
Simple water and air pump patterns
Example MAHLE product :

Motors for electric pumps for water and other liquids

Pumps for water (or other liquids) are driven by electric motors. These can be used in wet or dry rotor environments. More controlled flow of coolant, reduction of fuel consumption and pollution (CO2), longer pump life, and quieter operation are some of the advantages found in new, modern, hybrid and electric passenger cars with electrically driven water pumps. Highly innovative rotor protection for operation in liquid is used in the motor design to ensure reliable, long-life operation.
Electronics—the key to integrated systems solutions
Electric components account for a growing range of tasks in combustion engine drives. They operate separately from the combustion engine, off-load it, and significantly increase the drive’s efficiency throughout the system.
The first step in electrification is to replace hydraulic and pneumatic actuators with electric actuators. Because they allow faster, more precise control, electric actuators improve combustion, for example, thus reducing fuel consumption and emissions.
“intelligent”: Equipped with an electric motor, engine accessories can run independently of the engine speed and pressure. They can therefore be designed purely based on specific requirements and with extreme precision. They also support stop-start functions in the combustion engine and can be powered by the energy recuperated during braking phases.
Control and power electronics
HVAC systems (heating, ventilation, and air conditioning) are responsible for heating, ventilating, and air conditioning the vehicle and provide comfortable cabin temperatures in the summer heat and winter cold. In addition to comfort, they also improve passive safety, because driver performance lasts longer with their help, and they keep the windshield free of ice and fog in the wintertime. In the field of power electronic components for HVAC systems, MAHLE provides PTC auxiliary heaters and associated control electronics for both combustion and electric vehicles. They heat up the cabin air to the desired temperature very quickly and require very little energy. Regulators from MAHLE for fan motors in the HVAC system set the fan speed very precisely to meet the requirements of the air conditioning system. They also protect the system from damage due to overheating, for example.
Just a few years ago, vehicle engine cooling was relatively simple in design and its primary task was to protect the engine block against overheating. With requirements for fuel consumption, emissions, and passenger comfort, as well as increasing electrification of the powertrain, cooling of the powertrain has transformed more and more into complex thermal management. Precise control of the cooling air flows in the cooling circuit is increasing in significance. High-performance control units from MAHLE for fan motors allow switching of cooling air flows to meet demand, enable rapid engine warm-up, reduce consumption and CO2 emissions, and prevent overheating of the cooling system.
Today’s exhaust gas aftertreatment systems are an important part of the overall engine system for further reducing pollutant emissions. In order to reach the operating temperatures necessary for cleaning diesel particulate filters even in short-range operations, MAHLE is developing control units that handle the temperature management of the system. They do this, for example, by briefly raising engine output at idle so that more hot exhaust gases reach the filter, by injecting chemical substances to promote particle burn-off, or by increasing the temperature in the exhaust gas tract by injecting fuel or with electrical heaters in the exhaust gas system. addition to electric controls, MAHLE also supplies the sensor elements needed for particulate filter management.
Glow controllers from MAHLE support the starting process in diesel engines at cold temperatures. They enable better combustion of the diesel fuel mixture, thus reducing emissions. The controllers are designed for glow plugs with a voltage of 4.4 volts, which reach their full glow temperature very quickly. The systems from MAHLE can actuate up to four glow plugs—both metal and ceramic—independently of each other. A protection system shields the individual channels and ensures robust and reliable protection against short circuits and overheating. Glow controllers from MAHLE are designed for operating voltages from 6 to 16 volts. A wider temperature range from –40°C to +90°C allows them to be positioned flexibly in the engine compartment.

Horns are legally mandated for cars and increase safety in street traffic, because the driver can warn other vehicle operators acoustically in case of danger. MAHLE supplies both electronic horns and the associated control electronics. Due to their robust construction, the service life has been increased by a factor of 20 in comparison with conventional concepts.

Sensors capture important measurement parameters in the vehicle and pass them along to the controlling devices. This makes them an important part of today’s vehicle electronics. The MAHLE product range includes temperature sensors, thick-film resistors for tank level indicators, steering angle sensors, and encoders—for example for electric window lifts.
Fuel management
Fuel management

A central aspect of fuel management is the efficient filtration of the fuel, in order to protect the engine and its components from contamination and damage. As manufacturers increasingly pursue a strategy of identical parts or modular design, the same engine is being used in more and more regions of the world. The fuel quality varies accordingly, at times due to biocomponents in the fuel. The water content plays a role along with dirt particles. Water separation systems can pave the way for the global application of an engine while making it possible to use biodiesel .
product range for fuel management includes products such as fuel filters, water separation systems, fuel heaters, and activated carbon canisters.
product range for fuel management includes products such as fuel filters, water separation systems, fuel heaters, and activated carbon canisters.
Fuel filter modules efficiently prepare gasoline and diesel fuels for the combustion process. For this purpose, they use high-separation filter media and feature an advanced functionality scope. The fuel pressure in gasoline filters can thus be adjusted by a pressure regulator integrated in the fuel filter.
For diesel engines, the functional range of the MAHLE fuel filter modules can be significantly more complex. The fuel can be cooled or heated, for example, or the water content of the fuel can be separated.
For diesel engines, the functional range of the MAHLE fuel filter modules can be significantly more complex. The fuel can be cooled or heated, for example, or the water content of the fuel can be separated.
In order to comply with demanding emissions limits, modern diesel engines typically employ common rail injection systems. These are extremely sensitive to solid particles and diesel fuel containing unsolved water. Since world engines are also used in countries with poor fuel quality and varying shares of biofuel, it is necessary to enable optimal separation of contaminants and water even under these conditions.
For this purpose, MAHLE has developed a solution with the active prefilter module that achieves a separation level of up to 98 percent in new condition.
For this purpose, MAHLE has developed a solution with the active prefilter module that achieves a separation level of up to 98 percent in new condition.
Every fuel tank has a pressure balance pipe, which ensures that no vacuum develops as the tank is emptied, and that heating and expansion of the fuel does not create overpressure in the tank. The fuel fumes that escape when the overpressure is relieved are fed through a pipe to the activated carbon canister, where they are captured or stored. The fuel fumes stored in the filter are then burned during engine operation. Activated carbon canister modules thus reliably reduce the emission of hydrocarbons and pollutants.
Electrical heaters for fuel systems
MAHLE electrical heaters are used in diesel and ethanol engines for cold starting and operation at low ambient temperatures. For diesel engines, they ensure that flowability is maintained and prevent flocculation of fuel components that could lead to clogging of the filter. In ethanol engines, MAHLE heaters significantly improve the critical cold start

Mechatronics
MAHLE develops and manufactures trendsetting starter motors, alternators, and electric motors as well as electric drive and mechatronic systems for industrial applications, agricultural and construction machinery, commercial vehicles, industrial vehicles, electric transport vehicles, and the automotive industry.
With its products and solutions, MAHLE contributes to making transportation more sustainable, fostering e-mobility and energy efficiency, and significantly reducing air pollution from vehicles. Thanks to comprehensive research and development, trends can be identified early on and turned into sustainable, application-specific customer solutions.

Mechatronic components for small engines
Flywheel and ignition coil with integrated ignition system
For electronic ignition systems, MAHLE supplies flywheels with integrated magnets and ignition coils with integrated ignition electronics. When the engine is operating, the magnets in the rotating flywheel generate an electrical current that is used in the engine to ignite the combustible mixture. The ignition coils with integrated electronics control the ignition process. MAHLE supplies systems for high-voltage capacitor discharge ignition (CDI) as well as transistor-controlled ignition (TCI). In CDI units, the discharge of a high-voltage capacitor is used—via ignition coil and spark plug—to ignite the air-fuel mixture. TCI ignition involves a steady current flowing through the ignition coils. If the contact is interrupted, the self-induction in the ignition coil gives rise to a voltage surge that generates the ignition spark in the spark plug.
MAHLE ignition systems are robust and designed for adverse conditions, making them ideal for use in hand-held power equipment or off-road motorcycles.
MAHLE ignition systems are robust and designed for adverse conditions, making them ideal for use in hand-held power equipment or off-road motorcycles.
Fuel injection systems

MAHLE fuel injection systems match the fuel quantity and timing to the specific operating/load condition so that the engine delivers the required performance, coupled with low emissions and low consumption. The MAHLE system comprises the electronic control unit, sensors, fuel pump, injectors, and throttle valve. MAHLE fuel injection systems are available in a battery-powered or battery-free concept.
ACGs (alternating current generators) and voltage regulators

MAHLE permanent-magnet alternating current generators are connected directly to the combustion engine crankshaft. They generate electricity that can be used to charge the battery, for instance, or to power electronic control units. The external circumference of the alternator is fitted with a ring gear that is probed by a sensor. As the alternator rotates, the probe relays signals to the ignition management system, which are used by the electronics to calculate the engine speed. The moment of inertia of the rotor in the alternator has a stabilizing effect on the engine speed, and the combustion engine runs more smoothly as a result. MAHLE voltage regulators convert the alternating current generated in the alternator to direct current, while at the same time ensuring a constant battery charge voltage.
MAHLE alternators thus combine several engine functions, reducing complexity and cost, as well as weight.
MAHLE alternators thus combine several engine functions, reducing complexity and cost, as well as weight.
Air conditioning for passenger cars
The level of climate comfort experienced in today’s vehicles is already at a high level and will continue to rise in the future. However, vehicle air conditioners have more to offer than just a comfortable ride. They also play a key role in terms of safety. In addition to keeping the driver comfortable and alert, the air conditioner also dehumidifies the cabin air, thus preventing windows from fogging up. We develop HVAC systems for all market segments—from subcompact cars to premium passenger cars and commercial vehicles. Our engineers work continuously to enhance HVAC system efficiency by employing optimized heat exchangers and state-of-the-art electrical components. A further key objective is to minimize weight. In combination with the battery cooling system in electrified vehicles or with the engine cooling system—e.g., through the integration of a coolant-cooled condenser in the low-temperature circuit—, ever more complex systems emerge, which we are able to master perfectly with our networked validation tool.
MAHLE power for e-mobility
MAHLE develops high-efficiency drive systems and power electronics for electric powertrains. Systems solutions cover every kind of vehicle: from e-scooters and machinery to commercial vehicles and passenger cars.
Thanks to our expertise in electric and electronic components and systems, we can offer integrated system solutions for the future of mobility.

MEET – MAHLE Efficient Electric Transport
MAHLE has developed a highly efficient 48-volt vehicle concept for urban mobility, which can be transferred to a wide range of platforms owing to its modular approach.
In the urban application area, the technical focus of MEET is on maximum energy efficiency. The meshing of different energy-saving technologies in the areas of the powertrain and thermal management increases efficiency and significantly enhances the cruising range of the vehicle—even and especially at low external temperatures.
MEET Highlights:
- Highly efficient 48-volt twin-power drive unit
- Application-specific speed range
- Balancing heat and cold
- 167 km cruising range in actual operation
- Personal comfort zones
- Surface heating
- 100% natural refrigerant
- MoodConnect
- High degree of agility
- Connectivity
- Urban mobility designed beyond the vehicle
- Platform concept

MAHLE Electronics—the key to integrated systems solutions
With the acquisition of the electronics specialist Nagares SA, MAHLE has further strengthened its competence in products for the e-mobility sector and is now in a position to offer integrated systems solutions across the broad product portfolio of electric drives, auxiliary components, and thermal management.
MAHLE develops both hardware and software in-house for complex controls tasks and also manufactures its own control units. The same applies to power electronics for hybrid systems and purely electric drives, in both the low-voltage range up to 48 volts and the high-voltage range. This makes MAHLE a single-source supplier of integrated systems solutions with compatible mechanical and electronic components.
MAHLE Electronics: product portfolio for electric vehicles
In electric and fuel cell vehicles, the optimization of the heating system is essential in order to improve cruising range, efficiency, comfort and service life of the complete system. Due to efficiency, electrically driven cars do not generate sufficient waste heat to enable rapid heating of the vehicle cabin. To keep the windows clear and ensure optimal thermal comfort, additional heating can be provided with high voltage PTC heaters. This technology can also be used for battery heating, to ensure that the high voltage battery operates within its temperature range.
Another requirement for battery-powered electric vehicles is to minimize electrical energy consumption in order to optimize the vehicle's cruising range. In this complete system, high-performance electronic components from MAHLE ensure high efficiency and thereby increase the operating range of electric vehicles.
Another requirement for battery-powered electric vehicles is to minimize electrical energy consumption in order to optimize the vehicle's cruising range. In this complete system, high-performance electronic components from MAHLE ensure high efficiency and thereby increase the operating range of electric vehicles.
Voltage converters are the link between the high-voltage (HV) drive train battery and the existing 12-volt low-voltage system. These DC-DC converters not only have to ensure high reliability in the car, they also need to score with efficiency and high power density. Based on specialized components developed in-house, MAHLE offers systems solutions that can be used both as a stand-alone unit and as a module in integrated concepts, covering a wide voltage range.
MAHLE has developed an interface module within the charging structure of electric vehicles. This specific component placed between the power mains and the charger power stage works closely with the latter and unites a configurable EMI filter, protection devices and sensors to ensure high flexibility, maximum efficiency and user safety during the charging process. The configurable EMI filter enables compatibility with single- and three-phase mains configuration.
By sensing the mains currents and voltages and reporting the values to the charger control unit it is part of the power factor correction system for high charging efficiency. A residual current detector and earth quality measurement device provide user safety to the highest degree. The communication with the ECU is ensured through BUS communication.
By sensing the mains currents and voltages and reporting the values to the charger control unit it is part of the power factor correction system for high charging efficiency. A residual current detector and earth quality measurement device provide user safety to the highest degree. The communication with the ECU is ensured through BUS communication.

Battery-management systems from MAHLE monitor and control temperatures, voltages, charge states, and charging and discharging processes for lithium-ion cells. They ensure reliable, trouble-free functionality and optimal performance of automotive traction batteries, even under peak currents. Thick-film resistors on a ceramic substrate make the system extremely robust and rugged.

MAHLE thermal management: enabler for electromobility
Applying its high-level systems expertise, MAHLE develops holistic thermal management solutions for electric vehicles, which cover interior temperature control as well as thermal management of the technical drive components.
E-mobility will be a key component of CO2-neutral individual transportation over the long term. MAHLE aims to be one of the innovation drivers in this field too. The refined management of the occurring heat flows is the foundation for the performance, cruising range, and service life of electric vehicles.
Greater range with MAHLE thermal management
In this way, MAHLE is creating the basic conditions for the acceptance of battery-powered electric mobility. For interior air conditioning in the winter, MAHLE supplies electric PTC heating elements. MAHLE concepts designed to utilize waste heat from the electric motor and power electronics ensure high energy efficiency—synonymous with extending the electric cruising range in battery-powered electric vehicles. When a MAHLE heat pump is used, the battery range can be increased significantly—by up to 20 percent at an outside temperature of 0°C.
Rapid charge capability with MAHLE battery conditioning
Another aspect of e‑mobility that is relevant to the customer is the battery’s rapid charge capability. Decreased charging time results in increased heat buildup due to higher currents. Protecting the battery from damage in such cases calls for active cooling involving all available cooling circuits, independent of outside temperatures. MAHLE already offers high-performance components that make fast charging functionality possible.

Electric heater vs. heat pump
XXX . V00 gas station payment system is directly proportional to the value of money issued commonly called retail payments
The point of sale (POS) or point of purchase (POP) is the time and place where a retail transaction is completed. At the point of sale, the merchant calculates the amount owed by the customer, indicates that amount, may prepare an invoice for the customer (which may be a cash register printout), and indicates the options for the customer to make payment. It is also the point at which a customer makes a payment to the merchant in exchange for goods or after provision of a service. After receiving payment, the merchant may issue a receipt for the transaction, which is usually printed but is increasingly being dispensed with or sent electronically.
To calculate the amount owed by a customer, the merchant may use various devices such as weighing scales, barcode scanners, and cash registers. To make a payment, payment terminals, touch screens, and other hardware and software options are available.
The point of sale is often referred to as the point of service because it is not just a point of sale but also a point of return or customer order. POS terminal software may also include features for additional functionality, such as inventory management, CRM, financials, or warehousing.
Businesses are increasingly adopting POS systems, and one of the most obvious and compelling reasons is that a POS system does away with the need for price tags. Selling prices are linked to the product code of an item when adding stock, so the cashier merely needs to scan this code to process a sale. If there is a price change, this can also be easily done through the inventory window. Other advantages include the ability to implement various types of discounts, a loyalty scheme for customers, and more efficient stock control.
Points of sale at a Target store
Retailers and marketers will often refer to the area around the checkout instead as the point of purchase (POP) when they are discussing it from the retailer's perspective. This is particularly the case when planning and designing the area as well as when considering a marketing strategy and offers.
Some point of sale vendors refer to their POS system as "retail management system" which is actually a more appropriate term given that this software is no longer just about processing sales but comes with many other capabilities such as inventory management, membership system, supplier record, bookkeeping, issuing of purchase orders, quotations and stock transfers, hide barcode label creation, sale reporting and in some cases remote outlets networking or linkage, to name some major ones.
Nevertheless, it is the term POS system rather than retail management system that is in vogue among both end-users and vendors.
Software before the 1990s

McDonald's POS device by Brobeck
Early electronic cash registers (ECR) were controlled with proprietary software and were limited in function and communication capability. In August 1973, IBM released the IBM 3650 and 3660 store systems that were, in essence, a mainframe computer used as a store controller that could control up to 128 IBM 3653/3663 point of sale registers. This system was the first commercial use of client-server technology, peer-to-peer communications, local area network (LAN) simultaneous backup, and remote initialization. By mid-1974, it was installed in Pathmark stores in New Jersey and Dillard's department stores.
One of the first microprocessor-controlled cash register systems was built by William Brobeck and Associates in 1974, for McDonald's Restaurants.[4] It used the Intel 8008, a very early microprocessor (and forerunner to the Intel 8088 processor used in the original IBM Personal Computer). Each station in the restaurant had its own device which displayed the entire order for a customer — for example, [2] Vanilla Shake, [1] Large Fries, [3] BigMac — using numeric keys and a button for every menu item. By pressing the [Grill] button, a second or third order could be worked on while the first transaction was in progress. When the customer was ready to pay, the [Total] button would calculate the bill, including sales tax for almost any jurisdiction in the United States. This made it accurate for McDonald's and very convenient for the servers and provided the restaurant owner with a check on the amount that should be in the cash drawers. Up to eight devices were connected to one of two interconnected computers so that printed reports, prices, and taxes could be handled from any desired device by putting it into Manager Mode. In addition to the error-correcting memory, accuracy was enhanced by having three copies of all important data with many numbers stored only as multiples of 3. Should one computer fail, the other could handle the entire store.
In 1986, Gene Mosher introduced the first graphical point of sale software[5] featuring a touchscreen interface under the ViewTouch[6] trademark on the 16-bit Atari 520ST color computer.[7] It featured a color touchscreen widget-driven interface that allowed configuration of widgets representing menu items without low level programming.[8] The ViewTouch point of sale software was first demonstrated in public at Fall Comdex, 1986,[9] in Las Vegas Nevada to large crowds visiting the Atari Computer booth. This was the first commercially available POS system with a widget-driven color graphic touch screen interface and was installed in several restaurants in the USA and Canada.
In 1986, IBM introduced its 468x series of POS equipment based on Digital Research's Concurrent DOS 286 and FlexOS 1.xx, a modular real-time multi-tasking multi-user operating system.
Modern software (post-1990s)
In 1992, Martin Goodwin and Bob Henry created the first point of sale software that could run on the Microsoft Windows platform named IT Retail.[10] Since then a wide range of POS applications have been developed on platforms such as Windows and Unix. The availability of local processing power, local data storage, networking, and graphical user interface made it possible to develop flexible and highly functional POS systems. Cost of such systems has also declined, as all the components can now be purchased off-the-shelf.
In 1993, IBM adopted FlexOS 2.32 as the basis of their IBM 4690 OS in their 469x series of POS terminals. This was developed up to 2014 when it was sold to Toshiba, who continued to support it up to at least 2017.
As far as computers are concerned, off-the-shelf versions are usually newer and hence more powerful than proprietary POS terminals. Custom modifications are added as needed. Other products, like touchscreen tablets and laptops, are readily available in the market. And they are also more portable than traditional POS terminals. The only advantage of the latter has is because they are typically built to withstand rough handling and spillages; a benefit for food & beverage businesses.
The key requirements that must be met by modern POS systems include high and consistent operating speed, reliability, ease of use, remote supportability, low cost, and rich functionality. Retailers can reasonably expect to acquire such systems (including hardware) for about $4000 US (as of 2009) per checkout lane.
Reliability depends not completely on the developer but at times on the compatibility between a database and an OS version. For example, the widely used MS Access database system had a compatibility issue when Windows XP machines were updated to a newer Windows OS. No solution was immediately offered by Microsoft. Some businesses were seriously disrupted in the process, and many downgraded back to Windows XP for a quick resolution. Other companies utilized community support, for a registry tweak solution has been found for this.[11]
POS systems are one of the most complex software systems available because of the features that are required by different end-users. Many POS systems are software suites that include sale, inventory, stock counting, vendor ordering, customer loyalty and reporting modules. Sometimes purchase ordering, stock transferring, quotation issuing, barcode creating, bookkeeping or even accounting capabilities are included. Furthermore, each of these modules are interlinked if they are to serve their practical purpose and maximize their usability.
For instance, the sale window is immediately updated on a new member entry through the membership window because of this interlinking. Similarly when a sale transaction is made, any purchase by a member is on record for the membership window to report providing information like payment type, goods purchased, date of purchase, points accumulated. Comprehensive analysis performed by a POS machine may need to process several qualities about a single product, like selling price, balance, average cost, quantity sold, description and department. Highly complex programming is involved (and possibly considerable computer resources) to generate such extensive analyses.
POS systems are designed not only to serve the retail, wholesale and hospitality industries as historically is the case. Nowadays POS systems are also used in goods and property leasing businesses, equipment repair shops, healthcare management, ticketing offices such as cinemas and sports facilities and many other operations where capabilities such as the following are required: processing monetary transactions, allocation and scheduling of facilities, keeping record and scheduling services rendered to customers, tracking of goods and processes (repair or manufacture), invoicing and tracking of debts and outstanding payments.
Different customers have different expectations within each trade. The reporting functionality alone is subject to so many demands, especially from those in the retail/wholesale industry. To cite special requirements, some business's goods may include perishables and hence the inventory system must be capable of prompting the admin and cashier on expiring or expired products. Some retail businesses require the system to store credit for their customers, credit which can be used subsequently to pay for goods. A few companies even expect the POS system to behave like a full-fledged inventory management system, including the ability to provide even FIFO (First In First Out) and LIFO (Last In First Out) reports of their goods for accounting and tax purposes.
In the hospitality industry, POS system capabilities can also diverge significantly. For instance, while a restaurant is typically concerned about how the sale window functions, whether it has functionality such as for creating item buttons, for various discounts, for adding a service charge, for holding of receipts, for queuing, for table service as well as for takeaways, merging and splitting of a receipt, these capabilities may yet be insufficient for a spa or slimming center which would require in addition a scheduling window with historical records of customers' attendance and their special requirements.
It may be said that a POS system can be made to serve different things to different end-users depending on their unique business processes. Quite often an off-the-shelf POS system is inadequate for customers; some customization is required and this is why a POS system can become very complex. The complexity of a mature POS system even extends to remote networking or interlinking between remote outlets and the HQ such that updating both ways is possible. Some POS systems even offer the linking of web-based orders to their sale window. Even when local networking is only required (as in the case of a high-traffic supermarket), there is the ever-present challenge for the developer to keep most if not all of their POS stations running. This puts high demand not just on software coding but also designing the whole system covering how individual stations and the network work together, and a special consideration for the performance capability and usage of databases. Due to such complexity, bugs and errors encountered in POS systems are frequent.[citation needed]
With regards to databases, POS systems are very demanding on their performance because of numerous submissions and retrievals of data - required for correct sequencing the receipt number, checking up on various discounts, membership, calculating subtotal, so forth - just to process a single sale transaction. The immediacy required of the system on the sale window such as may be observed at a checkout counter in a supermarket also cannot be compromised. This places much stress on certain enterprise databases if there are just several tens of thousands of sale records in the database. Enterprise database Ms SQL for example has been known to freeze up (including the OS) completely for many minutes under such conditions showing a "Timeout Expired" error message. Even a lighter database like Ms Access will slow to a crawl over time if the problem of database bloating is not foreseen and managed by the system automatically. Therefore, the need to do extensive testing, debugging and improvisation of solutions to preempt failure of a database before commercialization further complicates the development.
POS system accuracy is demanding, given that monetary transactions are constantly involved not only via the sale window but also at the backend through the receiving and inputting of goods into the inventory. Calculations involved are not always straightforward. There may be many discounts and deals that are unique to certain products, and the POS machine must quickly process the differences and the effect on pricing. There is much complexity in the programming of such operations, especially when no error in calculation can be allowed.
Other requirements include that the system must have functionality for membership discount and points accumulation/usage, quantity and promotional discounts, mix and match offers, cash rounding up, invoice/delivery-order issuance with outstanding amount. It should enable a user to adjust the inventory of each product based on physical count, track expiry of perishable goods, change pricing, provide audit trail when modification of inventory records is performed, be capable of multiple outlet functionality, control of stocks from HQ, doubling as an invoicing system, just to name some.
It is clear that POS system is a term that implies a wide range of capabilities depending on the end-user requirements. POS system review websites cannot be expected to cover most let alone all the features; in fact unless one is a developer himself it is unrealistic to expect the reviewer to know all the nuts and bolts of a POS system. For instance a POS system might work smoothly on a test database during review but not when the database grows significantly in size over months of usage. And this is only one among many hidden critical functionality issues of a POS system.
Hardware interface standardization (post-1980s)
Vendors and retailers are working to standardize development of computerized POS systems and simplify interconnecting POS devices. Two such initiatives are OPOS and JavaPOS, both of which conform to the UnifiedPOS standard led by The National Retail Foundation.
OPOS (OLE for POS) was the first commonly adopted standard and was created by Microsoft, NCR Corporation, Epson and Fujitsu-ICL. OPOS is a COM-based interface compatible with all COM-enabled programming languages for Microsoft Windows. OPOS was first released in 1996. JavaPOS was developed by Sun Microsystems, IBM, and NCR Corporation in 1997 and first released in 1999. JavaPOS is for Java what OPOS is for Windows, and thus largely platform independent.
There are several communication ways POS systems use to control peripherals such as:
- Logic Controls \ BemaTech
- Epson Esc/POS
- UTC Standard
- UTC Enhanced
- AEDEX
- ICD 2002
- Ultimate
- CD 5220
- DSP-800
- ADM 787/788
- HP
User interface design
The design of the sale window is the most important one for the user. This user interface is highly critical when compared to those in other software packages such as word editors or spreadsheet programs where speed of navigation is not so crucial for business performance.For businesses at prime locations where real estate comes at a premium, it can be common to see a queue of customers. The faster a sale is completed the shorter the queue and hence the more room available in a store for customers to shop around and employees to do their work. High-traffic operations like such as grocery outlets and cafes need to process sales quickly at the sales counter so the UI flow is often designed with as few popups or other interruptions to ensure the operator isn't distracted and the transaction can be processed as quickly as possible.
Although improving the ergonomics is possible, a clean, fast-paced look may come at the expense of sacrificing functions that are often wanted by end-users such as discounts, access to commission earned screens, membership and loyalty schemes can involve looking at a different function of the POS to ensure the point of sale screen contains only what a cashier needs at their disposal to serve customers.
Cloud-based (post-2000s)
The advent of cloud computing has given birth to the possibility of POS systems to be deployed as software as a service, which can be accessed directly from the Internet, using any internet browser. Using the previous advances in the communication protocols for POS's control of hardware, cloud-based POS systems are independent from platform and operating system limitations. Cloud-based POS systems are also created to be compatible with a wide range of POS hardware and sometimes tablets such as Apple's IPad. Thus cloud-based POS also helped expand POS systems to mobile devices, such as tablet computers or smartphones.[12] These devices can also act as barcode readers using a built-in camera and as payment terminals using built-in NFC technology or an external payment card reader. A number of POS companies built their software specifically to be cloud-based. Other businesses who launched pre-2000s have since adapted their software to evolving technology.Cloud-based POS systems are different from traditional POS largely because user data, including sales and inventory, are not stored locally, but in a remote server. The POS system is also not run locally, so there is no installation required.[13][14]
Depending on the POS vendor and the terms of contract, compared to traditional on-premises POS installation, the software is more likely to be continually updated by the developer with more useful features and better performance in terms of computer resources at the remote server and in terms of lesser bugs and errors.
Other advantages of a cloud-based POS are instant centralization of data (important especially to chain stores), ability to access data from anywhere there is internet connection, and lower start-up costs.[14][15]
Cloud based POS requires an internet connection. For this reason it important to use a device which has its own 3G capability in case the device's primary internet goes down. In addition to being significantly less expensive than traditional legacy point of sale systems, the real strength of a cloud based point of sale system is that there are developers all over the world creating software applications for cloud based POS. Cloud based POS systems are often described[by whom?] as future proof as new applications are constantly being conceived and built.
A number of noted emerging cloud-based POS systems came on the scene less than a decade or even half a decade back. These systems are usually designed for restaurants, small and medium-sized retail operations with fairly simple sale processes as can be culled from POS system review sites. It appears from such software reviews that enterprise-level cloud-based POS systems are currently lacking in the market. "Enterprise-level" here means that the inventory should be capable of handling a large number of records, such as required by grocery stores and supermarkets. It can also mean that the system--software and cloud server--must be capable of generating reports such as analytics of sale against inventory for both a single and multiple outlets that are interlinked for administration by the headquarters of the business operation.
POS vendors of such cloud based systems should also have a strong contingency plan for the breakdown of their remote server such as represented by failover server support. However, sometimes even a major data center can fail completely, such as in a fire.[16] On-premises installations are therefore sometimes seen alongside cloud-based implementation to preempt such incidents, especially for businesses with very high traffic. However the on-premises installations may not have the most up-to-date inventory and membership information.
For such contingency, a more innovative though highly complex approach for the developer is to have a trimmed down version of the POS system installed on the cashier computer at the outlet. On a daily basis the latest inventory and membership information from the remote server is automatically updated into the local database. Thus should the remote server fail, the cashier can switch over to the local sale window without disrupting sales. When the remote server is restored and the cashier switches over to the cloud system, the locally processed sale records are then automatically submitted to the remote system, thus maintaining the integrity of the remote database.
Although cloud-based POS systems save the end-user startup cost and technical challenges in maintaining an otherwise on-premises installation, there is a risk that should the cloud-based vendor close down it may result in more immediate termination of services for the end-user compared to the case of a traditional full on-premises POS system where it can still run without the vendor.
Another consideration is that a cloud-based POS system actually exposes business data to service providers - the hosting service company and the POS vendor which have access to both the application and database. The importance of securing critical business information such as supplier names, top selling items, customer relationship processes cannot be underestimated given that sometimes the few key success factors or trade secrets of a business are actually accessible through the POS system. This security and privacy concern is an ongoing issue in cloud computing.
Retail industry
The retail industry is one of the predominant users of POS terminals.A retail point of sale system typically includes a cash register (which in recent times comprises a computer, monitor, cash drawer, receipt printer, customer display and a barcode scanner) and the majority of retail POS systems also include a debit/credit card reader. It can also include a conveyor belt, weight scale, integrated credit card processing system, a signature capture device and a customer pin pad device. While the system may include a keyboard and mouse, more and more POS monitors use touch-screen technology for ease of use, and a computer is built into the monitor chassis for what is referred to as an all-in-one unit. All-in-one POS units liberate counter space for the retailer. The POS system software can typically handle a myriad of customer based functions such as sales, returns, exchanges, layaways, gift cards, gift registries, customer loyalty programs, promotions, discounts and much more. POS software can also allow for functions such as pre-planned promotional sales, manufacturer coupon validation, foreign currency handling and multiple payment types.
The POS unit handles the sales to the consumer but it is only one part of the entire POS system used in a retail business. "Back-office" computers typically handle other functions of the POS system such as inventory control, purchasing, receiving and transferring of products to and from other locations. Other typical functions of a POS system are: store sales information for enabling customer returns, reporting purposes, sales trends and cost/price/profit analysis. Customer information may be stored for receivables management, marketing purposes and specific buying analysis. Many retail POS systems include an accounting interface that "feeds" sales and cost of goods information to independent accounting applications.
A multiple point of sale system used by big retailers like supermarkets and department stores has a far more demanding database and software architecture than that of a single station seen in small retail outlets. A supermarket with high traffic cannot afford a systemic failure, hence each point of sale station should not only be very robust both in terms of software, database and hardware specifications but also designed in such a way as to prevent causing a systemic failure - such as may happen through the use of a single central database for operations.
At the same time updating between multiple stations and the backend administrative computer should be capable of being efficiently performed, so that on one hand either at the start of the day or at any time each station will have the latest inventory to process all items for sale, while on the other hand at the end of the day the backend administrative computer can be updated in terms of all sale records.
This gets even more complicated when there is a membership system requiring real-time two-way updating of membership points between sale stations and the backend administrative computer.
Retail operations such as hardware stores (lumber yards), electronic stores and so-called multifaceted superstores need specialized additional features compared to other stores. POS software in these cases handles special orders, purchase orders, repair orders, service and rental programs as well as typical point of sale functions.[17] Rugged hardware is required for point of sale systems used in outdoor environments. Wireless devices, battery powered devices, all-in-one units, and Internet-ready machines are typical in this industry.
Recently new applications have been introduced, enabling POS transactions to be conducted using mobile phones and tablets. According to a recent study, mobile POS (mPOS) terminals are expected to replace the contemporary payment techniques because of various features including mobility, upfront low cost investment and better user experience. Convenience of conducting remote financial transactions is expected to augment the demand from small and medium businesses for mPOS.
In the mid-2000s, the blind community in the United States engaged in structured negotiations to ensure that retail point of sale devices had tactile keypads. Without keys that can be felt, a blind person cannot independently enter her or his PIN. In the mid-2000s retailers began using "flat screen" or "signature capture" devices that eliminated tactile keypads. Blind people were forced to share their confidential PIN with store clerks in order to use their debit and other PIN-based cards. The blind community reached agreement with Walmart, Target, CVS and eight other retailers that required real keys so blind people could use the devices.
Physical configuration
Early stores typically kept merchandise behind a counter. Staff would fetch items for customers to prevent the opportunity for theft and sales would be made at the same counter. Self-service grocery stores such as Piggly Wiggly, beginning in 1916, allowed customers to fetch their own items and pass the point of sale on the way to the exit. Many stores have a number of cash registers for checkout, possibly now including self-checkout. This requires customers to guess which line will move the fastest, if they want to minimize their wait times; they are often frustrated to be wrong or be stuck behind another customer who encounters a problem or who takes a long time to check out. Some stores use a single, much longer but faster-moving line, that is served by multiple registers, which produces the same average wait time, but reduces the frustration and variance in wait time from person to person.[20] Regardless of the configuration, checkout lines usually pass by impulse buy items to grab the attention of otherwise idle customers.Hospitality industry
Hospitality point of sale systems are computerized systems incorporating registers, computers and peripheral equipment, usually on a computer network to be used in restaurants, hair salons or hotels. Like other point of sale systems, these systems keep track of sales, labor and payroll, and can generate records used in accounting and bookkeeping. They may be accessed remotely by restaurant corporate offices, troubleshooters and other authorized parties.Point of sale systems have revolutionized the restaurant industry, particularly in the fast food sector. In the most recent technologies, registers are computers, sometimes with touch screens. The registers connect to a server, often referred to as a "store controller" or a "central control unit". Printers and monitors are also found on the network. Additionally, remote servers can connect to store networks and monitor sales and other store data.
Typical restaurant POS software is able to create and print guest checks, print orders to kitchens and bars for preparation, process credit cards and other payment cards, and run reports. In addition, some systems implement wireless pagers and electronic signature-capture devices.
In the fast food industry, displays may be at the front counter, or configured for drive-through or walk-through cashiering and order taking. Front counter registers allow taking and serving orders at the same terminal, while drive-through registers allow orders to be taken at one or more drive-through windows, to be cashiered and served at another. In addition to registers, drive-through and kitchen displays are used to view orders. Once orders appear they may be deleted or recalled by the touch interface or by bump bars. Drive-through systems are often enhanced by the use of drive-through wireless (or headset) intercoms. The efficiency of such systems has decreased service times and increased efficiency of orders.
Another innovation in technology for the restaurant industry is wireless POS. Many restaurants with high volume use wireless handheld POS to collect orders which are sent to a server. The server sends required information to the kitchen in real time. Wireless systems consist of drive-through microphones and speakers (often one speaker will serve both purposes), which are wired to a "base station" or "center module." This, in turn, will broadcast to headsets. Headsets may be an all-in-one headset or one connected to a belt pack.
In hotels, POS software allows for transfer of meal charges from dining room to guest room with a button or two. It may also need to be integrated with property management software.
Newer, more sophisticated systems are getting away from the central database "file server" type system and going to what is called a "cluster database". This eliminates any crashing or system downtime that can be associated with the back office file server. This technology allows 100% of the information to not only be stored, but also pulled from the local terminal, thus eliminating the need to rely on a separate server for the system to operate.
Tablet POS systems popular for retail solutions are now available for the restaurant industry. Initially these systems were not sophisticated and many of the early systems did not support a remote printer in the kitchen. Tablet systems today are being used in all types of restaurants including table service operations. Most tablet systems upload all information to the Internet so managers and owners can view reports from anywhere with a password and Internet connection. Smartphone Internet access has made alerts and reports from the POS very accessible. Tablets have helped create the Mobile POS system, and Mobile POS applications also include payments, loyalty, online ordering, table side ordering by staff and table top ordering by customers. Regarding the payments, mobile POS can accept all kinds of payment methods from contactless cards, EMV chip-enabled cards, and mobile NFC enabled cards. Mobile POS (AKA mPOS) is growing quickly with new developers entering the market almost on a daily basis.
With the proliferation of low-priced touchscreen tablet computers, more and more restaurants have implemented self-ordering through tablet POS placed permanently on every table. Customers can browse through the menu on the tablet and place their orders which are then sent to the kitchen. Most restaurants that have iPad self-order menus include photos of the dishes so guests can easily choose what they want to order. This apparently improves service and saves manpower on the part of the restaurant. However this depends on how intelligently the system has been programmed to be.
As a case in point, some self-ordering systems not requiring staff assistance may not properly recognize a subsequent order from the same customer at a table. As a result, the customer is left waiting and wondering why his second order of food and drink is not being served.
Another example of how intelligent the system can be, is whether an order that has been placed but not yet been processed by the kitchen can be modified by the customer through the tablet POS. For such an unprocessed order the customer should be given the option to easily retrieve his order and modify it on the tablet POS. But when his order is being processed this function should then be automatically disabled.
Self-ordering systems are not always free completely from intervention by the staff and for some good reasons. For example, some restaurants require that items selected by the customers be attended to and can only be placed by the waiter who has the password required to do so. This prevents fake orders - such as may be entered by playful kids - and subsequent dispute on the items ordered. If alcoholic drinks are ordered, it also becomes necessary for the waiter to first verify the age of the customer before sending the order.
The technical specifications for implementing such self-ordering system are more demanding than a single cashier-controlled POS station. On the software and hardware side each tablet on a customer table has to be networked to the cashier POS station and the kitchen computer so that both are continually updated on orders placed. The common database that serves this network must also be capable of serving many concurrent users - cashier, customers, kitchen and perhaps even a drink bar.
It is therefore to be noted by developers that some databases like popularly used Ms Access may have the specifications that it is capable of usage by multiple concurrent users. However under the stress of a POS system, they can fail miserably resulting in constant errors and corruption of data.
POS systems are often designed for a variety of clients, and can be programmed by the end users to suit their needs. Some large clients write their own specifications for vendors to implement. In some cases, POS systems are sold and supported by third-party distributors, while in other cases they are sold and supported directly by the vendor.
The selection of a restaurant POS system is critical to the restaurant's daily operation and is a major investment that the restaurant's management and staff must live with for many years. The restaurant POS system interfaces with all phases of the restaurant operation and with everyone that is involved with the restaurant including guests, suppliers, employees, managers and owners. The selection of a restaurant POS system is a complex process that should be undertaken by the restaurant owner and not delegated to an employee. The purchase process can be summarized into three steps: Design, Compare and Negotiate. The Design step requires research to determine which restaurant POS features are needed for the restaurant operation. With this information the restaurant owner or manager can Compare various restaurant POS solutions to determine which POS systems meet their requirements. The final step is to Negotiate the price, payment terms, included training, initial warranty and ongoing support costs.
Accounting forensics
POS systems record sales for business and tax purposes. Illegal software dubbed "zappers" can be used on POS devices to falsify these records with a view to evading the payment of taxes.Security
Despite the more advanced technology of a POS system as compared to a simple cash register, the POS system is still as vulnerable to employee theft through the sale window. A dishonest cashier at a retail outlet can collude with a friend who pretends to be just another customer. During checkout the cashier can bypass scanning certain items or enter a lower quantity for some items thus profiting thereby from the "free" goods.The ability of a POS system to void a closed sale receipt for refund purpose without needing a password from an authorized superior also represents a security loophole. Even a function to issue a receipt with a negative amount which can be useful under certain circumstances, can be exploited by a cashier to easily lift money from the cash drawer.
In order to prevent such employee theft, it is crucial for a POS system to provide an admin window for the boss or administrator to generate and inspect a daily list of sale receipts, especially pertaining to the frequency of cancelled receipts before completion, refunded receipts and negative receipts. This is one effective way to alert the company to any suspicious activity - such as a high number of cancelled sales by a certain cashier - that may be going on and to take monitoring action.
To further deter employee theft the sale counter should also be equipped with a closed-circuit television camera pointed at the POS system to monitor and record all the activities.
At the backend, price and other changes like discounts to inventory items through the administration module should also be secured with passwords provided only to trusted administrators. Any changes made should also be logged and capable of being subsequently retrieved for inspection.
The sale records and inventory are highly important to the business because they provide very useful information to the company in terms of customer preferences, customer membership particulars, what are the top selling products, who are the vendors and what margins the company is getting from them, the company monthly total revenue and cost, just to name some.
It is therefore important that reports on these matters generated at the administrative backend be restricted only to trusted personnel. The database from which these reports are generated should also be secured via passwords or via encryption of data stored in the database so as to prevent them from being copied or tampered with.
Despite all such precautions and more, the POS system can never be entirely water tight in security from internal misuse if a clever but dishonest employee knows how to exploit many of its otherwise useful capabilities.
News reports on POS system hacking show that hackers are more interested in stealing credit card information than anything else. The ease and advantage offered by the ability of a POS system to integrate credit card processing thus has a downside. In 2011, hackers were able to steal credit card data from 80,000 customers because Subway's security and POS configuration standards for PCI Compliance - which governs credit card and debit card payment systems security - were "directly and blatantly disregarded" by Subway franchisees.
In June 2016, several hundred of Wendy's fast food restaurants had their POS systems hacked by an illegally installed malware.[24] The report goes on to say that "the number of franchise restaurants impacted by these cybersecurity attacks is now expected to be considerably higher than the 300 restaurants already implicated" and that the "hackers made hundreds of thousands of fraudulent purchases on credit and debit cards issued by various financial institutions after breaching Wendy's computer systems late last year".
Again this exploit by hackers could only be made possible because payment cards were processed through the POS system allowing the malware to either intercept card data during processing or steal and transmit unencrypted card data that is stored in the system database.
In April 2017, security researchers identified critical vulnerabilities in point of sale systems developed by SAP and Oracle [25] and commented, “POS systems are plagued by vulnerabilities, and incidents occurred because their security drawbacks came under the spotlight.” If successfully exploited, these vulnerabilities provide a perpetrator with access to every legitimate function of the system, such as changing prices, remotely start and stop terminals. To illustrate the attack vector, the researchers used the example of hacking POS to change the price of a MacBook to $1. [28] The security issues were reported to the vendor, and a patch was released soon after the notification.
In some countries credit and debit cards are only processed via payment terminals. Thus one may see quite a number of such terminals for different cards cluttering up a sale counter. This inconvenience is however offset by the fact that credit and debit card data is far less vulnerable to hackers, unlike when payment cards are processed through the POS system where security is contingent upon the actions taken by end-users and developers.
With the launch of mobile payment particularly Android Pay and Apple Pay both in 2015, it is expected that because of its greater convenience coupled with good security features, this would eventually eclipse other types of payment services - including the use of payment terminals. However, for mobile payment to go fully mainstream, mobile devices like smartphones that are NFC-enabled must first become universal. This would be a matter of several years from the time of this writing (2017) as more and more models of new smartphones are expected to become NFC-enabled for such a purpose. For instance iPhone 6 is fully NFC-enabled for mobile payment while iPhone 5 and older models are not. The aforesaid disastrous security risks connected with processing payment card usage through a POS system would then be greatly diminished.
XXX . V00000 How does a gas pump know to shut itself off?
so cleanse your mind of distracting thoughts. In a gas pump handle you have two valves: the main valve, which is actuated by the oversize trigger you squeeze to make the gas flow, and the check valve, which lets gas flow out but won't let anything back in again, thus reducing fire hazard. In the seat of the check valve you have a little hole. To the backside of this hole is connected a Y-shaped tube. One branch of this tube runs down the nozzle and exits at the tip while the other runs back to a diaphragm connected to a release mechanism on the main valve. When you squeeze the gas pump trigger, gas running past the hole in the check valve sucks air out of the Y-shaped tube. (This is because of the Bernoulli principle: a moving stream of fluid tends to pull things in from the sides. Take my word for it.) As long the end of the Y-shaped tube exiting at the spout is unobstructed, air is simply pulled into the tube and nothing much else happens. However, as soon as the gas in your car's fill-up pipe gets high enough to cover the end of the tube, a partial vacuum is created therein, which yanks on the diaphragm, releases the main valve, and shuts off the gas. If the gas happens to be especially foamy one day, it may actuate the release mechanism prematurely, with the result that you end up with less than a full tank of gas. Simple .
Fuel pump
A fuel pump is a frequently (but not always) essential component on a car or other internal combustion engined device. Many engines (older motorcycle engines in particular) do not require any fuel pump at all, requiring only gravity to feed fuel from the fuel tank or under high pressure to the fuel injection system. Often, carbureted engines use low pressure mechanical pumps that are mounted outside the fuel tank, whereas fuel injected engines often use electric fuel pumps that are mounted inside the fuel tank (and some fuel injected engines have two fuel pumps: one low pressure/high volume supply pump in the tank and one high pressure/low volume pump on or near the engine)
Mechanical pump

Mechanical fuel pump, fitted to cylinder head
The carburetor typically contains a float bowl into which the expelled fuel is pumped. When the fuel level in the float bowl exceeds a certain level, the inlet valve to the carburetor will close, preventing the fuel pump from pumping more fuel into the carburetor. At this point, any remaining fuel inside the pump chamber is trapped, unable to exit through the inlet port or outlet port. The diaphragm will continue to allow pressure to the diaphragm, and during the subsequent rotation, the eccentric will pull the diaphragm back to bottom dead center, where it will remain until the inlet valve to the carburetor reopens.
Because one side of the pump diaphragm contains fuel under pressure and the other side is connected to the crankcase of the engine, if the diaphragm splits (a common failure), it can leak fuel into the crankcase. The capacity of both mechanical and electric fuel pump is measured in psi (which stands for pounds per square inch). Usually this unit is general measurement for pressure, yet it has slightly different meaning, when talking about fuel pumps[2]. In this context it denotes the speed, at which the pump delivers fuel from the tank to the engine. This is one of fuel pump characteristics. The higher pressure is, the faster fuel flows.
The pump creates negative pressure to draw the fuel through the lines. However, the low pressure between the pump and the fuel tank, in combination with heat from the engine and/or hot weather, can cause the fuel to vaporize in the supply line. This results in fuel starvation as the fuel pump, designed to pump liquid, not vapor, is unable to suck more fuel to the engine, causing the engine to stall. This condition is different from vapor lock, where high engine heat on the pressured side of the pump (between the pump and the carburetor) boils the fuel in the lines, also starving the engine of enough fuel to run. Mechanical automotive fuel pumps generally do not generate much more than 10-15 psi, which is more than enough for most carburetors.
Decline of mechanical pumps
As engines moved away from carburetors and towards fuel injection, mechanical fuel pumps were replaced with electric fuel pumps, because fuel injection systems operate more efficiently at higher fuel pressures (40-60 psi) than mechanical diaphragm pumps can generate. Electric fuel pumps are generally located in the fuel tank, in order to use the fuel in the tank to cool the pump and to ensure a steady supply of fuel.Another benefit of an in-tank mounted fuel pump is that a suction pump at the engine could suck in air through a (difficult to diagnose) faulty hose connection, while a leaking connection in a pressure line will show itself immediately. A potential hazard of a tank-mounted fuel pump is that all of the fuel lines are under (high) pressure, from the tank to the engine. Any leak will be easily detected, but is also hazardous.
Electric pump
In many modern cars the fuel pump is usually electric and located inside the fuel tank. The pump creates positive pressure in the fuel lines, pushing the gasoline to the engine. The higher gasoline pressure raises the boiling point. Placing the pump in the tank puts the component least likely to handle gasoline vapor well (the pump itself) farthest from the engine, submersed in cool liquid. Another benefit to placing the pump inside the tank is that it is less likely to start a fire. Though electrical components (such as a fuel pump) can spark and ignite fuel vapors, liquid fuel will not explode (see flammability limit) and therefore submerging the pump in the tank is one of the safest places to put it. In most cars, the fuel pump delivers a constant flow of gasoline to the engine; fuel not used is returned to the tank. This further reduces the chance of the fuel boiling, since it is never kept close to the hot engine for too long.The ignition switch does not carry the power to the fuel pump; instead, it activates a relay which will handle the higher current load. It is common for the fuel pump relay to become oxidized and cease functioning; this is much more common than the actual fuel pump failing. Modern engines utilize solid-state control which allows the fuel pressure to be controlled via pulse-width modulation of the pump voltage. This increases the life of the pump, allows a smaller and lighter device to be used, and reduces electrical load.
Cars with electronic fuel injection have an electronic control unit (ECU) and this may be programmed with safety logic that will shut the electric fuel pump off, even if the engine is running. In the event of a collision this will prevent fuel leaking from any ruptured fuel line. Additionally, cars may have an inertia switch (usually located underneath the front passenger seat) that is "tripped" in the event of an impact, or a roll-over valve that will shut off the fuel pump in case the car rolls over.
Some ECUs may also be programmed to shut off the fuel pump if they detect low or zero oil pressure, for instance if the engine has suffered a terminal failure (with the subsequent risk of fire in the engine compartment).
The fuel sending unit assembly may be a combination of the electric fuel pump, the filter, the strainer, and the electronic device used to measure the amount of fuel in the tank via a float attached to a sensor which sends data to the dash-mounted fuel gauge. The fuel pump by itself is a relatively inexpensive part. But a mechanic at a garage might have a preference to install the entire unit assembly.
Centrifugal turbopumps
Most turbopumps are centrifugal - the fluid enters the pump near the axis and the rotor accelerates the fluid to high speed. The fluid then passes through a diffuser which is a progressively enlarging pipe, which permits recovery of the dynamic pressure. The diffuser turns the high kinetic energy into high pressures (hundreds of bars is not uncommon), and if the outlet backpressure is not too high, high flow rates can be achieved.Axial turbopumps
Axial turbopumps also exist. In this case the axle essentially has propellers attached to the shaft, and the fluid is forced by these parallel with the main axis of the pump. Generally, axial pumps tend to give much lower pressures than centrifugal pumps, and a few bars is not uncommon. They are, however, still useful – axial pumps are commonly used as "inducers" for centrifugal pumps, which raise the inlet pressure of the centrifugal pump enough to prevent excessive cavitation from occurring therein.Complexities of centrifugal turbopumps
Turbopumps have a reputation for being extremely hard to design to get optimal performance. Whereas a well engineered and debugged pump can manage 70–90% efficiency, figures less than half that are not uncommon. Low efficiency may be acceptable in some applications, but in rocketry this is a severe problem. Turbopumps in rockets are important and problematic enough that launch vehicles using one have been caustically described as a "turbopump with a rocket attached"–up to 55% of the total cost has been ascribed to this area.Common problems include:
- excessive flow from the high-pressure rim back to the low-pressure inlet along the gap between the casing of the pump and the rotor,
- excessive recirculation of the fluid at inlet,
- excessive vortexing of the fluid as it leaves the casing of the pump,
- damaging cavitation to impeller blade surfaces in low-pressure zones.
Driving turbopumps
Steam turbine-powered turbopumps are employed when there is a source of steam, e.g. the boilers of steam ships. Gas turbines are usually used when electricity or steam is not available and place or weight restrictions permit the use of more efficient sources of mechanical energy.One of such cases are rocket engines, which need to pump fuel and oxidizer into their combustion chamber. This is necessary for large liquid rockets, since forcing the fluids or gases to flow by simple pressurizing of the tanks is often not feasible; the high pressure needed for the required flow rates would need strong and heavy tanks.
Ramjet motors are also usually fitted with turbopumps, the turbine being driven either directly by external freestream ram air or internally by airflow diverted from combustor entry. In both cases the turbine exhaust stream is dumped overboard.
Expander cycle
Because of the necessary phase change, the expander cycle is thrust limited by the square-cube rule. As the size of a bell-shaped nozzle increases with increasing thrust, the nozzle surface area (from which heat can be extracted to expand the fuel) increases as the square of the radius. However, the volume of fuel that must be heated increases as the cube of the radius. Thus there exists a maximum engine size of approximately 300 kN of thrust beyond which there is no longer enough nozzle area to heat enough fuel to drive the turbines and hence the fuel pumps. Higher thrust levels can be achieved using a bypass expander cycle where a portion of the fuel bypasses the turbine and or thrust chamber cooling passages and goes directly to the main chamber injector. Non-toroidal aerospike engines do not suffer from the same limitations because the linear shape of the engine is not subject to the square-cube law. As the width of the engine increases, both the volume of fuel to be heated and the available thermal energy increase linearly, allowing arbitrarily wide engines to be constructed. All expander cycle engines need to use a cryogenic fuel such as hydrogen, methane, or propane that easily reach their boiling points.
Some expander cycle engines may use a gas generator of some kind to start the turbine and run the engine until the heat input from the thrust chamber and nozzle skirt increases as the chamber pressure builds up.
In an open cycle, or "bleed" expander cycle, only some of the fuel is heated to drive the turbines, which is then vented to atmosphere to increase turbine efficiency. While this increases power output, the dumped fuel leads to a decrease in propellant efficiency (lower engine specific impulse). A closed cycle expander engine sends the turbine exhaust to the combustion chamber (see image at right.)
Some examples of an expander cycle engine are the Pratt & Whitney RL10 and the Vinci engine for the future Ariane 6.
Expander bleed cycle (open cycle)
This operational cycle is a modification of the traditional expander cycle. In the bleed (or open) cycle, instead of routing heated propellant through the turbine and sending it back to be combusted, only a small portion of the propellant is heated and used to drive the turbine and is then bled off, being vented overboard without going through the combustion chamber. Bleeding off the turbine exhaust allows for a higher turbopump output by decreasing backpressure and maximizing the pressure drop through the turbine. Compared with a standard expander cycle, this leads to higher engine thrust at the cost of sacrificing some efficiency due to essentially wasting the bled propellant by not combusting it.Dual expander (closed cycle)
In a similar way that the staged combustion can be implemented separately on the oxidizer and fuel on the full flow cycle, the expander cycle can be implemented on two separate paths as the dual expander cycle. The use of hot gases of the same chemistry as the liquid for the turbine and pump side of the turbopumps eliminates the need for purges and some failures modes. Additionally, when the density of the fuel and oxidizer is significantly different, as it is in the H2/LOX case, the optimal turbopump speeds differ so much that they need a gearbox between the fuel and oxidizer pumps.The use of dual expander cycle, with separate turbines, eliminates this failure-prone piece of equipment.Dual expander cycle can be implemented by either using separated sections on the regenerative cooling system for the fuel and the oxidizer, or by using a single fluid for cooling and a heat exchanger to boil the second fluid. In the first case, for example, you could use the fuel to cool the combustion chamber, and the oxidizer to cool the nozzle. In the second case, you could use the fuel to cool the whole engine and a heat exchanger to boil the oxidizer.
Advantages
The expander cycle has a number of advantages over other designs:- Low temperature
- The advantage is that after they have turned gaseous, the fuels are usually near room temperature, and do very little or no damage to the turbine, allowing the engine to be reusable. In contrast gas-generator or staged combustion engines operate their turbines at high temperature.
- Tolerance
- During the development of the RL10 engineers were worried that insulation foam mounted on the inside of the tank might break off and damage the engine. They tested this by putting loose foam in a fuel tank and running it through the engine. The RL10 chewed it up without problems or noticeable degradation in performance. Conventional gas-generators are in practice miniature rocket engines, with all the complexity that implies. Blocking even a small part of a gas generator can lead to a hot spot, which can cause violent loss of the engine. Using the engine bell as a 'gas generator' also makes it very tolerant of fuel contamination because of the wider fuel flow channels used.
- Inherent safety
- Because a bell-type expander-cycle engine is thrust limited, it can easily be designed to withstand its maximum thrust conditions. In other engine types, a stuck fuel valve or similar problem can lead to engine thrust spiraling out of control due to unintended feedback systems. Other engine types require complex mechanical or electronic controllers to ensure this does not happen. Expander cycles are by design incapable of malfunctioning that way.
XXX . V000000 Pumps and compressors
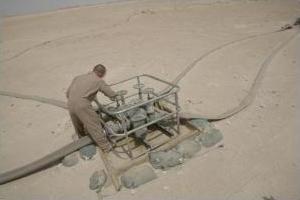
Some inventions are glamorous—microchips and fiber-optic cables spring to mind. Others are quieter and more humble, but no less important. Pumps and compressors certainly fall into that category. Try to picture life without them and you won't get very far. Take away pumps and you'll have nothing to push hot water through your home central-heating pipes, and no way to remove the heat from your refrigerator. Might as well start walking too, because you won't be able to blow up the tires on your bicycle or put gasoline in your car. From jackhammers to air conditioners, all kinds of machines use pumps and compressors to move liquids and gases from place to place. Let's take a closer look at how they work!
Photo: A fuel pump operating in the desert. The pump is drawing liquid in through the hose on the left and pushing it out through the hoses on the right. Pumps play a vital part in supplying our energy by transporting liquids such as oil and natural gas down long pipelines. Photo by Derek D. Meitzer courtesy of US Marine Corps.
How to move solids, liquids, and gases
Suppose you want to move a solid block of metal. There's little choice in how to go about it: you have to pick it up and carry it. But if you want to move liquids or gases, things are a whole lot easier. That's because they move with only a little bit of help from us. We call liquids and gases fluids because they flow down channels and pipes from one place to another. They don't, however, move without some help. It takes energy to move things and usually we have to provide that ourselves. Sometimes liquids and gases do have stored potential energy that they can use to move themselves (for example, rivers flow downhill from source to sea by using the force of gravity), but often we want to move them to places where they wouldn't normally go—and for that we need pumps and compressors. (You can read more about solids, liquids, and gases in our article on states of matter.)What's the difference between a pump and a compressor?
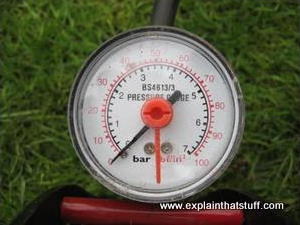
Sometimes the words "pump" and "compressor" are used interchangeably, but there is a difference:
- A pump is a machine that moves a fluid (either liquid or gas) from one place to another.
- A compressor is a machine that squeezes a gas into a smaller volume and (often) pumps it somewhere else at the same time.
Photo: Pump or compressor? If it has a pressure gauge on it and the pressure increases as you pump, technically it's also working as a compressor. With this foot pump, as you inflate your car tires, you're pumping and compressing at the same time. Even so, you wouldn't really describe this as an air compressor, because it's job is really to move air from the atmosphere into your tires. A compressor is normally designed to make use of compressed air in some way, for example, by powering a jackhammer (pneumatic air drill).
How do pumps work?
There are really just two different kinds of pumps: reciprocating pumps (which pump by moving alternately back-and-forth) and rotary pumps (which spin around).Reciprocating pumps
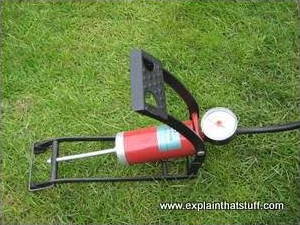
Bicycle pumps are perhaps the most familiar examples of reciprocating pumps. They have a piston that moves back and forth inside a cylinder, alternately drawing in air from outside (when you pull out the handle) and pushing it into the rubber tire (when you push the handle back in again). One or more valves ensure that the air you've drawn into the pump doesn't go straight back out again the way it came. It's worth noting, incidentally, that bicycle pumps are actually air compressors because they force air from the atmosphere into the closed space of the rubber tire, reducing its volume and increasing its pressure.
Photo: Foot pumps are familiar examples of reciprocating pumps: they move air as you push your foot up and down. With this pump, you put your foot on the black lever at the top and pump your leg up and down, making the red cylinder move back and forth. A valve inside the cylinder lets air in (when you raise your leg), which is then pumped out through the black hose on the right (when you lower your leg). A gauge on the top of the pump (on the right) shows the air pressure in the tire in Imperial units (bars and pounds per square inch or psi).
Rotary pumps
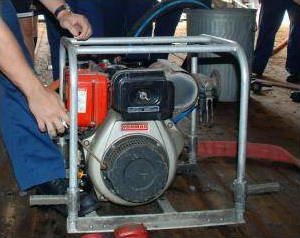
Photo: A typical rotary pump used in firefighting. The impeller is inside the silver housing under the black circular case. Photo by Melrose Afaese courtesy of US Navy.
Rotary pumps work a completely different way using a spinning wheel to move the fluid from the inlet to the outlet. Devices like this are sometimes called centrifugal pumps because they fling the fluid outward by making it spin around (a bit like the way a clothes washer gets your jeans dry by spinning them at high speed). Rotary pumps work in exactly the opposite way to turbines. Where a turbine captures energy from a liquid or gas that's moving of its own accord (for example, the wind in the air around us or the water flowing in a river), a pump uses energy (typically supplied through an electric motor) to move a fluid from place to place.
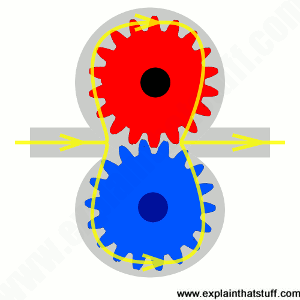
Rotary pumps all tend to look the same from the outside: there's a sealed circular or cylindrical case with an inlet on one side and an outlet on the other. Inside, however, they can work in various different ways. Vane pumps use vanes (flat blades) that slide in and out as they rotate, moving the fluid from the inlet to the outlet and flinging it out at speed. Impeller pumps use a wheel with curved blades called an impeller, which is a bit like a multi-bladed propeller fitted snugly in the middle of a closed pipe. The impeller draws the fluid through the inlet, spins it around at speed, and then forces it out through the outlet pipe, usually pointed in the opposite direction. Sometimes impellers are made of rigid metal or plastic (like the one in the photo below), though they can also have flexible, rubbery blades that change length as they rotate (in a similar way to the sliding blades of a vane pump) so they always make a tight seal. In yet another design, the vanes and impellers are replaced by two or more large screws or gears that mesh and rotate in opposite directions, pulling fluid around them as they go. Auger pumps use a single long screw that transports material as it spins around, effectively like an auger mounted inside a pipe.
Which is best, rotary or reciprocating?
A rotary pump is much faster than a reciprocating pump because the fluid is continually entering and leaving; in a reciprocating pump, it's entering half the time and leaving the other half of the time. It's also easier to power with an electric motor than a reciprocating pump, because the motor is rotating as well; it's easy to drive one rotating machine with another, and somewhat harder to use a rotating machine (a motor) to drive a reciprocating one (a pump that needs moving back and forth). Generally, rotary pumps are mechanically simpler and more reliable than reciprocating ones because they don't have moving valves that will gradually wear out.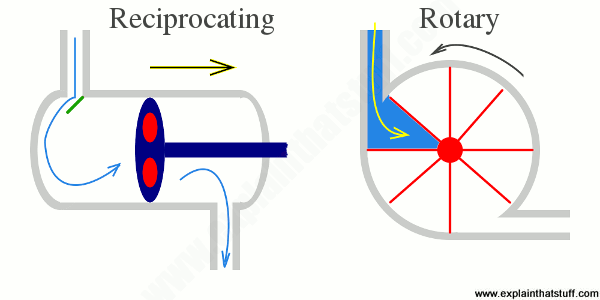
Right: A rotary pump shifts fluid from inlet to outlet like a paddle wheel. Watching what happens to a single segment, we can see that it fills with fluid one moment, before being pushed around to the outlet some time later. This is a very simplified example of what's called a vane pump: the vanes are the "blades" that turn on the wheel. You can see that half the chambers (the upper ones) are going to be empty all the time, which makes the pump less effective. For that reason, practical pumps tend to have the wheel mounted off-center, which makes a bigger, crescent-shaped chamber at the bottom, allowing more fluid to be pumped in the same time.
Using pumps and compressors
There are pumps inside virtually any machine that uses liquids, from car engines (which need to pump fuel) to dishwashers (where a pump cycles hot water round the tub) and personal water craft (powered through the water by a high-pressure jet of water pushing backward).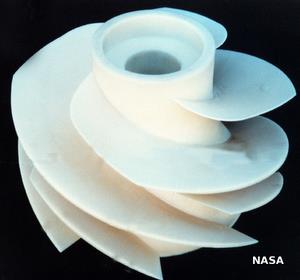
Photo: A typical pump impeller. Photo courtesy of NASA Marshall Image Gallery.
Unlike machines based around pumps, machines that use compressors don't work simply by moving a fluid: they also harness the energy that was stored inside the fluid when it was originally compressed. It takes energy to compress a gas, but that energy doesn't vanish into thin air and it isn't wasted. It's stored inside the gas and you can use it again later, whenever you like, by allowing the gas to move elsewhere (gas springs, used in office chairs and the hinges that hold open the tailgates of cars, are a good example of this).
Lots of machines (such as jackhammers) use highly pressurized air from a compressor to do useful jobs—we say they're pneumatic (a word that generally means air-powered machine). In a jackhammer, for example, the pressurized air pushes a drill bit back and forth when it's released through a long pipe. (You may have noticed that a jackhammer is attached to a big air compressor machine by a large air hose.) Compressed air is also used for cleaning things like stone blocks. Another really important use is in powering the air brakes in trains, trucks, and buses. To stop a really big vehicle quickly, you can't rely on the pressure supplied by a driver's leg, as you can in a car (where the brakes are hydraulic). Instead, truck and train brakes are powered by compressed air that's released when the driver pushes a pedal. You may have heard a sudden whooshing sound after trucks have stopped suddenly. That's compressed air being released after it pushes the brakes against the wheels to bring them to rest.
XXX . V0000000 DC Inverter air-to-water heat pumps S-THERM
DC Inverter air-to-water heat pumps S-THERM
Air-to-water heat pump takes heat from the outdoor air and transfers it to the water which is then used for heating of a house or of domestic hot water. Modern heat pump can take heat from air even in low ambient temperatures, so they can work almost all year-round.
S-THERM heat pump is designed for providing hot water for heating in the winter but it can also provide cold water for cooling in summer. If you use fan-coil units, this heat pump can be used for cooling and heating. There is no need for independent air-conditioning unit.
Why to choose our heat pump
Because our S-THERM heat pumps adopt DC inverter technology, the compressor can adapt its power to meet actual requirements. This prevents from overheating the house, mainly if outdoor temperatures are around 0°C. Inverter technology is the main advantage over heat pumps with an on/off compressor which runs at their maximum capacity all the time.
The compressor is located in the outdoor unit, so indoor unit is as quiet as possible. A water pump is the only one moving component in the indoor unit. There are two fans in the outdoor unit. Due to this, fans can run at lower speed and noise from outdoor unit is lower.
Features
- Panasonic rotary compressor with DC Inverter
- Wilo water pump
- Integrated expansion tank and safety valve
- Electronic expansion valve
- Refrigerant R410A
- Integrated 6 kW electric heater
- Outflow water temperature 55°C
Complex control system
Not only the refrigerant circuit, but also the heating system can be both controlled by control system of the heat pump. A user can activate weather compensation mode, which accommodates the outlet water temperature according to the outdoor temperature. When outdoor temperatures are higher, the heat pump will provide lower water temperature and will work with better COP.
In the summer, the control system can close valves to radiator or floor-heating and use only fan coil units for cooling. Therefore, these units can provide comfort all year-round, in winter and in summer.
Advantages of products
Indoor unit- Wall mounted - it takes less space than stationary units
- Integrated expansion tank and safety valve
- User-friendly interface
- Backlighted display
- 6 kW integrated e-heater
- Very quiet operation
- Automatic air vent valve
- Easy installation
- Optimized grille of the fan for better efficiency
- Connection valves inside the unit - nicer, undisturbed appearance of the unit
- Large surface of the evaporator for more effective heat transfer
- Insulated components to prevent from frosting
- Low noise
The device contains fluorinated greenhouse gases covered by the Kyoto Protocol. Used refrigerant R410A (50% HFC-32, 50% HFC-125), GWP 2088, environmentally friendly.

XXX . V0000000 Air source heat pumps
Air source heat pumps (ASHPs) absorb heat from the outside air. This heat can then be used to heat radiators, under floor heating systems, or warm air convectors and hot water in your home.
Different from a ground source heat pump, an air source heat pump extracts heat from the outside air in the same way that a fridge extracts heat from its inside. It can get heat from the air even when the temperature is as low as -15° C. Heat pumps have some impact on the environment as they need electricity to run, but the heat they extract from the ground, air, or water is constantly being renewed naturally.The benefits of air source heat pumps
- Lower fuel bills, especially if you are replacing conventional electric heating
- potential income through the UK government’s Renewable Heat Incentive (RHI)
- lower home carbon emissions, depending on which fuel you are replacing
- no fuel deliveries needed
- can heat your home as well as your water
- minimal maintenance required
- can be easier to install than a ground source heat pump.
View case studies and examples of homeowners who live in Scotland who have installed an air source heat pump.
How do air source heat pumps work?
Heat from the air is absorbed at low temperature into a fluid. This fluid then passes through a compressor where its temperature is increased, and transfers its higher temperature heat to the heating and hot water circuits of the house. There are two main types of air source heat pump systems.- Air-to-water
An air-to-water system distributes heat via your wet central heating system. Heat pumps work much more efficiently at a lower temperature than a standard boiler system would. This makes them more suitable for underfloor heating systems or larger radiators, which give out heat at lower temperatures over longer periods of time.
- Air-to-air
An air-to-air system produces warm air which is circulated by fans to heat your home. They are unlikely to provide you with hot water as well.
Is an air source heat pump suitable for me?
To tell if an air source heat pump is right for you, there are a few key questions to consider:- Do you have somewhere to put it? You'll need a place outside your home where a unit can be fitted to a wall or placed on the ground. It will need plenty of space around it to get a good flow of air. A sunny wall is ideal.
- Is your home well insulated? Since air source heat pumps work best when producing heat at a lower temperature than traditional boilers, it's essential that your home is well insulated and draught-proofed for the heating system to be most efficient.
- What fuel will you be replacing? The system will pay for itself much more quickly if it's replacing an electricity or coal heating system. Heat pumps may not be the best option for homes using mains gas.
- What type of heating system will you use? Air source heat pumps can perform better with under floor heating systems or warm air heating than with radiator-based systems because of the lower water temperatures required.
- Is the system intended for a new development? Combining the installation with other building work can reduce the cost of installing the system.
Costs, savings and financial support
Costs
Installing a typical system costs around £6,000 to £8,000. Running costs will vary depending on a number of factors including the size of your home, how well insulated it is and what room temperatures you are aiming to achieve.Savings
How much you can save will depend on what system you use now, as well as what you are replacing it with. Your savings will be affected by:- Your heat distribution system. If you have the opportunity, under floor heating can be more efficient than radiators because the water doesn’t need to be so hot. If under floor heating isn’t possible, use the largest radiators you can. Your installer should be able to advise on this.
- Your fuel costs. You will still have to pay fuel bills with a heat pump because it is powered by electricity, but you will save on the fuel you are replacing.
- Your old heating system. If your old heating system was inefficient, you are more likely to see lower running costs with a new heat pump.
- Water heating. If the heat pump is providing hot water then this could limit the overall efficiency. You might want to consider solar water heating to provide hot water in the summer and help keep your heat pump efficiency up.
- Using controls. Learn how to control the system so you can get the most out of it. You will probably need to set the heating to come on for longer hours, but you might be able to set the thermostat lower and still feel comfortable. Your installer should explain to you how to control the system so you can use it most effectively.
Potential annual savings of installing a standard air source heat pump in an average sized, four-bedroom detached home:
England, Scotland and Wales
Existing system | Fuel bill saving(per year) | Annual RHI payments(installations between20 September to 31 December 2017) | Carbon savings(per year) |
---|---|---|---|
Old (G-rated) gas boiler New (A-rated) gas boiler |
£455 - £485
An increase of £10 - £15
|
£1,140 - £1,235
|
3,000 - 3,300 kg
900 kg
|
Old electric storage heaters New electric storage heaters |
£735 - £820
£410 - £445
|
5,500 - 6,100 kg
3,800 - 4,100 kg
| |
Old (G-rated) oil boiler New (A-rated) oil boiler |
£290 - £315
An increase of £155 - £165
|
4,900 - 5,400 kg
1,900 - 2,100 kg
| |
Old (G-rated) LPG boiler New (A-rated) LPG boiler |
£1,000 - £1,090
£290 - £315
|
3,900 - 4,200 kg
1,400 - 1,500 kg
| |
Coal | £415 - £465 | 6,700 - 7,300 kg |
See the domestic Renewable Heat Incentive page for the latest information and proposed changes to the RHI scheme.
Northern Ireland
Existing system | Fuel bill saving(per year) | Carbon savings(per year) |
---|---|---|
Old (G-rated) gas boiler New (A-rated) gas boiler |
£315 - £345
An increase of £135 - £145
|
3,000 - 3,300 kg
900 kg
|
Old electric storage heaters New electric storage heaters |
£575 - £650
£270 - £295
|
5,500 - 6,100 kg
3,800 - 4,100 kg
|
Old (G-rated) oil boiler New (A-rated) oil boiler |
£170 - £185
An increase of £230 - £250
|
4,900 - 5,400 kg
1,900 - 2,100 kg
|
Old (G-rated) LPG boiler New (A-rated) LPG boiler |
£1,280 - £1,390
£455 - £490
|
3,900 - 4,200 kg
1,400 - 1,500 kg
|
Coal |
£245 - £275
|
6,700 - 7,300 kg
|
Find out more about how we made these calculations.
Note: The Renewable Heat Incentive is no longer available in Northern Ireland.
Financial support
You may be eligible to receive payments for the heat you generate using a heat pump through the UK Government’s Renewable Heat Incentive (RHI).Domestic RHI is no longer available in Northern Ireland - details of the previous scheme can be viewed at NI Direct.
Maintenance
Heat pump systems typically come with a warranty of two to three years. Workmanship warranties for heat pumps can last for up to 10 years, for example through QANW (Quality Assured National Warranties). Many manufacturers also offer options for warranty extensions for a fee. You can expect them to operate for 20 years or more, however they do require regular scheduled maintenance. A yearly check by you and a more detailed check by a professional installer every three to five years should be sufficient.The installer should leave written details of any maintenance checks you should undertake to ensure everything is working properly. Consult with your supplier for exact maintenance requirements before you commit to installing a heat pump. You are likely to be advised to carry out a yearly check that the air inlet grill and evaporator are free of leaves or other debris. Any plants that have started to grow near the heat pump unit will also need to be removed.
You may also be advised by your installer to check the central heating pressure gauge in your house from time to time. If so, you should be shown how to do this. To prevent the heat pump from freezing in cold winter weather anti-freeze is used. Levels of anti-freeze and its concentration is one of the things that a professional installer will check when he comes to service your heat pump. If your heat pump has external refrigeration pipes, (very unusual for a domestic system) these will need to be serviced annually by a refrigeration engineer.
Planning permission
Before starting, the developer must apply to the relevant planning authority for a determination as to whether the prior approval of the authority will be required for the siting and external appearance of the air source heat pump. The application needs to be accompanied by a range of other information and several other conditions apply.

= MA THEREFORE AIR AND WATER PUMPS USE ELECTRONIC AND ELECTRIC MATIC =