In the processing of gold and copper seeds which are usually obtained from mining materials in the form of rock rocks in the processing are bound in one compound and we can separate the metal compounds in atomic atoms using mercury which will be separated between gold and copper which are both metals This noble is commonly used for high quality electronic component components both in terms of sound as well as image and control; let's discuss the process made : Many space and telecommunication industry use Gold and recent trend is to use gold in mobile phone , computers and etc to make performance better .
Gold conducts electricity, does not tarnish, is very easy to work, can be drawn into wire. Industrial use of gold is in the manufacture of electronics. Gold is the highly efficient conductor that can carry these tiny currents and remain free of corrosion. Electronic components made with gold are highly reliable. Gold is used in connectors, switch and relay contacts, soldered joints, connecting wires and connection strips.
A small amount of gold is used in almost every sophisticated electronic device. This includes cell phones, calculators, personal digital assistants, global positioning system (GPS) units, and other small electronic devices. Most large electronic appliances such as television sets also contain gold.
Gold is used in many places in the standard desktop or laptop computer. The rapid and accurate transmission of digital information through the computer and from one component to another requires an efficient and reliable conductor. Gold meets these requirements better than any other metal.
THE USE OF GOLD PLATING IN ELECTRONIC
Most of the electronics we use in our daily lives contain at least a little bit of gold. While this precious metal is widely known for its beautiful, shiny appearance, it also has quite a few functional purposes that make it a sought-after material in a variety of industries.
The electronics sector, though, is the main consumer of gold today. Even though that gold is rarely seen, it plays a critical role in keeping the components of your devices functioning properly over time. Electronic parts aren’t typically made entirely of gold because of the material’s cost. More often, manufacturers use electroplating to apply a thin layer of gold over the main material that comprises the component.
Frequently used in combination with nickel plating, the thin layer of gold protects the component from corrosion, heat, wear and helps ensure a reliable electrical connection. At Sharretts Plating Company, 99% of our gold plating work serves the electronics industry. Over the last eight decades, we’ve perfected our gold plating, also called Au plating, processes and offer both electroplating and immersion plating.
In the rest of this article, we’ll look in more detail at the processes, benefits and uses of gold plating for electronics and electrical components.
WHAT IS GOLD PLATING?
At SPC, we’ve developed and applied many gold plating processes. We use electro-deposition, which is commonly known as electroplating and uses an electric current to apply the coating. We also use immersion plating, which doesn’t use electricity.
To plate an item with electro-deposition, we connect the gold to the anode, the positively charged electrode, of an electrical circuit. We also connect the substrate, the material that we’ll be plating, to the cathode, which is the negatively charged electrode. We then immerse both pieces in an electrolytic solution.
Then, we apply a DC current to the anode. This oxidizes the metal atoms in the gold and dissolves them into the solution. The dissolved ions are reduced at the cathode, and they then deposit onto the substrate.
TYPES OF GOLD PLATING BATHS
There are three basic types of gold plating baths:
- Alkaline: An alkaline bath is a non-cyanide solution that uses sodium gold sulfite as the source of the gold ions. It has a pH level ranging from 9.0 to 13.0. Alkaline solutions produce a hard and bright deposit and reduce the co-deposition of base metals. Adding complexing agents can improve conductivity.
- Acid: Acid baths, which have a low pH of 3.0 to 6.0, produce exceptionally pure gold deposits. In fact, these deposits can be up to 99.999% pure. Acid gold baths allow for the formation of alloys with base metals, but you can also prevent this with complexing agents.
- Neutral: Neutral baths, which have a pH between 6.0 and 8.0, are typically used for plastic or ceramic substrates because they don’t contain free cyanide, which can damage these more delicate materials.
REEL-TO-REEL GOLD ELECTROPLATING
We most frequently use reel-to-reel electroplating, also known as continuous electroplating, when applying gold to a material. We use this method to plate reels of raw material before they get shaped into electronic components. It can coat strips of manufactured parts.
We load the reels onto our equipment and feed it through our electroplating processes before re-reeling it. Reel-to-reel plating can cover an entire substrate or be used more precisely to plate specific parts.
GOLD RACK ELECTROPLATING
At SPC, we also build our own racking equipment, which allows us to meet the precise requirements of our clients’ projects. Rack plating is ideal for fragile components or larger, more complex projects. However, it can be difficult to create a uniform deposit, and discoloration may appear where the item attaches to the rack.
The process involves hanging the substrate on a rack that uses hooks to apply the electrical current and hold the items in place. Once everything is properly attached, we lower the rack into the electrolytic bath, depositing the plating material.
GOLD BARREL ELECTROPLATING
Barrel electroplating is useful for quickly and economically applying a uniform coating to a substrate. This method is less precise than other methods, and works best when the entire surface of an item needs to be plated. It’s also not ideal for large or fragile components, as the piece may be too large for the barrel or become damaged during the plating process.
In this method, we place the component to be plated in a barrel that contains the plating bath, as well as bars that provide the electrical contact. Machinery rotates the substrate in the barrel while electrical current is applied, resulting in a complete and uniform deposit.
GOLD IMMERSION PLATING
For some applications, we use immersion plating, which doesn’t involve an electrical current. We dip the substrate into an electrolyte solution with gold ions, which causes the dissolution of ions from the substrate material. This releases electrons, allowing the gold ions to deposit onto the substrate. The gold ions replace the ions of the less noble metal, which typically results in a thin coating that has similar properties to electroplated gold.
PROPERTIES OF GOLD PLATING
While gold’s aesthetic appeal does contribute to its value, in the electronics industry, its functionality is what makes it such a prized material. Gold has several physical properties that lend themselves perfectly to use in electronic components. Manufacturers typically apply gold plating to connection points within electronic devices because it improves conductivity and protects the component, which helps that reliable connection last longer.
These properties include:
- Corrosion Resistance: One of gold plating’s most valuable attributes is its ability to resistant the corrosion that affects so many other metals. Gold is among the least reactive of all metals and won’t react with oxygen and rust like other metals do. Gold may tarnish slightly, but this isn’t damaging and can be removed by polishing. Resistance to corrosion is critical for electrical components because oxidation may cause a less reliable electrical connection. Its non-corrosive capabilities enable it to retain the smooth surface that’s needed for a strong connection.
- Expanded Connection Area: Gold is also highly ductile and malleable. This means it can stretch out into thin wire and will deform when placed under pressure, allowing it to spread out and cover more surface area. This creates a larger connection area, which leads to more reliable connectivity. Even with repeated use, gold’s flexibility helps electronic devices to continue to function correctly.
- Protection From Heat: Au plating is suitable for applications that involve high temperatures and will protect other materials from damage caused by heat. Gold has a melting point of 1943 degrees Fahrenheit, or 1062 degrees Celsius. It conducts heat well, in addition to electricity, and will continue to function appropriately even under intense temperatures. This makes it a useful for electronics that may become hot when used. For applications likely to involve frequent and intense heat, making the plating layer thicker will increase its resistance to heat.
- Reflectivity: Gold’s reflective properties make it ideal for use in components such as semiconductor parts, including reflector rings and reflector arrays. Gold reflects higher amounts of UV radiation below 0.35 µm than other metals do. It also reflects infrared radiation with wavelengths above 0.7 µm, which helps keep electronics cool. These reflective properties have made gold plating an integral part of spacecraft and satellite design.
- Resistance to Wear: Applying a gold plating to a piece of equipment can help it last longer, as the coating will protect the component itself from wearing away. Gold isn’t susceptible to fretting degradation, which wears away material due to repeated low amplitude relative motion. This can lead to corrosion, and then resistance. Because gold doesn’t corrode, it won’t become damaged due to fretting, protecting the layer beneath it. Gold is resistant to wear, so your plating will last a substantial amount of time. Like anything, it will eventually wear off naturally, buy when it does, you can easily re-plate the piece of equipment.
USE CASES FOR GOLD PLATING IN ELECTRONICS
You can find gold in all sorts of electronics including smartphones, laptops and desktop computers. One ton of smartphones, or about 10,000 phones, contains approximately 10 troy ounces of gold, which is equal to around three fifths of a pound. From 200 laptops, you could get about five troy ounces of gold, which is worth roughly $8000.
Gold’s ability to improve and sustain electrical connectivity makes it ideal for all types of applications in electronics. Manufacturers can apply it to any place that must facilitate an electrical connection to improve its reliability. You can find Au plating on the outside of devices, such as on electrical connectors. Most of the gold in electronics, however, is located inside the devices in the circuit boards.
Electronics companies use gold plating to enhance the conductivity of the circuit board and protect it from corrosion. Keeping a reliable connection within the circuit board is crucial to the reliable operation of any device.
Semiconductor components, such as top chucks, reflector rings and reflector arrays, are another area where gold plating is especially useful. Semiconductors, such as transistors, chips and other control parts, are partially conductive and may use plating to make a device more electrically efficiently. It also helps to protect these vital components from outside elements.
Because semiconductor chips are so small and fragile, the electroplating used for them varies slightly from the standard procedures. The chip must be handled carefully to avoid breaking any of the tiny wires inside, which would cause a faulty component. Even dust particles getting into the chip can result in a malfunction.
Because of this, the room where semiconductor plating takes place must have 0.01% of the amount of dust normally in outside air. The electrolytic bath must also be thoroughly filtered to remove any dust or other small particles.
In fact, in all electronics plating procedures, it’s necessary to prepare the substrate surface adequately to prevent the deposition of ionic and nonionic residue. These residues can reduce conductivity and even prevent the metal coating from adhering properly. Although the process of removing these residues required using hazardous organic solvents in the past, today we use eco-friendly, high-pressure water systems to prepare the surfaces of electronics for electroplating.
THE BENEFITS OF UNDERLAYERS FOR GOLD PLATING
As useful as gold is, it’s even more useful when combined with other metals. A layer of nickel is often placed on a substrate directly under the gold plating layer. This underlayer provides several benefits:
- It acts as an extra layer of protection against corrosion that may creep in through pores located in thin areas of the gold plating. It also helps prevent existing corrosion from spreading.
- It prevents other metals, such as zinc and copper, from diffusing into the gold where they may oxidize.
- It adds to the thickness of the plating. Because gold is relatively expensive, adding a thicker underlayer can reduce costs while still allowing access to the benefits of gold. This extra thickness also increases the plating’s overall durability.
Another common way to increase durability is to add a small amount of cobalt or nickel directly to the gold. This substance is referred to as hard gold — it’s relatively common and highly durable. Pure gold is often called soft gold.
Gold plating doesn’t need to be thick to be effective. In most cases, the gold should be as thin as possible without comprising any of its useful properties. For most connector manufacturing uses, a 0.8 micron layer of gold over a 1.3 micron layer of nickel should provide enough durability. Based on the application, however, you may need to vary the thickness of the plating.
The needs of your project will also determine whether you should choose hard gold or soft gold. For applications where durability is the most important aspect, hard gold is the best option. If you want a malleable coating, or if durability isn’t a priority, soft gold may be the right choice.
CHOOSING GOLD FOR ELECTRICAL COMPONENT PLATING
When it comes to metal plating for electronics, gold is an ideal choice. It offers the resistance to corrosion, wear and heat, as well as the enhanced conductivity vital to properly functioning electronic equipment.
Gold is used in electronics mainly in the form of
electroplating chemicals, gold bonding wire and sputter
targets. Smaller quantities are used in hybrid inks and solders.
The largest use of gold in electronics is as an electroplated
coating on connectors and contacts. This is followed by gold
bonding wires within semiconductor packages. Other uses
include hybrid circuits, solderable coatings for printed circuit
boards and components, as gold-based solders and for metal
layers on semiconductors as conductor tracks and contact pads.
Connectors and Contacts
Gold is used on connectors and contacts because it has
excellent corrosion resistance, high electrical conductivity
(only copper and silver are better) and, alloyed with small
amounts of nickel or cobalt, has good wear resistance. For
low voltage, low current and low contact force applications,
gold is the best material.
The resistivity of metals for electrical contacts is
important, but the contact resistance which depends on
other factors may be more significant. Some examples are
given in Table 1. The contact resistance figures are taken
from reference 2. These figures are very dependent on the
test conditions, in particular the contact pressure and so
contact resistance data from other sources may not be
comparable.
Table 1 Resistivity and Contact Resistance of Some Contact Materials
Contact Material Resistivity Contact Resistance
cm (2) m
Pure gold 2.4 x 10-8 0.8
Cobalt hardened gold 2.4 x 10-8 2.6 - 2.8
Palladium on nickel 1.08 x 10-7 3.1 - 5.8
Silver 1.6 x 10-8 Not determined
Resistance to oxidation and corrosion is important for
connector and contact materials. A useful guide to the
susceptibility of metals in these respects is their standard
electrode potential although this is not a reliable guide for
susceptibility to tarnishing in sulphide atmospheres where
silver is particularly liable to attack. The values for a selection
of metals are given in Table 2 (3). A large positive value
indicates good resistance to corrosion and a large negative
value, indicates a high reactivity but the situation is not as
simple as this as some metals including aluminium and nickel
form very thin, highly protective oxides which prevent further
attack once they are formed. However these oxides are
usually insulators.
A wide range of materials can be used for connectors and
contacts and the most appropriate choice will depend on
many criteria which include: current, voltage, contact force,
wear, fretting (due to vibration and thermal cycling),
environmental conditions (temperature, corrosive gases, etc.)
and of course cost (4). The number of times that a connector
or contact makes and breaks is also important as it will affect
wear. Often a compromise between performance and cost is
made. The most commonly used materials for low current
and voltage are listed in Table 3 and are compared with gold.
The total area actually making contact in a closed
connector or a pair of contacts is usually very small in
comparison with the apparent dimensions as contact is
made at only a few very small locations. This increases the
resistance across the contacts and so the passage of current
will generate heat. Increased contact pressure increases the
area making contact and so lowers resistance. The voltage
and contact pressure both affect localised heating which in
turn can lead to surface oxidation (but not of gold) or
melting of the surface. Arcing can also occur. All of these will
affect the life of the contact (6).
Oxidation or corrosion will affect less noble alloying
elements added to gold but these are used to modify its
properties such as the hardness or the rate of dissolution in liquid solders. Where a thin gold coating is deposited onto
another metal, this will diffuse into the gold and eventually
reach the outer surface where it can corrode or oxidise. The
time this takes depends on the thickness of the gold layer,
the temperature and the nature of the substrate metal. Silver
and copper will diffuse faster than nickel and so gold is
usually electroplated onto nickel (7). For hostile
environments, the gold thickness will need to be increased.
Electrical connectors are used to connect a wide range of
equipment such as in computers, mobile phones and cars.
Computers have plug-in printed circuit boards with gold
plated ‘finger’ connectors and the various parts of the
computer, monitor, printer, etc are connected by plug-in
sockets which usually have gold plated pins and sockets.
Some examples are shown in Figure 1.
Cars have an increasing number of electrical components
which need reliable electrical connections. These include the
air bag accelerometers, engine management systems and a
variety of pressure and other sensors. Car manufacturers
need high reliability and the environment within a car,
especially close to the engine, is hostile with a high
temperature and so frequently gold is the only suitable
material for these conditions. Most other metals would
oxidise or corrode. Most connectors are used for very small
currents at low voltage and so an increase in contact
resistance as a result of oxidation, corrosion or fretting will
affect the function of the components.
Table 2 Standard Electrode Potentials of Metals
Metal Standard Electrode Potential (volts) Comments
Gold Au+ → Au: + 1.68 Very inert and resistant to oxidation and corrosion
Palladium Pd2+ → Pd: +0. 83 Resistance to corrosion and oxidation less than for gold
Silver Ag+ → Ag: + 0.80 Good resistance to oxidation and corrosion but susceptible to
sulphide and chloride attack.
Copper Cu2+ → Cu : + 0.34 Readily oxidises in air and corrodes where moisture is present
Tin Sn2+ → Sn : - 0.136 Forms a thin inert and protective oxide but is easily
damaged because tin is relatively soft
Nickel Ni2+ → Ni : - 0.23 Readily forms a thin but inert and highly protective oxide.
This prevents further oxidation but is a good electrical
insulator
Aluminium Al3+ → Al : - 1.7 Aluminium is very reactive but rapidly forms a thin and
inert oxide which is highly protective
Figure 1
Gold plated computer D plug and connector pins on a computer PCB .
Table 2 Standard Electrode Potentials of Metals
Metal Standard Electrode Potential (volts) Comments
Gold Au+ → Au: + 1.68 Very inert and resistant to oxidation and corrosion
Palladium Pd2+ → Pd: +0. 83 Resistance to corrosion and oxidation less than for gold
Silver Ag+ → Ag: + 0.80 Good resistance to oxidation and corrosion but susceptible to
sulphide and chloride attack.
Copper Cu2+ → Cu : + 0.34 Readily oxidises in air and corrodes where moisture is present
Tin Sn2+ → Sn : - 0.136 Forms a thin inert and protective oxide but is easily
damaged because tin is relatively soft
Nickel Ni2+ → Ni : - 0.23 Readily forms a thin but inert and highly protective oxide.
This prevents further oxidation but is a good electrical
insulator
Aluminium Al3+ → Al : - 1.7 Aluminium is very reactive but rapidly forms a thin and
inert oxide which is highly protective
Comparison of Connector and Contact Materials
Coating MaterialPerformance
Gold Pure gold is fairly soft so hard gold is usually used. Pure gold is not susceptible to corrosion or
oxidation but alloying elements may be. Hard gold which is alloyed with 0.4% Co cannot be used at
200°C as it forms an insulating oxide whereas gold hardened with nickel is satisfactory at this
temperature (5). Gold is usually electroplated onto nickel.
Silver Often used as substitute for gold due to its lower cost but is susceptible to tarnishing from minute
traces of sulphide. It is fairly soft so wear resistance is not good.
Tin Even cheaper than silver but is very soft, and more susceptible to corrosion. Initial contact resistance
is higher than gold and deteriorates if oxidation or corrosion occurs. Particularly poor where fretting
occurs.
Palladium/Nickel Originally introduced as a lower cost alternative to gold but now palladium is more expensive but is
nevertheless used as it has very good wear resistance. It is however susceptible to oxidation,
corrosion and the formation of insulating films, particularly at higher temperatures. Usually,
palladium is electroplated onto a layer of electroplated nickel.
Gold/Palladium/Nickel A thin gold flash is used on palladium to reduce oxidation and corrosion
Gold alloys Used for electrical contacts and applied by cladding. Dilution of gold reduces costs but the
conductivity is not as high as pure gold. Alloys have good corrosion resistance.
Copper and its alloys Clean unoxidised copper has very good conductivity but oxidation and corrosion can occur rapidly
giving an insulating oxide coating. Useful where higher contact force is available and for power
transmission.
Internet communication uses high frequency signals to
pass data between users. This requires very good and reliable
electrical connections and so gold is used for coating
connector pins and for sockets in telecommunications
generally.
Wire Bonding
Most semiconductor packages use very fine gold wires to make
electrical connections between the semiconductor chip and
the leadframe within the package (8). These wires are typically
2mm long and 25μm thick so only about 20 nanograms of
gold is used per wire. However, some ICs can have over 200
wire bond connections and it is estimated that about 80,000
million ICs were manufactured in 2001 (9), which in total
accounts for a large quantity of gold. The quantity of gold used
for wire bonding is continually increasing as more and more ICs
are manufactured. Gold Fields Mineral Services estimate that
demand for gold bonding wire has doubled since 1994 to
about 100 tonnes in 2000 and the continuing long term
demand for new consumer electronics will ensure that this
growth continues (1).
Wire bonding is carried out thermosonically, which uses a
combination of heat and ultrasonic energy, or ultrasonically
without heat. The use of heat alone is rarely used and is
relatively slow. Gold is used for several reasons. Bonding with
gold can be carried out thermosonically with very high
reliability. This is essential where possibly millions of devices
having over 100 leads are manufactured. Manufacturers do
not want to carry out complex and costly tests on every device and so rely on being able to achieve a very high yield
of good ICs. Another advantage with gold is that ball bonds
can be made at a rate of 20 bonds per second. Aluminium is
also used for wire bonding (ultrasonically) but reliable ball
bonds cannot be made and so wedge bonds have to be used
which occupy more space than ball bonds and can be
bonded at a rate of only 8 per second. Gold does not oxidise
or corrode so packages do not need to be hermetically
sealed.
Research into lower cost metals is being carried out.
Copper is difficult to use as it forms an inert oxide which
prevents bonding. Silver is not used as it does not form good . ball bonds, and is susceptible to tarnishing and to
electromigration which can lead to short circuiting between
electrical connections. The interface between silver wire
bonds and the aluminium bonding pads on chips is
susceptible to galvanic corrosion, especially under humid
conditions. Research into silver/gold alloys is being carried
out but reliability is still an issue (10).
Gold Solders
Silicon chips which produce a significant amount of heat
such as those used in power amplifiers need to lose this heat
to prevent damage. Generally, any device that produces
more than 5 watts needs a good thermally conducting
pathway to loose this heat and prevent overheating. This is
achieved by bonding the chip to the package using a solder
alloy. There are two main choices, tin/lead solders and gold
alloys. Eutectic tin/lead forms good bonds and is relatively
ductile but is unsuitable if the component leads are soldered
with standard solder to a PCB or other parts. High melting
point solders having a high lead content can be used but
bonds can be porous with voids, which lead to stresses and
hotspots in the joint. The properties of the more commonly
used die attach solders are listed in Table 4.
The gold solders have better thermal conductivity than tin
or lead based solders and they also have higher melting
temperatures than the lead-free alloys. Thermal fatigue can
also be a problem in power semiconductor components.
Gold alloy solders have better fatigue properties than high
lead content alloys but of course are more costly. However, a
typical IC will use only 2 - 3 mg of gold (11). These gold alloys
are the only lead-free solder alternative to high melting point
lead-rich solder alloys with melting points in the 280 - 360°C
range.
Gold tin solder is also used to hermetically seal some types
of packaging. One example is laser diodes used for internet
communications using 80Au20Sn for the package lid seal as
well as the die attach solder. Solderable Coatings
Gold is wetted very easily by liquid solders and so is used as a
protective solderable coating. Once a printed circuit board
(PCB) has been manufactured, the copper circuitry rapidly
oxidises and it soon becomes impossible for solder to wet the
surface using an electronics flux. Therefore PCB
manufacturers nearly always coat their boards with a
protective coating to protect them during storage. One of
the most popular is electroless nickel, followed by immersion
gold (12). This is more costly than some of the alternatives
but gives superior performance. Organic solderability
preservatives (OSP) are popular because they are low cost but
the protective coating is very susceptible to damage by
fingerprints and light rubbing. Tin and silver coatings are also
available and are less susceptible to damage than OSPs but
more susceptible to tarnishing or corrosion than nickel/gold.
Nickel gold forms a very flat surface and is suitable for
soldering bare chips directly onto the PCB. Another
advantage is that the gold colour makes inspection easier,
but rework can be more difficult. The thickness of gold used
is typically 0.08μm so very little gold is used on each PCB.
When soldered, this very small quantity of gold dissolves into
the solder and remains in solution so does not affect joint
reliability. The solder forms a strong bond to the nickel which
dissolves much more slowly in liquid solder than gold or
copper. Nickel cannot be used alone without the thin
immersion gold layer as it oxidises on exposure to air to form
a thin layer of a very stable oxide which prevents solder
wetting the surface. Extremely corrosive fluxes, which would
alleviate this problem, are unsuitable for electronic circuits.
Electromigration is a process that can affect printed circuit
boards, hybrid PCBs and some electronic components under
certain conditions such as high humidity, an electrical potential
and ionic material, such as flux residues (13). Silver is particularly
prone to electromigration but most other metals will also do this
under certain conditions. Even aluminium conductors within
semiconductor integrated circuits have been known to suffer
from electromigration. Electromigration of gold is very rare and
occurs only if chloride ions are present. Electromigration appears
as a filamental growth of metal that runs between two
conductors and is an electrochemical process. Metal from the
anode dissolves and diffuses under the influence of an applied
current and is electroplated onto the negative electrode.
Anode reaction - metal dissolution with release of electrons:
M = Mn+ + neCathode
reaction - metal electroplating, consumes electrons:
Mn+ + ne-
= M . The relatively large positive electrode potential of gold
makes these reactions less likely to occur than with other
more reactive metals.
Hybrid Circuits
Where the higher production cost is justified, hybrid circuits
are used as they have many advantages over plastic laminate
PCBs. Hybrids are normally used to save space and weight but
thermal dissipation is better. Signal paths are shorter so that
circuits are faster, they can use less power and they have
enhanced performance at high frequencies, and are
therefore often used for microwave circuits. It is possible to
build resistors, capacitors and inductors into inner layers
which saves space on the outer layers. Some types can be
made with hundreds of individual layers and circuits can
safely be used at over 100°C, neither of which is possible for
standard FR4 PCBs.
Hybrid circuits use metal inks to create the conductors.
Gold, silver, palladium, platinum and their alloys are used as
circuits and need to be fired at 850°C during manufacture.
The inks or pastes contain metals in the form of fine powders.
As a conductor, gold is the best material as it has high
conductivity and excellent resistance to corrosion. However it
is more expensive than silver which is an even better
conductor but can suffer from tarnishing and
electromigration problems. Despite these potential
difficulties, many hundreds of times as much silver is used as
gold. Gold is, however, usually used for wire bond pads. A
hybrid circuit can be overall a lower cost option than a plastic
laminate board. Bosch have developed an ABS module which
is designed to be fitted close to the engine. This avoids the
need for an expensive cable so that the overall cost is lower.
One of the advantages with hybrid circuits is that a very
fine pitch can be achieved although the limit is currently
about 400μm (line + space) for screen printed circuitry. There are new products on the market from Dupont and from
Heraeus for making finer lines using photolithographic
techniques but these involve several process steps and create
effluents and are therefore relatively expensive. An
alternative is to print directly with the ERA μ-Screen (14, 15).
This can print 50μm gold lines and 50μm spaces and the
edges of lines are much smoother than screen printed lines
which are affected by the weave of the mesh screens. This
gives superior performance with high frequency circuits.
Sputter Coated Gold
Gold can be coated onto a wide variety of substrates including
metals, ceramics and plastics using various vacuum coating
techniques. With sputtering, gold is used in the form of a
‘target’ which is a specially shaped piece of gold. High energy
ions eject atoms of gold from the surface and these are
deposited onto the material which is being coated. The
quantity of gold that is sputtered has increased significantly
over the last few years, mainly due to the introduction of
Read/Write CDs and DVDs. These have a very thin pure gold
coating that is deposited by sputtering. Gold is used because
it is the best optical reflector with excellent resistance to
corrosion and tarnishing.
Gold is also sputter coated onto gallium arsenide (GaAs)
integrated circuits as the conducting pathways. Gold is not
used on silicon as it reacts with the silicon (for which
aluminium and more recently copper conductors are used)
but it can be used on GaAs and other compound
semiconductors unlike aluminium which interacts (16). The
use of GaAs ICs has increased significantly recently as a result
of new uses in mobile phones, internet communications and
DVD players. GaAs is used because signal speeds are up to 40
times faster than with silicon.
There is a rapid growth in the use of
microelectromechanical systems (MEMS) devices for a wide
range of applications (17). These include crash sensors in
automobiles, optical switches for the internet and pressure
sensors for automobiles and medical applications. Their use
in mobile phones is predicted to grow rapidly as MEMS
switches and other devices are introduced. Most optical
switches are coated with a thin layer of gold, using a vacuum
technique, to make a reflecting mirror surface. Most MEMS
switches operate with a very low contact force and so only
gold can be used to obtain a low contact resistance.
Recycling of Gold from Electronics
The EU is planning to introduce the Waste from Electrical and
Electronic Equipment (WEEE) directive which will require . manufacturers to recycle electronic and electrical equipment
at the ‘end of life’. Currently, only equipment that can be
recycled economically is recycled and the most valuable
component in often gold, particularly in IT and telecom scrap.
The final form of the directive is still unclear but manufacturers
will have to pay for their products to be recycled and any
recovered gold will contribute to cost savings (18).
Conclusions
Gold has a wide variety of uses in electronics because of its
unique physical and chemical properties:
•It has excellent resistance to corrosion and oxidation,
whereas silver tarnishes in atmospheres containing minute
traces of sulphide. Palladium oxidises especially at higher
temperatures and can catalyse the polymerisation of
hydrocarbons and form insulating films. Most other metals
including copper, nickel, iron and cobalt will oxidise in air
and corrode in the presence of moisture and ions,
particularly halides.
•The inertness of gold makes it invaluable as a solderable
coating to maintain the solder wetting properties of PCBs
and component leads. It also allows gold to be used within
the human body as it is not affected by body fluids and is
completely non-toxic.
•The electrical resistivity of gold is the lowest of all metals
except for silver and copper but both of these readily
tarnish causing the contact resistance to increase. For low
current, low voltage conditions and low contact force,
gold is frequently the best choice technically and in some
applications such as automotive and RF connectors and
MEMS switch contacts, it is the only choice.
•Pure gold is a relatively soft metal and so is not ideal for
contacts where wear occurs. Hard gold has been
developed for wear applications but better results are
obtained if this is electroplated onto Pd/Ni layers.
•Gold’s ductile properties combined with the lack of an air
formed oxide allows fine gold wires to be used for wire
bonding within semiconductor ICs. No other metal has the
same reliability at the highest production rates.
•Gold is also used for its light reflecting properties in optical
devices such as optical switches and Read/Write CDs and
DVDs.
The only significant disadvantage of gold that
sometimes discourages its more widespread use is relatively
high metal price compared with base metals such as
copper and nickel. Usually, however, only very small
quantities of gold are used in each product so the effect on
the total cost is often insignificant whereas improved
reliability can result in significant savings.

Most Computers & electronic devices contain circuit boards inside that will contain many types of precious metals. Printed Circuit Boards, Connectors and Components have high levels of precious metal content.
VALUABLE & PRECIOUS METALS – WHERE THEY ARE IN COMPUTERS:
- Gold – Printed Circuit Boards, Computer Chips (CPU), connectors / fingers
- Silver – Printed Circuit Boards, Computer Chips, keyboard membranes, some capacitors
- Platinum – Hard Drives, Circuit board components
- Palladium – Hard Drives, Circuit board components (capacitors)
- Copper – CPU heat sinks, wiring and cables, Printed Circuit Boards, Computer Chips
- Nickel – Circuit board components
- Tantalum – Circuit board components (some capacitors)
- Cobalt – Hard Drives
- Aluminum – Printed Circuit Boards, Computer Chips, Hard Drives, CPU heat sinks
- Tin – Printed Circuit Boards, Computer Chips
- Zinc – Printed Circuit Boards
- Neodymium – Hard Drives (magnets)
EXTRACTION
Chemical extraction of Gold, Silver, Platinum, Palladium and Rhodium can be extracted from such components and the removal and disposal of hazardous materials including Mercury, Cadmium, Beryllium Oxide and Batteries (NiCd, Lithium etc.) is also undertaken.
Elements found in trace amounts include Americium, Antimony, Arsenic, Barium, Bismuth, Boron, Cobalt, Europium, Gallium, Germanium, Gold, Indium, Lithium, Manganese, Nickel, Niobium, Palladium, Platinum, Rhodium, Ruthenium, Selenium, Silver, Tantalum, Terbium, Thorium, Titanium, Vanadium, and Yttrium.
Almost all electronics contain Lead and Tin (as solder) and Copper (as wire and printed circuit board tracks), though the use of lead-free solder is now spreading rapidly.
Computer components containing valuable metals include Motherboards, connector cards, graphic cards, memory cards, CPU’s and other various small electronic components, connectors/cables & Hard drives.
Computer CPU’s (processors) have the most precious metal value by weight, followed by Memory (RAM) & Circuit Board Fingers / Connectors / Pins, then Circuit Boards (Motherboards), then cables / wires, with hard drives & whole computers being last.
CD/DVD drives, monitors, cases, keyboards/mouse, printers, scanners & power supplies typically do not contain enough precious metal to be considered of value.
LIST OF CHEMICAL ELEMENTS USED IN COMPUTERS & ELECTRONICS:
Magnesium, Radium, Barium, Niobium, Osmium, Cobalt, Manganese, Titanium, Hafnium, Tungsten, Germanium, Gold, Silver, Copper, Mercury, Bismeth, Silicon, Gallium, Zinc, Iorn, Sulfur, Phosphorus, Cadmium, Palladium, Tantalum, Platinum, Aluminum, Carbon, Lead, Nickel, Boron, Chromium, Potassium, Fancium, Casium, Sodium, Lithium, Calcium, Nitrogen, Oxygen , Arsenic, neodymium, Selenium, & Tin.
Gold and Gold Alloys in Electronics
Overview
.jpg)
Gold is the material of choice in many electronic applications, especially in telecommunications, information technology and other high performance and safety critical applications. Examine your mobile phone and you will almost certainly see goldplated contacts. Take apart an old computer and there will probably be gold plated edge connectors on the circuit boards. As a result of the growth of these sectors, long term annual consumption of gold in electronics is increasing. During 2007, it was estimated that around 280 tonnes of gold found its way into electronics and electrical components. Where the voltages are small, the circuitry complex or the required reliability high, gold is usually the preferred choice.
Material Properties of Gold
The beneficial material properties of gold include outstanding resistance to corrosion, the ease with which it can be worked and high thermal and electrical conductivity. Only silver and copper are better conductors of electricity, but do not have comparable resistance to tarnishing or corrosion. In conditions under which most other metals either tarnish or corrode away, gold remains inert and extremely durable.
.gif)
So where resistance to tarnish or corrosion is essential, it is therefore common to either use gold or a gold alloy, or to plate gold onto a less noble metal. For electronic applications, the resistance of gold to environmental effects is perhaps its most important property. It means that the technical performance of gold bonding wires or gold electroplating remain essentially unaltered with time.
Optimum Use of Gold
In general, the more sophisticated the equipment and the greater the need for reliability, the greater the requirement to exploit the advantages of gold as a material. This means that in telecommunications, computers, automotive electronics and defence systems where safety is critical, gold is indispensable.
Research and development is continuing to study the optimum use of gold in the electronic sector, including the development of high strength connecting wires and improved wetting solder alloys. Innovations required for information technology in the future will be highly integrated electronic devices, designed and fabricated on the nanometre scale (one billionth of a metre).
Gold will be an indispensable element for nanoscale electronic devices because it is resistant to oxidation and mechanically robust at the incredibly small dimensions defined by nanotechnology.The reliability of gold is an essential characteristic for the increasing use of electronic components in cars.
What Metals Are In Your Electronics?
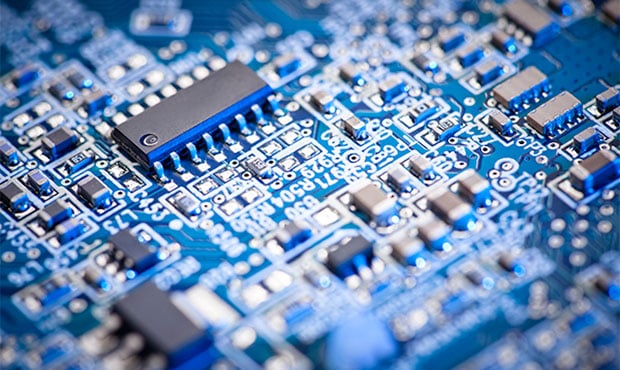
Some people might not know that there are precious metals in your electronic devices but there are some very valuable metals that can be found in your e-waste. Used electronic devices can be reused, recycled, resold, and salvaged. If you choose to recycle your electronic devices not only are making sure that your are protecting your data, you’re also making money off these precious metals that are in these devices. Making sure that you recycle your electronics is very important because the number of people and companies recycling their electronics is low. There are two billion smartphone users upgrade to a new phone roughly every 11 months and barley 10% of those phones get recycled. These phones are just put to waste in a drawer or in a landfill.

By recycling your e-waste the precious metals it allows for these precious metals to be reused, therefore reducing the need to mine and process new materials. Which ultimately has a negative affects the environment. Some of the precious metals that are in these electronic devices include:
Gold: Gold is used in printed circuit boards, cell phones, computer chips (CPU), connectors and fingers.
Silver: SIlver is used in printed circuit boards, cell phones, computer chips, keyboard membranes and some capacitors.
Platinum: Platinum is used in hard drives and circuit boards components.
Palladium: Palladium is used in cell phones, hard drives, circuit board components and capacitors.
Copper: Copper is used in CPU heat sinks, wiring cables, cell phones, printed circuit boards and computer chips.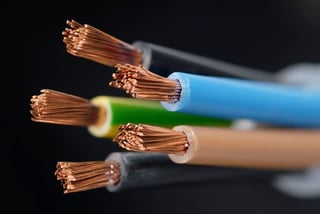
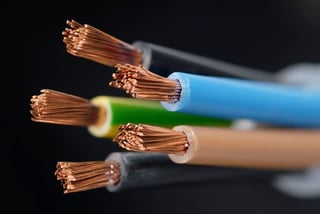
Nickel: Nickel is used in to circuit board components.
Tantalum: Tantalum is used in circuit board components and some capacitors.
Cobalt: Cobalt is included hard drives.
Aluminum: Aluminum is used in printed circuit boards, computer chips, hard drive, CPU heat sinks.
Tin: Tin is used in printed circuit boards and computer chips.
Zinc: Zinc is used in printed circuit boards.
Neodymium: Neodymium is used in hard drives.
The amount of precious metals that are found in electronic devices can be substantial. The EPA estimates for every 1 millions cell phones recycled you can get these amounts of precious metals:
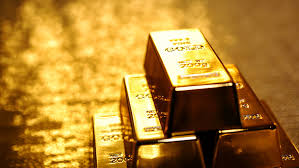
- 35,274 pounds of copper
- 772 pounds of silver
- 75 pounds of gold
- 33 pounds of palladium
When looking at electronics you should be looking at recycling, the computer components with the highest precious metal content by weight:
- Computer CPU’s (Processors)
- Memory (RAM) & Circuit Fingers/ Connectors/ Pins
- Circuit Boards (Motherboard)
- Cables/WIres
- Hard Drives
- Whole Computers
- Cell Phones
Mayer Metals Corporation is based in the Metro Detroit area and provides business to business electronic waste recycling. We provide our customers with:
- Data Security Solutions
- Hard Drive Shredding
- Environmentally Responsible Recycling via an R2 Certified Facility
- Competitive Prices
USE OF GOLD PLATING IN ELECTRONICS
The use of gold plating in the electronics industry has been an ongoing part of the expansion of more complex digital electronics and equipment throughout many industry sectors. According to BullionStreet, over 320 tons of gold are used each year in the electronics industry. This includes gold in PCs, mobile phones, tablets and other devices. The overall use of gold in electronics is via gold plating. Gold plating is primarily used on contacts for switches, relays, and connectors
Gold has the combined elements of electrical conductivity, ductility, and doesn’t corrode at high or low temperatures. The corrosion resistance of gold is one of the key factors that it is used for in electronics. According to GoldAvenue, gold’s resistance to corrosion offers “atomically clean metal surface which has an electrical contact resistance close to zero, while its high thermal conductivity ensures rapid dissipation of heat when gold is used for contacts.”
Several guidelines have been established by AMP Incorporated for the use of gold plating in electrical contacts. Below is a summary of some of these guidelines.
High Reliability Applications and Gold Plating – For connector applications in electronics that require reliability, it is important for the separable contact interface to be shielded from environmental deterioration. An application of gold onto the interface of a separable connector provides a long, stable and very low contact resistance for the component.
Corrosive Environments and Gold Plating – Corrosive environments such as high humidity locations or an environment that contains corrosive pollutants like chlorine or sulfur gases will attack and degrade metals like nickel. This corrosion will interfere with electrical contact. Gold doesn’t break down in these conditions. However, if the gold plating is too thin or porous, it will break up, so it is important for the plating to be done at the correct thickness for full protection and with a suitable under layer metal.
Suitable Under Layer Metals for Gold Plating –In order to avoid degradation of gold plating, especially in corrosive environments as mentioned above, gold plating should be applied over an under layer of a quality metal like nickel. An under layer of nickel will act as the following for a gold plated surface:
- Pore-Corrosion Inhibitor – Nickel as an underplate prevents corrosion via pores in thin areas of gold plating.
- Corrosion Creep Inhibitor – Provides a barrier against corrosion
- Diffusion Barrier – Prevents diffusion of other metals like copper or zinc into the gold surface.
- Mechanically Supporting Under Layer for Contacting Surfaces – Nickel increases gold plating’s durability.
Thickness of Gold Plating Based on Requirements of Electronic Component – The determination of the correct gold plating thickness depends on the application of the electronic component. Despite the decline in the price of gold in recent months, keeping the plating thickness as low as feasible is a good place to begin when determining the overall thickness of the plating. According to the AMP report, “In general, a 0.8 micron (30 micro inches) coating of hard gold over a minimum of 1.3 microns (50 micro inches) of nickel gives a degree of durability considered adequate for most connector applications. Thin coatings of 0.03 - 0.1 microns (1 - 4 micro inches) of hard or soft gold over nickel underplate should be used only for applications in which the risk of fretting is minimal. Increasing the thickness of a gold coating tends to decrease the porosity which reduces the contacts’ vulnerability to pore corrosion.
Gold Plated Contacts Effective at High Temperatures – With gold’s properties, it is an effective protection for electronic contacts exposed to high temperatures (>125⁰C/>257°F). To be certain of protection against elevated temperatures, the nominal gold and nickel thickness should be increased.
These are just a few guidelines for the use of gold plating in electronics. Each application of the electronic component that is to be plated should be determined to make certain that all factors are considered and planned for prior to plating in order to obtain the target performance.
XO__XO Copper
, Silver
and Gold




All three are not only delightful in appearance and resistant to corrosion, but can be hammered into ornaments of artistic distinction. The three are ductile, capable of being drawn into fine wires, and malleable, capable of being hammered into thin sheets. Gold, indeed, is outstandingly ductile and malleable, able to be drawn into wires thinner than a hair and beaten into sheets thin enough to transmit light. All three metals are important in technology, especially in electronics.
Copper and silver, and perhaps even gold, harden when they have been worked, and it becomes impossible to work them further, even with great effort, without danger of cracking and crumbling. This work hardening is seen even when you bend the lid of a tin can back and forth to break it off. However, if the metal is heated sufficiently to allow the metal to recrystallize, on cooling it will be restored to its original soft, workable state. This process of annealing could have been the first metallurgical practice discovered. Copper anneals at a temperature of 200°C - 750°C, the pure native copper at lower rather than higher temperatures. These temperatures are less than a red heat, and are obtained in any common fire.
However, the artisans were still limited to the size of the nugget that was picked up. Large objects required large nuggets, and were correspondingly more valuable than a handful of small objects of the same weight. To make larger objects, the metal has to be melted and poured into a mould. The temperature required to melt the noble metals is close to 1000°C, practically a "white heat." This requires a fire blown by bellows or some other means, though in favorable circumstances a good natural draft might suffice. The fusion of metals could have been the second metallurgical process discovered.
It should be mentioned that most stories about the history of metallurgy are just that: stories. There is no detailed evidence of methods, only the rare object found in excavations, often misidentified, mislabeled and misinterpreted by those unversed in metallurgy or chemistry. Nobody knows the order of discovery, or who the discoverers were. From the scraps of information, a story is constructed on the basis of our current understanding of metals, just as I did in making annealing the first discovery, and fusion the second. This is logical, but not proved. We have much better evidence from classical times, but still do not know much in detail.
Copper knives and weapons were made in pre-dynastic Egypt, perhaps as long ago as 6000 BC by some authorities. Pipes and tubes were found from 2750 BC, and a bronze mirror dates from 1800 BC. However, metals were rare in Egypt, and a non-metallic culture predominated. The smelting of metals from ores is a significant and much later discovery than the use of native metals, annealing and fusion. This is discussed at more length in Tin. This metallurgy may have originated in Mesopotamia around 2000 BC, and perhaps also in India. The Phoenicians made smelted copper and tin available to the Mediterranean world, and with it the alloy bronze, around 1800-1500 BC. I would like to have better estimates of these dates, but the authorities seem to be in disagreement, and not all that knowledgeable about metals anyway.
Although copper was probably originally encountered in nature as the native metal, it was also probably the first to be extracted by smelting from ores. Zippe proposes that this was discovered when heat was used to break rocks for the native copper they contained, since stone tools would not suffice, and some of the ore, so different in appearance from metallic copper, was reduced. Copper was the first metal whose ores were mined, and some of the earliest mines have left traces, as in the Sinai peninsula.
Copper
Copper was the predominant early metal, especially after the technique of smelting it from its ores and trade made it widely available. It is still the third most important industrial metal, after iron and aluminium. Our word "copper" comes from the Plattdeutsch coper or koper, still used in Dutch. In Latin, it was known as cyprium aes, "brass from Cyprus" or "brass of Venus." Aes was the Latin for all coppery-bronzy-brassy alloys, which I have translated as "brass," though what we call brass was a later development, but still Classical. Copper in particular was also called adhenus, as was a copper pot. However, the Venusian name stuck in the West, and gave us cobre in Spanish, cuivre in French and Kupfer in German. In Welsh it is copr, which suggests that this word comes from old Celtic, and is unassociated with Venus. In Russian, copper is med', a quite different word, whose etymology might give us valuable information.
Greek, also, had a different word. Here, the equivalent of aes was calkos, "chalcos," named after the copper mines at Chalcis in Euboea. This stem is often seen as referring to copper, notably in mineralogy. "Chalcopyrite" is copper pyrites. The word was applied to iron as well after its introduction, long before the coining of sideros, "sideros." The word for steel is caluy, clearly related to chalcos. The Phoenicians, and others, worked copper mines and smelters in Cyprus, Kupris. Venus, or Aphrodite, the Kupris, was born there, always loved the island, and was its patron. She is very often referred to as Cypris. The word "cuprium" could have come either from the island or the goddess, and it is impossible to make a distinction. The word cuprum was probably later Latin, and gave us the chemical symbol Cu. The alchemical symbol was the sign of Venus, shown in the title of this article. The Phoenicians were surely the ones who spread the knowledge and use of copper around the Mediterranean, and their metallurgical procedures were probably kept secret.
The fact that pure copper and its alloys were not distinguished in ancient words shows that a fundamental difference was not appreciated. Our recognition of chemical elements is recent, and quite foreign to earlier thought. Most ancient "copper" is indeed bronze, containing tin but also lead and zinc. The alloys have a somewhat lower melting point than pure copper, and so would be easier to work, besides being much harder and more usable as tools and weapons. Zippe concludes from the various names of copper and its alloys used by different peoples the probable multiple discovery of its smelting. He also remarks, quite to the point, that it is just as possible that a source of a metal was named after the metal as that the metal was named after a place.
Copper is often described as a "red" metal, though its actual color is an orange-red of lower intensity, not a bright signal red. It is not a spectral color by any means, but a particular impure one requiring its own name, such as "copper-red." The red color is produced by the density of electrons being insufficient to cause a high plasma frequency, so the shorter wavelengths are not reflected as efficiently as the longer, redder ones. The red color is unique to copper and its alloys.
Copper has atomic number 29, atomic weight 63.57, and density 8.94 g/cc. Its naturally-occurring isotopes have mass numbers 63 (69%) and 65 (31%). The electron configuration has one 4s electron outside a filled 3d shell in the ground state. However, the energies of the 3d and 4s orbitals are about equal, so a 3d94s2 configuration is as favored as a 3d104s. Copper exhibits valences +1 (cuprous) and +2 (cupric), with the +2 predominating. Copper metal has a face-centered cubic structure, with a = 0.361 nm. Each ion has donated one electron to the Fermi sphere. The work function of copper is about 4.7 eV (tabulated values vary from 3.85 to 4.86). The Fermi energy is 7.0 eV. The electrical resistivity of annealed copper is 1.7241 μΩ-cm, of hard-drawn, 1.771 μΩ-cm, and the temperature coefficients are 0.00393 and 0.00382 per °C, respectively. For pure copper, the resistivity is 1.683 μΩ-cm. The thermal conductivity is 0.923 cal/cm-s-K, and the linear coefficient of expansion is 16.42 x 10-6 per °C. The specific heat is 0.0918 cal/g-K. The melting point of copper is 1083°C, boiling point 2325°C, and the heat of fusion is 50.6 cal/g. Its hardness is 3.0 on the Mohs scale. The tensile strength of annealed copper is about 30 ksi, of hard-drawn copper, 60 ksi. The Young's modulus is 16 x 106 psi.
For most uses, copper is alloyed with other metals, though copper usually predominates. Bronze is discussed in Tin and brass in Zinc. Copper-nickel alloys are used in coinage. Aluminium makes the excellent aluminium bronze. Pure copper is used for electrical conductors, since any alloy usually greatly increases the resistivity. Silver, cadmium and zinc have the least effect. 1% Cd decreases the conductivity to 94%, while hardening and strengthening the copper. Cadmium copper is used for contact wires. Arsenic, a common hardening addition to copper, has a large effect. 0.1% As lowers the conductivity to 75% of the value for pure copper, 0.5% As to 40%. Arsenic raises the softening (annealing) temperature to around 550°C from 190°C for pure copper. Arsenical copper with 0.5% As is used in boiler fireboxes, tubes and rivets to give strength at elevated temperatures. More arsenic embrittles the copper, and is very undesirable. Speculum metal, 89 Cu 33 Sn, is white and can be polished to make good mirrors. It was known in antiquity and used for mirrors.
Copper, like the other members of the royal family, is unreactive, with an electrode potential of 0.47V. It is not attacked by nonoxidizing acids or alkalies. In moist air, however, it may be attacked even by dilute acids. The CO2 in moist air creates a layer of CuCO3·Cu(OH)2, a basic copper carbonate called verdigris of a greenish color, called a patina, considered to be attractive. Otherwise, as in household copper, oxygen and sulphur make a film of black CuO or CuS tarnish. This happens very slowly, and the copper is not corroded. If regularly polished, it remains shiny and attractive.
The process of "flashing" a deep red surface layer of glass containing colloidal copper oxide was discovered in Bohemia around 1842, and became an alternative to the ruby glass that was a colloidal suspension of gold. This process was widely used to make signal lenses and similar products in place of the more expensive ruby glass. Note that the colour here is superficial, while in ruby glass it is a body colour. Copper also makes green, blue and brown pigments.
Cuprous oxide, Cu2O is red, and cuprous sulphide, Cu2S is black. Both are very insoluble. In any soluble cuprous compound, auto-oxidation generally occurs, 2Cu+ → Cu + Cu++, producing the cupric salt. Cupric oxide, CuO is produced by heating copper in air, or by strongly heating any oxygen-containing cupric salt. CuS is produced in an analogous way. In solution, the copper ion forms complex ions, such as Cu(H2O)4++, or Cu(NH3)4++. These are flat, square ions, of blue color. The water ion is medium blue, the ammonia ion dark blue.
Soluble copper compounds are all very poisonous. Indeed, they are often used as insecticides and algacides. This is not unexpected, since most heavy metal ions are also poisonous. Copper, however, seems to have escaped the notice of chemophobes who have persecuted lead and mercury.
Copper tarnish is composed of CuO, and the basic carbonate if moisture and air are present. It can be removed by solutions containing the ammonium ion, which forms the soluble ammonia complex. The commercial preparation Brasso is an example. Other copper polishes use different means not revealed on the labels, but boast that they do not contain ammonia. Copper polishes should not be used on silver, since they will attack it. Copper polishes seem to attack the copper as well, but not seriously. Kitchen ammonia does not seem to remove copper tarnish. Lemon juice, salt and vinegar, however, seem to remove tarnish well. None of the three works on its own, but all three together do. Mechanical scouring is also recommended for copper.
Cupric sulphate, CuSO4·5H2O, called bluestone or blue vitriol, is soluble in 0°C water to 24.3%, in 100°C water to 205%. The blue color requires the water. The anhydrous salt, prepared by heating, is white or pale green. Its solutions are slightly acidic, and are strong germicides and fungicides. Bordeaux mixture is a garden insecticide that contains copper sulphate. The triclinic crystals are easily grown. This is the substance that supplies the copper ions in a Daniell cell or gravity cell. The sulphate can be recovered by dissolving the copper cathodes of the cells in sulphuric acid, so the copper is continuously regenerated as the zinc is burned. The Daniell and gravity cells are discussed in Electrochemistry.
Copper is easily electrolytically plated from an acid solution of Cu(SO)4, since it is below hydrogen on the electrochemical scale, or from an alkaline solution of potassium cuprocyanide, KCu(CN)2. It will not give cathodic protection to iron, so care must be taken that the coating is continuous to avoid corrosion at pinholes. The copper layer is usually excellent, and can be a base for other plating for decorative effect. Chromium plating, which is always porous and non-protective, is conveniently done on a thin copper plate, or on nickel on top of the copper. Many automotive parts are zinc die-castings, plated with copper, nickel and finally chromium. Chromium is protected by a thin, invisible adherent layer of Cr2O3 like aluminium, but this does not rob its lustre after polishing of the plated layer.
Cuprous oxide was used in one kind of metallic rectifier, a predecessor of the semiconductor diodes of today. A plate of copper was strongly oxidized on one side to produce a thick layer of CuO. This was heat-treated so that a thin layer of Cu2O would grow between the Cu and the CuO. Then the CuO was stripped off with acid, and a contact of lead or similar material applied. The copper base plate acted as an n-type material, while the Cu2O was p-type, and a pn-junction was formed. This junction had a forward bias voltage of a few tenths of a volt, a reverse breakdown voltage of 5V or 6V, and a rather low maximum operating temperature. A stack of such elements could be assembled for higher voltages. The reverse current was larger than would be tolerated now, but was satisfactory for battery chargers and other similar devices. Similar rectifiers were made from Cu2S on magnesium, and selenium on iron or aluminium. These were quite satisfactory for low voltages and moderate currents, but have been completely replaced by the cheaper silicon diodes with far superior characteristics.

The sulphide ores are roasted to drive off the sulphur, arsenic and antimony, then calcined with sand or lime to slag off iron and more sulphur, producing a black matte consisting mainly of sulphides, like Cu2S. The matte is reduced in a blast furnace with air and the sulphur it contains to produce blister copper. Oxide ores are reduced with carbon. The blister copper is then dissolved in H2SO4, which can be made from the gases evolved in roasting and reduction, and the solution electrolyzed to produce cathodes of pure electrolytic copper. Gold and silver are usually recovered from the electrolysis sludge, and help the economics of the process. Modern smelting is much different from ancient smelting, since the ores treated are much leaner. Electrolytic copper was once traded principally in "wire bar," which was ready for the wire-drawing process. It is now supplied as "refined cathodes," which are continuous-cast at the beginning of wire drawing. The price is often quoted for 100 lb cathodes. The current price of copper is about $0.77 per pound.
Early copper smelting in the United States was established in the vicinity of New York, and the copper was used in the brass works in the Housatonic Valley of Connecticut. Electrolytic reduction favored locations on the coal fields of western Pennsylvania where power could be produced cheaply, and even later in the far west where hydroelectric power was used. This expanded greatly with the creation of government-subsidized electricity from large hydroelectric projects, since there was otherwise no need for the electricity produced, and it was all but given away to create a little benefit to the cost-benefit ratio. Free enterprise thrives with government's aid to channel the public's wealth into private pockets, then as now.
Silver
Silver is the same as Dutch zilver, German Silber, and the Anglo-Saxon seolfor, except for the orthography. The sound is the same, except for the well-known s/z and b/v alternatives. The Greek argyros and Latin argentum are clearly cognate, and Latin would even have used argyrum, with its normal transliteration of a Greek word. These give argento in Italian, and argent in French. Spanish is different, using plata instead. In Welsh, silver is arian, a Celtic word probably also related to argyros. In Russian, we have cerebro, with still another root. This suggests that silver was earlier than copper in daily life, and had a name in Indo-European. The alchemical symbol for silver is the sign of the Moon, a white crescent.
Silver is a white metal, like tin and cadmium, which resemble it, but are softer and lighter. When polished and untarnished, it has excellent, uniform reflectivity and so was preferred for mirrors. The white color is different from this perfect reflectivity, and is seen on matte surfaces. It was by far the earliest and most used coinage metal, and its name in many languages also is the simple word for money of any kind: j'ai de l'argent--I have money. In America, plata is money, though in Spain it is dinero, from the Arabic dinars that were once familiar there.
Silver has atomic number 47, atomic weight 107.880, and density 10.5 g/cc. Its naturally-occurring isotopes have mass numbers 107 (52%) and 109 (48%). The electron configuration has one 5s electron outside a filled 4d shell in the ground state, just like copper. However, the energies of the 4d and 5s orbitals are about equal, so a 4d95s2 configuration is as favored as a 4d105s. Silver exhibits valence +1 in most of its compounds, and forms complex ions. Silver metal has a face-centered cubic structure, with a = 0.408 nm. Each ion has donated one electron to the Fermi sphere. The work function of silver is about 3.7 eV (tabulated values range from 3.0 to 4.75). The Fermi energy is 5.5 eV. The electrical resistivity of silver is 1.62 μΩ-cm and the temperature coefficient is 0.0038 per °C. The thermal conductivity is 0.974 cal/cm-s-K, and the linear coefficient of expansion is 18.6 x 10-6 per °C. The electrical and thermal conductivities are slightly greater than those of copper, and the largest of any metal's. The specific heat is 0.0558 cal/g-K. The melting point of silver is 961°C, boiling point 1955°C, and the heat of fusion is 24.3 cal/g. Its hardness is 2.7 on the Mohs scale. The tensile strength of cast silver is about 40 ksi, of hard-drawn, 51 ksi. The Young's modulus is 10.3 x 106 psi.
Silver has a relatively simple chemistry. It dissolves in concentrated nitric acid to form colorless silver nitrate, AgNO3, called lunar caustic. This is a powerful antiseptic. Adding sodium hydroxide to a solution of silver nitrate precipitates brown Ag2O, which is only slightly soluble. Adding silver oxide to halogen acids makes the silver halides, such as AgCl, which, like most silver compounds, are insoluble. Silver chloride is white, and the bromide is pale yellow. On exposure to light, they gradually turn black by the photochemical reduction of the silver to metal. Silver forms soluble ammonia Ag(NH3)2+, thiosulphate Ag(S2O3)2--- and cyanide Ag(CN)2- complex ions. The thiosulphate ion is used to dissolve undeveloped AgBr and "fix" a photographic image. The cyanide ion is used in silver plating and in the cyanidation process for the recovery of silver. Silver fulminate, Ag2(CNO)2, is a powerful explosive. It has been formed in small amounts when mirrors are chemically silvered.
The salt KAg(CN)2, potassium argenticyanide, is soluble, and is made the electrolyte in a silver plating bath. The object to be plated forms the cathode (the negative electrode) and the anode can be silver or an inert substance. For every electron entering the cathode from the external circuit, one atom of silver is reduced. The concentration of uncomplexed silver ions is very small in the argenticyanide solution, which aids the deposition of a dense and uniform coat of silver. Many precautions must be observed to get a good result, among them thorough cleaning of the surface to be plated, and plating on a suitable metal, such as copper or nickel. Silver is plated at a current density of 5-15 A/sqft, which requires 1-2V. Each Faraday of charge, 96 480 C, deposits 108 grams of silver.
Silver is used for tableware, a practice that used to be much more common than it is now. The best silverware is made from Sterling, 0.925 fine silver, and has an excellent appearance, though it was expensive. To bring silver within the reach of more of the public, Sheffield Plate was introduced in 1743. Silver was melted onto brass or copper ingots, and the ingots were then rolled, giving a thin cladding of silver on the base metal, greatly reducing the cost of items made from it, which were as beautiful as solid Sterling. This was the earliest industrial use of cladding, which has become a very useful process. In Alclad, the pure aluminium cladding gives corrosion resistance to the underlying Duralumin allow. A later method of making inexpensive silverware was also introduced in Sheffield, the EPNS or electro-plated nickel silver process that uses electroplating.
Silver is quite resistant to corrosion, but is tarnished by materials containing sulphur, such as eggs, mustard and rubber. Silver tarnish contains only black Ag2S, since silver resists oxidation and does not form a carbonate. The tarnish can be removed by rubbing with a sodium bicarbonate, NaHCO3, paste. In the alkaline environment, soluble Na2S is formed and can be washed away. There are proprietary silver polishes that do the same thing, possibly more rapidly than the bicarbonate. Household hints suggest the use of ammonia, or salt and ammonia. One household hint suggested the use of electrolysis. In an enameled kettle, bring a solution of one tablespoon each of bicarbonate of soda and salt to one quart water to a boil. Put an aluminium pie pan in the bottom of the kettle, and in it the silver to be cleaned. Boil for 2-5 minutes. There is a warning against using this for hollow ware or plate. If you have valuable silver coins, it is best not to clean them, since the "toning" is often desirable, especially when blue, violet or orange.
Only limited amounts of silver are found as the native metal. Most comes from argentite, Ag2S, a soft black mineral that can be cut by a knife. The fresh surface is metallic and shiny, but tarnishes rapidly. Argentite is often associated with native silver. Mexico's wealth in silver was revealed through the Patio process, developed at Pachuca in 1557 by Bartoloméo de Medina. Crushed ore was roasted with salt and cupric sulphate to reduce the silver to metal, after which the matte was amalgamated with mercury on an amalgamating table. The mercury coated the surfaces of the small particles of silver and made them coalesce into a mass that could be scraped from table and distilled to recover the silver. A similar amalgamation process was used for gold. Amalgamation does not give as great a recovery as the cyanidation process that has succeeded it. In this process, the finely divided silver or gold is dissolved by a dilute cyanide solution, which is filtered, and silver and gold are precipitated from the filtrate by zinc. Infinitely more wealth was acquired by mining than from filching the metal the natives had picked up from the ground. Mexico is probably still the largest producer of silver, as it has been since the 16th century.
Silver is often associated with lead, from which it is separated by the process known as cupellation, in which the lead is oxidized and leaves the silver behind. For more information on cupellation, see Lead.
Silver is also found as AgCl, cerargyrite, or horn silver. It is soft and translucent, like animal horn, not silver used for horns. It rapidly darkens on exposure to light as silver is photochemically reduced, becoming violet-brown. It is a supergene ore, created in zones enriched by percolating water containing chlorine. Cerargyrite was common at Leadville, Colorado, and also in the Comstock Lode in Nevada, as well as other places.
The silver photographic process uses an emulsion of AgBr in gelatin coated on a cellulose acetate film or glass plate. The emulsion may be sensitized by treatment with a solution that deposits active impurities in the emulsion. On exposure to light, these centers are photochemically altered to become centers that catalyze the reduction of metallic silver. The reduction is carried out by means of a reducing agent called a developer. When a sufficient density of silver has been reached, the film is passed through a stop bath of acetic acid to stop the developing action, and then soaked in a bath of Na2S2O3, sodium thiosulphate or "hypo" to remove the remaining AgBr before it can darken. The film is then thoroughly washed and dried. Positive prints are made from the transparent negative in the same way. This is not the only photographic process, but it is by far the fastest and most sensitive, and has been extensively developed.
Silver, or analog, photography is now being replaced by digital photography, where the image is created and scanned on a matrix of sensors, and stored digitally. Silver photography is to digital photography as a manuscript is to a disk file.
Silver was also used in photosensitive cathodes. Although silver does not have a particularly low work function, Ag2O and Cs on Ag do, and can be sensitive into the infrared. Such cathodes were widely used in vacuum phototubes and photomultipliers. Ag2O is also used in alkaline battery cathodes.
Silver and gold were traditionally weighed in troy measure. A troy pound contained 12 troy ounces or 240 pennyweights (pwt), and was 373.2417 g. The prices of silver and gold are quoted in dollars per troy ounce for 0.900 fine metal. On 22 November 2002, the New York spot price of silver was $4.475, and gold $317.65. Sterling silver is 92.5 Ag, 7.5 Cu. Purity is also indicated by the carat system. Pure metal is 24 carat. 0.900 fine is 21.6 carat. Sterling silver is 22.2 carat. 18 carat gold is 0.750 fine. In Britain, silver and gold were "hallmarked" by stamps to show the fineness and the source. U.S. silver coins, minted up to the 1960's, were .900 fine were beautiful, very unlike the unattractive base tokens that replaced them. British silver coins had been debased much earlier, before finally being replaced by base metal.
Gold
Gold is Gold in German, goud in Dutch. In Latin, it was aurum, from which come French or, and Italian and Spanish oro. In the country, "au" sounded more like "o" than the city pronunciation "ow," and this has been reflected in the later spelling. The Welsh is aur, cognate to aurum. The Greek is chrysos, from a different stem, as is Russian zóloto. Like silver, gold is an ancient metal with different words for its name in the Teutonic, Celtic/Italic and Greek languages. The word aura in Latin and Greek is a light, cool breeze, while aurion is "tomorrow" in Greek. Neither of these has much to do with gold. "Aurum" could have given its name to the dawn as well as the dawn to aurum, and I don't believe they have anything to do with each other. The alchemical symbol for gold is the sign of the Sun. Gold is generally regarded as the first metal known and prized by mankind. This is likely, but there is absolutely no hard evidence. Copper and silver, as native metals, are also contenders, and less rare. To the alchemist, gold was associated with the sun, whose name and symbol were adopted for it.
The yellow of gold is an orangish-yellow, not a bright cadmium yellow, a complex color that has its distinctive name. It has long been used for the most precious ornaments, as a repository of wealth, and for transactions of great value. It can be drawn into fine wire or hammered to a foil with ease. It can be inlaid on heated base metals by hammering, or applied as an amalgam with mercury. For normal daily transactions, it has been much less used than silver. Anyone who has acquired gold does not generally like to give it away; the hoarding of gold is notorious. It is among the heaviest of metals. At 19.3 g/cc, it is nearly twice as heavy as silver, and even lead. Like Martha Stewart, gold is not only beautiful, but is quite useful.
Archimedes was faced with the problem of determining if the crown made for Hiero, tyrant of Syracuse, contained the full weight of gold furnished to the goldsmith who made it. The crown, of course, weighed the full weight, but there was the possibility that the goldsmith had taken a certain weight of the gold for himself, and replaced it with base metal. No base metal had half the density of gold, so although the crown was of the same weight, it would be larger in volume. Archimedes immersed the crown in a bath just full with water, and measured the volume of the water that overflowed when the crown was submerged in it. He found that the crown was of larger volume than it should have been, and that the goldsmith was indeed guilty of defalcation. The story is told in Vitruvius, de Architectura, IX 9-12.
Gold has atomic number 79, atomic weight 197.2, and density 19.32 g/cc. Its single naturally-occurring stable isotope has mass number 197. The electron configuration has one 6s electron outside a filled 3d shell in the ground state, just like copper. However, the energies of the 5d and 6s orbitals are about equal, so a 5d96s2 configuration is as favored as a 5d106s. Gold forms very few stable compounds, and exhibits valences of +1 and +3. Complex ions are important in its chemistry. Gold metal has a face-centered cubic structure, with a = 0.408 nm, almost exactly the same as silver. Each ion has donated one electron to the Fermi sphere. The work function of gold is about 4.7 eV (tabulated values range from 4.0 to 4.86). The Fermi energy is 5.5 eV. The electrical resistivity of gold is 2.44 μΩ-cm and the temperature coefficient is 0.0034 per °C. The thermal conductivity is 0.7003 cal/cm-s-K, and the linear coefficient of expansion is 14.43 x 10-6 per °C. The electrical and thermal conductivities are less than those of copper and silver, but gold is still a good electrical and thermal conductor. The specific heat is 0.0316 cal/g-K. The melting point of gold is 1063°C, boiling point 2530°C, and the heat of fusion is 16.3 cal/g. Its hardness is 2.5 on the Mohs scale. The tensile strength of cast gold is about 20 ksi, of hard-drawn wire, 37 ksi. The Young's modulus is 11.3 x 106 psi.
Gold is found almost entirely as the native metal, originally widely disseminated in quartz veins in hypothermal deposits. As the veins weather, the gold particles get into streams where they are concentrated by the natural action of the water into placer deposits. Many of the famous California placers were "elevated placers," covered with lava and then left high on the hillsides by erosion. The problems of winning gold are those of separating it from the gangue that accompanies it. No smelting is required. Some gold is found in the rare minerals calaverite, AuTe2 and sylvanite AuAgTe2. These tellurides have been found at Cripple Creek, Colorado, Kalgoorlie, Australia, and in Transylvania (Siebenbürgen), with smaller amounts elsewhere, such as Calaveras County, California. There does not appear to be very much, if any, at Telluride, Colorado. Heating the telluride ore is sufficient to liberate the gold. Gold is frequently associated with silver, and the two metals are alloyed in the recovered metal.
Unlike other metals, gold has not been acquired by mining until modern times. It was traditionally found in placer deposits in rivers, which form easily since the density of gold, 19.3, is much higher than the density of gangue, which is about 2.6. The gold is concentrated at certain locations where the flow is locally diminished so the gold can settle out. These deposits originate when gold-bearing quartz veins are weathered out, but often the source of placers was not known. The Tajo (in Spain), the Po, the Pactolus (in Asia Minor) and the Ganges were historically well-known sources of gold, mentioned in Pliny. In more recent times, the "mother lodes" in granitic rocks have been located and mined, sometimes by tracing placer gold back to its source. Although nuggets of gold weighing as much as 600 lbs have been found, most gold is very finely divided. Even in a rich placer, the gold may not be detectable by the eye, even when aided with a magnifier. Sometimes, with the passage of time, an exhausted placer may become productive again as its source continually weathers and more gold is deposited.
Gold can be separated from gangue by panning, using water in a shallow pan to sluice away the lighter gangue from the heavy gold. This method, also called washing, gives very poor recovery, especially of the smaller particles, even when mechanized. Waste heaps from this gravity recovery can be profitably exploited by using more efficient methods of recovery. The finer gold can be separated by amalgamation with mercury. At 100°C, mercury can dissolve 15.7% gold. An amalgamation table consists of a copper trough which is thoroughly amalgamated. The finely ground mixture ("slime") of gold and gangue is then treated with excess mercury and agitated, so that the amalgamated gold particles adhere to the table. At intervals, this amalgam is scraped off and distilled to recover the gold. Amalgamation gives much better recovery, but there is still a considerable loss of gold. Placer gold was discovered in California in 1848, and mercury in 1850, a convenient circumstance. Still more thorough recovery is possible with the cyanide process, introduced in 1893. Gold is recovered as sodium aurocyanide, NaAu(CN)2 on leaching of the concentrate with NaCN, sodium cyanide. The amount of gold recoverable by cyanidation of tailings is probably comparable that originally recovered by amalgamation, and amalgamation probably recovered more gold than the initial washing.
Zippe gives an excellent account of the exploitation of gold in Europe from ancient times. Once-rich sources have been exhausted, in locations like Spain and France. Spain was the most prolific gold producer in ancient times, enriching the Visigoths as well as the Moors before its exhaustion. The Rhine, Garonne and the Rhône carried gold from the Alps. Little gold was found in Scandinavia, but the Harz, Thüringer Wald, and the Fichtelgebirge all contributed. Ireland had placer gold near Wicklow, and Scotland near Leadhills. In the middle ages, Bohemia was a prolific gold producer, in the Sudeten mountains and Silesia; the gold rush there was like later California and Australia. Gold washing left large heaps of refuse, destroying most of the valuable farmland in mountain valleys, and sometimes leading to famine, always to conflict betweeen miners and farmers. It is not mentioned if these tailings have been later treated by amalgamation or cyanidation to recover the large amounts of gold they must still retain. By the 19th century, Austria-Hungary was the only considerable producer of gold remaining in Europe. The Siebenbürgen (57%) and Hungary (40%) were the major producers, with smaller contributions (3%) from Salzburg, Tirol, the Balkans, and what remained from Bohemia. The average annual production from 1823 to 1848 was 450,000 ducats, about the same as the southern U.S. states. California produced about 22,000,000 ducats a year in its early days.
Currently, the gold and gangue, sometimes of very lean concentration--often tailings of the amalgamation process--are leached in the open air with a dilute cyanide solution. The solution is drawn off and filtered at intervals, and gold is precipitated in the filtrate by metallic zinc. This can give 97% recovery, an excellent result. There is also a chlorine process, where the gold dissolves as AuCl2- ion when chlorine is bubbled through the ore. Open-heap cyanidation is much less hazardous than would be imagined. Attempts to outlaw it are ignorant and misguided; much better would be to ensure that it is done in a safe manner.
Most gold is accompanied by up to 10% silver, while other metals are exceptional. If there is 20%-40% silver, the alloy is called electrum. Incidentally, alloys in which gold predominates still have the properties of gold, including its resistance to corrosion, but are harder and of lighter color. Electrum may be white like silver, but will not tarnish. Separating gold from impurities is called parting, and was a very difficult thing in antiquity, when strong acids were unknown. Nevertheless, it was eventually possible, and Roman gold coins were quite pure, though later gold coins often had considerable silver content. The ancient process is probably no longer known. Modern methods of parting include the use of sulphuric or nitric acid, which dissolves the silver, or electrolysis. Silver can be parted from gold by bubbling chlorine through the molten metal; under these conditions it produces AgCl and leaves the pure gold behind.
Gold forms complex ions with cyanide and chlorine, as we have seen. Aside from this, gold has very little chemistry. It should be noted that although gold will not combine with other elements willingly, it combines very well with itself to form the metal. Any gold compound will decompose to the metal on heating. The metal is not attacked by the air, simple acids (except selenic), or alkalis. Gold oxides are difficult to form and unstable. It is attacked by selenic acid, but more notably by aqua regia, "royal water," composed of 1 part concentrated nitric acid to 3 parts concentrated hydrochloric acid. The Cl- forms the complex chloride ion with the gold, thereby dissolving it. If stannous chloride, SnCl2, solution is added, stannic ion is formed which immediately hydrolyzes to a hydrosol of stannic hydroxide. Simultaneously, gold is reduced from the complex ion and is adsorbed on the hydrosol, making a brilliant purple color called the Purple of Cassius. This is a very sensitive test for gold, detecting one part in a hundred million (10 ppb).
Aqua regia, in German Königswasser, appears to have been first prepared by Andreas Libau (Libavius) around 1600. Libau discovered concentrated hydrochloric acid, while strong nitric acid was discovered by the "False" Geber around 1300. The ascription of aqua regia or nitric acid to Geber (Jabir ibn-Hayyan, ca. 760-815) appears to be erroneous. Among other things, nitrates were yet unknown in the West in Geber's times. Alchemists long strove to purify lead so that the pure heavy substance, gold, would appear, or to make gold from mercury and sulphur, combining their attributes. Aqua regia made the purification of gold much easier.
In the AuCl4- ion, the gold is bonded covalently to the four chlorines at the corners of a square. In acid solution, this becomes chlorauric acid, which makes salts: for example, sodium chloraurate, NaAuCl4·2H2O. Auric chloride, AuCl3, is formed by oxidizing the ion. Chlorauric acid crystallizes out when an aqua regia solution of gold is evaporated.
Gold is used in microelectronics to plate connection pads, since it solders very well, and for electrical contacts, because it does not corrode. Fine gold wires connect chips to the pads leading to the package pins. Because gold is so inactive, it is not poisonous. It is excellent for dental work, making durable crowns. If gold were cheaper, it would find many additional uses in technology.
XO___XO REXXX Redox Reactions
Redox reactions, or oxidation-reduction reactions, have a number of similarities to acid-base reactions. Fundamentally, redox reactions are a family of reactions that are concerned with the transfer of electrons between species. Like acid-base reactions, redox reactions are a matched set -- you don't have an oxidation reaction without a reduction reaction happening at the same time. Oxidation refers to the loss of electrons, while reduction refers to the gain of electrons. Each reaction by itself is called a "half-reaction", simply because we need two (2) half-reactions to form a whole reaction. In notating redox reactions, chemists typically write out the electrons explicitly:
This half-reaction says that we have solid copper (with no charge) being oxidized (losing electrons) to form a copper ion with a plus 2 charge. Notice that, like the stoichiometry notation, we have a "balance" between both sides of the reaction. We have one (1) copper atom on both sides, and the charges balance as well. The symbol "e-" represents a free electron with a negative charge that can now go out and reduce some other species, such as in the half-reaction:
Here, two silver ions (silver with a positive charge) are being reduced through the addition of two (2) electrons to form solid silver. The abbreviations "aq" and "s" mean aqueous and solid, respectively. We can now combine the two (2) half-reactions to form a redox equation:
We can also discuss the individual components of these reactions as follows. If a chemical causes another substance to be oxidized, we call it the oxidizing agent. In the equation above, Ag+ is the oxidizing agent, because it causes Cu(s) to lose electrons. Oxidants get reduced in the process by a reducing agent. Cu(s) is, naturally, the reducing agent in this case, as it causes Ag+ to gain electrons.
As a summary, here are the steps to follow to balance a redox equation in acidic medium (add the starred step in a basic medium):
- Divide the equation into an oxidation half-reaction and a reduction half-reaction
- Balance these
- Balance the elements other than H and O
- Balance the O by adding H2O
- Balance the H by adding H+
- Balance the charge by adding e-
- Multiply each half-reaction by an integer such that the number of e- lost in one equals the number gained in the other
- Combine the half-reactions and cancel
- **Add OH- to each side until all H+ is gone and then cancel again**
In considering redox reactions, you must have some sense of the oxidation number (ON) of the compound. The oxidation number is defined as the effective charge on an atom in a compound, calculated according to a prescribed set of rules. An increase in oxidation number corresponds to oxidation, and a decrease to reduction. The oxidation number of a compound has some analogy to the pH and pK measurements found in acids and bases -- the oxidation number suggests the strength or tendency of the compound to be oxidized or reduced, to serve as an oxidizing agent or reducing agent. The rules are shown below. Go through them in the order given until you have an oxidation number assigned.
- For atoms in their elemental form, the oxidation number is 0
- For ions, the oxidation number is equal to their charge
- For single hydrogen, the number is usually +1 but in some cases it is -1
- For oxygen, the number is usually -2
- The sum of the oxidation number (ONs) of all the atoms in the molecule or ion is equal to its total charge.
As a side note, the term "oxidation", with its obvious root from the word "oxygen", assumes that oxygen has an oxidation number of -2. Using this as a benchmark, oxidation numbers were assigned to all other elements. For example, if we look at H2O, and assign the value of -2 to the oxygen atom, the hydrogens must each have an oxidation number of +1 by default, since water is a neutral molecule. As an example, what is the oxidation number of sulfur in sulfur dioxide (SO2)? Given that each oxygen atom has a -2 charge, and knowing that the molecule is neutral, the oxidation number for sulfur must be +4. What about for a sulfate ion (SO4 with a total charge of -2)? Again, the charge of all the oxygen atoms is 4 x -2 = -8. Sulfur must then have an oxidation number of +6, since +6 + (-8) = -2, the total charge on the ion. Since the sulfur in sulfate has a higher oxidation number than in sulfur dioxide, it is said to be more highly oxidized.
Working with redox reactions is fundamentally a bookkeeping issue. You need to be able to account for all of the electrons as they transfer from one species to another. There are a number of rules and tricks for balancing redox reactions, but basically they all boil down to dealing with each of the two half-reactions individually. Consider for example the reaction of aluminum metal to form alumina (Al2O3). The unbalanced reaction is as follows:
Looking at each half reaction separately:
This reaction shows aluminum metal being oxidized to form an aluminum ion with a +3 charge. The half-reaction below shows oxygen being reduced to form two (2) oxygen ions, each with a charge of -2.
If we combine those two (2) half-reactions, we must make the number of electrons equal on both sides. The number 12 is a common multiple of three (3) and four (4), so we multiply the aluminum reaction by four (4) and the oxygen reaction by three (3) to get 12 electrons on both sides. Now, simply combine the reactions. Notice that we have 12 electrons on both sides, which cancel out. The final step is to combine the aluminum and oxygen ions on the right side using a cross multiply technique:
Taking care of the number of atoms, you should end up with:
One of the more useful calculations in redox reactions is the Nernst Equation. This equation allows us to calculate the electric potential of a redox reaction in "non-standard" situations. There exist tables of how much voltage, or potential, a reaction is capable of producing or consuming. These tables, known as standard potential tables, are created by measuring potential at "standard" conditions, with a pressure of 1 bar (≅1 atm), a temperature of 298° K (or 25° C, or room temperature) and with a concentration of 1.0 M for each of the products. This standard potential, or E°, can be corrected by a factor that includes the actual temperature of the reaction, the number of moles of electrons being transferred, and the concentrations of the redox reactants and products. The equation is:
Perhaps the best way of understanding this equation is through an example. Suppose we have this reaction:
In this reaction iron (Fe) is being oxidized to iron(II) ion, while the cadmium ion (Cd2+) in aqueous solution is being reduced to cadmium solid. The question is: how does this reaction behave in "non-standard" conditions?
The first thing to answer is how does it behave in standard conditions? We need to look at the standard potential for each half-reaction, then combine them to get a net potential for the reaction. The two (2) half-reactions are:
Cd2+ (aq) +2 e- ------> Cd (s), E° = -0.40 V
Notice that both half-reactions are shown as reductions -- the species gains electrons, and is changed to a new form. But in the complete reaction above, Fe is oxidized, so the half-reaction needs to be reversed. Quite simply, the potential for the half-reaction of iron is now 0.44 V. To get the potential for the entire reaction, we add up the two (2) half-reactions to get 0.04 V for the standard potential.
The question now is: what is the total potential (in volts) for a nonstandard reaction? Suppose again that we have the same reaction, except now we have 0.0100 M Fe2+ instead of the standard 1.0 M. We need to use the Nernst equation to help us calculate that value. If you go to the Redox Half-Reaction Calculator, you should notice that the reaction is selected and the appropriate values are entered into the boxes. Since we don't have any species "B" or "D", we have entered zero for their concentrations. The concentration of the solid Fe is 1.0 M (actually, concentrations of solids and solvents (liquids) don't enter into the Nernst equation, but we set them to 1.0 so that the mathematics works out). If you click on the "Evaluate" button, you should learn that the standard potential is -0.44 V, while the nonstandard potential is -0.5 V. If you scroll down on the calculator, you can enter 0.5 as the first half-reaction. We again change the sign since we're actually reversing the Fe reaction
Using the calculator again, we calculate the nonstandard potential of the Cd reaction. Suppose we now have a concentration of Cd2+ of 0.005 M, what is its potential? The calculator should return a standard potential of -0.4 V and a nonstandard potential of -0.47 V. Place this value in the box for the second half-reaction, then click on "Evaluate". You should learn that the net nonstandard potential is 0.03 V, slightly less than the value of the net standard potential. Since this value is less than the net standard potential of 0.04 V, there is less of a tendency for this reaction to transfer electrons from reactants to products. In other words, less iron will be oxidized and cadmium will be reduced than at standard conditions.
Test your use of the redox calculator by calculating the net standard potential for this reaction:
Answer: 0.025 V. Since the value is positive, the reaction will work to form the products indicated. Negative values of the potential indicate that the reaction tends to stay as reactants and not form the products. The net standard potential for this reaction is 0.01 V -- since the nonstandard potential is higher, this reaction will form products than the standard reaction.
Free energy and the standard potential can also be related through the following equation:
Where:
ΔG = change in free energy
n = number of moles
n = number of moles
If a reaction is spontaneous, it will have a positive Eo, and negative ΔG, and a large K value (where K is the equilibrium constant-this is discussed more in the kinetics section).
The energy released in any spontaneous redox reaction can be used to perform electrical work using an electrochemical cell (a device where electron transfer is forced to take an external pathway instead of going directly between the reactants. Think of the reaction between zinc and copper. Instead of placing a piece of zinc directly into a solution containing copper, we can form a cell where solid pieces of zinc and copper are placed in two different solutions such as sodium nitrate. The two solids are called electrodes. The anode is the electrode where oxidation occurs and mass is lost where as the cathode is the electrode where reduction occurs and mass is gained. The two electrodes are connected by a circuit and the two (2) solutions are connected by a "salt bridge" which allows ions to pass through. The anions are the negative ions and they move towards the anode. The cations are the positive ions and they move towards the cathode.
The following is a diagram of an electrochemical cell with zinc and copper acting as the electrodes.
An external electric current hooked up to an electrochemical cell will make the electrons go backwards. This process is called electrolysis. This is used, for example, to make something gold plated. You would put the copper in a solution with gold and add a current which causes the gold ions to bond to the copper and therefore coating the copper. The time, current, and electrons needed determine how much "coating" occurs. The key to solving electolysis problems is learning how to convert between the units. Useful information: 1 A=1 C/sec; 96,500 coulombs can produce one (1) mole of e-; the electrons needed is determined by the charge of the ion involved
Example Problem: If you are trying to coat a strip with aluminum and you have a current of 10.0 A (amperes) running for one hour, what mass of Al is formed?
The solution of this problem involves a lengthly unit conversion process:
The redox solution is available.
+++++++++++++++++++++++++++++++++++++++++++++++++++++++++++++++++++++
e- Gold and Copper in Electronics component
+++++++++++++++++++++++++++++++++++++++++++++++++++++++++++++++++++++++
S
Thanks for information.
BalasHapusmetal detector price in india
metal detector price in mumbai
metal detector principle
Thanks for information.
BalasHapusmetal detectors cost
metal detector circuit
metal detector coil
Thank you for such a valuable blog on gold detection methods
BalasHapus