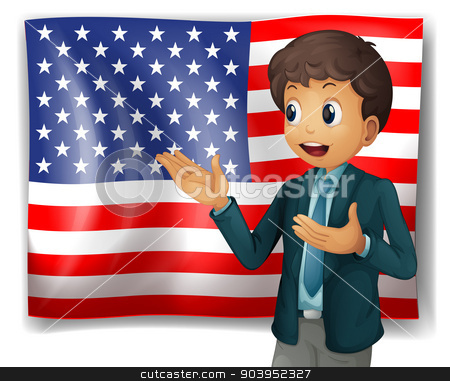
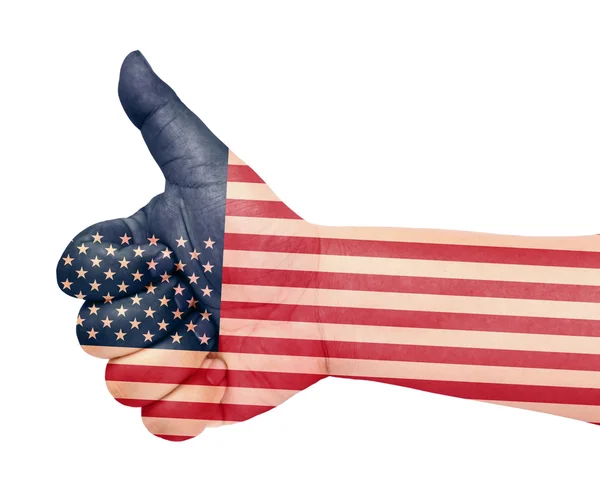
A. XO Classification of Signals
_____________________________________________________________________________________
Signals Surround Us
We're surrounded by signals. Visual, audio, mechanical, electrical; active, passive; physical events which convey information, alert us to the specific conditions, and deliver our energy. With prearranged signals, we know what has happened as soon as evidence of the signal occurs. Other signals carry information within them and need to be decoded and processed in order to learn what they mean. Still, other signals carry power and the only information we get is that our building is still receiving 120V AC.
Signals get us up on time, control traffic; deliver radio, TV, and news. They let us know when our rivers are at flood stage or the force of a gale wind. Even when not activated, as long as we know what is being monitored, we are getting information. When the Check Engine icon is not activated, we know our car's system is working as expected. Other systems may provide a heartbeat signal or a continuously lit LED to show the system is functioning within specs.
Embedded within systems, electrical signals can also initiate actions to ensure our safety and comfort. We're alerted to a possible fire; fire suppressors are activated. Our air conditioner goes on automatically when the temperature rises. A leak in an underground system is detected and made known. We depend on our signals!
Even within this narrow definition there are so many types of signals that classifying them by physical characteristics or other methods helps organize the type of equipment needed, the test procedures and measurement equipment required, as well as address any safety concerns or regulations. Classifying signals helps in analyzing, processing, and validating circuits. Signals can be classified by any of their physical properties, their intended use; and their visual and mathematical properties. The same signal may be classified in more than one way depending on what the system is doing and how the signals are used. The specific field of engineering may emphasize one way to classify one signal versus another. And each field may classify signals differently, adding more detail as they continue their research, like in acoustics, power, or electroencephalographic signals (EEG) signals. Broadcast engineers might work in cabled systems (digitized, compressed, encrypted signals) or over-the-air signals (analog, RF). Within software operating systems, signals can indicate errors, normal interrupts, illegal events, and take direct actions.
Circuit designers and systems engineers work on a variety of systems. The way they classify signals may refer to individual signals or the entire system which handles that type of signal. Many times a mathematical representation of a signal is possible and helps in the analysis. Let's look at some ways signals might be classified.
Direct current (DC) is available from batteries in standard voltages (1.5V DC, 9V DC), generators, or power supplies designed to deliver the specific voltage needed for the circuit or appliance. (24V DC, 48V DC, 120V DC). Except for transient effects, the voltage delivered is constant.
Frequency
Classifying signals by frequency identifies the spectrum and propagation methods. Visual, audio, RF, microwave; wired, fiber optics, air/vacuum/space. AC signals identify frequency. In DC systems with system clocks driving circuitry, terms used may be the clock speed, processor machine instructions per second (MIPS), and pulses per second (PPS).
Voltages
Both AC and DC electrical power systems are classified as low or high voltage. The IEEE defines standards for AC and DC with papers, conferences, labs, and research devoted to each. Definitions are generally given as:
Low VoltageAC :1000 V and below; DC: 3200 V and below
High Voltage: AC: above 1000 V
Ultra High Voltage: 1000kV or Greater AC Systems
High Voltage: AC: above 1000 V
Ultra High Voltage: 1000kV or Greater AC Systems
In digital systems, where logic families dictate voltage requirements, much lower signal levels are used. Transistor logic usually requires 5VDC, while CMOS and low power systems may use higher and lower voltages.
Analog/Digital
Signals within electrical circuits can be classified by the continuity of amplitude values - analog or digital. Analog AC signals like the sine and cosine waveforms have constantly changing values which range from the minimum to the maximum of the signal's amplitude range. There is an amplitude value for each point of time that is proportional to a previous and future value for the waveform.
Digital signals have specific values for amplitude. Digital binary systems have only 2 values, typically operating between 0 and 5V DC; (though in practical circuits a range is accepted). This is a result of the characteristics of the transistor. Either On or Off, conducting or not, two values are presented at the output port.
Continuous/Discrete
The signals may also be classified by time continuity: a continuous signal has values for all values of time without breaks or areas where the signal doesn't exist. Sine and cosine waveforms are continuous, where the tangent waveform has discontinuities where values don't exist.
Discrete signals have values at only specific times. A sampling circuit yields signal values only for times the sampling takes place.
Figures 2 and 3 show discrete and continuous signals.


Figure 2. Discrete Signals: Time and Amplitude

Figure 3. Continuous signal for both time and amplitude values
Waveform characteristics - Periodic/Aperiodic
Signals may be classified according to the visual nature of the waveform. Periodic signals repeat within a given time period. Mathematically represented by the equation:
s(t) = s(t + T) where T is the period (1/frequency).
Periodic signals exist in both AC (analog) and DC (digital) systems, like the sine wave or digital system clock signal. Figure 4 shows some periodic signals. Aperiodic signals do not repeat. Some mathematical tools are only available for periodic signals. The Fourier series was developed for use for periodic signals. To be used on aperiodic signals, the signal was treated as a periodic signal with an infinite period. This allowed Fourier transforms to be used for all signals.


Figure 4. Digital and Analog Periodic Signals
Waveform Characteristics - Even/Odd
Even signals are symmetrical about the y-axis. Mathematically, f(x) = f(-x). A point(X,Y) would have the same value of a point at (-X,Y). The Fourier series decomposes a signal into a sum of sines and cosines:
FS = A0 + ∑ An sin(n) + ∑ Bn cosine(n);
Where A0 is the DC component and each term has an associated amplitude and trigonometric component (sine and cosine).
Even signals result when only cosine components compose the signal. The cosine itself is an even signal and symmetric about the y-axis. Figure 5 shows an even signal and the cosine waveform.
Odd signals are symmetrical about the origin. Mathematically, f(t) = -(f(-t)). Fourier series of odd signals only have sine components. The sine itself is an odd signal and symmetric about the origin, as shown in Figure 6. A signal can be decomposed into even and odd signals.

Figure 5. Even Signals; symmetrical about the y-axis

Figure 6. Odd Signals; symmetrical about the Origin
Deterministic/Random
If you're familiar with modeling and analysis programs, you've worked with signals that are classified as deterministic or random. Deterministic signals can be predicted by past behavior and totally captured by mathematical equations. All possible outcomes are known and there are no risk factors. Deterministic signals are useful in communications where knowing the exact values of a carrier signal is important for modulation techniques.
Random signals are not predictable and are represented by probabilistic functions, familiar from probability theory, like the Poisson function. Circuit noise is usually modeled as, and is, a random signal.
Somewhat similar are causal signals. Though it's tempting to look at causal waveform graphs and think they have to do with timing, the causality is a result of how the system was modeled. Causal signals are only determined from past or present conditions as inputs. When the system starts at t=0, the following data are computed from the initial conditions and then generated from previous results. The system can continue to infinity. Control systems illustrate this behavior.
Anti-causal systems generate results from future events as well and stop at t=0. Not represented in real life, anti-causal signals allow scenarios where possible future events can be analyzed. Non-causal signal waveforms have value and results for any time t < 0 and t > 0.
Encoding
Sensor signal output can be classified by the type of data encoding used. Sensors usually measure physical quantities; analog data like temperature, pressure, etc. Depending on the sensor, the analog-to-digital conversion can be handled within the unit and results are provided in digital form: binary, octal, hexadecimal, binary-coded-decimal (BCD), and gray code output.
Synchronous/Asynchronous
Digital systems have signals that are divided into control or data signals. Control signals may be classified as synchronous or asynchronous. Repetitive periodic clock signals drive the timing for the logic and processing functions. When the logic levels all change state based on the timing of the clock, the signals are synchronous, synced to the clock. Logic levels at the inputs of components only take effect with the timing of the clock signal.
Asynchronous signals have output logic states changing anytime, regardless of the clock cycle. Reset signals can be received anytime and cause output levels to go to predetermined states regardless of the clock timing. Asynchronous signals can also provide handshaking and other protocols to accommodate slower or external peripherals.
Summary
Signals are in involved in all aspects of electrical engineering. Classifying signals act as a shorthand in designing, discussing, conveying results, and analysis. There are many ways to classify a signal, depending on the area of interest, field of study, and mathematical representations.
B. XO Analog and Digital Signals
_____________________________________________________________________
Instrumentation is a field of study and work centering on measurement and control of physical processes. These physical processes include pressure, temperature, flow rate, and chemical consistency. An instrument is a device that measures and/or acts to control any kind of physical process. Due to the fact that electrical quantities of voltage and current are easy to measure, manipulate, and transmit over long distances, they are widely used to represent such physical variables and transmit the information to remote locations.
A signal is any kind of physical quantity that conveys information. Audible speech is certainly a kind of signal, as it conveys the thoughts (information) of one person to another through the physical medium of sound. Hand gestures are signals, too, conveying information by means of light. This text is another kind of signal, interpreted by your English-trained mind as information about electric circuits. In this chapter, the word signal will be used primarily in reference to an electrical quantity of voltage or current that is used to represent or signify some other physical quantity.
An analog signal is a kind of signal that is continuously variable, as opposed to having a limited number of steps along its range (called digital). A well-known example of analog vs. digital is that of clocks: analog being the type with pointers that slowly rotate around a circular scale, and digital being the type with decimal number displays or a “second-hand” that jerks rather than smoothly rotates. The analog clock has no physical limit to how finely it can display the time, as its “hands” move in a smooth, pauseless fashion. The digital clock, on the other hand, cannot convey any unit of time smaller than what its display will allow for. The type of clock with a “second-hand” that jerks in 1-second intervals is a digital device with a minimum resolution of one second.
Both analog and digital signals find application in modern electronics, and the distinctions between these two basic forms of information is something to be covered in much greater detail later in this book. For now, I will limit the scope of this discussion to analog signals, since the systems using them tend to be of simpler design.
With many physical quantities, especially electrical, analog variability is easy to come by. If such a physical quantity is used as a signal medium, it will be able to represent variations of information with almost unlimited resolution.
In the early days of industrial instrumentation, compressed air was used as a signaling medium to convey information from measuring instruments to indicating and controlling devices located remotely. The amount of air pressure corresponded to the magnitude of whatever variable was being measured. Clean, dry air at approximately 20 pounds per square inch (PSI) was supplied from an air compressor through tubing to the measuring instrument and was then regulated by that instrument according to the quantity being measured to produce a corresponding output signal. For example, a pneumatic (air signal) level “transmitter” device set up to measure height of water (the “process variable”) in a storage tank would output a low air pressure when the tank was empty, a medium pressure when the tank was partially full, and a high pressure when the tank was completely full.

The “water level indicator” (LI) is nothing more than a pressure gauge measuring the air pressure in the pneumatic signal line. This air pressure, being a signal, is in turn a representation of the water level in the tank. Any variation of level in the tank can be represented by an appropriate variation in the pressure of the pneumatic signal. Aside from certain practical limits imposed by the mechanics of air pressure devices, this pneumatic signal is infinitely variable, able to represent any degree of change in the water’s level, and is therefore analog in the truest sense of the word.
Crude as it may appear, this kind of pneumatic signaling system formed the backbone of many industrial measurement and control systems around the world, and still sees use today due to its simplicity, safety, and reliability. Air pressure signals are easily transmitted through inexpensive tubes, easily measured (with mechanical pressure gauges), and are easily manipulated by mechanical devices using bellows, diaphragms, valves, and other pneumatic devices. Air pressure signals are not only useful for measuring physical processes, but for controlling them as well. With a large enough piston or diaphragm, a small air pressure signal can be used to generate a large mechanical force, which can be used to move a valve or other controlling device. Complete automatic control systems have been made using air pressure as the signal medium. They are simple, reliable, and relatively easy to understand. However, the practical limits for air pressure signal accuracy can be too limiting in some cases, especially when the compressed air is not clean and dry, and when the possibility for tubing leaks exist.
With the advent of solid-state electronic amplifiers and other technological advances, electrical quantities of voltage and current became practical for use as analog instrument signaling media. Instead of using pneumatic pressure signals to relay information about the fullness of a water storage tank, electrical signals could relay that same information over thin wires (instead of tubing) and not require the support of such expensive equipment as air compressors to operate:

Analog electronic signals are still the primary kinds of signals used in the instrumentation world today (January of 2001), but it is giving way to digital modes of communication in many applications (more on that subject later). Despite changes in technology, it is always good to have a thorough understanding of fundamental principles, so the following information will never really become obsolete.
One important concept applied in many analog instrumentation signal systems is that of “live zero,” a standard way of scaling a signal so that an indication of 0 percent can be discriminated from the status of a “dead” system. Take the pneumatic signal system as an example: if the signal pressure range for transmitter and indicator was designed to be 0 to 12 PSI, with 0 PSI representing 0 percent of process measurement and 12 PSI representing 100 percent, a received signal of 0 percent could be a legitimate reading of 0 percent measurement or it could mean that the system was malfunctioning (air compressor stopped, tubing broken, transmitter malfunctioning, etc.). With the 0 percent point represented by 0 PSI, there would be no easy way to distinguish one from the other.
If, however, we were to scale the instruments (transmitter and indicator) to use a scale of 3 to 15 PSI, with 3 PSI representing 0 percent and 15 PSI representing 100 percent, any kind of a malfunction resulting in zero air pressure at the indicator would generate a reading of -25 percent (0 PSI), which is clearly a faulty value. The person looking at the indicator would then be able to immediately tell that something was wrong.
Not all signal standards have been set up with live zero baselines, but the more robust signals standards (3-15 PSI, 4-20 mA) have, and for good reason.
- REVIEW:
- A signal is any kind of detectable quantity used to communicate information.
- An analog signal is a signal that can be continuously, or infinitely, varied to represent any small amount of change.
- Pneumatic, or air pressure, signals used to be used predominately in industrial instrumentation signal systems. This has been largely superseded by analog electrical signals such as voltage and current.
- A live zero refers to an analog signal scale using a non-zero quantity to represent 0 percent of real-world measurement, so that any system malfunction resulting in a natural “rest” state of zero signal pressure, voltage, or current can be immediately recognized.
C. XO Electronic Testing Equipment and Their Types
______________________________________________________________________
The testing equipment used to detect faults in the operation of electronic devices by creating stimulus signals and capture responses from electronic devices under test is known as electronic test equipment. If any faults are detected, then identified faults can be traced an rectified using electronic testing equipment. Most often all electrical and electronic circuits are tested and troubleshooted to detect faults or abnormal functioning if any.
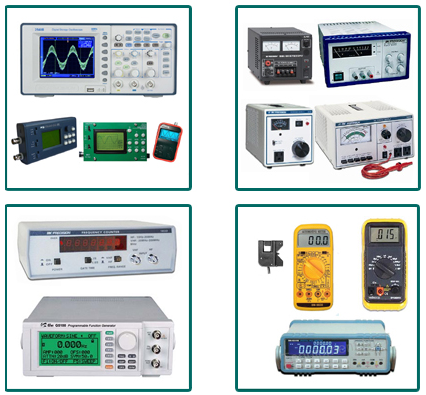
Therefore, testing equipment is necessary to find and analyze the circuit conditions, for checking electronic test equipment and maintenance in various industries. Many industries utilize different types of electronic test equipment ranging from the very simple and inexpensive to complex and sophisticated ones.
Types of Electronic Testing Equipments
The Basic Electronics Testing Equipments Under this Category Include the Following
Voltmeter
A basic electronics device or instrument used to measure voltage or electrical potential difference between two points in electrical circuits is known as voltmeter. There are two types of voltmeters: analog and digital. An analog voltmeter moves a pointer across a scale in proportional to the voltage of the electrical circuit. A digital voltmeter measures an unknown input voltage by converting the voltage to a digital value by using a converter and then displays the voltage in numeric form.
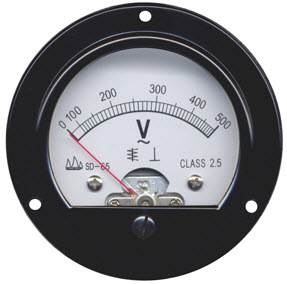
Ohmmeter
An electrical instrument that measures electrical resistance is known as an ohmmeter. The instrument used to measure small value of resistance are micro-ohmmeters. Similarly meg-ohmmeters is used to make large resistance measurements. Resistance values are measured in ohms (Ω). Originally, ohmmeter is designed with a small battery to apply a voltage to a resistance.
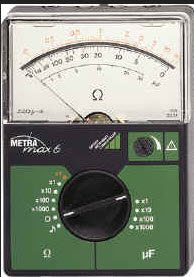
It uses a galvanometer to measure the electric current through the resistance. The scale of the galvanometer was marked in ohms (Ω), because the fixed voltage from the battery assures that the resistance decreases and the current through the meter increases.
Ammeter
A measuring instrument which is used to measure the electric current in a circuit is known as an ammeter. The units of measurement for electric current is amperes (A) Earlier ammeters were laboratory instruments which depend on the earth’s magnetic field for operation. In an era of the 19th century, improved instruments were designed which could be placed in any position and allows accurate measurements in electric power systems.
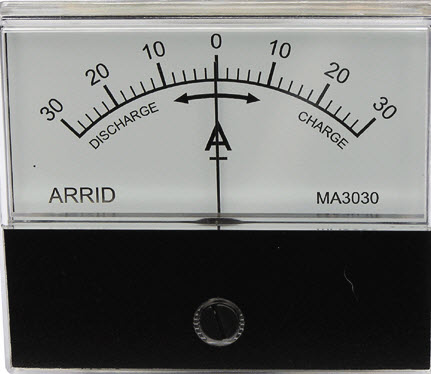
The smaller currents can be measured by using milliammeters or micro ammeters, units of measuring the smaller current are in the milliampere or micro-ampere range. There are different types of ammeters such as moving-coil, moving magnet and moving-iron, etc.
Multimeter
A multimeter is an electronic instrument used to measure the three basic electrical characteristics: voltage, current and resistance. It has multiple functions and acts like ohmmeter, voltmeter and ammeter and also used for household wiring, electric motors, testing batteries and power supplies. The multimeter is a handheld device with a needle over a numeric LCD digital display for indication purpose. It is also used to test continuity between two points in an electrical circuit. There are three types of multimeters made available in the market such as: digital multimeter, analog multimeter and fluke multimeter.
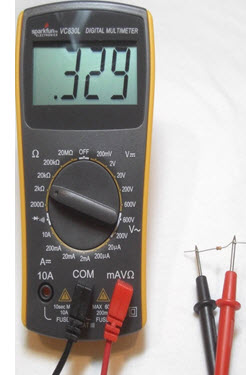
The Following are used for Testing Stimulus Signals of the Circuit Under Test
Power Supplies
A power supply is an electronic instrument that supplies electric energy to an electric load. Regulated power supplies refers to a power supply which supplies a variety of output voltages used for bench testing of electronic circuits, with the variation of output voltages or some preset voltages. Almost all the electronic circuits make use of a DC source of power for operation. A regulated power supply consists of various blocks such as an ordinary power supply and a voltage regulating device. The output generated from ordinary power supply is fed to the voltage regulating device that provides the final output. The main function of a power supply is to convert one form of electrical energy into another.
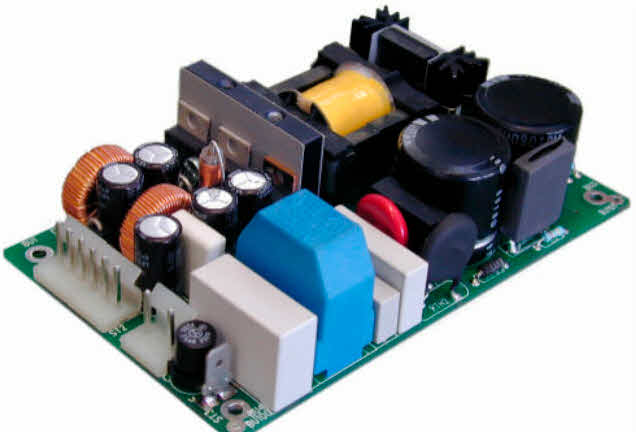
Signal Generator
A signal generator is also named as pitch generator, function generator or frequency generator is an electronic device used for generating electronic signals either in the analog or digital domains (repeating or non-repeating signals). Signal generators are used in testing, designing and repairing electro acoustic or electronic devices.
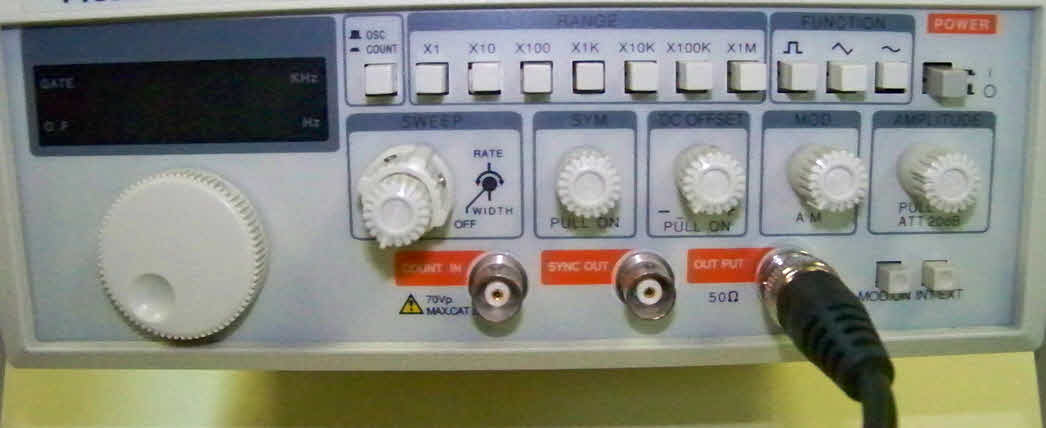
In general no electronic device is suitable for all applications. There are various types of signal generators with different applications and purposes. During the development in technology, compared to signal generators there are flexible and programmable software tone generators with embedded hardware units are made available in the market.
Pulse Generator
A pulse generator is either an electronic circuit or a piece of electronic test equipment used to generate electrical pulses in different shapes: mostly used for tests at analog or electrical level. Pulse generators are used to control the width, frequency,delay based on the low and high voltage levels of the pulses and with respect to an internal and external triggering. There are three types of pulse generators namely optical pulse generator, bench pulse generators and microwave pulsers.
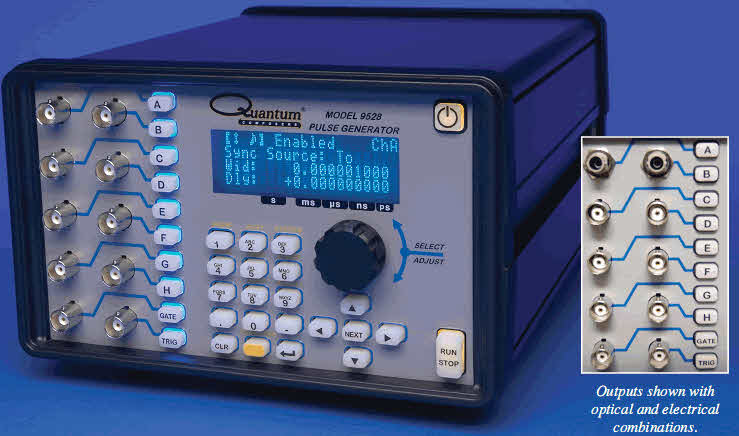
Digital Pattern Generator
A digital generator is an electronic testing equipment or software used to generate digital electronics stimuli. Digital electronics stimuli are a specific type of electrical waveform varying between two conventional voltages corresponding to two logic gates (either 1 or 0, low or high). The function of the digital pattern generator is to stimulate the inputs of a electronic device. For that purpose, the voltage levels are generated by a digital pattern generator are compared to I/O standards of digital electronics: TTL, LVTTL and LVDS. It is also known as a logic source because it is a source of synchronous digital stimulus.
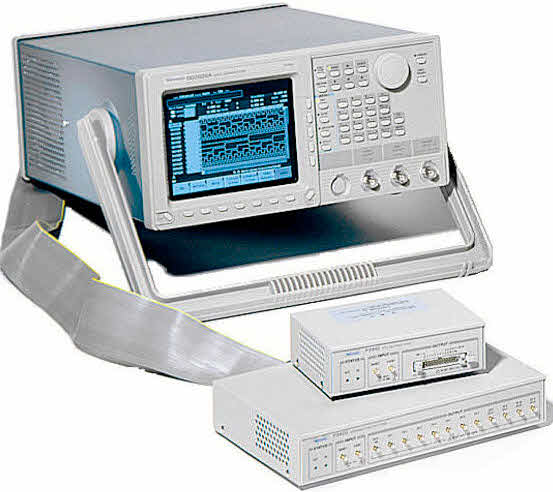
It generates a signal for testing digital electronics at logic level. This generator also produces a single shot or repetitive signals in which some sort of triggering source takes place ( internally or externally)
The Following Equipments Analyze the Response of the Circuit Under Test
Oscilloscope
The oscilloscope is an electronic test instrument that constantly obverses varying voltage signals as a two dimensional plot of one or more signals as a function of time. The other names for oscilloscope are oscillograph, cathode ray oscilloscope or digital storage oscilloscope. It is also used for converting non electrical signals such as vibration or sound into voltages and then displays the result.
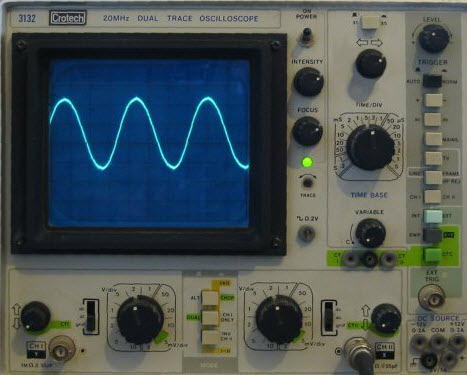
Oscilloscopes are used to observe the change of an electrical signal based on time such that voltage and time describe a shape of the signals and graphed continuously compared with a calibrated scale.The obtained waveforms can be considered for following properties such as frequency, amplitude, time interval, rise time and others. Modern digital instruments may calculate these properties directly and displays them.
Frequency counter
Digital frequency counter is an electrical test equipment used for measuring the frequency of repetitive signals and elapsed time between events. Digital frequency counters are also used to measure the radio frequency where it is important to measure the precise frequency of a particular signal.
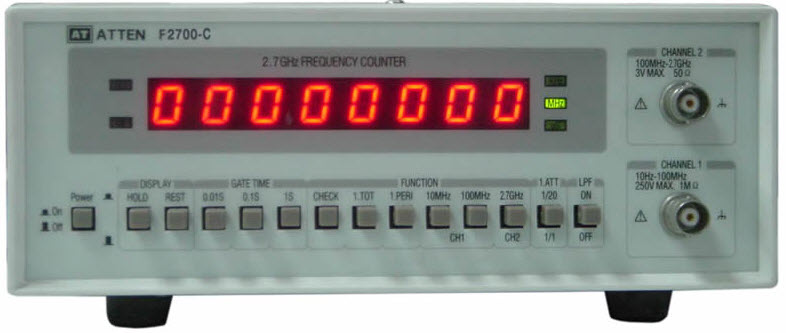
There is a slight difference between the timers and frequency counters in the electronic industry. It is often possible to use both timers and frequency counters to perform the both functions: to measure the time and frequency. Frequency counters are mostly used as general purpose laboratory test equipment to measure higher frequencies.
Advanced or Less Commonly used Testing Equipment
LCR Meter
LCR Meter name itself indicates that it is used to measure the inductance, capacitance and resistance of electronics components. The inductance, capacitance and resistance are denoted by the letters L, C, and R so it is named as LCR Meter. A variety of meters are made available in the market, but simple versions of LCR meters indicates impedance only for converting the values to capacitance or inductance.
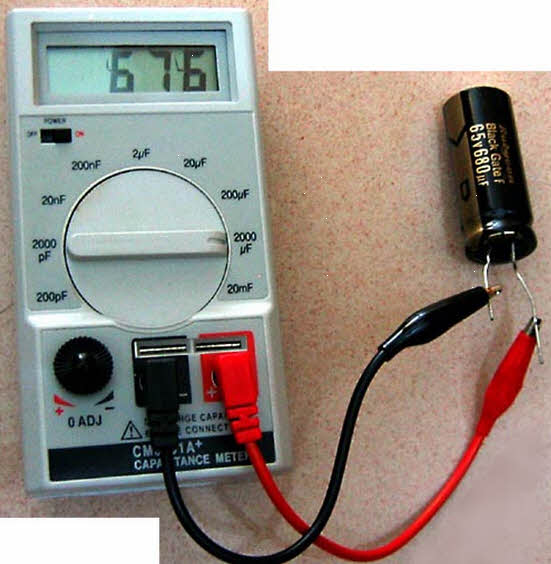
More designs are available and used to measure the capacitance or inductance, and also the equivalent series resistance of capacitors and the Q factor of inductive components. These conditions make the LCR meters valuable for measuring the quality and overall performance of the component.
C. XO Electronic Systems
________________________________________________
An Electronic System is a physical interconnection of components, or parts, that gathers various amounts of information together .
It does this with the aid of input devices such as sensors, that respond in some way to this information and then uses electrical energy in the form of an output action to control a physical process or perform some type of mathematical operation on the signal.
But electronic control systems can also be regarded as a process that transforms one signal into another so as to give the desired system response. Then we can say that a simple electronic system consists of an input, a process, and an output with the input variable to the system and the output variable from the system both being signals.
There are many ways to represent a system, for example: mathematically, descriptively, pictorially or schematically. Electronic systems are generally represented schematically as a series of interconnected blocks and signals with each block having its own set of inputs and outputs.
As a result, even the most complex of electronic control systems can be represented by a combination of simple blocks, with each block containing or representing an individual component or complete sub-system. The representing of an electronic system or process control system as a number of interconnected blocks or boxes is known commonly as “block-diagram representation”.
Block Diagram Representation of a Simple Electronic System

Electronic Systems have both Inputs and Outputs with the output or outputs being produced by processing the inputs. Also, the input signal(s) may cause the process to change or may itself cause the operation of the system to change. Therefore the input(s) to a system is the “cause” of the change, while the resulting action that occurs on the systems output due to this cause being present is called the “effect”, with the effect being a consequence of the cause.
In other words, an electronic system can be classed as “causal” in nature as there is a direct relationship between its input and its output. Electronic systems analysis and process control theory are generally based upon this Cause and Effect analysis.
So for example in an audio system, a microphone (input device) causes sound waves to be converted into electrical signals for the amplifier to amplify (a process), and a loudspeaker (output device) produces sound waves as an effect of being driven by the amplifiers electrical signals.
But an electronic system need not be a simple or single operation. It can also be an interconnection of several sub-systems all working together within the same overall system.
Our audio system could for example, involve the connection of a CD player, or a DVD player, an MP3 player, or a radio receiver all being multiple inputs to the same amplifier which in turn drives one or more sets of stereo or home theatre type surround loudspeakers.
But an electronic system can not just be a collection of inputs and outputs, it must “do something”, even if it is just to monitor a switch or to turn “ON” a light. We know that sensors are input devices that detect or turn real world measurements into electronic signals which can then be processed. These electrical signals can be in the form of either voltages or currents within a circuit. The opposite or output device is called an actuator, that converts the processed signal into some operation or action, usually in the form of mechanical movement.
Types of Electronic System
Electronic systems operate on either continuous-time (CT) signals or discrete-time (DT) signals. A continuous-time system is one in which the input signals are defined along a continuum of time, such as an analogue signal which “continues” over time producing a continuous-time signal.
But a continuous-time signal can also vary in magnitude or be periodic in nature with a time period T. As a result, continuous-time electronic systems tend to be purely analogue systems producing a linear operation with both their input and output signals referenced over a set period of time.

For example, the temperature of a room can be classed as a continuous time signal which can be measured between two values or set points, for example from cold to hot or from Monday to Friday. We can represent a continuous-time signal by using the independent variable for time t, and where x(t) represents the input signal and y(t) represents the output signal over a period of time t.
Generally, most of the signals present in the physical world which we can use tend to be continuous-time signals. For example, voltage, current, temperature, pressure, velocity, etc.
On the other hand, a discrete-time system is one in which the input signals are not continuous but a sequence or a series of signal values defined in “discrete” points of time. This results in a discrete-time output generally represented as a sequence of values or numbers.
Generally a discrete signal is specified only at discrete intervals, values or equally spaced points in time. So for example, the temperature of a room measured at 1pm, at 2pm, at 3pm and again at 4pm without regards for the actual room temperature in between these points at say, 1:30pm or at 2:45pm.

However, a continuous-time signal, x(t) can be represented as a discrete set of signals only at discrete intervals or “moments in time”. Discrete signals are not measured versus time, but instead are plotted at discrete time intervals, where n is the sampling interval. As a result discrete-time signals are usually denoted as x(n) representing the input and y(n) representing the output.
Then we can represent the input and output signals of a system as x and y respectively with the signal, or signals themselves being represented by the variable, t, which usually represents time for a continuous system and the variable n, which represents an integervalue for a discrete system as shown.
Continuous-time and Discrete-time System

Interconnection of Systems
One of the practical aspects of electronic systems and block-diagram representation is that they can be combined together in either a series or parallel combinations to form much bigger systems. Many larger real systems are built using the interconnection of several sub-systems and by using block diagrams to represent each subsystem, we can build a graphical representation of the whole system being analysed.
When subsystems are combined to form a series circuit, the overall output at y(t) will be equivalent to the multiplication of the input signal x(t) as shown as the subsystems are cascaded together.
Series Connected System

For a series connected continuous-time system, the output signal y(t) of the first subsystem, “A” becomes the input signal of the second subsystem, “B” whose output becomes the input of the third subsystem, “C” and so on through the series chain giving A x B x C, etc.
Then the original input signal is cascaded through a series connected system, so for two series connected subsystems, the equivalent single output will be equal to the multiplication of the systems, ie, y(t) = G1(s) x G2(s). Where G represents the transfer function of the subsystem.
Note that the term “Transfer Function” of a system refers to and is defined as being the mathematical relationship between the systems input and its output, or output/input and hence describes the behaviour of the system.
Also, for a series connected system, the order in which a series operation is performed does not matter with regards to the input and output signals as: G1(s) x G2(s) is the same as G2(s) x G1(s). An example of a simple series connected circuit could be a single microphone feeding an amplifier followed by a speaker.
Parallel Connected Electronic System

For a parallel connected continuous-time system, each subsystem receives the same input signal, and their individual outputs are summed together to produce an overall output, y(t). Then for two parallel connected subsystems, the equivalent single output will be the sum of the two individual inputs, ie, y(t) = G1(s) + G2(s).
An example of a simple parallel connected circuit could be several microphones feeding into a mixing desk which in turn feeds an amplifier and speaker system.
Electronic Feedback Systems
Another important interconnection of systems which is used extensively in control systems, is the “feedback configuration”. In feedback systems, a fraction of the output signal is “fed back” and either added to or subtracted from the original input signal. The result is that the output of the system is continually altering or updating its input with the purpose of modifying the response of a system to improve stability. A feedback system is also commonly referred to as a “Closed-loop System” as shown.
Closed-Loop Feedback System

Feedback systems are used a lot in most practical electronic system designs to help stabilise the system and to increase its control. If the feedback loop reduces the value of the original signal, the feedback loop is known as “negative feedback”. If the feedback loop adds to the value of the original signal, the feedback loop is known as “positive feedback”.
An example of a simple feedback system could be a thermostatically controlled heating system in the home. If the home is too hot, the feedback loop will switch “OFF” the heating system to make it cooler. If the home is too cold, the feedback loop will switch “ON” the heating system to make it warmer. In this instance, the system comprises of the heating system, the air temperature and the thermostatically controlled feedback loop.
Transfer Function of Systems

Any subsystem can be represented as a simple block with an input and output as shown. Generally, the input is designated as: θi and the output as: θo. The ratio of output over input represents the gain, ( G ) of the subsystem and is therefore defined as: G = θo/θi
In this case, G represents the Transfer Function of the system or subsystem. When discussing electronic systems in terms of their transfer function, the complex operator, s is used, then the equation for the gain is rewritten as: G(s) = θo(s)/θi(s)
Electronic System Summary
We have seen that a simple Electronic System consists of an input, a process, an output and possibly feedback. Electronic systems can be represented using interconnected block diagrams where the lines between each block or subsystem represents both the flow and direction of a signal through the system.
Block diagrams need not represent a simple single system but can represent very complex systems made from many interconnected subsystems. These subsystems can be connected together in series, parallel or combinations of both depending upon the flow of the signals.
We have also seen that electronic signals and systems can be of continuous-time or discrete-time in nature and may be analogue, digital or both. Feedback loops can be used be used to increase or reduce the performance of a particular system by providing better stability and control. Control is the process of making a system variable adhere to a particular value, called the reference value.
D. XO Sensors and Transducers
______________________________________________________________________

Simple stand alone electronic circuits can be made to repeatedly flash a light or play a musical note.
But in order for an electronic circuit or system to perform any useful task or function it needs to be able to communicate with the “real world” whether this is by reading an input signal from an “ON/OFF” switch or by activating some form of output device to illuminate a single light.
In other words, an Electronic System or circuit must be able or capable to “do” something and Sensors and Transducers are the perfect components for doing this.
The word “Transducer” is the collective term used for both Sensors which can be used to sense a wide range of different energy forms such as movement, electrical signals, radiant energy, thermal or magnetic energy etc, and Actuators which can be used to switch voltages or currents.
There are many different types of sensors and transducers, both analogue and digital and input and output available to choose from. The type of input or output transducer being used, really depends upon the type of signal or process being “Sensed” or “Controlled” but we can define a sensor and transducers as devices that converts one physical quantity into another.
Devices which perform an “Input” function are commonly called Sensors because they “sense” a physical change in some characteristic that changes in response to some excitation, for example heat or force and covert that into an electrical signal. Devices which perform an “Output” function are generally called Actuators and are used to control some external device, for example movement or sound.
Electrical Transducers are used to convert energy of one kind into energy of another kind, so for example, a microphone (input device) converts sound waves into electrical signals for the amplifier to amplify (a process), and a loudspeaker (output device) converts these electrical signals back into sound waves and an example of this type of simple Input/Output (I/O) system is given below.
Simple Input/Output System using Sound Transducers

There are many different types of sensors and transducers available in the marketplace, and the choice of which one to use really depends upon the quantity being measured or controlled, with the more common types given in the table below:
Common Sensors and Transducers
Quantity being Measured | Input Device (Sensor) | Output Device (Actuator) |
Light Level | Light Dependant Resistor (LDR) Photodiode Photo-transistor Solar Cell | Lights & Lamps LED’s & Displays Fibre Optics |
Temperature | Thermocouple Thermistor Thermostat Resistive Temperature Detectors | Heater Fan |
Force/Pressure | Strain Gauge Pressure Switch Load Cells | Lifts & Jacks Electromagnet Vibration |
Position | Potentiometer Encoders Reflective/Slotted Opto-switch LVDT | Motor Solenoid Panel Meters |
Speed | Tacho-generator Reflective/Slotted Opto-coupler Doppler Effect Sensors | AC and DC Motors Stepper Motor Brake |
Sound | Carbon Microphone Piezo-electric Crystal | Bell Buzzer Loudspeaker |
Input type transducers or sensors, produce a voltage or signal output response which is proportional to the change in the quantity that they are measuring (the stimulus). The type or amount of the output signal depends upon the type of sensor being used. But generally, all types of sensors can be classed as two kinds, either Passive Sensors or Active Sensors.
Generally, active sensors require an external power supply to operate, called an excitation signal which is used by the sensor to produce the output signal. Active sensors are self-generating devices because their own properties change in response to an external effect producing for example, an output voltage of 1 to 10v DC or an output current such as 4 to 20mA DC. Active sensors can also produce signal amplification.
A good example of an active sensor is an LVDT sensor or a strain gauge. Strain gauges are pressure-sensitive resistive bridge networks that are external biased (excitation signal) in such a way as to produce an output voltage in proportion to the amount of force and/or strain being applied to the sensor.
Unlike an active sensor, a passive sensor does not need any additional power source or excitation voltage. Instead a passive sensor generates an output signal in response to some external stimulus. For example, a thermocouple which generates its own voltage output when exposed to heat. Then passive sensors are direct sensors which change their physical properties, such as resistance, capacitance or inductance etc.
But as well as analogue sensors, Digital Sensors produce a discrete output representing a binary number or digit such as a logic level “0” or a logic level “1”.
Analogue and Digital Sensors
Analogue Sensors
Analogue Sensors produce a continuous output signal or voltage which is generally proportional to the quantity being measured. Physical quantities such as Temperature, Speed, Pressure, Displacement, Strain etc are all analogue quantities as they tend to be continuous in nature. For example, the temperature of a liquid can be measured using a thermometer or thermocouple which continuously responds to temperature changes as the liquid is heated up or cooled down.
Thermocouple used to produce an Analogue Signal

Analogue sensors tend to produce output signals that are changing smoothly and continuously over time. These signals tend to be very small in value from a few mico-volts (uV) to several milli-volts (mV), so some form of amplification is required.
Then circuits which measure analogue signals usually have a slow response and/or low accuracy. Also analogue signals can be easily converted into digital type signals for use in micro-controller systems by the use of analogue-to-digital converters, or ADC’s.
Digital Sensors
As its name implies, Digital Sensors produce a discrete digital output signals or voltages that are a digital representation of the quantity being measured. Digital sensors produce a Binary output signal in the form of a logic “1” or a logic “0”, (“ON” or “OFF”). This means then that a digital signal only produces discrete (non-continuous) values which may be outputted as a single “bit”, (serial transmission) or by combining the bits to produce a single “byte” output (parallel transmission).
Light Sensor used to produce an Digital Signal

In our simple example above, the speed of the rotating shaft is measured by using a digital LED/Opto-detector sensor. The disc which is fixed to a rotating shaft (for example, from a motor or robot wheels), has a number of transparent slots within its design. As the disc rotates with the speed of the shaft, each slot passes by the sensor in turn producing an output pulse representing a logic “1” or logic “0” level.
These pulses are sent to a register of counter and finally to an output display to show the speed or revolutions of the shaft. By increasing the number of slots or “windows” within the disc more output pulses can be produced for each revolution of the shaft. The advantage of this is that a greater resolution and accuracy is achieved as fractions of a revolution can be detected. Then this type of sensor arrangement could also be used for positional control with one of the discs slots representing a reference position.
Compared to analogue signals, digital signals or quantities have very high accuracies and can be both measured and “sampled” at a very high clock speed. The accuracy of the digital signal is proportional to the number of bits used to represent the measured quantity. For example, using a processor of 8 bits, will produce an accuracy of 0.390% (1 part in 256). While using a processor of 16 bits gives an accuracy of 0.0015%, (1 part in 65,536) or 260 times more accurate. This accuracy can be maintained as digital quantities are manipulated and processed very rapidly, millions of times faster than analogue signals.
In most cases, sensors and more specifically analogue sensors generally require an external power supply and some form of additional amplification or filtering of the signal in order to produce a suitable electrical signal which is capable of being measured or used. One very good way of achieving both amplification and filtering within a single circuit is to use Operational Amplifiers as seen before.
Signal Conditioning of Sensors
As we saw in the Operational Amplifier tutorial, op-amps can be used to provide amplification of signals when connected in either inverting or non-inverting configurations.
The very small analogue signal voltages produced by a sensor such as a few milli-volts or even pico-volts can be amplified many times over by a simple op-amp circuit to produce a much larger voltage signal of say 5v or 5mA that can then be used as an input signal to a microprocessor or analogue-to-digital based system.
Therefore, to provide any useful signal a sensors output signal has to be amplified with an amplifier that has a voltage gain up to 10,000 and a current gain up to 1,000,000 with the amplification of the signal being linear with the output signal being an exact reproduction of the input, just changed in amplitude.
Then amplification is part of signal conditioning. So when using analogue sensors, generally some form of amplification (Gain), impedance matching, isolation between the input and output or perhaps filtering (frequency selection) may be required before the signal can be used and this is conveniently performed by Operational Amplifiers.
Also, when measuring very small physical changes the output signal of a sensor can become “contaminated” with unwanted signals or voltages that prevent the actual signal required from being measured correctly. These unwanted signals are called “Noise“. This Noise or Interference can be either greatly reduced or even eliminated by using signal conditioning or filtering techniques as we discussed in the Active Filter tutorial.
By using either a Low Pass, or a High Pass or even Band Pass filter the “bandwidth” of the noise can be reduced to leave just the output signal required. For example, many types of inputs from switches, keyboards or manual controls are not capable of changing state rapidly and so low-pass filter can be used. When the interference is at a particular frequency, for example mains frequency, narrow band reject or Notch filters can be used to produce frequency selective filters.
Typical Op-amp Filters

Were some random noise still remains after filtering it may be necessary to take several samples and then average them to give the final value so increasing the signal-to-noise ratio. Either way, both amplification and filtering play an important role in interfacing both sensors and transducers to microprocessor and electronics based systems in “real world” conditions.
As their name implies, Position Sensors detect the position of something which means that they are referenced either to or from some fixed point or position. These types of sensors provide a “positional” feedback.
One method of determining a position, is to use either “distance”, which could be the distance between two points such as the distance travelled or moved away from some fixed point, or by “rotation” (angular movement). For example, the rotation of a robots wheel to determine its distance travelled along the ground. Either way, Position Sensorscan detect the movement of an object in a straight line using Linear Sensors or by its angular movement using Rotational Sensors.
The Potentiometer
The most commonly used of all the “Position Sensors”, is the potentiometer because it is an inexpensive and easy to use position sensor. It has a wiper contact linked to a mechanical shaft that can be either angular (rotational) or linear (slider type) in its movement, and which causes the resistance value between the wiper/slider and the two end connections to change giving an electrical signal output that has a proportional relationship between the actual wiper position on the resistive track and its resistance value. In other words, resistance is proportional to position.

Potentiometer
Potentiometers come in a wide range of designs and sizes such as the commonly available round rotational type or the longer and flat linear slider types. When used as a position sensor the moveable object is connected directly to the rotational shaft or slider of the potentiometer.
A DC reference voltage is applied across the two outer fixed connections forming the resistive element. The output voltage signal is taken from the wiper terminal of the sliding contact as shown below.
This configuration produces a potential or voltage divider type circuit output which is proportional to the shaft position. Then for example, if you apply a voltage of say 10v across the resistive element of the potentiometer the maximum output voltage would be equal to the supply voltage at 10 volts, with the minimum output voltage equal to 0 volts. Then the potentiometer wiper will vary the output signal from 0 to 10 volts, with 5 volts indicating that the wiper or slider is at its half-way or centre position.
Potentiometer Construction

The output signal (Vout) from the potentiometer is taken from the centre wiper connection as it moves along the resistive track, and is proportional to the angular position of the shaft.
Example of a simple Positional Sensing Circuit

While resistive potentiometer position sensors have many advantages: low cost, low tech, easy to use etc, as a position sensor they also have many disadvantages: wear due to moving parts, low accuracy, low repeatability, and limited frequency response.
But there is one main disadvantage of using the potentiometer as a positional sensor. The range of movement of its wiper or slider (and hence the output signal obtained) is limited to the physical size of the potentiometer being used.
For example a single turn rotational potentiometer generally only has a fixed mechanical rotation of between 0o and about 240 to 330o maximum. However, multi-turn pots of up to 3600o (10 x 360o) of mechanical rotation are also available.
Most types of potentiometers use carbon film for their resistive track, but these types are electrically noisy (the crackle on a radio volume control), and also have a short mechanical life.
Wire-wound pots also known as rheostats, in the form of either a straight wire or wound coil resistive wire can also be used, but wire wound pots suffer from resolution problems as their wiper jumps from one wire segment to the next producing a logarithmic (LOG) output resulting in errors in the output signal. These too suffer from electrical noise.
For high precision low noise applications conductive plastic resistance element type polymer film or cermet type potentiometers are now available. These pots have a smooth low friction electrically linear (LIN) resistive track giving them a low noise, long life and excellent resolution and are available as both multi-turn and single turn devices. Typical applications for this type of high accuracy position sensor is in computer game joysticks, steering wheels, industrial and robot applications.
Inductive Position Sensors
Linear Variable Differential Transformer
One type of positional sensor that does not suffer from mechanical wear problems is the “Linear Variable Differential Transformer” or LVDT for short. This is an inductive type position sensor which works on the same principle as the AC transformer that is used to measure movement. It is a very accurate device for measuring linear displacement and whose output is proportional to the position of its moveable core.
It basically consists of three coils wound on a hollow tube former, one forming the primary coil and the other two coils forming identical secondaries connected electrically together in series but 180o out of phase either side of the primary coil.
A moveable soft iron ferromagnetic core (sometimes called an “armature”) which is connected to the object being measured, slides or moves up and down inside the tubular body of the LVDT.
A small AC reference voltage called the “excitation signal” (2 – 20V rms, 2 – 20kHz) is applied to the primary winding which in turn induces an EMF signal into the two adjacent secondary windings (transformer principles).
If the soft iron magnetic core armature is exactly in the centre of the tube and the windings, “null position”, the two induced emf’s in the two secondary windings cancel each other out as they are 180o out of phase, so the resultant output voltage is zero. As the core is displaced slightly to one side or the other from this null or zero position, the induced voltage in one of the secondaries will be become greater than that of the other secondary and an output will be produced.
The polarity of the output signal depends upon the direction and displacement of the moving core. The greater the movement of the soft iron core from its central null position the greater will be the resulting output signal. The result is a differential voltage output which varies linearly with the cores position. Therefore, the output signal from this type of position sensor has both an amplitude that is a linear function of the cores displacement and a polarity that indicates direction of movement.
The phase of the output signal can be compared to the primary coil excitation phase enabling suitable electronic circuits such as the AD592 LVDT Sensor Amplifier to know which half of the coil the magnetic core is in and thereby know the direction of travel.
The Linear Variable Differential Transformer

When the armature is moved from one end to the other through the centre position the output voltages changes from maximum to zero and back to maximum again but in the process changes its phase angle by 180 deg’s. This enables the LVDT to produce an output AC signal whose magnitude represents the amount of movement from the centre position and whose phase angle represents the direction of movement of the core.
A typical application of a linear variable differential transformer (LVDT) sensor would be as a pressure transducer, were the pressure being measured pushes against a diaphragm to produce a force. The force is then converted into a readable voltage signal by the sensor.
Advantages of the linear variable differential transformer, or LVDT compared to a resistive potentiometer are that its linearity, that is its voltage output to displacement is excellent, very good accuracy, good resolution, high sensitivity as well as frictionless operation. They are also sealed for use in hostile environments.
Inductive Proximity Sensors.
Another type of inductive position sensor in common use is the Inductive Proximity Sensor also called an Eddy current sensor. While they do not actually measure displacement or angular rotation they are mainly used to detect the presence of an object in front of them or within a close proximity, hence their name “proximity sensor”.
Proximity sensors, are non-contact position sensors that use a magnetic field for detection with the simplest magnetic sensor being the reed switch. In an inductive sensor, a coil is wound around an iron core within an electromagnetic field to form an inductive loop.
When a ferromagnetic material is placed within the eddy current field generated around the inductive sensor, such as a ferromagnetic metal plate or metal screw, the inductance of the coil changes significantly. The proximity sensors detection circuit detects this change producing an output voltage. Therefore, inductive proximity sensors operate under the electrical principle of Faraday’s Law of inductance.
Inductive Proximity Sensors

An inductive proximity sensor has four main components; The oscillator which produces the electromagnetic field, the coil which generates the magnetic field, the detection circuitwhich detects any change in the field when an object enters it and the output circuit which produces the output signal, either with normally closed (NC) or normally open (NO) contacts.
Inductive proximity sensors allow for the detection of metallic objects in front of the sensor head without any physical contact of the object itself being detected. This makes them ideal for use in dirty or wet environments. The “sensing” range of proximity sensors is very small, typically 0.1mm to 12mm.

Proximity Sensor
As well as industrial applications, inductive proximity sensors are also commonly used to control the flow of traffic by changing of traffic lights at junctions and cross roads. Rectangular inductive loops of wire are buried into the tarmac road surface.
When a car or other road vehicle passes over this inductive loop, the metallic body of the vehicle changes the loops inductance and activates the sensor thereby alerting the traffic lights controller that there is a vehicle waiting.
One main disadvantage of these types of position sensors is that they are “Omni-directional”, that is they will sense a metallic object either above, below or to the side of it. Also, they do not detect non-metallic objects although Capacitive Proximity Sensors and Ultrasonic Proximity Sensors are available. Other commonly available magnetic positional sensors include: reed switches, Hall Effect Sensors and variable reluctance sensors.
Rotary Encoders
Rotary Encoders are another type of position sensor which resemble potentiometers mentioned earlier but are non-contact optical devices used for converting the angular position of a rotating shaft into an analogue or digital data code. In other words, they convert mechanical movement into an electrical signal (preferably digital).
All optical encoders work on the same basic principle. Light from an LED or infra-red light source is passed through a rotating high-resolution encoded disk that contains the required code patterns, either binary, grey code or BCD. Photo detectors scan the disk as it rotates and an electronic circuit processes the information into a digital form as a stream of binary output pulses that are fed to counters or controllers which determine the actual angular position of the shaft.
There are two basic types of rotary optical encoders, Incremental Encoders and Absolute Position Encoders.
Incremental Encoder

Encoder Disk
Incremental Encoders, also known as quadrature encoders or relative rotary encoder, are the simplest of the two position sensors. Their output is a series of square wave pulses generated by a photocell arrangement as the coded disk, with evenly spaced transparent and dark lines called segments on its surface, moves or rotates past the light source. The encoder produces a stream of square wave pulses which, when counted, indicates the angular position of the rotating shaft.
Incremental encoders have two separate outputs called “quadrature outputs”. These two outputs are displaced at 90o out of phase from each other with the direction of rotation of the shaft being determined from the output sequence.
The number of transparent and dark segments or slots on the disk determines the resolution of the device and increasing the number of lines in the pattern increases the resolution per degree of rotation. Typical encoded discs have a resolution of up to 256 pulses or 8-bits per rotation.
The simplest incremental encoder is called a tachometer. It has one single square wave output and is often used in unidirectional applications where basic position or speed information only is required. The “Quadrature” or “Sine wave” encoder is the more common and has two output square waves commonly called channel A and channel B. This device uses two photo detectors, slightly offset from each other by 90o thereby producing two separate sine and cosine output signals.
Simple Incremental Encoder

By using the Arc Tangent mathematical function the angle of the shaft in radians can be calculated. Generally, the optical disk used in rotary position encoders is circular, then the resolution of the output will be given as: θ = 360/n, where n equals the number of segments on coded disk.
Then for example, the number of segments required to give an incremental encoder a resolution of 1o will be: 1o = 360/n, therefore, n = 360 windows, etc. Also the direction of rotation is determined by noting which channel produces an output first, either channel A or channel B giving two directions of rotation, A leads B or B leads A. This arrangement is shown below.
Incremental Encoder Output

One main disadvantage of incremental encoders when used as a position sensor, is that they require external counters to determine the absolute angle of the shaft within a given rotation. If the power is momentarily shut off, or if the encoder misses a pulse due to noise or a dirty disc, the resulting angular information will produce an error. One way of overcoming this disadvantage is to use absolute position encoders.
Absolute Position Encoder
Absolute Position Encoders are more complex than quadrature encoders. They provide a unique output code for every single position of rotation indicating both position and direction. Their coded disk consists of multiple concentric “tracks” of light and dark segments. Each track is independent with its own photo detector to simultaneously read a unique coded position value for each angle of movement. The number of tracks on the disk corresponds to the binary “bit”-resolution of the encoder so a 12-bit absolute encoder would have 12 tracks and the same coded value only appears once per revolution.
4-bit Binary Coded Disc

One main advantage of an absolute encoder is its non-volatile memory which retains the exact position of the encoder without the need to return to a “home” position if the power fails. Most rotary encoders are defined as “single-turn” devices, but absolute multi-turn devices are available, which obtain feedback over several revolutions by adding extra code disks.
Typical application of absolute position encoders are in computer hard drives and CD/DVD drives were the absolute position of the drives read/write heads are monitored or in printers/plotters to accurately position the printing heads over the paper.
These types of temperature sensor vary from simple ON/OFF thermostatic devices which control a domestic hot water heating system to highly sensitive semiconductor types that can control complex process control furnace plants.
We remember from our school science classes that the movement of molecules and atoms produces heat (kinetic energy) and the greater the movement, the more heat that is generated. Temperature Sensors measure the amount of heat energy or even coldness that is generated by an object or system, allowing us to “sense” or detect any physical change to that temperature producing either an analogue or digital output.
There are many different types of Temperature Sensor available and all have different characteristics depending upon their actual application. A temperature sensor consists of two basic physical types:
- Contact Temperature Sensor Types – These types of temperature sensor are required to be in physical contact with the object being sensed and use conduction to monitor changes in temperature. They can be used to detect solids, liquids or gases over a wide range of temperatures.
- Non-contact Temperature Sensor Types – These types of temperature sensor use convection and radiation to monitor changes in temperature. They can be used to detect liquids and gases that emit radiant energy as heat rises and cold settles to the bottom in convection currents or detect the radiant energy being transmitted from an object in the form of infra-red radiation (the sun).
The two basic types of contact or even non-contact temperature sensors can also be sub-divided into the following three groups of sensors, Electro-mechanical, Resistive and Electronic and all three types are discussed below.
The Thermostat
The Thermostat is a contact type electro-mechanical temperature sensor or switch, that basically consists of two different metals such as nickel, copper, tungsten or aluminium etc, that are bonded together to form a Bi-metallic strip. The different linear expansion rates of the two dissimilar metals produces a mechanical bending movement when the strip is subjected to heat.
The bi-metallic strip can be used itself as an electrical switch or as a mechanical way of operating an electrical switch in thermostatic controls and are used extensively to control hot water heating elements in boilers, furnaces, hot water storage tanks as well as in vehicle radiator cooling systems.
The Bi-metallic Thermostat

The thermostat consists of two thermally different metals stuck together back to back. When it is cold the contacts are closed and current passes through the thermostat. When it gets hot, one metal expands more than the other and the bonded bi-metallic strip bends up (or down) opening the contacts preventing the current from flowing.

On/Off Thermostat
There are two main types of bi-metallic strips based mainly upon their movement when subjected to temperature changes. There are the “snap-action” types that produce an instantaneous “ON/OFF” or “OFF/ON” type action on the electrical contacts at a set temperature point, and the slower “creep-action” types that gradually change their position as the temperature changes.
Snap-action type thermostats are commonly used in our homes for controlling the temperature set point of ovens, irons, immersion hot water tanks and they can also be found on walls to control the domestic heating system.
Creeper types generally consist of a bi-metallic coil or spiral that slowly unwinds or coils-up as the temperature changes. Generally, creeper type bi-metallic strips are more sensitive to temperature changes than the standard snap ON/OFF types as the strip is longer and thinner making them ideal for use in temperature gauges and dials etc.
Although very cheap and are available over a wide operating range, one main disadvantage of the standard snap-action type thermostats when used as a temperature sensor, is that they have a large hysteresis range from when the electrical contacts open until when they close again. For example, it may be set to 20oC but may not open until 22oC or close again until 18oC.
So the range of temperature swing can be quite high. Commercially available bi-metallic thermostats for home use do have temperature adjustment screws that allow for a more precise desired temperature set-point and hysteresis level to be pre-set.
The Thermistor
The Thermistor is another type of temperature sensor, whose name is a combination of the words THERM-ally sensitive res-ISTOR. A thermistor is a special type of resistor which changes its physical resistance when exposed to changes in temperature.

Thermistor
Thermistors are generally made from ceramic materials such as oxides of nickel, manganese or cobalt coated in glass which makes them easily damaged. Their main advantage over snap-action types is their speed of response to any changes in temperature, accuracy and repeatability.
Most types of thermistor’s have a Negative Temperature Coefficient of resistance or (NTC), that is their resistance value goes DOWN with an increase in the temperature, and of course there are some which have a Positive Temperature Coefficient, (PTC), in that their resistance value goes UP with an increase in temperature.
Thermistors are constructed from a ceramic type semiconductor material using metal oxide technology such as manganese, cobalt and nickel, etc. The semiconductor material is generally formed into small pressed discs or balls which are hermetically sealed to give a relatively fast response to any changes in temperature.
Thermistors are rated by their resistive value at room temperature (usually at 25oC), their time constant (the time to react to the temperature change) and their power rating with respect to the current flowing through them. Like resistors, thermistors are available with resistance values at room temperature from 10’s of MΩ down to just a few Ohms, but for sensing purposes those types with values in the kilo-ohms are generally used.
Thermistors are passive resistive devices which means we need to pass a current through it to produce a measurable voltage output. Then thermistors are generally connected in series with a suitable biasing resistor to form a potential divider network and the choice of resistor gives a voltage output at some pre-determined temperature point or value for example:
Temperature Sensors Example No1
The following thermistor has a resistance value of 10KΩ at 25oC and a resistance value of 100Ω at 100oC. Calculate the voltage drop across the thermistor and hence its output voltage (Vout) for both temperatures when connected in series with a 1kΩ resistor across a 12v power supply.

At 25oC

At 100oC

By changing the fixed resistor value of R2 (in our example 1kΩ) to a potentiometer or preset, a voltage output can be obtained at a predetermined temperature set point for example, 5v output at 60oC and by varying the potentiometer a particular output voltage level can be obtained over a wider temperature range.
It needs to be noted however, that thermistor’s are non-linear devices and their standard resistance values at room temperature is different between different thermistor’s, which is due mainly to the semiconductor materials they are made from. The Thermistor, have an exponential change with temperature and therefore have a Beta temperature constant ( β ) which can be used to calculate its resistance for any given temperature point.
However, when used with a series resistor such as in a voltage divider network or Wheatstone Bridge type arrangement, the current obtained in response to a voltage applied to the divider/bridge network is linear with temperature. Then, the output voltage across the resistor becomes linear with temperature.
Resistive Temperature Detectors (RTD).
Another type of electrical resistance temperature sensor is the Resistance Temperature Detector or RTD. RTD’s are precision temperature sensors made from high-purity conducting metals such as platinum, copper or nickel wound into a coil and whose electrical resistance changes as a function of temperature, similar to that of the thermistor. Also available are thin-film RTD’s. These devices have a thin film of platinum paste is deposited onto a white ceramic substrate.

A Resistive RTD
Resistive temperature detectors have positive temperature coefficients (PTC) but unlike the thermistor their output is extremely linear producing very accurate measurements of temperature.
However, they have very poor thermal sensitivity, that is a change in temperature only produces a very small output change for example, 1Ω/oC.
The more common types of RTD’s are made from platinum and are called Platinum Resistance Thermometer or PRT‘s with the most commonly available of them all the Pt100 sensor, which has a standard resistance value of 100Ω at 0oC. The downside is that Platinum is expensive and one of the main disadvantages of this type of device is its cost.
Like the thermistor, RTD’s are passive resistive devices and by passing a constant current through the temperature sensor it is possible to obtain an output voltage that increases linearly with temperature. A typical RTD has a base resistance of about 100Ω at 0oC, increasing to about 140Ω at 100oC with an operating temperature range of between -200 to +600oC.
Because the RTD is a resistive device, we need to pass a current through them and monitor the resulting voltage. However, any variation in resistance due to self heat of the resistive wires as the current flows through it, I2R , (Ohms Law) causes an error in the readings. To avoid this, the RTD is usually connected into a Wheatstone Bridge network which has additional connecting wires for lead-compensation and/or connection to a constant current source.
The Thermocouple
The Thermocouple is by far the most commonly used type of all the temperature sensor types. Thermocouples are popular due to its simplicity, ease of use and their speed of response to changes in temperature, due mainly to their small size. Thermocouples also have the widest temperature range of all the temperature sensors from below -200oC to well over 2000oC.
Thermocouples are thermoelectric sensors that basically consists of two junctions of dissimilar metals, such as copper and constantan that are welded or crimped together. One junction is kept at a constant temperature called the reference (Cold) junction, while the other the measuring (Hot) junction. When the two junctions are at different temperatures, a voltage is developed across the junction which is used to measure the temperature sensor as shown below.
Thermocouple Construction

The operating principal of a thermocouple is very simple and basic. When fused together the junction of the two dissimilar metals such as copper and constantan produces a “thermo-electric” effect which gives a constant potential difference of only a few millivolts (mV) between them. The voltage difference between the two junctions is called the “Seebeck effect” as a temperature gradient is generated along the conducting wires producing an emf. Then the output voltage from a thermocouple is a function of the temperature changes.
If both the junctions are at the same temperature the potential difference across the two junctions is zero in other words, no voltage output as V1 = V2. However, when the junctions are connected within a circuit and are both at different temperatures a voltage output will be detected relative to the difference in temperature between the two junctions, V1 – V2. This difference in voltage will increase with temperature until the junctions peak voltage level is reached and this is determined by the characteristics of the two dissimilar metals used.
Thermocouples can be made from a variety of different materials enabling extreme temperatures of between -200oC to over +2000oC to be measured. With such a large choice of materials and temperature range, internationally recognised standards have been developed complete with thermocouple colour codes to allow the user to choose the correct thermocouple sensor for a particular application. The British colour code for standard thermocouples is given below.
Thermocouple Colour Codes
Thermocouple Sensor Colour CodesExtension and Compensating Leads | |||
Code Type | Conductors (+/-) | Sensitivity | British BS 1843:1952 |
E | Nickel Chromium / Constantan | -200 to 900oC | ![]() |
J | Iron / Constantan | 0 to 750oC | ![]() |
K | Nickel Chromium / Nickel Aluminium | -200 to 1250oC | ![]() |
N | Nicrosil / Nisil | 0 to 1250oC | ![]() |
T | Copper / Constantan | -200 to 350oC | ![]() |
U | Copper / Copper Nickel Compensating for “S” and “R” | 0 to 1450oC | ![]() |
The three most common thermocouple materials used above for general temperature measurement are Iron-Constantan (Type J), Copper-Constantan (Type T), and Nickel-Chromium (Type K). The output voltage from a thermocouple is very small, only a few millivolts (mV) for a 10oC change in temperature difference and because of this small voltage output some form of amplification is generally required.
Thermocouple Amplification

The type of amplifier, either discrete or in the form of an Operational Amplifier needs to be carefully selected, because good drift stability is required to prevent recalibration of the thermocouple at frequent intervals. This makes the chopper and instrumentation type of amplifier preferable for most temperature sensing applications.
Other Temperature Sensor Types not mentioned here include, Semiconductor Junction Sensors, Infra-red and Thermal Radiation Sensors, Medical type Thermometers, Indicators and Colour Changing Inks or Dyes.
A Light Sensor generates an output signal indicating the intensity of light by measuring the radiant energy that exists in a very narrow range of frequencies basically called “light”, and which ranges in frequency from “Infra-red” to “Visible” up to “Ultraviolet” light spectrum.
The light sensor is a passive devices that convert this “light energy” whether visible or in the infra-red parts of the spectrum into an electrical signal output. Light sensors are more commonly known as “Photoelectric Devices” or “Photo Sensors” because the convert light energy (photons) into electricity (electrons).
Photoelectric devices can be grouped into two main categories, those which generate electricity when illuminated, such as Photo-voltaics or Photo-emissives etc, and those which change their electrical properties in some way such as Photo-resistors or Photo-conductors. This leads to the following classification of devices.
- • Photo-emissive Cells – These are photodevices which release free electrons from a light sensitive material such as caesium when struck by a photon of sufficient energy. The amount of energy the photons have depends on the frequency of the light and the higher the frequency, the more energy the photons have converting light energy into electrical energy.
- • Photo-conductive Cells – These photodevices vary their electrical resistance when subjected to light. Photoconductivity results from light hitting a semiconductor material which controls the current flow through it. Thus, more light increase the current for a given applied voltage. The most common photoconductive material is Cadmium Sulphide used in LDR photocells.
- • Photo-voltaic Cells – These photodevices generate an emf in proportion to the radiant light energy received and is similar in effect to photoconductivity. Light energy falls on to two semiconductor materials sandwiched together creating a voltage of approximately 0.5V. The most common photovoltaic material is Selenium used in solar cells.
- • Photo-junction Devices – These photodevices are mainly true semiconductor devices such as the photodiode or phototransistor which use light to control the flow of electrons and holes across their PN-junction. Photojunction devices are specifically designed for detector application and light penetration with their spectral response tuned to the wavelength of incident light.
The Photoconductive Cell
A Photoconductive light sensor does not produce electricity but simply changes its physical properties when subjected to light energy. The most common type of photoconductive device is the Photoresistor which changes its electrical resistance in response to changes in the light intensity.
Photoresistors are Semiconductor devices that use light energy to control the flow of electrons, and hence the current flowing through them. The commonly used Photoconductive Cell is called the Light Dependent Resistor or LDR.
The Light Dependent Resistor

Typical LDR
As its name implies, the Light Dependent Resistor (LDR) is made from a piece of exposed semiconductor material such as cadmium sulphide that changes its electrical resistance from several thousand Ohms in the dark to only a few hundred Ohms when light falls upon it by creating hole-electron pairs in the material.
The net effect is an improvement in its conductivity with a decrease in resistance for an increase in illumination. Also, photoresistive cells have a long response time requiring many seconds to respond to a change in the light intensity.
Materials used as the semiconductor substrate include, lead sulphide (PbS), lead selenide (PbSe), indium antimonide (InSb) which detect light in the infra-red range with the most commonly used of all photoresistive light sensors being Cadmium Sulphide (Cds).
Cadmium sulphide is used in the manufacture of photoconductive cells because its spectral response curve closely matches that of the human eye and can even be controlled using a simple torch as a light source. Typically then, it has a peak sensitivity wavelength (λp) of about 560nm to 600nm in the visible spectral range.
The Light Dependent Resistor Cell

The most commonly used photoresistive light sensor is the ORP12 Cadmium Sulphide photoconductive cell. This light dependent resistor has a spectral response of about 610nm in the yellow to orange region of light. The resistance of the cell when unilluminated (dark resistance) is very high at about 10MΩ’s which falls to about 100Ω’s when fully illuminated (lit resistance).
To increase the dark resistance and therefore reduce the dark current, the resistive path forms a zigzag pattern across the ceramic substrate. The CdS photocell is a very low cost device often used in auto dimming, darkness or twilight detection for turning the street lights “ON” and “OFF”, and for photographic exposure meter type applications.

Connecting a light dependant resistor in series with a standard resistor like this across a single DC supply voltage has one major advantage, a different voltage will appear at their junction for different levels of light.
The amount of voltage drop across series resistor, R2is determined by the resistive value of the light dependant resistor, RLDR. This ability to generate different voltages produces a very handy circuit called a “Potential Divider” or Voltage Divider Network.
As we know, the current through a series circuit is common and as the LDR changes its resistive value due to the light intensity, the voltage present at VOUT will be determined by the voltage divider formula. An LDR’s resistance, RLDR can vary from about 100Ω in the sun light, to over 10MΩ in absolute darkness with this variation of resistance being converted into a voltage variation at VOUT as shown.
One simple use of a Light Dependent Resistor, is as a light sensitive switch as shown below.

LDR Switch
This basic light sensor circuit is of a relay output light activated switch. A potential divider circuit is formed between the photoresistor, LDR and the resistor R1. When no light is present ie in darkness, the resistance of the LDR is very high in the Megaohms (MΩ) range so zero base bias is applied to the transistor TR1 and the relay is de-energised or “OFF”.
As the light level increases the resistance of the LDR starts to decrease causing the base bias voltage at V1 to rise. At some point determined by the potential divider network formed with resistor R1, the base bias voltage is high enough to turn the transistor TR1 “ON” and thus activate the relay which in turn is used to control some external circuitry. As the light level falls back to darkness again the resistance of the LDR increases causing the base voltage of the transistor to decrease, turning the transistor and relay “OFF” at a fixed light level determined again by the potential divider network.
By replacing the fixed resistor R1 with a potentiometer VR1, the point at which the relay turns “ON” or “OFF” can be pre-set to a particular light level. This type of simple circuit shown above has a fairly low sensitivity and its switching point may not be consistent due to variations in either temperature or the supply voltage. A more sensitive precision light activated circuit can be easily made by incorporating the LDR into a “Wheatstone Bridge” arrangement and replacing the transistor with an Operational Amplifier as shown.
Light Level Sensing Circuit

In this basic dark sensing circuit, the light dependent resistor LDR1 and the potentiometer VR1 form one adjustable arm of a simple resistance bridge network, also known commonly as a Wheatstone bridge, while the two fixed resistors R1 and R2 form the other arm. Both sides of the bridge form potential divider networks across the supply voltage whose outputs V1 and V2 are connected to the non-inverting and inverting voltage inputs respectively of the operational amplifier.
The operational amplifier is configured as a Differential Amplifier also known as a voltage comparator with feedback whose output voltage condition is determined by the difference between the two input signals or voltages, V1 and V2. The resistor combination R1 and R2 form a fixed voltage reference at input V2, set by the ratio of the two resistors. The LDR – VR1 combination provides a variable voltage input V1 proportional to the light level being detected by the photoresistor.
As with the previous circuit the output from the operational amplifier is used to control a relay, which is protected by a free wheel diode, D1. When the light level sensed by the LDR and its output voltage falls below the reference voltage set at V2 the output from the op-amp changes state activating the relay and switching the connected load.
Likewise as the light level increases the output will switch back turning “OFF” the relay. The hysteresis of the two switching points is set by the feedback resistor Rf can be chosen to give any suitable voltage gain of the amplifier.
The operation of this type of light sensor circuit can also be reversed to switch the relay “ON” when the light level exceeds the reference voltage level and vice versa by reversing the positions of the light sensor LDR and the potentiometer VR1. The potentiometer can be used to “pre-set” the switching point of the differential amplifier to any particular light level making it ideal as a simple light sensor project circuit.
Photojunction Devices
Photojunction Devices are basically PN-Junction light sensors or detectors made from silicon semiconductor PN-junctions which are sensitive to light and which can detect both visible light and infra-red light levels. Photo-junction devices are specifically made for sensing light and this class of photoelectric light sensors include the Photodiode and the Phototransistor.
The Photodiode.

Photo-diode
The construction of the Photodiode light sensor is similar to that of a conventional PN-junction diode except that the diodes outer casing is either transparent or has a clear lens to focus the light onto the PN junction for increased sensitivity. The junction will respond to light particularly longer wavelengths such as red and infra-red rather than visible light.
This characteristic can be a problem for diodes with transparent or glass bead bodies such as the 1N4148 signal diode. LED’s can also be used as photodiodes as they can both emit and detect light from their junction. All PN-junctions are light sensitive and can be used in a photo-conductive unbiased voltage mode with the PN-junction of the photodiode always “Reverse Biased” so that only the diodes leakage or dark current can flow.
The current-voltage characteristic (I/V Curves) of a photodiode with no light on its junction (dark mode) is very similar to a normal signal or rectifying diode. When the photodiode is forward biased, there is an exponential increase in the current, the same as for a normal diode. When a reverse bias is applied, a small reverse saturation current appears which causes an increase of the depletion region, which is the sensitive part of the junction. Photodiodes can also be connected in a current mode using a fixed bias voltage across the junction. The current mode is very linear over a wide range.
Photo-diode Construction and Characteristics

When used as a light sensor, a photodiodes dark current (0 lux) is about 10uA for geranium and 1uA for silicon type diodes. When light falls upon the junction more hole/electron pairs are formed and the leakage current increases. This leakage current increases as the illumination of the junction increases.
Thus, the photodiodes current is directly proportional to light intensity falling onto the PN-junction. One main advantage of photodiodes when used as light sensors is their fast response to changes in the light levels, but one disadvantage of this type of photodevice is the relatively small current flow even when fully lit.
The following circuit shows a photo-current-to-voltage converter circuit using an operational amplifier as the amplifying device. The output voltage (Vout) is given as Vout = IP*Rƒ and which is proportional to the light intensity characteristics of the photodiode.
This type of circuit also utilizes the characteristics of an operational amplifier with two input terminals at about zero voltage to operate the photodiode without bias. This zero-bias op-amp configuration gives a high impedance loading to the photodiode resulting in less influence by dark current and a wider linear range of the photocurrent relative to the radiant light intensity. Capacitor Cf is used to prevent oscillation or gain peaking and to set the output bandwidth (1/2πRC).
Photo-diode Amplifier Circuit

Photodiodes are very versatile light sensors that can turn its current flow both “ON” and “OFF” in nanoseconds and are commonly used in cameras, light meters, CD and DVD-ROM drives, TV remote controls, scanners, fax machines and copiers etc, and when integrated into operational amplifier circuits as infrared spectrum detectors for fibre optic communications, burglar alarm motion detection circuits and numerous imaging, laser scanning and positioning systems etc.
The Phototransistor

Photo-transistor
An alternative photo-junction device to the photodiode is the Phototransistor which is basically a photodiode with amplification. The Phototransistor light sensor has its collector-base PN-junction reverse biased exposing it to the radiant light source.
Phototransistors operate the same as the photodiode except that they can provide current gain and are much more sensitive than the photodiode with currents are 50 to 100 times greater than that of the standard photodiode and any normal transistor can be easily converted into a phototransistor light sensor by connecting a photodiode between the collector and base.
Phototransistors consist mainly of a bipolar NPN Transistor with its large base region electrically unconnected, although some phototransistors allow a base connection to control the sensitivity, and which uses photons of light to generate a base current which in turn causes a collector to emitter current to flow. Most phototransistors are NPN types whose outer casing is either transparent or has a clear lens to focus the light onto the base junction for increased sensitivity.
Photo-transistor Construction and Characteristics

In the NPN transistor the collector is biased positively with respect to the emitter so that the base/collector junction is reverse biased. therefore, with no light on the junction normal leakage or dark current flows which is very small. When light falls on the base more electron/hole pairs are formed in this region and the current produced by this action is amplified by the transistor.
Usually the sensitivity of a phototransistor is a function of the DC current gain of the transistor. Therefore, the overall sensitivity is a function of collector current and can be controlled by connecting a resistance between the base and the emitter but for very high sensitivity optocoupler type applications, Darlington phototransistors are generally used.

Photo-darlington
Photodarlington transistors use a second bipolar NPN transistor to provide additional amplification or when higher sensitivity of a photodetector is required due to low light levels or selective sensitivity, but its response is slower than that of an ordinary NPN phototransistor.
Photo darlington devices consist of a normal phototransistor whose emitter output is coupled to the base of a larger bipolar NPN transistor. Because a darlington transistor configuration gives a current gain equal to a product of the current gains of two individual transistors, a photodarlington device produces a very sensitive detector.
Typical applications of Phototransistors light sensors are in opto-isolators, slotted opto switches, light beam sensors, fibre optics and TV type remote controls, etc. Infrared filters are sometimes required when detecting visible light.
Another type of photojunction semiconductor light sensor worth a mention is the Photo-thyristor. This is a light activated thyristor or Silicon Controlled Rectifier, SCR that can be used as a light activated switch in AC applications. However their sensitivity is usually very low compared to equivalent photodiodes or phototransistors.
To help increase their sensitivity to light, photo-thyristors are made thinner around the gate junction. The downside to this process is that it limits the amount of anode current that they can switch. Then for higher current AC applications they are used as pilot devices in opto-couplers to switch larger more conventional thyristors.
Photovoltaic Cells.
The most common type of photovoltaic light sensor is the Solar Cell. Solar cells convert light energy directly into DC electrical energy in the form of a voltage or current to a power a resistive load such as a light, battery or motor. Then photovoltaic cells are similar in many ways to a battery because they supply DC power.
However, unlike the other photo devices we have looked at above which use light intensity even from a torch to operate, photovoltaic solar cells work best using the suns radiant energy.
Solar cells are used in many different types of applications to offer an alternative power source from conventional batteries, such as in calculators, satellites and now in homes offering a form of renewable power.

Photovoltaic Cell
Photovoltaic cells are made from single crystal silicon PN junctions, the same as photodiodes with a very large light sensitive region but are used without the reverse bias. They have the same characteristics as a very large photodiode when in the dark.
When illuminated the light energy causes electrons to flow through the PN junction and an individual solar cell can generate an open circuit voltage of about 0.58v (580mV). Solar cells have a “Positive” and a “Negative” side just like a battery.
Individual solar cells can be connected together in series to form solar panels which increases the output voltage or connected together in parallel to increase the available current. Commercially available solar panels are rated in Watts, which is the product of the output voltage and current (Volts times Amps) when fully lit.
Characteristics of a typical Photovoltaic Solar Cell.

The amount of available current from a solar cell depends upon the light intensity, the size of the cell and its efficiency which is generally very low at around 15 to 20%. To increase the overall efficiency of the cell commercially available solar cells use polycrystalline silicon or amorphous silicon, which have no crystalline structure, and can generate currents of between 20 to 40mA per cm2.
Other materials used in the construction of photovoltaic cells include Gallium Arsenide, Copper Indium Diselenide and Cadmium Telluride. These different materials each have a different spectrum band response, and so can be “tuned” to produce an output voltage at different wavelengths of light.
In this tutorial about Light Sensors, we have looked at several examples of devices that are classed as Light Sensors. This includes those with and those without PN-junctions that can be used to measure the intensity of light.
Thus far we have seen a selection of Input devices that can be used to detect or “sense” a variety of physical variables and signals and are therefore called Sensors. But there are also a variety of electrical and electronic devices which are classed as Output devices used to control or operate some external physical process. These output devices are commonly called Actuators.
Actuators convert an electrical signal into a corresponding physical quantity such as movement, force, sound etc. An actuator is also classed as a transducer because it changes one type of physical quantity into another and is usually activated or operated by a low voltage command signal. Actuators can be classed as either binary or continuous devices based upon the number of stable states their output has.
For example, a relay is a binary actuator as it has two stable states, either energised and latched or de-energised and unlatched, while a motor is a continuous actuator because it can rotate through a full 360o motion. The most common types of actuators or output devices are Electrical Relays, Lights, Motors and Loudspeakers.
We saw previously that solenoids can be used to electrically open latches, doors, open or close valves, and in a variety of robotic and mechatronic applications, etc. However, if the solenoid plunger is used to operate one or more sets of electrical contacts, we have a device called a relay that is so useful it can be used in an infinite number of different ways and in this tutorial we will look at Electrical Relays.
Electrical Relays can also be divided into mechanical action relays called “Electromechanical Relays” and those which use semiconductor transistors, thyristors, triacs, etc, as their switching device called “Solid State Relays” or SSR’s.
The Electromechanical Relay
The term Relay generally refers to a device that provides an electrical connection between two or more points in response to the application of a control signal. The most common and widely used type of electrical relay is the electromechanical relay or EMR.

An Electrical Relay
The most fundamental control of any equipment is the ability to turn it “ON” and “OFF”. The easiest way to do this is using switches to interrupt the electrical supply. Although switches can be used to control something, they have their disadvantages. The biggest one is that they have to be manually (physically) turned “ON” or “OFF”. Also, they are relatively large, slow and only switch small electrical currents.
Electrical Relays however, are basically electrically operated switches that come in many shapes, sizes and power ratings suitable for all types of applications. Relays can also have single or multiple contacts within a single package with the larger power relays used for mains voltage or high current switching applications being called “Contactors”.
In this tutorial about electrical relays we are just concerned with the fundamental operating principles of “light duty” electromechanical relays we can use in motor control or robotic circuits. Such relays are used in general electrical and electronic control or switching circuits either mounted directly onto PCB boards or connected free standing and in which the load currents are normally fractions of an ampere up to 20+ amperes. The relay circuit are common in Electronics applications.
As their name implies, electromechanical relays are electro-magnetic devices that convert a magnetic flux generated by the application of a low voltage electrical control signal either AC or DC across the relay terminals, into a pulling mechanical force which operates the electrical contacts within the relay. The most common form of electromechanical relay consist of an energizing coil called the “primary circuit” wound around a permeable iron core.
This iron core has both a fixed portion called the yoke, and a moveable spring loaded part called the armature, that completes the magnetic field circuit by closing the air gap between the fixed electrical coil and the moveable armature. The armature is hinged or pivoted allowing it to freely move within the generated magnetic field closing the electrical contacts that are attached to it. Connected between the yoke and armature is normally a spring (or springs) for the return stroke to “reset” the contacts back to their initial rest position when the relay coil is in the “de-energized” condition, i.e. turned “OFF”.
Electromechanical Relay Construction

In our simple relay above, we have two sets of electrically conductive contacts. Relays may be “Normally Open”, or “Normally Closed”. One pair of contacts are classed as Normally Open, (NO) or make contacts and another set which are classed as Normally Closed, (NC) or break contacts. In the normally open position, the contacts are closed only when the field current is “ON” and the switch contacts are pulled towards the inductive coil.
In the normally closed position, the contacts are permanently closed when the field current is “OFF” as the switch contacts return to their normal position. These terms Normally Open, Normally Closed or Make and Break Contacts refer to the state of the electrical contacts when the relay coil is “de-energized”, i.e, no supply voltage connected to the relay coil. Contact elements may be of single or double make or break designs. An example of this arrangement is given below.

The relays contacts are electrically conductive pieces of metal which touch together completing a circuit and allow the circuit current to flow, just like a switch. When the contacts are open the resistance between the contacts is very high in the Mega-Ohms, producing an open circuit condition and no circuit current flows.
When the contacts are closed the contact resistance should be zero, a short circuit, but this is not always the case. All relay contacts have a certain amount of “contact resistance” when they are closed and this is called the “On-Resistance”, similar to FET’s.
With a new relay and contacts this ON-resistance will be very small, generally less than 0.2Ωbecause the tips are new and clean, but over time the tip resistance will increase.
For example. If the contacts are passing a load current of say 10A, then the voltage drop across the contacts using Ohms Law is 0.2 x 10 = 2 volts, which if the supply voltage is say 12 volts then the load voltage will be only 10 volts (12 – 2). As the contact tips begin to wear, and if they are not properly protected from high inductive or capacitive loads, they will start to show signs of arcing damage as the circuit current still wants to flow as the contacts begin to open when the relay coil is de-energized.
This arcing or sparking across the contacts will cause the contact resistance of the tips to increase further as the contact tips become damaged. If allowed to continue the contact tips may become so burnt and damaged to the point were they are physically closed but do not pass any or very little current.
If this arcing damage becomes to severe the contacts will eventually “weld” together producing a short circuit condition and possible damage to the circuit they are controlling. If now the contact resistance has increased due to arcing to say 1Ω the volt drop across the contacts for the same load current increases to 1 x 10 = 10 volts dc. This high voltage drop across the contacts may be unacceptable for the load circuit especially if operating at 12 or even 24 volts, then the faulty relay will have to be replaced.
To reduce the effects of contact arcing and high “On-resistances”, modern contact tips are made of, or coated with, a variety of silver based alloys to extend their life span as given in the following table.
Electrical Relay Contact Tip Materials
- Ag (fine silver)
- 1. Electrical and thermal conductivity are the highest of all the metals.
- 2. Exhibits low contact resistance, is inexpensive and widely used.
- 3. Contacts tarnish easily through sulphurisation influence.
- AgCu (silver copper)
- 1. Known as “Hard silver” contacts and have better wear resistance and less tendency to arc and weld, but slightly higher contact resistance.
- AgCdO (silver cadmium oxide)
- 1. Very little tendency to arc and weld, good wear resistance and arc extinguishing properties.
- AgW (silver tungsten)
- 1. Hardness and melting point are high, arc resistance is excellent.
- 2. Not a precious metal.
- 3. High contact pressure is required to reduce resistance.
- 4. Contact resistance is relatively high, and resistance to corrosion is poor.
- AgNi (silver nickel)
- 1. Equals the electrical conductivity of silver, excellent arc resistance.
- AgPd (silver palladium)
- 1. Low contact wear, greater hardness.
- 2. Expensive.
- Platinum, Gold and Silver Alloys
- 1. Excellent corrosion resistance, used mainly for low-current circuits.
Relay manufacturers data sheets give maximum contact ratings for resistive DC loads only and this rating is greatly reduced for either AC loads or highly inductive or capacitive loads. In order to achieve long life and high reliability when switching alternating currents with inductive or capacitive loads some form of arc suppression or filtering is required across the relay contacts.
Extending the life of relay tips by reducing the amount of arcing generated as they open is achieved by connecting a Resistor-Capacitor network called an RC Snubber Networkelectrically in parallel with an electrical relay contact tips. The voltage peak, which occurs at the instant the contacts open, will be safely short circuited by the RC network, thus suppressing any arc generated at the contact tips. For example.
Electrical Relay Snubber Circuit

Electrical Relay Contact Types.
As well as the standard descriptions of Normally Open, (NO) and Normally Closed, (NC) used to describe how the relays contacts are connected, relay contact arrangements can also be classed by their actions. Electrical relays can be made up of one or more individual switch contacts with each “contact” being referred to as a “pole”. Each one of these contacts or poles can be connected or “thrown” together by energizing the relays coil and this gives rise to the description of the contact types as being:
- SPST – Single Pole Single Throw
- SPDT – Single Pole Double Throw
- DPST – Double Pole Single Throw
- DPDT – Double Pole Double Throw
with the action of the contacts being described as “Make” (M) or “Break” (B). Then a simple relay with one set of contacts as shown above can have a contact description of:
“Single Pole Double Throw – (Break before Make)”, or SPDT – (B-M)
Examples of just some of the more common diagrams used for electrical relay contact types to identify relays in circuit or schematic diagrams is given below but there are many more possible configurations.
Electrical Relay Contact Configurations

- Where:
- C is the Common terminal
- NO is the Normally Open contact
- NC is the Normally Closed contact
Electromechanical relays are also denoted by the combinations of their contacts or switching elements and the number of contacts combined within a single relay. For example, a contact which is normally open in the de-energised position of the relay is called a “Form A contact” or make contact. Whereas a contact which is normally closed in the de-energised position of the relay is called a “Form B contact” or break contact.
When both a make and a break set of contact elements are present at the same time so that the two contacts are electrically connected to produce a common point (identified by three connections), the set of contacts are referred to as “Form C contacts” or change-over contacts. If no electrical connection exists between the make and break contacts it is referred to as a double change-over contact.
One final point to remember about using electrical relays. It is not advisable at all to connect relay contacts in parallel to handle higher load currents. For example, never attempt to supply a 10A load with two relay contacts in parallel that have 5A contact ratings each, as the mechanically operated relay contacts never close or open at exactly the same instant of time. The result is that one of the contacts will always be overloaded even for a brief instant resulting in premature failure of the relay over time.
Also, while electrical relays can be used to allow low power electronic or computer type circuits to switch relatively high currents or voltages both “ON” or “OFF”. Never mix different load voltages through adjacent contacts within the same relay such as for example, high voltage AC (240v) and low voltage DC (12v), always use separate relays for safety.
One of the more important parts of any electrical relay is its coil. This converts electrical current into an electromagnetic flux which is used to mechanically operate the relays contacts. The main problem with relay coils is that they are “highly inductive loads” as they are made from coils of wire. Any coil of wire has an impedance value made up of resistance ( R ) and inductance ( L ) in series (LR Series Circuit).
As the current flows through the coil a self induced magnetic field is generated around it. When the current in the coil is turned “OFF”, a large back emf (electromotive force) voltage is produced as the magnetic flux collapses within the coil (transformer theory). This induced reverse voltage value may be very high in comparison to the switching voltage, and may damage any semiconductor device such as a transistor, FET or micro-controller used to operate the relay coil.

One way of preventing damage to the transistor or any switching semiconductor device, is to connect a reverse biased diode across the relay coil.
When the current flowing through the coil is switched “OFF”, an induced back emf is generated as the magnetic flux collapses in the coil.
This reverse voltage forward biases the diode which conducts and dissipates the stored energy preventing any damage to the semiconductor transistor.
When used in this type of application the diode is generally known as a Flywheel Diode, Free-wheeling Diode and even Fly-back Diode, but they all mean the same thing. Other types of inductive loads which require a flywheel diode for protection are solenoids, motors and inductive coils.
As well as using flywheel Diodes for protection of semiconductor components, other devices used for protection include RC Snubber Networks, Metal Oxide Varistors or MOV and Zener Diodes.
The Solid State Relay.
While the electromechanical relay (EMR) are inexpensive, easy to use and allow the switching of a load circuit controlled by a low power, electrically isolated input signal, one of the main disadvantages of an electromechanical relay is that it is a “mechanical device”, that is it has moving parts so their switching speed (response time) due to physically movement of the metal contacts using a magnetic field is slow.
Over a period of time these moving parts will wear out and fail, or that the contact resistance through the constant arcing and erosion may make the relay unusable and shortens its life. Also, they are electrically noisy with the contacts suffering from contact bounce which may affect any electronic circuits to which they are connected.
To overcome these disadvantages of the electrical relay, another type of relay called a Solid State Relay or (SSR) for short was developed which is a solid state contactless, pure electronic relay.
The solid state relay being a purely electronic device has no moving parts within its design as the mechanical contacts have been replaced by power transistors, thyristors or triac’s. The electrical separation between the input control signal and the output load voltage is accomplished with the aid of an opto-coupler type Light Sensor.
The Solid State Relay provides a high degree of reliability, long life and reduced electromagnetic interference (EMI), (no arcing contacts or magnetic fields), together with a much faster almost instant response time, as compared to the conventional electromechanical relay.
Also the input control power requirements of the solid state relay are generally low enough to make them compatible with most IC logic families without the need for additional buffers, drivers or amplifiers. However, being a semiconductor device they must be mounted onto suitable heatsinks to prevent the output switching semiconductor device from over heating.
Solid State Relay

The AC type Solid State Relay turns “ON” at the zero crossing point of the AC sinusoidal waveform, prevents high inrush currents when switching inductive or capacitive loads while the inherent turn “OFF” feature of Thyristors and Triacs provides an improvement over the arcing contacts of the electromechanical relays.
Like the electromechanical relays, a Resistor-Capacitor (RC) snubber network is generally required across the output terminals of the SSR to protect the semiconductor output switching device from noise and voltage transient spikes when used to switch highly inductive or capacitive loads. In most modern SSR’s this RC snubber network is built as standard into the relay itself reducing the need for additional external components.
Non-zero crossing detection switching (instant “ON”) type SSR’s are also available for phase controlled applications such as the dimming or fading of lights at concerts, shows, disco lighting etc, or for motor speed control type applications.
As the output switching device of a solid state relay is a semiconductor device (Transistor for DC switching applications, or a Triac/Thyristor combination for AC switching), the voltage drop across the output terminals of an SSR when “ON” is much higher than that of the electromechanical relay, typically 1.5 – 2.0 volts. If switching large currents for long periods of time an additional heat sink will be required.
Input/Output Interface Modules.
Input/Output Interface Modules, (I/O Modules) are another type of solid state relay designed specifically to interface computers, micro-controller or PIC’s to “real world” loads and switches. There are four basic types of I/O modules available, AC or DC Input voltage to TTL or CMOS logic level output, and TTL or CMOS logic input to an AC or DC Output voltage with each module containing all the necessary circuitry to provide a complete interface and isolation within one small device. They are available as individual solid state modules or integrated into 4, 8 or 16 channel devices.
Modular Input/Output Interface System.

The main disadvantages of solid state relays (SSR’s) compared to that of an equivalent wattage electromechanical relay is their higher costs, the fact that only single pole single throw (SPST) types are available, “OFF”-state leakage currents flow through the switching device, and a high “ON”-state voltage drop and power dissipation resulting in additional heat sinking requirements. Also they can not switch very small load currents or high frequency signals such as audio or video signals although special Solid State Switches are available for this type of application.
The linear solenoid works on the same basic principal as the electromechanical relay seen in the previous tutorial and just like relays, they can also be switched and controlled using transistors or MOSFET’s. A “Linear Solenoid” is an electromagnetic device that converts electrical energy into a mechanical pushing or pulling force or motion.

Linear Solenoid
Linear solenoid’s basically consist of an electrical coil wound around a cylindrical tube with a ferro-magnetic actuator or “plunger” that is free to move or slide “IN” and “OUT” of the coils body. Solenoids can be used to electrically open doors and latches, open or close valves, move and operate robotic limbs and mechanisms, and even actuate electrical switches just by energising its coil.
Solenoids are available in a variety of formats with the more common types being the linear solenoid also known as the linear electromechanical actuator, (LEMA) and the rotary solenoid.
Both types of solenoid, linear and rotational are available as either a holding (continuously energised) or as a latching type (ON-OFF pulse) with the latching types being used in either energised or power-off applications. Linear solenoids can also be designed for proportional motion control were the plunger position is proportional to the power input.
When electrical current flows through a conductor it generates a magnetic field, and the direction of this magnetic field with regards to its North and South Poles is determined by the direction of the current flow within the wire. This coil of wire becomes an “Electromagnet” with its own north and south poles exactly the same as that for a permanent type magnet.
The strength of this magnetic field can be increased or decreased by either controlling the amount of current flowing through the coil or by changing the number of turns or loops that the coil has. An example of an “Electromagnet” is given below.
Magnetic Field produced by a Coil

When an electrical current is passed through the coils windings, it behaves like an electromagnet and the plunger, which is located inside the coil, is attracted towards the centre of the coil by the magnetic flux setup within the coils body, which in turn compresses a small spring attached to one end of the plunger. The force and speed of the plungers movement is determined by the strength of the magnetic flux generated within the coil.
When the supply current is turned “OFF” (de-energised) the electromagnetic field generated previously by the coil collapses and the energy stored in the compressed spring forces the plunger back out to its original rest position. This back and forth movement of the plunger is known as the solenoids “Stroke”, in other words the maximum distance the plunger can travel in either an “IN” or an “OUT” direction, for example, 0 – 30mm.
Linear Solenoid Construction
This type of solenoid is generally called a Linear Solenoid due to the linear directional movement and action of the plunger. Linear solenoids are available in two basic configurations called a “Pull-type” as it pulls the connected load towards itself when energised, and the “Push-type” that act in the opposite direction pushing it away from itself when energised. Both push and pull types are generally constructed the same with the difference being in the location of the return spring and design of the plunger.
Pull-type Linear Solenoid Construction

Linear solenoids are useful in many applications that require an open or closed (in or out) type motion such as electronically activated door locks, pneumatic or hydraulic control valves, robotics, automotive engine management, irrigation valves to water the garden and even the “Ding-Dong” door bell has one. They are available as open frame, closed frame or sealed tubular types.
Rotary Solenoids
Most electromagnetic solenoids are linear devices producing a linear back and forth force or motion. However, rotational solenoids are also available which produce an angular or rotary motion from a neutral position in either clockwise, anti-clockwise or in both directions (bi-directional).

Rotary Solenoid
Rotary solenoids can be used to replace small DC motors or stepper motors were the angular movement is very small with the angle of rotation being the angle moved from the start to the end position.
Commonly available rotary solenoids have movements of 25, 35, 45, 60 and 90o as well as multiple movements to and from a certain angle such as a 2-position self restoring or return to zero rotation, for example 0-to-90-to-0o, 3-position self restoring, for example 0o to +45o or 0o to -45o as well as 2-position latching.
Rotary solenoids produce a rotational movement when either energised, de-energised, or a change in the polarity of an electromagnetic field alters the position of a permanent magnet rotor. Their construction consists of an electrical coil wound around a steel frame with a magnetic disk connected to an output shaft positioned above the coil.
When the coil is energised the electromagnetic field generates multiple north and south poles which repel the adjacent permanent magnetic poles of the disk causing it to rotate at an angle determined by the mechanical construction of the rotary solenoid.
Rotary solenoids are used in vending or gaming machines, valve control, camera shutter with special high speed, low power or variable positioning solenoids with high force or torque are available such as those used in dot matrix printers, typewriters, automatic machines or automotive applications etc.
Solenoid Switching
Generally solenoids either linear or rotary operate with the application of a DC voltage, but they can also be used with AC sinusoidal voltages by using full wave bridge rectifiers to rectify the supply which then can be used to switch the DC solenoid. Small DC type solenoids can be easily controlled using Transistor or MOSFET switches and are ideal for use in robotic applications.
However, as we saw previously with electromechanical relays, linear solenoids are “inductive” devices so some form of electrical protection is required across the solenoid coil to prevent high back emf voltages from damaging the semiconductor switching device. In this case the standard “Flywheel Diode” is used, but you could equally use a zener diode or small value varistor.
Switching Solenoids using a Transistor

Reducing Energy Consumption
One of the main disadvantages of solenoids and especially the linear solenoid is that they are “inductive devices” made from coils of wire. This means that the solenoid coil converts some of the electrical energy used to operate them into “HEAT” due to the resistance of the wire.
In other words when connected for long periods of time to an electrical supply they get hot!, and the longer the time that the power is applied to a solenoid coil, the hotter the coil will become. Also as the coil heats up, its electrical resistance also changes allowing more current to flow increasing its temperature.
With a continuous voltage input applied to the coil, the solenoids coil does not have the opportunity to cool down because the input power is always on. In order to reduce this self generated heating effect it is necessary to reduce either the amount of time the coil is energised or reduce the amount of current flowing through it.
One method of consuming less current is to apply a suitable high enough voltage to the solenoid coil so as to provide the necessary electromagnetic field to operate and seat the plunger but then once activated to reduce the coils supply voltage to a level sufficient to maintain the plunger in its seated or latched position. One way of achieving this is to connect a suitable “holding” resistor in series with the solenoids coil, for example:
Reducing Solenoid Energy Consumption

Here, the switch contacts are closed shorting out the resistance and passing the full supply current directly to the solenoid coils windings. Once energised the contacts which can be mechanically connected to the solenoids plunger action open connecting the holding resistor, RH in series with the solenoids coil. This effectively connects the resistor in series with the coil.
By using this method, the solenoid can be connected to its voltage supply indefinitely (continuous duty cycle) as the power consumed by the coil and the heat generated is greatly reduced, which can be up to 85 to 90% using a suitable power resistor. However, the power consumed by the resistor will also generate a certain amount of heat, I2R (Ohm’s Law) and this also needs to be taken into account.
Solenoid Duty Cycle
Another more practical way of reducing the heat generated by the solenoids coil is to use an “intermittent duty cycle”. An intermittent duty cycle means that the coil is repeatedly switched “ON” and “OFF” at a suitable frequency so as to activate the plunger mechanism but not allow it to de-energise during the OFF period of the waveform. Intermittent duty cycle switching is a very effective way to reduce the total power consumed by the coil.
The Duty Cycle (%ED) of a solenoid is the portion of the “ON” time that a solenoid is energised and is the ratio of the “ON” time to the total “ON” and “OFF” time for one complete cycle of operation. In other words, the cycle time equals the switched-ON time plus the switched-OFF time. Duty cycle is expressed as a percentage, for example:


Then if a solenoid is switched “ON” or energised for 30 seconds and then switched “OFF” for 90 seconds before being re-energised again, one complete cycle, the total “ON/OFF” cycle time would be 120 seconds, (30+90) so the solenoids duty cycle would be calculated as 30/120 secs or 25%. This means that you can determine the solenoids maximum switch-ON time if you know the values of duty cycle and switch-OFF time.
For example, the switch-OFF time equals 15 secs, duty cycle equals 40%, therefore switch-ON time equals 10 secs. A solenoid with a rated Duty Cycle of 100% means that it has a continuous voltage rating and can therefore be left “ON” or continuously energised without overheating or damage.
E.XO Protecting Inputs in Digital Electronics
____________________________________________________________________
Introduction
In a generic electronic system there are some inputs that are controlled by the end user. These inputs are read by electronics and acted upon by using outputs. The inputs can come from a myriad of sources: buttons, switches, sensors, relays, and communication devices, to name a few. In certain environments and situations, these input signals can pose a threat to the electronics reading them – especially if those electronics are designed without thought of protection. One such environment is the world of industrial electronics.
An important aspect of designs for this environment is interfacing sensitive electronics with inputs coming from the harsh conditions of a factory floor. Usually, inputs are read by some sort of intelligent processor such as a microcontroller, FPGA, or state machine. In cases like these, it is imperative to protect the processor from the inputs, while still providing a usable signal for the processor to read.
Problem definition
In a typical factory system there may be buttons on a control panel located remotely from the central processing unit. The buttons are connected to central processing via long wires. Unfortunately this can lead to inadvertent electronic failure. Long wires can act as an inductor and when a button is opened or closed, large voltage spikes can show up on the electronic paths. Figure 1 shows a simplified diagram of this situation.
In a generic electronic system there are some inputs that are controlled by the end user. These inputs are read by electronics and acted upon by using outputs. The inputs can come from a myriad of sources: buttons, switches, sensors, relays, and communication devices, to name a few. In certain environments and situations, these input signals can pose a threat to the electronics reading them – especially if those electronics are designed without thought of protection. One such environment is the world of industrial electronics.
An important aspect of designs for this environment is interfacing sensitive electronics with inputs coming from the harsh conditions of a factory floor. Usually, inputs are read by some sort of intelligent processor such as a microcontroller, FPGA, or state machine. In cases like these, it is imperative to protect the processor from the inputs, while still providing a usable signal for the processor to read.
Problem definition
In a typical factory system there may be buttons on a control panel located remotely from the central processing unit. The buttons are connected to central processing via long wires. Unfortunately this can lead to inadvertent electronic failure. Long wires can act as an inductor and when a button is opened or closed, large voltage spikes can show up on the electronic paths. Figure 1 shows a simplified diagram of this situation.

Figure 1: Simplified electronic system.
In order to discuss approaches to overcoming this problem, a more specific example will be used. Typical microcontrollers have input impedance on the order of 20 MΩ. In addition, system voltages range from 1.2 V to 5.0 V. In this case, we will assume a 5 V system. Figure 2 shows Figure 1 reconfigured as a simplified electronic model.

Figure 2: Input model into a simplified electronic model.
Using this model, it is easy to see the problems with unprotected inputs. Any large voltage that shows up on input pin is presented directly to the interior electronics (microcontroller). Regardless of how this voltage is produced (ESD, induced EMI, switch closure, user error), this can damage the microcontroller, and perhaps cause the entire system to fail. Because of this, different protection strategies must be implemented to create a robust system.
In order to discuss the problem in detail, a simple system will be set up as shown in Figure 3. It is a simple switch that is connected to a microcontroller with a 25 foot wire connection. Note the switch is a 2-pole switch and it switches between open and ground. A pull-up resistor on the microcontroller causes the open position to be read as ‘high’ by the microcontroller.
In order to discuss the problem in detail, a simple system will be set up as shown in Figure 3. It is a simple switch that is connected to a microcontroller with a 25 foot wire connection. Note the switch is a 2-pole switch and it switches between open and ground. A pull-up resistor on the microcontroller causes the open position to be read as ‘high’ by the microcontroller.

Figure 3: Simple switch circuit.
When the position of the switch is changed, a large voltage is induced over the 25 feet of wire, and it appears at the microcontroller. This is demonstrated in Figure 4. Note the minimum voltage caused by the inductive ringing is -5.88V. This is more than large enough to cause serious problems within an electronic system.
With this circuit and the simple scope captures, the large voltage problem can be seen. Now it is time to look at approaches to fixing this problem.
With this circuit and the simple scope captures, the large voltage problem can be seen. Now it is time to look at approaches to fixing this problem.

Figure 4: Switch from open to ground.
Protection approaches
An important aspect of microcontroller inputs (and the vast majority of any logic ICs) that was left out of the simple model shown in Figure 3 is that they have internal protection diodes that are used to protect the inputs, as shown in Figure 5. These normally forward bias at 0.7 V.
Under ideal circumstances, this can protect the microcontroller. However, if the voltage is large enough or lasts for a long enough time, it can destroy the internal diodes in a shorted position, thereby ‘breaking’ the input pin. Even worse, the input pin is now directly connected to a power rail, so, when the next large voltage shows up on the input pin, it is shunted directly to the power bus, wreaking havoc throughout the microcontroller and most-likely damaging it further.
An important aspect of microcontroller inputs (and the vast majority of any logic ICs) that was left out of the simple model shown in Figure 3 is that they have internal protection diodes that are used to protect the inputs, as shown in Figure 5. These normally forward bias at 0.7 V.
Under ideal circumstances, this can protect the microcontroller. However, if the voltage is large enough or lasts for a long enough time, it can destroy the internal diodes in a shorted position, thereby ‘breaking’ the input pin. Even worse, the input pin is now directly connected to a power rail, so, when the next large voltage shows up on the input pin, it is shunted directly to the power bus, wreaking havoc throughout the microcontroller and most-likely damaging it further.

Figure 5: Enhanced microcontroller input model.
Even if the diodes are not destroyed, a large ESD spike can induce a current surge through the microcontroller’s power bus, which can corrupt internal registers and settings leading to unpredictable behavior. With all of this in mind, the first attempt to protect the input pin is found within current limiting.
Current limiting
The simplest protection mechanism is a current limiting resistor, as shown in Figure 6. The input resistor is sized so that the voltage drop across it does not affect the voltage at the microcontroller input. As this is a simple voltage divider, and the input resistance in the controller is about 20 MΩ, this resistor can be fairly big. For most digital inputs, a good value is between 100 Ω and 10 kΩ. For our system, a value of 1 kΩ is used.
Current limiting
The simplest protection mechanism is a current limiting resistor, as shown in Figure 6. The input resistor is sized so that the voltage drop across it does not affect the voltage at the microcontroller input. As this is a simple voltage divider, and the input resistance in the controller is about 20 MΩ, this resistor can be fairly big. For most digital inputs, a good value is between 100 Ω and 10 kΩ. For our system, a value of 1 kΩ is used.

Figure 6: Current limit protection for an input.
This type of protection works well for short wire connection lengths and enclosed wire runs (little chance of EMI, etc.). Figure 7 shows how this circuit works to implement the protection. In Figure 7, the ringing edges from the induced voltage are clipped at -0.810 V.

Figure 7: Current limit circuit results.
Filtering
Figure 6 showed a simple current limit circuit. However, with the addition of a capacitor, more protection can be added by turning the current limit circuit into a simple low-pass filter as shown in Figure 8.
Figure 6 showed a simple current limit circuit. However, with the addition of a capacitor, more protection can be added by turning the current limit circuit into a simple low-pass filter as shown in Figure 8.

Figure 8: Low pass filter protection for an input.
With this type of circuit, a little more thought must be applied to component selection. Because of the frequency limiting characteristics of the circuit in Figure 8, the value of the resistor and the capacitor must be sized so that the microcontroller does not miss any signals. The simple equation shown in Figure 9 can be used to determine the value of the resistor and the capacitor.

Figure 9: Equation for determining the resistor and capacitor values in a low pass filter circuit used for a digital input.
To calculate the value of R and C, use the following steps:
- Find the fastest edge of the incoming signal – or determine the fastest frequency of the incoming signal and assume an edge speed of 1/100th of the input period (a 1 kHz input frequency has an edge of 10 µs).
- Select ‘R’. Usually this can be selected to a common value already in the system, such as 1 kΩ.
- Use the equation in Figure 9 to determine the value of ‘C’.
- In some cases, the input signal is a very slow moving signal (button press, switch closure, etc.), so the value of ‘C’ can be then changed to match a common value on the board, as long as the order of magnitude is maintained.
As shown in Figure 8, the values for R and C are 1 kΩ and 0.01 µF (assumed a maximum input frequency of 1 kHz). Figure 10 shows how this circuit works with the input switch circuit. Note how the overshoot edges are now gone compared to Figure 7. This is the effect of the capacitor.

Figure 10: RC filter performance.
One added advantage to the RC filter circuit for a digital input is that it also rejects spurious/fast inputs that could cause false readings on the microcontroller. Unfortunately, for large ESD events and long wire runs, there can still be voltage spikes in the microcontroller because the circuit is relying on the clipping action of the internal diodes. This leads to the next approach.
External clipping diodes
To eliminate the use of the microcontroller’s internal diodes, external Schottky clipping diodes can be used. This is shown in Figure 11. Schottky diodes are implemented because they conduct before the internal diodes of the microcontroller (Schottky diodes forward bias at about 0.2 V as opposed to the 0.7 V of the internal diodes). Note that a small series resistor is used to protect the Schottky diodes from overcurrent. As these diodes are only on for a short time, a small resistor works well; something on the order of 10 Ω usually works fine. Alternatively, the 10 Ω resistor can be omitted if the Schottky diodes are beefy enough to handle short-duration, high current pulses.
External clipping diodes
To eliminate the use of the microcontroller’s internal diodes, external Schottky clipping diodes can be used. This is shown in Figure 11. Schottky diodes are implemented because they conduct before the internal diodes of the microcontroller (Schottky diodes forward bias at about 0.2 V as opposed to the 0.7 V of the internal diodes). Note that a small series resistor is used to protect the Schottky diodes from overcurrent. As these diodes are only on for a short time, a small resistor works well; something on the order of 10 Ω usually works fine. Alternatively, the 10 Ω resistor can be omitted if the Schottky diodes are beefy enough to handle short-duration, high current pulses.

Figure 11: External clipping diode circuit.
Figure 12 shows the results of this circuit with the input switch circuit. The yellow trace is the positive side of the capacitor, while the green trace is where the resistor meets the Schottky diodes. Note the negative spike is -0.650 V, which is below the forward bias voltage of the microcontroller. A voltage of this level on a well-designed PCB should not cause any problems.

Figure 12: External diode protection results.
So for the most ruggedized digital input protection, a combination of external resistors, capacitors, and diodes should be used.
Other ideas
These basic ideas can be further expanded for known high voltage inputs. For example, if the input signal was changed to switching a high voltage instead of ground, a circuit like the one shown in Figure 13 can be used.
Other ideas
These basic ideas can be further expanded for known high voltage inputs. For example, if the input signal was changed to switching a high voltage instead of ground, a circuit like the one shown in Figure 13 can be used.

Figure 13: Reading high voltage inputs.
The input clipping diode to ground is to protect from less than zero volt spikes. The input clipping diode to the positive bus is removed in favor of the zener diode after the current limiting resistor. This provides a known voltage for the input pin and reduces the amount of current shunted to the power bus. In addition, all of the connections on the input are now to ground, which can ease PCB routing. Note, in this case, the current limiting resistor must be sized small enough to provide enough current to allow zener breakdown at the correct voltage (about 1 mA minimum). Figure 14 shows the operation of this circuit, using a switched 12 V input.

Figure 14: Reading large input voltage digital inputs.
Conclusion
When interfacing digital circuitry with the outside world, care must be taken to protect the sensitive electronics. However, the circuitry required to provide the protection is small, inexpensive, and easy to understand. If a little bit of forethought is used when designing the system, many difficulties can be avoided once the system is deployed.
When interfacing digital circuitry with the outside world, care must be taken to protect the sensitive electronics. However, the circuitry required to provide the protection is small, inexpensive, and easy to understand. If a little bit of forethought is used when designing the system, many difficulties can be avoided once the system is deployed.
F, XO Digital I/O basic knowledge
_____________________________________________________________________
. What is a digital I/O board?
A digital I/O board is an interface board that adds the ability to input and output digital signals in parallel to a computer. Using a digital I/O device makes it possible to monitor (read) the statuses of measuring devices as well as the relays and operation switches of various types of control circuits. In addition to controlling output for lamps, LEDs, 7-segment displays, and relays, such products can also be used as an interface for digital communication with controllers such as a PLC (sequencer).
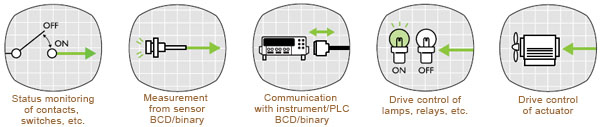
2. Digital I/O board types and applications
2-1. Photocoupler-isolated I/O type
This type provides isolation of the I/O circuit and the logic circuit inside the board using a photocoupler. Transmitting a signal (information) using light makes it possible to prevent the effects of electrical disturbances generated in the operation circuit. However, an external DC power source is required to drive the photocoupler. This is used for connecting the operation circuit to weak electrical devices using 5 to 48 VDC, such as digital switches and indicators.
- Opto-Isolated Input type (Current sink output)
- Opto-Isolated Input type (Current sink and source output)
- Opto-Isolated Input type (Source output)
- Opto-Isolated TTL level Input type (negative logic)
- Opto-Isolated Open Collector output type (Current sink)
- Opto-Isolated Output type (Source output)
- Opto-Isolated TTL level Output type (negative logic)
2-1-1. High-speed photocoupler-isolated I/O type
This type enables faster signal transmission speeds by using a high-speed photocoupler as the isolating element. This type is used when high-speed input and output is required.
2-1-2. High-speed photocoupler-isolated I/O type with built-in power source
This internal logic circuit is equipped with an isolated DC power source. Because power is supplied to the photocoupler's drive and operation circuits, this type is useful when power cannot be provided.
2-2. Contact output type
This type uses a relay in the output circuit. The logic circuit and output circuit inside the board are isolated by this relay contact. Also, because there are no limits on the direction the current flows, AC (alternating current) loads can also be connected. Use this type with AC operating circuits or to directly control strong electrical devices using more than 48 VDC.
2-3. Non-isolated I/O type
This type features a direct connection of the logic circuit inside the board and the I/O circuit without isolation. Compared with photocoupler-isolated I/O types, this type offers high-speed responses. However, because it is susceptible to electrical disturbances, this type is suitable for environments with favorable noise characteristics and when wiring distances can be shortened. Use this type for devices with 5 VDC / 3.3 VDC I/O circuits and TTL/LVTTL devices, including small relays and controllers.
- Non-Isolated TTL level Input type (negative logic)
- Non-Isolated TTL level Input type (positive logic)
- Non-Isolated LVTTL level Input type (positive logic)
- Non-Isolated TTL level Open Collector Output (negative logic)
- Non-Isolated TTL level Output type (positive logic)
- Non-Isolated LVTTL level Output type (positive logic)
2-3-1. Bidirectional I/O type
This type features a direct connection without isolation between the logic circuit inside the board and an i8255 PPI or equivalent bidirectional I/O circuit. Using a program allows the number of inputs and outputs to be changed in 8-point units. Use this type of product when connecting to equipment that requires TTL (5 VDC) or LVTTL (3.3 VDC) bidirectional I/O.
3. Output circuit
Output circuits for digital input and output are categorized into the following types according to application and electrical differences.
3-1. Transistor output (contact-less output)
Using a transistor that functions as a semiconductor device, this output circuit is capable of driving and opening/closing DC loads. This type of output is called contact-less output because there is no real contact involved, unlike contact output.
3-1-1. Photocoupler-isolated open-collector output (current sink type)
This output circuit is where the output transistor collector becomes the output terminal and the status becomes open. The internal logic is "ON (short): 1, OFF (open): 0." In this sink type, when the output transistor becomes "ON" (a load is operated), the current flows from the load to the output terminal. This output is used to send signals to typical weak electrical devices using 12 to 48 VDC.
3-1-2. Photocoupler-isolated output (current source type and negative common type)
In this output circuit, the output transistor emitter becomes the output terminal. The internal logic is "ON (short): 1, OFF (open): 0." In this source type, when the output transistor becomes "ON" (a load is operated), the current flows from the output terminal to the load. This output is used to send signals to weak electrical devices using 12 to 48 VDC and is the preferred source type in European countries because it offers high safety concerning ground faults.
3-1-3. Non-isolated TTL open-collector output (negative logic)
With this output circuit, the output transistor collector becomes the output terminal, the status is open, and the input circuit side is pulled up. The internal logic is negative logic of "Low (short): 1, High (open): 0." This output is used to send signals to devices with TTL input circuits and 5 VDC devices.
3-1-4. Photocoupler-isolated TTL level output (negative logic)
In this output circuit, the output transistor collector becomes the output terminal. The internal logic is negative logic of "Low: 1, High: 0." This output is used when the operation circuit wiring of devices with TTL input circuits and 5 VDC devices becomes too long or to isolate such devices.
3-2. Contact output (reed output)
This output circuit, which uses a relay contact, is isolated with the internal logic circuit. The circuit is also called a reed output because, using real contact, it drives and opens/closes the load. Also, because there are no limits on the direction the current flows, AC (alternating current) loads, as well as DC loads, can be connected. This output is used with alternating currents (AC) or to send signals to strong electrical devices using more than 48 VDC.
4. Input circuit
Input circuits for digital input and output are categorized into the following types.
4-1. DC input
This input circuit can be connected to such contact output circuits as DC transistor outputs or DC operation circuits.
4-1-1. Photocoupler-isolated input (type compatible with current sink output)
This is the input circuit with the cathode side of the photocoupler as the input terminal. This input is used to receive output signals from such sources as sink-type transistor outputs and relay switches. The internal logic is "ON (short): 1, OFF (open): 0." The input terminal is a source-type terminal that feeds an electrical current. This type is used to input signals from typical weak electrical devices using 12 to 48 VDC.
4-1-2. Photocoupler-isolated input (current source output-compatible type and negative common type)
This is the input circuit with the anode side of the photocoupler as the input terminal. This input is used to receive output signals from such sources as source-type transistor outputs and relay switches. The internal logic is "ON (short): 1, OFF (open): 0." The input terminal is a sink-type terminal that accepts an electrical current. This is the preferred type in European countries because it offers high safety concerning ground faults. This type is used to input signals from weak electrical devices using 12 to 48 VDC.
4-1-3. Non-isolated TTL level input (Negative logic)
With this input circuit, pulled up at 5 VDC, the transistor base becomes the input terminal. The internal logic is negative logic of "Low: 1, High: 0." This type is used to input signals from devices with TTL output circuits and 5 VDC devices.
4-1-4. Photocoupler-isolated TTL level input (negative logic)
This is the input circuit with a photocoupler cathode as the input terminal. The internal logic is negative logic of "Low: 1, High: 0." This input is used when the operation circuit wiring of devices with TTL output circuits and 5 VDC devices becomes too long or to isolate such devices.
5. Bidirectional I/O circuit
5-1. Non-isolated TTL/LVTTL level input/output (positive logic)
This is the i8255 PPI (or equivalent) I/O circuit. The internal logic is positive logic of "Low (short): 0, High (open): 1." Use this type of product when connecting to signal inputs/outputs from equipment with TTL I/O circuits, 5 VDC equipment, or equipment that requires TTL (5 VDC) or LVTTL (5 VDC) bidirectional I/O.
6. Selection hints
CASE 1 Performing relay control at the digital output board
With ON/OFF relay control, the number of devices usually becomes the number of outputs needed. To control 10 relays, select a board with 10 or more outputs.
- ※The device you are using may offer such functions as alarms, resetting, and handshaking. In such instances, it is necessary to supply the appropriate number of additional inputs/outputs.
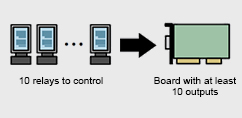
CASE 2 Monitoring switches at the digital input board
When monitoring the ON/OFF status of switches, the number of devices usually becomes the necessary number of inputs. To monitor 20 switches, select a board with 20 or more inputs.
- ※The device you are using may offer such functions as alarms, resetting, and handshaking. In such instances, it is necessary to supply the appropriate number of additional inputs/outputs.
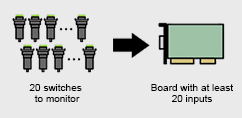
CASE 3 Controlling a 7-segment display with BCD/binary data input from the digital output board
CASE 4 Inputting BCD/binary data from the digital switches at the digital input board
With typical decimal and hexadecimal types, usually 4-bit (4-point) output and input is needed for 1 digit. With 3-digit, 7-segment display devices or digital switches, select a board with at least 12 inputs and outputs (4 points × 3 digits).
- ※The device you are using may offer such functions as alarms, resetting, and handshaking. In such instances, it is necessary to supply the appropriate number of additional inputs/outputs.
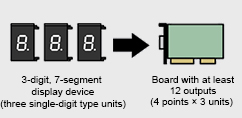
CASE 5 Absolute-type (binary data output) rotary encoder
In general, the number of inputs is related to the resolution for one revolution. For example, for a resolution of 256 in one revolution, 8-bit (256=28) binary data will be output. Select a board with 8 or more inputs.
- ※The device you are using may offer such functions as alarms, resetting, and handshaking. In such instances, it is necessary to supply the appropriate number of additional inputs/outputs.
- ※For incremental-type rotary encoders, use a "counter board" equipped with a pulse-counting function.
G. XO The Computer System
____________________________________________________________________
COMPUTER SYSTEM
COMPUTER SYSTEM
Definition: Is a collection of entities(hardware,software and liveware) that are designed to receive, process, manage and present information in a meaningful format.
COMPONENTS OF COMPUTER SYSTEM
B. POINTING DEVICESAre devices that enter data and instructions into the computer using a pointer that appears on the screen. The items to be entered are selected by either pointing to or clicking on them.e.g mice, joystick, touch sensitive screen, trackballs
i) THE MOUSE
A mouse is a small device used to point to and select items on your computer screen. Although mice come in many shapes, the typical mouse does look a bit like an actual mouse. It's small, oblong, and connected to the system unit by a long wire that resembles a tail and the connector which can either be PS/2 or USB. Some newer mice are wireless.
A motherboard (mainboard, system board, planar board or logic board) is the main printed circuit board found in computers and other expandable systems. It holds many of the crucial electronic components of the system, such as the central processing unit (CPU) and memory, and provides connectors for other peripherals.
Definition: Is a collection of entities(hardware,software and liveware) that are designed to receive, process, manage and present information in a meaningful format.
COMPONENTS OF COMPUTER SYSTEM
- Computer hardware - Are physical parts/ intangible parts of a computer. eg Input devices, output devices, central processing unit and storage devices
- Computer software - also known as programs or applications. They are classified into two classes namely - sytem software and application software
- Liveware - is the computer user. Also kwon as orgwareor the humanware. The user commands the computer system to execute on instructions.
Hardware refers to the physical, tangible computer equipment and devices, which provide support for major functions such as input, processing (internal storage, computation and control), output, secondary storage (for data and programs), and communication.


HARDWARE CATEGORIES (Functional Parts)
A computer system is a set of integrated devices that input, output, process, and store data and information. Computer systems are currently built around at least one digital processing device. There are five main hardware components in a computer system: Input, Processing, Storage, Output and Communication devices.
Are devices used for entering data or instructions to the central processing unit. Are classifie according to the method they use to enter data.
a) KEYING DEVICES
Are devices used to enter data into the computer using a set of Keys eg Keyboard, key-to- storage and keypad.
i) The keyboard
Are devices used to enter data into the computer using a set of Keys eg Keyboard, key-to- storage and keypad.
i) The keyboard
Keyboard (similar to a typewriter) is the main input device of a computer . It contains three types of keys-- alphanumeric keys, special keys and function keys. Alphanumeric keys are used to type all alphabets, numbers and special symbols like $, %, @, A etc. Special keys such as <Shift>, <Ctrl>, <Alt>, <Home>, <Scroll Lock> etc. are used for special functions. Function keys such as <Fl>, <F2>, <F3> etc. are used to give special commands depending upon the software used e.g.F5 reloads a page of an internet browser. The function of each and every key can be well understood only after working on a PC. When any key is pressed, an electronic signal is produced. This signal is detected by a keyboard encoder that sends a binary code corresponding to the key pressed to the CPU. There are many types of keyboards but 101 keys keyboard is the most popular one.
How the keys are organized
The keys on your keyboard can be divided into several groups based on function:
- Typing (alphanumeric) keys. These keys include the same letter, number, punctuation, and symbol keys found on a traditional typewriter.
- Special (Control) keys. These keys are used alone or in combination with other keys to perform certain actions. The most frequently used control keys are CTRL, ALT, the Windows key, and ESC.
- Function keys. The function keys are used to perform specific tasks. They are labelled as F1, F2, F3, and so on, up to F12. The functionality of these keys differs from program to program.
- Cursor Movement (Navigation) keys. These keys are used for moving around in documents or WebPages and editing text. They include the arrow keys, HOME, END, PAGE UP, PAGE DOWN, DELETE, and INSERT and ARROW KEYS.
- Numeric keypad. The numeric keypad is handy for entering numbers quickly. The keys are grouped together in a block like a conventional calculator or adding machine.
B. POINTING DEVICESAre devices that enter data and instructions into the computer using a pointer that appears on the screen. The items to be entered are selected by either pointing to or clicking on them.e.g mice, joystick, touch sensitive screen, trackballs
i) THE MOUSE
A mouse is a small device used to point to and select items on your computer screen. Although mice come in many shapes, the typical mouse does look a bit like an actual mouse. It's small, oblong, and connected to the system unit by a long wire that resembles a tail and the connector which can either be PS/2 or USB. Some newer mice are wireless.
A mouse usually has two buttons: a primary button (usually the left button) and a secondary button. Many mice also have a wheel between the two buttons, which allows you to scroll smoothly through screens of information.
When you move the mouse with your hand, a pointer on your screen moves in the same direction. (The pointer's appearance might change depending on where it's positioned on your screen.) When you want to select an item, you point to the item and then click (press and release) the primary button. Pointing and clicking with your mouse is the main way to interact with your computer. There are several types of mice: Mechanical mouse, optical mouse, optical-mechanical mouse and laser mouse.
Basic parts
A mouse typically has two buttons: a primary button (usually the left button) and a secondary button (usually the right button). The primary button is the one you will use most often. Most mice also include a scroll wheel between the buttons to help you scroll through documents and WebPages more easily. On some mice, the scroll wheel can be pressed to act as a third button. Advanced mice might have additional buttons that can perform other functions.

Holding and moving the mouse

Holding and moving the mouse
Place your mouse beside your keyboard on a clean, smooth surface, such as a mouse pad. Hold the mouse gently with your index finger resting on the primary button and you thumb resting on the side. To move the mouse, slide it slowly in any direction. Don't twist it—keep the front of the mouse aimed away from you. As you move the mouse, a pointer (see picture) on your screen moves in the same direction. If you run out of room to move your mouse on your desk or mouse pad, just pick up the mouse and bring it back closer to you.
Pointing to an object often reveals a descriptive message about it.The pointer can change depending on what you're pointing at. For example, when you point to a link in your web browser, the pointer changes from an arrow to a hand with a pointing finger .
Most mouse actions combine pointing with pressing one of the mouse buttons. There are four basic ways to use your mouse buttons: clicking, double-clicking, right-clicking, and dragging.
Clicking (single-clicking)
To click an item, point to the item on the screen, and then press and release the primary button (usually the left button).
Clicking is most often used to select (mark) an item or open a menu. This is sometimes called single-clicking or left-clicking.
Double-clicking
To double-click an item, point to the item on the screen, and then click twice quickly. If the two clicks are spaced too far apart, they might be interpreted as two individual clicks rather than as one double-click.
Double-clicking is most often used to open items on your desktop. For example, you can start a program or open a folder by double-clicking its icon on the desktop.
Right-clicking
To right-click an item, point to the item on the screen, and then press and release the secondary button (usually the right button).
Right-clicking an item usually displays a list of things you can do with the item. For example, when you right-click the Recycle Bin on your desktop, Windows displays a menu allowing you to open it, empty it, delete it, or see its properties. If you are unsure of what to do with something, right-click it.
C) SCANNING DEVICESAre devices that capture an object or a document directly from the source. They are classifie according to the technology used to capture data e.g. Scanners and Document readers.
i) ScannersUsed to capture a source document and converts it into an electronic form.
Example are - FlatBed and HandHeld scanners.


ii) Document readersAre documents that reads data directly from source document and convey them as input in the form of electronic signal. e
Types of Document Readers
i) Optical Mar Reader (OMR)
ii) Barcode readers

iii) Optical Character Readers
b) Magnetic Readers Reads data using magnetic ink.t uses principle of magnetism to sense data which have been written using magnetised ink.
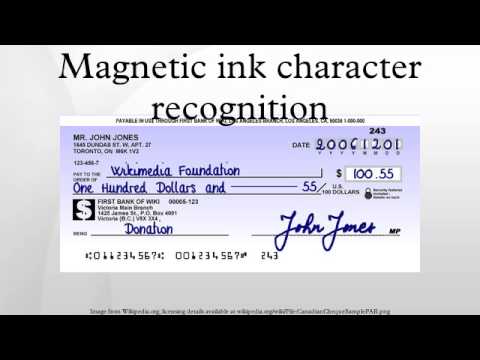
THE CENTRAL PROCESSING UNIT ( C P U)
Is the brain or the heart of a computer. Is also known as processor and consist of three units namely -
i) Control Unit ( C U)
ii) Arithmetic logic Unit ( A L U)
iii) Main Memory unit ( M M U)

The system unit is the core of a computer system. Usually it's a rectangular box placed on or underneath your desk. Inside this box are many electronic components that process data. The most important of these components is the central processing unit (CPU), or microprocessor, which acts as the "brain" of your computer. Another component is random access memory (RAM), which temporarily stores information that the CPU uses while the computer is on. The information stored in RAM is erased when the computer is turned off.
i) ScannersUsed to capture a source document and converts it into an electronic form.
Example are - FlatBed and HandHeld scanners.

ii) Document readersAre documents that reads data directly from source document and convey them as input in the form of electronic signal. e
Types of Document Readers
i) Optical Mar Reader (OMR)
ii) Barcode readers
iii) Optical Character Readers
b) Magnetic Readers Reads data using magnetic ink.t uses principle of magnetism to sense data which have been written using magnetised ink.
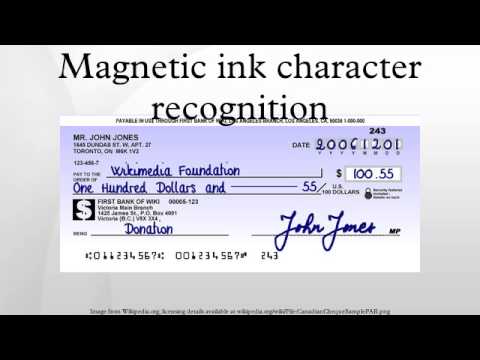
THE CENTRAL PROCESSING UNIT ( C P U)
Is the brain or the heart of a computer. Is also known as processor and consist of three units namely -
i) Control Unit ( C U)
ii) Arithmetic logic Unit ( A L U)
iii) Main Memory unit ( M M U)
The system unit is the core of a computer system. Usually it's a rectangular box placed on or underneath your desk. Inside this box are many electronic components that process data. The most important of these components is the central processing unit (CPU), or microprocessor, which acts as the "brain" of your computer. Another component is random access memory (RAM), which temporarily stores information that the CPU uses while the computer is on. The information stored in RAM is erased when the computer is turned off.
Almost every other part of your computer connects to the system unit using cables. The cables plug into specific ports (openings), typically on the back of the system unit. Hardware that is not part of the system unit is sometimes called a peripheral device. Peripheral devices can be external such as a mouse, keyboard, printer, monitor, external Zip drive or scanner or internal, such as a CD-ROM drive, CD-R drive or internal modem. Internal peripheral devices are often referred to as integrated peripherals. There are two types according to shape: tower and desktop.


Tower System Unit Desktop System Unit

Tower System Unit Desktop System Unit
A motherboard (mainboard, system board, planar board or logic board) is the main printed circuit board found in computers and other expandable systems. It holds many of the crucial electronic components of the system, such as the central processing unit (CPU) and memory, and provides connectors for other peripherals.
Motherboard
TYPES OF PROCESSORS
I) Comples Instruction Set Computers (CISC)
ii) Reduced Instruction Set Computers (RISC)
FUNCTIONS OF CENTRAL PROCESSING UNIT
- Process data
- Control sequence of operaions within the computers
- It gives command to all parts of a computer
- It control the use of the main memory in storing of data and instructions
- it provides temporary storage (RAM) and permanent storage(ROM) of data
THE CONTROL UNIT
Is the center of operations for the computer system, it directs the activities of the computer system.
TYPES OF PROCESSORS
I) Comples Instruction Set Computers (CISC)
ii) Reduced Instruction Set Computers (RISC)
FUNCTIONS OF CENTRAL PROCESSING UNIT
- Process data
- Control sequence of operaions within the computers
- It gives command to all parts of a computer
- It control the use of the main memory in storing of data and instructions
- it provides temporary storage (RAM) and permanent storage(ROM) of data
THE CONTROL UNIT
Is the center of operations for the computer system, it directs the activities of the computer system.
H. XO signal is active or passive
_______________________________________________
Example 1: Your device outputs a 4…20 mA signal which is measured by a PR module.
- Disconnect the two current loop wires from the PR module input terminal.
- Using a voltmeter, measure for DC voltage present on the wires.
- If no voltage is present, then your device is creating a passive current signal. This means a loop excitation source, (typically 12...24 VDC), must be used to power the current loop and measure the signal. Many PR modules have an input excitation source which powers a passive current loop, allowing our module to both measure and energize your device.
- If you measure voltage on the wires, (typically 12...24 VDC), then the current signal created by your device is active. Do NOT use our loop excitation source when measuring an active current signal.

Example 2: A PR module outputs a 4…20 mA signal which is measured by your device.
- Disconnect the two current loop wires from our output terminal.
- Using a voltmeter, measure for DC voltage present on the wires.
- If no voltage is present, then your device has a passive input. Therefore, the PR module must provide the excitation source needed to power and regulate current flow on the loop.
- If you measure voltage on the wires, (typically 12...24 VDC), then your device has an active input. Therefore, the PR module should only regulate the level of current flowing through the loop, it should NOT power the loop.

List of PR devices by active/passive input and output measurement type

A PR module that measures:
- an active input signal, simply measures the active input current. It does not excite the loop.
- a passive input signal, excites the current loop, excites other loop powered devices wired in the loop, and measures the current.
A PR module the creates:
- an active output signal, regulates the current level, excites the current loop, and excites other loop powered devices wired in the loop (e.g. a loop powered display). As an example, the output from the PR module can be connected directly to a passive input card on a PLC.
- a passive output signal, only regulates the loop current level. The loop is powered by an external excitation source. As an example the output from the PR module can be connected directly to an active (powering) input card on a PLC.
Signal Conditioners Information
Signal conditioning is a set of operations performed on a signal that makes it suitable for interfacing with other devices or systems. Signal conditioners are the actual devices that perform this operation. These devices have an input and an output. Normally the input is a sensor that measures a variable, not necessarily and electrical signal.
The signal conditioning process is also known as a transfer function because the final effect is to convert an input signal (or measurement) into a suitable output signal. For instance, when a temperature sensor measures the temperature of a system or environment, the output of the sensor (temperature) is not suitable to be an input signal to an electrical system. Therefore, the temperature measurement must be converted into an electrical signal.
The following diagram shows the evolution of a signal from the sensor through the central processing unit and to the output or load:
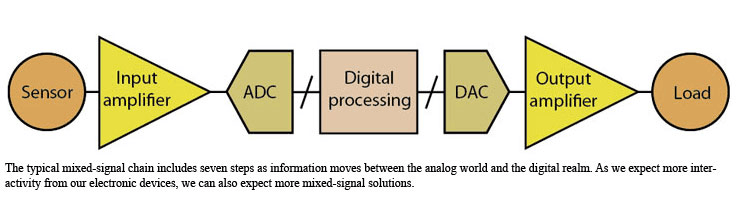
Signal Conditioner Functions
Signal conditioners provide filtering, amplification, converting, and/or other processes required to make sensor outputs suitable for reading by computer boards. They are used primarily for data acquisition, in which sensor signals must be normalized and filtered to levels suitable for analog-to-digital conversion. The digital signal is then available to be analyzed or interpreted by a computerized device.
Filtering
Filters can be constructed from either active or passive components. A passive filter uses only resistors, capacitors, and inductors with a maximum gain of one. An active filter uses passive components and active components like operational amplifiers and transistors. They have a higher gain with sharper frequency response curves.
The filter architecture can be analog or digital.
Analog (RC) - Analog filters are designed with resistors and capacitors. They are used for analog signals only, and are often used in low-noise requirement applications.
Digital (FIR, IIR) - Digital filters are designed with solid-state components and used for digital signals and quantized signals from a sample-and-hold amplifier. This category includes finite impulse response (FIR) and infinite impulse response (IIR) filters. Digital filtering can approach ideal bandpass characteristics.
Filter Type
The function of the filter is to separate the signal's frequency spectrum into valid data while blocking noise. The standard types of filter responses are low-pass, high-pass, band-pass, and band-reject (or notch filter). Filters are selected based on the frequency of the signal to be analyzed.
Low-pass filters block high frequency components; or allow the passage of low frequency signals. A simple passive low-pass filter can be constructed with only a resistor and a capacitor.
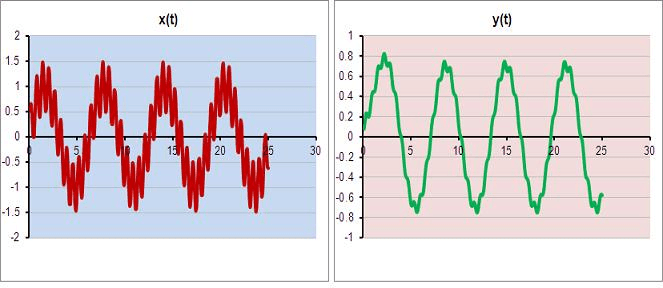
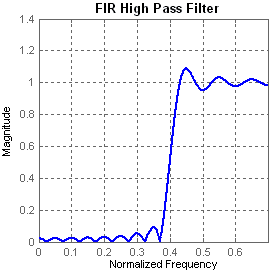
Band-pass filters allow the passage of signals within a range of frequencies and blocks signals with frequencies below the smallest frequency in the range and above the highest frequency in the range. If the range (band) of frequencies is between f1 and f2 then the filter allows the passage of signals with frequencies between f1 and f2 only.
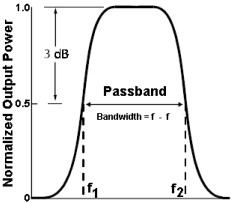
Band-pass Filter Response
Image Credit: Electronic Engineering Dictionary
Band-notch filters, also known as a band-reject filters, allow the passage of all frequencies with the exception of signals within a range of frequencies.

Amplification
Amplification is a process which increases (amplifies) the signal for possessing or digitization. Signal amplifiers often include electronic components that amplify signals without producing significant amounts of thermal noise. In some applications a signal must be amplified or attenuated in order to drive a circuit or a system. There are many types of amplifiers used in signal conditioning including the following:
- Voltage followers have a unity gain, so the output signal is a reproduction of the input signal. This type of amplifier is mainly used as an impedance matching device.
- Isolation amplifiers are designed specifically to isolate high DC levels from the data acquisition device while passing the relatively small AC or differential signal. The inputs and outputs are electrically isolated.
- Instrumentation amplifiers are differential amplifiers that have been optimized for use with DC signals. They are characterized by high gain, high common mode rejection ratio (CMRR), and high input impedance.
- Sample-and-hold amplifiers freeze analog voltage instantly. During this process the HOLD command is issued and analog voltage is available for an extended period.
Signal Converting
In many instances it is required to convert a signal from one type to another, in order to accommodate the driving input of circuits. Some important signal converters are:
- Current-to-voltage converters scale and convert current signal input to the desired output voltage range.
- Voltage-to-frequency converters accept a voltage signal and convert its analog level to a signal with a corresponding frequency.
- Frequency-to-voltage converters accept a signal and convert its frequency to a corresponding analog voltage level.
- Current loop converters convert an analog or digital signal to a current loop output such as 4-20 mA or 0-20 mA.
- Charge converters convert the charge output from a piezoelectric, capacitive or other charge-producing sensor to a signal such as analog voltage or current.
Digital Conversion
Data acquisition is the digitizing and processing of multiple sensor or signal inputs for the purpose of monitoring, analyzing and/or controlling systems and processes. Analog sensors and signals are first normalized by the use of filters, amplifiers and signal converters. The next wave of the signal chain is the exchange of this signal to a digitized format. The two most important conversion functions in this phase of the process are analog-to-digital conversion and digital-to-analog conversion.
Analog-to-Digital ConverterAn analog-to-digital (ADC) converter is a device that accepts, as input, an analog signal and at the output, produces an equivalent digital signal. Most of our sensors and transducers produce analog signals that have to be converted to digital signal in order to be processed by computers or other digital device. There are several types of analog-to-digital (ADC) converters including: direct conversion, successive-approximation, integrating and sigma-delta ADCs.
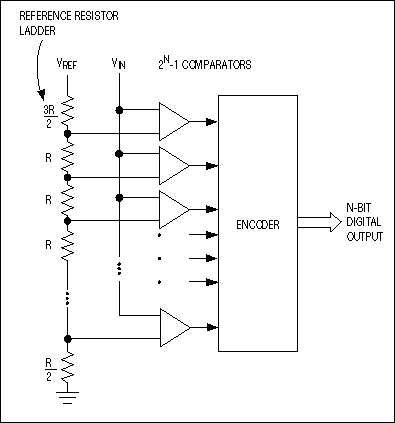
Digital-to-Analog Converter A digital-to-analog (DAC) converter produces the reverse operation of an ADC. These devices accept digital signals and convert them to analog signals (normally voltages).
Selection Criteria
After defining the function of the signal conditioner, the form factor, device specifications, signal inputs, sensor inputs, excitation, outputs and user interface are important parameters to consider when searching for signal conditioners.
Form Factor
Common form factors for signal conditioners include circuit board, panel or chassis mount, modular bay or slot system, rack mount, DIN rail, and stand-alone.
- Printed circuit boards(PCBs) attach to enclosures or plug into computer backplanes.
- Panel or chassis mounts are used to install the device in cabinets, enclosures, or panels with bolts.
- Modular style units include stackable units that dock in bays, slots, or boxes.
- Rack units that fit inside a standard 19” telecommunications rack.
- Devices can be designed for mount on a Standard Deutsches Institute for Normung (DIN) rail, which is a German standard.
- Benchtop or freestanding devices often feature full casings or cabinets and integral interfaces.
Device Specifications
Device specifications that are important to consider when searching for signal conditioning products include analog input channels, digital I/O channels, and accuracy.
Analog signals are a wave signal which means that the value changes steadily over time and can have any value in a range. Signal converters with analog inputs can have multiple channels. Channels are either single-end or differential.
Single-end inputs have only one low wire shared by all inputs. For example a board could have 2 single-end inputs; there will be two input lines and one ground line. Single-end inputs are less expensive and allow for twice the number of inputs in the same size wiring connector since they only require one analog input and one ground input which is shared by all the inputs. They save space and are easier to install. When single-ended outputs are available, suppliers often specify the maximum number of analog channel outputs as twice the number of differential outputs.
Differential channels have two inputs. The voltage is the signal processed between the two inputs. The board will have one signal and one ground pin for each input to allow for measurement voltage difference between two signals tied to the same ground. Differential channels provide excellent common-mode noise rejection. This type of input should be used when EMI, RIF or noise is present.
Digital signals do not have 'in between' values. They are an on or off signal producing a square wave. Digital signals break down the information into binary code, which is a series of 1sand 0s. The data receiver reassembles the code into useful information. Digital signal allows users to send more information in a smaller space.
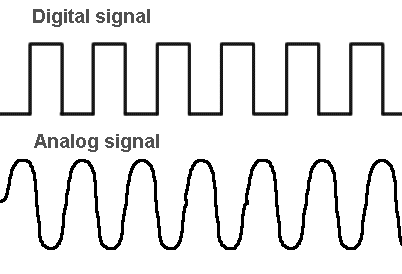
Analog and Digital Signals Compared
Image credit: Being Ministry
Accuracy is defined as the difference (error) between the true value and the indication expressed as percent of the span. Accuracy, which is represented as a percentage of a full-scale measurement range, depends on signal conditioning linearity, hysteresis, and temperature considerations. It includes the combined effects of method, observer, apparatus and environment.
Static accuracy is the combined effects of Linearity, Hysteresis, and Repeatability. It is expressed as +/- percentage of full scale output. The static error band is a good measure of the accuracy that can be expected at constant temperature.
- Linearity is the deviation of a calibration curve from a specified straight line. One way to measure linearity is to use the least squares method, which gives a best fit straight line. The best straight line (BSL) is a line between two parallel lines that enclose all output vs. pressure values on the calibration curve.
- Repeatability is the ability of a transducer to reproduce output readings when the same pressure is applied to the transducer repeatedly, under the same conditions and in the same direction.
- Hysteresis is the maximum difference in output at any pressure within the specified range, when the value is first approached with increasing and then with decreasing pressure. Temperatures hysteresis is the sensor's ability to give the same output at a given temperature before and after a temperature cycle.
Hysteresis
Image credit: Showa Measuring Instruments Co. LTD
Signal Inputs
The input signal can have a variety of specifications as it enters the converter. The type of converter selected depends largely on the type of input signal from the system and the desired output signal. The input signal could have properties such as:
- DC type voltage and/or current
- AC type voltage and/or current
- Frequency waveforms for varying frequency, pulse or specialized waveforms.
- Chargewhich comes from a piezoelectric device and usually requires conditioning.
Sensor Inputs
Sensor inputs can be accelerometer, thermocouple, thermistor, RTD, strain gauge or bridge, and LVDT or RVDT. Specialized inputs include encoder, counter or tachometer, timer or clock, relay or switch, and other specialized inputs.
Excitation
Sensors can be classified as either active or passive devices. Passive devices like thermocouples can generate a signal without a power supply. Active sensors need a power supply in order to control the flow of electrons and make a measurement. In some cases active sensors are powered by the signal conditioner. The output from the signal conditioner that powers the device is referred to as an excitation source. Signal excitation can either be a voltage or current output. The following schematic showcases how an excitation voltage powers a Wheatstone bridge:
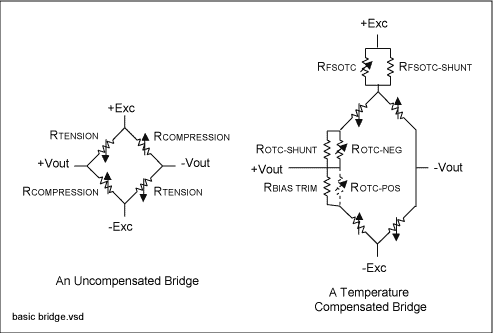
Outputs
Outputs for signal conditioning products can be voltage, current, frequency, timer or counter, relay, resistance or potentiometer, and other specialized outputs.
User Interface
Signal converters have several user interfaces available that allow the user to make adjustments to the system.
- A front panel is a local interface with integral controls, a keypad, and/or display on the panel of the unit
- Computer programmable converters are interfaced with a separate supervisory or host computer.
- Touch screens have a visual display which interacts with the user through touch. The user can directly put in information through the contact-sensitive screen.
- Remote and handheld devices can be mobile while the user enters program parameters.
++++++++++++++++++++++++++++++++++++++++++++++++++++++++++++++++++++++
e- form of a signal on an electronic sensor and then various types of signal input on electronic equipment
++++++++++++++++++++++++++++++++++++++++++++++++++++++++++++++++++++++
Tidak ada komentar:
Posting Komentar