through an appropriate fuse on the fuse panel or there might be an in-line fuse near the horns (it depends upon the production engineering decisions as to the most economical placement, but your schematic drawing will show its location).
Also, your car's designers might have fused the low-current side of the relay as well. Check the schematic.
Suppose the horns don't work. Where do you start your troubleshooting? Here's a good procedure:
1. Check the fuses.
2. Check for voltage to the horns at the horn connector. Push the horn button or jump the wire to ground to actuate the relay. If you have voltage the horns should be operable, so search elsewhere for the problem.
3. Check for voltage at the horn button. While there, check to be sure the button's contacts touch each other when pushed. If everything's ok, go to the relay.
4. With someone pushing the horn button, check for voltage (on the low-current wire coming from the dash) on the relay. If there is voltage, the relay isn't working, right?
1. Check the fuses.
2. Check for voltage to the horns at the horn connector. Push the horn button or jump the wire to ground to actuate the relay. If you have voltage the horns should be operable, so search elsewhere for the problem.
3. Check for voltage at the horn button. While there, check to be sure the button's contacts touch each other when pushed. If everything's ok, go to the relay.
4. With someone pushing the horn button, check for voltage (on the low-current wire coming from the dash) on the relay. If there is voltage, the relay isn't working, right?
That's right. Now you have isolated the problem to the relay and only two things can be wrong: either the relay's coil isn't energizing (due to an internal broken wire) or the high-current contacts are being drawn together but no current is passing through (remember high-resistance connections?). If the coil is bad the relay must be replaced. If the contacts are charred, file them smooth.
Conclusion:
Automotive circuits are quite simple in design. Remember always that the factory used as little wire as possible, so look at the schematic diagram to see where multiple connections are made. Remember also that your friendly electron travels through several devices on its way to doing its work so you need to systematically trace the path.
Schematic diagrams are printed way too small in the manuals. Take your drawings to a copier that enlarges and blow them up to easily-readable size. Tape all the sheets together into one big drawing an you will find that tracing electrical paths becomes very straightforward.
With a little practice and patience you will no longer fear your car's electrical system.



XXX . XXX 4 zero null 0 Charging Systems
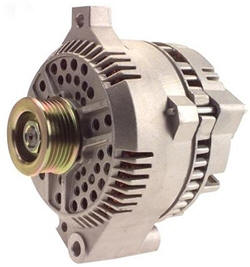
charging system or dynamo ampere
What is a Charging System?
The modern charging system hasn't changed much in over 40 years. It consists of the alternator, regulator (which is usually mounted inside the alternator) and the interconnecting wiring.
The purpose of the charging system is to maintain the charge in the vehicle's battery, and to provide the main source of electrical energy while the engine is running.
If the charging system stopped working, the battery's charge would soon be depleted, leaving the car with a "dead battery." If the battery is weak and the alternator is not working, the engine may not have enough electrical current to fire the spark plugs, so the engine will stop running.
If the battery is "dead", it does not necessarily mean that there is anything wrong with it. It is just depleted of its charge. It can be brought back to life by recharging it with a battery charger, or by running the engine so that the alternator can charge .
The main component in the charging system is the ALTERNATOR. The alternator is a generator that produces Alternating Current (AC), similar to the electrical current in your home. This current is immediately converted to Direct Current (DC) inside the alternator. This is because all modern automobiles have a 12 volt, DC electrical system.
A VOLTAGE REGULATOR regulates the charging voltage that the alternator produces, keeping it between 13.5 and 14.5 volts to protect the electrical components throughout the vehicle.
There is also a system to warn the driver if something is not right with the charging system. This could be a dash mounted voltmeter, an ammeter, or more commonly, a warning lamp. This lamp is variously labeled "Gen" Bat" and "Alt.". If this warning lamp lights up while the engine is running, it means that there is a problem in the charging system, usually an alternator that has stopped working. The most common cause is a broken alternator drive belt.
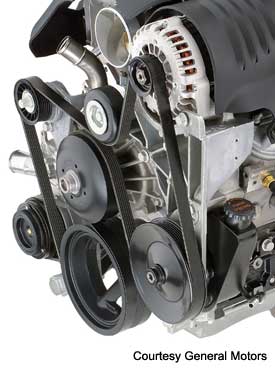
On engines with separate belts for each component, the belts will require periodic adjustments to maintain the proper belt tension. On engines that use a serpentine belt, there is usually a spring loaded belt tensioner that maintains the tension of the belt, so no periodic adjustments are required. A serpentine belt is designed to last around 30,000 miles. Check your owner's manual to see how often yours should be replaced.
Alternator output is measured in both voltage and amperage. To understand voltage and amperage, you must also know about resistance, which is measured in ohms. An easy way to picture this is to compare the movement of electricity to that of running water. Water flows through a pipe with a certain amount of pressure. The size (diameter) of the pipe dictates how much resistance there will be to the flowing water. The smaller the pipe, the more resistance. You can increase the pressure to get more water to flow through, or you can increase the size of the pipe to allow more water to flow using less pressure. Since too much pressure can burst the pipe, we should probably restrict the amount of pressure being used. You get the idea, but how is this related to the flow of electricity?
Well, voltage is the same as water pressure. Amperage is like the amount or volume of water flowing through, while resistance is the size of the wire transmitting the current. Since too much voltage will damage the electrical components such as light bulbs and computer circuits, we must limit the amount of voltage. This is the job of the voltage regulator. Too much water pressure and things could start breaking. Too much voltage and things could start burning out.
Let's get technical
Now, let's go a little deeper and see how these charging system components actually work to produce the electrical power that a modern automobile requires.
The Alternator
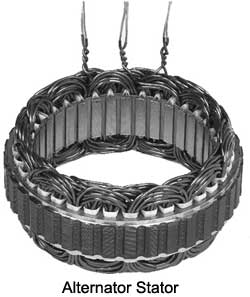
There are two main components that make up an alternator. They are the rotor and the stator. The rotor is connected directly to the alternator pulley. The drive belt spins the pulley, which in turn spins the rotor. The stator is mounted to the body of the alternator and remains stationary. There is just enough room in the center of the stator for the rotor to fit and be able to spin without making any contact.
The stator contains 3 sets of wires that have many loops each and are evenly distributed to form a three phase system. On some systems, the wires are connected to each other at one end and are connected to a rectifier assembly on the other end. On other systems, the wires are connected to each other end to end, and at each of the three connection points, there is also a connection to the rectifier. More on what a rectifier is later.
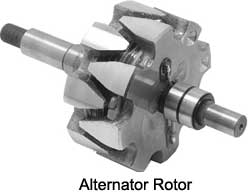
Now we know that every magnet has a north and a south pole and electro magnets are no exception. Our rotor has two interlocking sections of electro magnets that are arranged so that there are fingers of alternating north and south poles. that are evenly distributed on the outside of the rotor.
When we spin the rotor inside the stator and apply current to the rotor through a pair of brushes that make constant contact with two slip rings on the rotor shaft. This causes the rotor to become magnetized. The alternating north and south pole magnets spin past the three sets of wire loops in the stator and produce a constantly reversing voltage in the three wires. In other words, we are producing alternating current in the stator.
Now, we have to convert this alternating current to direct current current. This is done by using a series of 6 diodes that are mounted in a rectifier assembly. A diode allows current to flow only in one direction. If voltage tries to flow in the other direction, it is blocked. The six diodes are arranged so that all the voltage coming from the alternator is aligned in one direction thereby converting AC current into DC current.
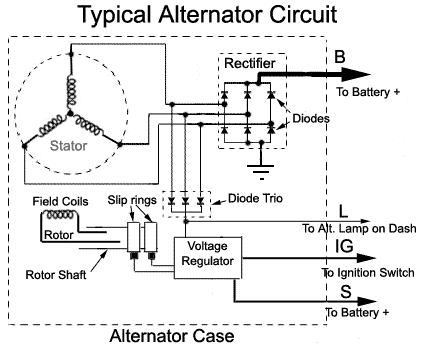
Current to generate the magnetic field in the rotor comes from the ignition switch and passes through the voltage regulator. Since the rotor is spinning, we need a way to connect this current from the regulator to the spinning rotor. This is accomplished by wires connected to two spring loaded brushes that rub against two slip rings on the rotor's shaft. The voltage regulator monitors the voltage coming out of the alternator and, when it reaches a threshold of about 14.5 volts, the regulator reduces the current in the rotor to weaken the magnetic field. When the voltage drops below this threshold, the current to the rotor is increased.
There is another circuit in the alternator to control the charging system warning lamp that is on the dash. Part of that circuit is another set of diodes mounted inside the alternator called the diode trio. The diode trio takes current coming from the three stator windings and passes a small amount through three diodes so that only the positive voltage comes through. After the diodes, the wires are joined into one wire and sent out of the alternator at the L connection. It then goes to one side of the dash warning lamp that is used to tell you when there is a problem with the charging system. The other side of the lamp is connected to the run side of the ignition switch. If both sides of the warning lamp have equal positive voltage, the lamp will not light. Remove voltage from one side and the lamp comes on to let you know there is a problem.
This system is not very efficient. There are many types of malfunctions of the charging system that it cannot detect, so just because the lamp is not lit does not mean everything is ok. A volt meter is probably the best method of determining whether the charging system is working properly
The Voltage Regulator
The voltage regulator can be mounted inside or outside of the alternator housing. If the regulator is mounted outside (common on some Ford products) there will be a wiring harness connecting it to the alternator.
The voltage regulator controls the field current applied to the spinning rotor inside the alternator. When there is no current applied to the field, there is no voltage produced from the alternator. When voltage drops below 13.5 volts, the regulator will apply current to the field and the alternator will start charging. When the voltage exceeds 14.5 volts, the regulator will stop supplying voltage to the field and the alternator will stop charging. This is how voltage output from the alternator is regulated. Amperage or current is regulated by the state of charge of the battery. When the battery is weak, the electromotive force (voltage) is not strong enough to hold back the current from the alternator trying to recharge the battery. As the battery reaches a state of full charge, the electromotive force becomes strong enough to oppose the current flow from the alternator, the amperage output from the alternator will drop to close to zero, while the voltage will remain at 13.5 to 14.5. When more electrical power is used, the electromotive force will reduce and alternator amperage will increase. It is extremely important that when alternator efficiency is checked, both voltage and amperage outputs are checked. Each alternator has a rated amperage output depending on the electrical requirements of the vehicle.
The charging system gauge or warning lamp monitors the health of the charging system so that you have a warning of a problem before you get stuck.
When a charging problem is indicated, you can still drive a short distance to find help unlike an oil pressure or coolant temperature problem which can cause serious engine damage if you continue to drive. The worst that can happen with a charging system problem is that you get stuck in a bad location.
A charging system warning lamp is a poor indicator of problems in that there are many charging problems that it will not recognize. If it does light while you are driving, it usually means the charging system is not working at all. The most common cause of this is a broken alternator belt.
There are two types of gauges used to monitor charging systems on some vehicles: a voltmeter which measures system voltage and an ammeter which measures amperage. Most modern cars that have gauges use a voltmeter because it is a much better indicator of charging system health. A mechanic's voltmeter is usually the first tool a technician uses when checking out a charging system
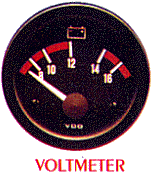
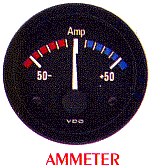
There are a number of things that can go wrong with a charging system:
- Insufficient Charging OutputIf one of the three stator windings failed, the alternator would still charge, but only at two thirds of its normal output. Since an alternator is designed to handle all the power that is needed under heavy load conditions, you may never know that there is a problem with the unit. It might only become apparent on a dark, cold rainy night when the lights, heater, windshield wipers and possible the seat heaters and rear defroster are all on at once that you may notice the lights start to dim as you slow down. If two sets of windings failed, you will probably notice it a lot sooner
It is more common for one or more of the six diodes in the rectifier to fail. If a diode burns out and opens one of the circuits, you would see the same problem as if one of the windings had failed. The alternator will run at a reduced output. However, if one of the diodes were to short out and allow current to pass in either direction, other problems will occur. A shorted diode will allow AC current to pass through to the automobile's electrical system which can cause problems with the computerized sensors and processors. This condition can cause the car to act unpredictably and cause all kinds of problems. - Too much voltageA voltage regulator is designed to limit the voltage output of an alternator to 14.5 volts or less to protect the vehicle's electrical system. If the regulator malfunctions and allows uncontrolled voltage to be released, you will see bulbs and other electrical components begin to fail. This is a dangerous and potentially costly problem. Fortunately, this type of failure is very rare. Most failures cause a reduction of voltage or amperage.
- NoiseSince the rotor is always spinning while the engine is running, there needs to be bearings to support the shaft and allow it to spin freely. If one of those bearings were to fail, you will hear a grinding noise coming from the alternator. A mechanic's stethoscope can be used to confirm which of the spinning components driven by the serpentine belt is making the noise.
The most common repair is the replacement of the alternator with a new or rebuilt one. A properly rebuilt alternator is as good as a new alternator and can cost hundreds less than purchasing a brand new one.
Labor time to replace an alternator is typically under an hour unless your alternator is in a hard to access location. Most alternators are easily accessible and visible on the top of the engine.
Replacing an alternator is usually an easy task for a backyard mechanic and rebuilt alternators are readily available for most vehicles at the local auto parts store. The most important task for the do-it-yourselfer is to be careful not to short anything out. ALWAYS DISCONNECT THE BATTERY BEFORE REPLACING AN ALTERNATOR.
Alternators can be repaired by a knowledgeable technician, but in most cases, it is not economical to do this. Also, since the rest of the alternator is not touched, a repair job is usually not guaranteed.
In some cases, if the problem is diagnosed as a bad voltage regulator, the regulator can be replaced without springing for a complete rebuild. The problem with this is that there will be an extra labor charge for disassembling the alternator in order to get to the internal regulator. That extra cost, along with the cost of the replacement regulator, will bring the total cost close to the cost of a complete (and guaranteed) rebuilt.
This is not the case when the regulator is not inside the alternator. In those cases, the usual practice is to just replace the part that is bad.
As the dynamo and battery are connected together, there has to be some means of stopping current running from the battery to the dynamo when the vehicle is switched off. This is what the cut out does.
The cut out is a coil of wire wound around a soft iron core and is therefore, an electromagnet. When the car is started current from the dynamo will flow in this coil, magnetising the soft iron core. When the current reaches a level greater than the static battery volts, the magnetism reaches sufficient strength to pull together a set of contacts that connect the dynamo to the battery. In this way the cut out ensures that current can only flow from the dynamo to the battery and not the other way around. This function is performed by diodes in the alternators of modern cars. Most cut outs are set to cut in at 14.3 dynamo volts.
When the car is switched off the dynamo stops producing current and the magnetism in the cut out coil collapses, opening the contacts and disconnecting the dynamo from the battery.
essentially an old fashioned voltage regulator .
The other type is a cut out switch used in racing to disable the alternator and get a little more horsepower.
It is usually a switch installed in the field circuit of the alternator. Switching it off stops the magnetic field and stops the alternator from producing electricity.
XXX . XXX 4 zero null 0 1 2 Cutout
While driving and using an original cutout, periodically check the Ammeter to see if the system is charging. The Ammeter can be used for a quick check for the cutout. With all electrical accessories off, the Ammeter should read to the right while driving, and zero when the engine is at low idle or turned off. | ||
The Cutout In its simplicity a cutout is a magnetically controlled switch that provides a path for current flow from the generator to the battery. The cutout permits charging of the battery when the engine is running and prevents the battery from discharging when not. | ![]() | |
The Coils Inner Coil-The inner coil is made up of multiple windings of a thin wire around an iron core. The fine-wire winding is just enough to get the points to close when the generator voltage rises above 6.2V or so. Its only purpose is to create a magnetic field to pull on the armature until the contact points close. By itself the magnetic field created by the inner coil is not strong enough to keep the points closed when subject to vibrating. Once the points close, the heavy-wire (Outer Coil) begins to conduct, creating a strong magnetic field that aids the inner coil in keeping the contacts firmly closed. Outer Coil-The outer coil is made with a heavy wire and few windings. With the points closed current from the generator travels thru the outer coil charging the battery and strengthening the magnetic field around the iron core which prevents the points from vibrating open. | ![]() | |
The Points Contact Points-The contact points of the cutout act as a switch and are held “Normally Open” by the armature spring. When the speed of the generator increases a magnetic field is created closing the points, thus, allowing current from the generator to flow and charge the battery. If the generator voltage drops below battery voltage, such that the battery begins to "charge" the generator ,instead of the other way around, the current in the heavy winding will be reversed, which means it's magnetic field will work AGAINST the fine winding, and cause the points to open. The point of "cut-in" (closure of points) is determined by the tension of the armature spring and the air gap between the iron core and contact arm. The contact points should close when the voltage of the generator has reached 6.1 to 6.3 volts. It is possible to change the "cut-in" by adjusting the air gap and/or bending the Armature Spring. (The "cut-in" charges the battery) The point of "cut-out" (opening of points) is determined by the tension of the Armature Spring. The air gap between the contact arm and the iron core has little or no effect on the "cut-out". The cutout should occur when the ammeter reads between 0 and 2 amps. It is possible to change the "cut-out" by bending the Armature Spring, set the "cut-out" as close to 0 as possible to prevent points from arcing and burning out. (The "cut-out"stops the charging of the battery and prevents the battery from draining) | ![]() | |
Testing Cutout On Car Equipment: • 3/4 Ohm Resistor • DC voltmeter
| ![]() | |
To Adjust
| ||
![]() |

XXX . XXX 4 zero null 0 1 2 3 AUTO RESET OVER/ UNDER VOLTAGE CUT- OUT
This over/under voltage cut-out will save your costly electrical and electronic appliances from the adverse effects of very high and very low mains voltages.
The circuit features auto reset and utilises easily available components. It makes use of the comparators available inside 555 timer ICs. Supply is tapped from different points of the power supply circuit for relay and control circuit operation to achieve reliability.
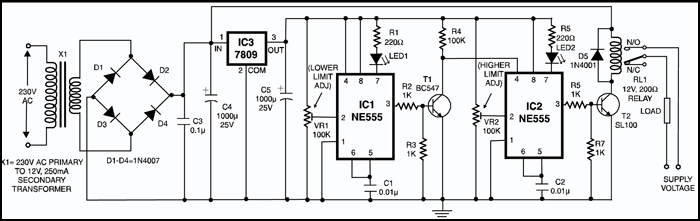
The circuit utilises comparator 2 for control while comparator 1 output (connected to reset pin R) is kept low by shorting pins 5 and 6 of 555 IC. The positive input pin of comparator 2 is at 1/3rd of Vcc voltage. Thus as long as negative input pin 2 is less positive than 1/3 Vcc, comparator 2 output is high and the internal flip-flop is set, i.e. its Q output (pin 3) is high. At the same time pin 7 is in high impedance state and LED connected to pin 7 is therefore off. The output (at pin 3) reverses (goes low) when pin 2 is taken more positive than 1/3 Vcc. At the same time pin 7 goes low (as Q output of internal flip-flop is high) and the ED connected to pin 7 is lit. Both timers (IC1 and IC2) are configured to function in the same fashion.
Preset VR1 is adjusted for under voltage (say 160 volts) cut-out by observing that LED1 just lights up when mains voltage is slightly greater than 160V AC. At this setting the output at pin 3 of IC1 is low and transistor T1 is in cut-off state. As a result RESET pin 4 of IC2 is held high since it is connected to Vcc via 100 kilo-ohm resistor R4.
Preset VR2 is adjusted for over voltage (say 270V AC) cut-out by observing that LED2 just extinguishes. when the mains voltage is slightly less than 270V AC. With RESET pin 4 of IC2 high, the output pin 3 is also high. As a result transistor T2 conducts and energises relay RL1, connecting load to power supply via its N/O contacts. This is the situation as long as mains voltage is greater than 160V AC but less than 270V AC.

When mains voltage goes beyond 270V AC, it causes output pin 3 of IC2 to go low and cut-off transistor T2 and de-energise relay RL1, in spite of RESET pin 4 still being high. When mains voltage goes below 160V AC, IC1’s pin 3 goes high and LED1 is extinguished. The high output at pin 3 results in conduction of transistor T1. As a result collector of transistor T1 as also RESET pin 4 of IC2 are pulled low. Thus output of IC2 goes low and transistor T2 does not conduct. As a result relay RL1 is de-energised, which causes load to be disconnected from the supply. When mains voltage again goes beyond 160V AC (but less than 270V AC) the relay again energises to connect the load to power supply.
XXX . XXX 4 zero null 0 1 2 3 Electronics cut out ( Auto timer electronics )
Description
The Clover Systems Dynamo Regulator is an all-electronic voltage and current regulator for DC generators used in pre-1970 motor vehicles. It can be used in vintage cars, motorcycles, trucks, tractors and boats.
Replace your old mechanical regulator with an all-electronic regulator that never requires cleaning or adjustment. Don’t waste your money on used or aftermarket mechanical replacements. This control box will be trouble free for the life of your car.
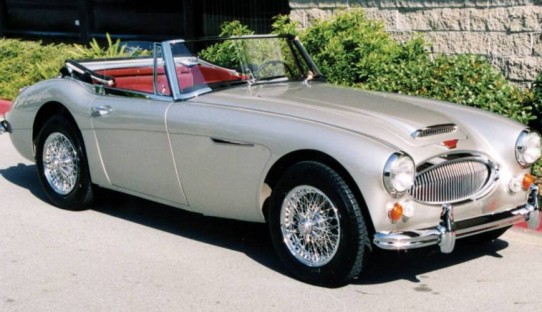
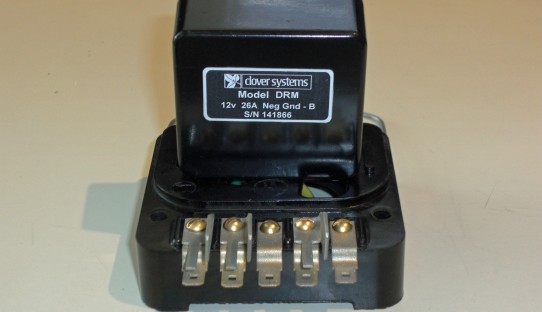
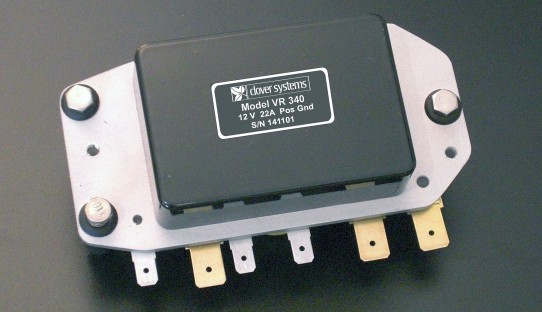
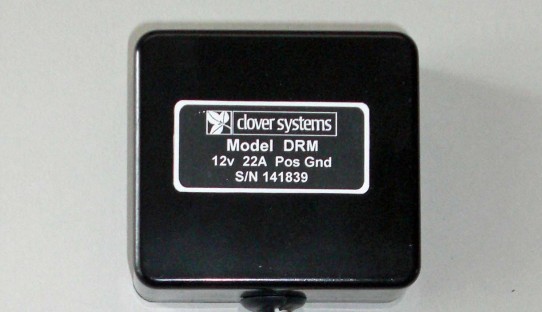