
In the era of the century before the century the warehousing was still from around the accumulation of food ingredients in barns of food such as grain barns - rice barns - barns and so on which aimed at storing food for certain seasons in human life in order to walk and all it still depends on natural processes and from the results of human activities which have not yet been categorized as business activities but are still in the form of activities to defend themselves, namely for the needs of community and royal life or for logistical needs of war between tribes and beliefs. but at this time, after or after the occurrence of additional functions than warehousing, namely for the purpose of storing goods produced as well as for national security of a country. the addition of additional functions from this warehousing in the 19th century and the 20th century became an essential limitation where humans have experienced life which has not been dependent on climate and environmental atmosphere but began by managing the environment so that the living system in a country and royal kingdom got something better of course we know the increasing number of people and the increasing number of countries on earth. and the trading process with more and more items is increasingly complex. whereas in the 21st to the 22nd century, commercial transaction processes have been influenced by electronic systems where transactions of many production items needed by many people are managed properly and efficiently and effectively so that quality and quantity can be increased, in the process of modernizing warehousing this warehouse in modern times should have been reduced because warehouses are a source of additional costs which are like costs that can indirectly increase the cost of goods sold where the price of manufactured goods will be more expensive and sources of bureaucratic and corruption costs if in countries with electronic technology which is not yet qualified due to transactions still from hand to hand and the recording is still manual and the process of receiving and sending goods manually. in this modern era the warehousing process has begun to be reduced by the on-line marketing which by this process the goods of production can be quickly sent and purchased as well as the process of financial transactions that are fast and appropriate in accordance with the price of the goods produced. so I explained briefly about warehousing --- now - and the future.
LOVE ( Line On Victory Endless )
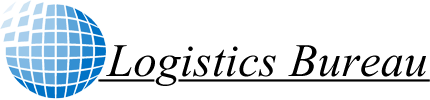
( Gen. Mac Tech Zone e- Bridge Warehouse )
_____________________________________
ADAPTER : 913204710250017
Warehouse is a room that is usually used to store goods that are generally in large quantities and are generally owned by companies in the manufacturing field. The types of goods stored in warehouses are very diverse, but usually stored in there are raw materials or merchandise supplies. Do you know? This warehouse is actually part of logistics activities whose functions are not only limited to storage, but there are other important things
The importance of warehouses in business continuity cannot be underestimated. Although it does not have a building for its own warehouse, several companies are willing to rent a place to be used as a storage warehouse. The warehouse function in the company is as follows :
• Assembling
Warehouse does have a main function as a storage place, but some companies also use it as a place to assemble, namely to assemble products ordered by clients or consumers.
• Dispatching
Another function is as dispatching for storage and shipping. With this the production process of an item can be controlled and in accordance with the schedule set.
• Inbound & Outbound Consolidation
The company uses warehouses as well as inbound and outbound consolidation. Inbound consolidation is a process where goods are consolidated first in the storage space before entering the production process. Whereas outbound consolidation is placing goods produced and consolidated before they are later handed over to customers.
• Maintaining Record
The warehouse is used as a storage place that serves to carry out product maintenance. Especially if the merchandise owned by the company does need to be placed in a good room so that the quality of the goods is maintained.
• Packaging
Warehouses are also used for packing a product before being delivered to customers. In the warehouse also the order selection is carried out before proceeding to the next process. In this storage room sorting activities are also carried out and inspection of goods in containers until they are sent to customers.
Looking at the warehouse functions above, of course you understand why warehouse management is an important aspect of running a business. Warehouse is actually not a mere stock business, but also can spread to other management including financial management of a company. Good warehouse management can help reduce production costs indirectly. Also read the article following the importance of financial management to gain profit in business. When production costs can be reduced, the profit generated can also be increased.
+++++++++++++++++++++++++++++++++++++++++++++++++++++++++++++++++++++++++
The following are some things that can be obtained by the company if the warehouse management is carried out properly:
• Reducing the risk of loss
With good warehouse management, you will also reduce the risk of future losses. The risk of loss in question is such as damage to merchandise that is stored too long to reduce logistics costs. Warehouses that are in place as transit, distribution and consolidation terminals can be utilized properly according to their functions if warehouse management is carried out properly.
• Able to Meet Faster Requests
With a good warehouse management system, the company can meet client demand faster. Sudden requests can also be fulfilled if the warehouse is properly managed. Shipping goods and checking or sorting goods can also be done faster if the company has good warehouse management.
• Can Present Stock Information in Real Time
Warehouse management also encourages the presentation of stock information in real time. You can find out the number of stocks, how many stocks have been damaged and how many units are still in process until the finished ones. You are able to calculate the cost in more detail and in accordance with the data in the field. This certainly makes it easier for you to compile and read related reports.
• Able to Determine Inventory and Re-Order More Precisely
Proper warehouse management can also help companies determine when to re-order inventory. The warehouse management system is able to estimate more precisely how much inventory is needed. That way the company will not experience shortages or excess stock in the future. In this way, not only inventory management is maintained, but the financial condition of the company is also saved because it is able to avoid excessive expenditure of funds to purchase inventory.
• As Material for Consideration in Taking Company Policy
Information related to warehouses is also needed to take policy in the company, especially in terms of production and logistics. Warehouse information is needed to determine the cost of goods sold which will be used to calculate the profit and loss obtained by the company. Warehouse data is also needed as a comparison with previous data in order to take the right company policy.
• Reducing fraud that might occur
Warehouse management is also needed to identify fraud and negligence that may occur in the company. Warehouse management can be used as a form of supervision, control and planning of existing inventory.
The following are some things that can be obtained by the company if the warehouse management is carried out properly:
• Reducing the risk of loss
With good warehouse management, you will also reduce the risk of future losses. The risk of loss in question is such as damage to merchandise that is stored too long to reduce logistics costs. Warehouses that are in place as transit, distribution and consolidation terminals can be utilized properly according to their functions if warehouse management is carried out properly.
• Able to Meet Faster Requests
With a good warehouse management system, the company can meet client demand faster. Sudden requests can also be fulfilled if the warehouse is properly managed. Shipping goods and checking or sorting goods can also be done faster if the company has good warehouse management.
• Can Present Stock Information in Real Time
Warehouse management also encourages the presentation of stock information in real time. You can find out the number of stocks, how many stocks have been damaged and how many units are still in process until the finished ones. You are able to calculate the cost in more detail and in accordance with the data in the field. This certainly makes it easier for you to compile and read related reports.
• Able to Determine Inventory and Re-Order More Precisely
Proper warehouse management can also help companies determine when to re-order inventory. The warehouse management system is able to estimate more precisely how much inventory is needed. That way the company will not experience shortages or excess stock in the future. In this way, not only inventory management is maintained, but the financial condition of the company is also saved because it is able to avoid excessive expenditure of funds to purchase inventory.
• As Material for Consideration in Taking Company Policy
Information related to warehouses is also needed to take policy in the company, especially in terms of production and logistics. Warehouse information is needed to determine the cost of goods sold which will be used to calculate the profit and loss obtained by the company. Warehouse data is also needed as a comparison with previous data in order to take the right company policy.
• Reducing fraud that might occur
Warehouse management is also needed to identify fraud and negligence that may occur in the company. Warehouse management can be used as a form of supervision, control and planning of existing inventory.
How to Build Correct Warehouse Management?
+++++++++++++++++++++++++++++++++++++++++++++++++++++++++++++++++++++++++
Without disregarding financial management, this article is made so that companies are increasingly aware of the importance of managing warehouses properly. Good warehouse management does not only depend on the budgeting control over inventory but also maintenance of the inventory itself.
This means that how to store inventory is very important not only to regulate how much inventory needs to be bought or produced. The following are steps you can take to build a good and correct warehouse management below:
• Prepare Data on Items that Need to Be Stored
The first step you need to do to build the right warehouse management is to prepare in advance what supplies will be stored in the warehouse. By preparing inventory data as accurately as possible you can calculate how much building is needed for storage.
• Determine Warehouse Location
Next you need to determine the location of the building that will be used as a storage location. Warehouse locations should be easy to access and have a spacious parking area so that vehicles can get in and out easily. The location of the warehouse should be close to the office so that it is easy to do an audit by interested parties.
• Set Inventory Layout
It doesn't stop there, but it also requires setting up inventory layout to make it easier to calculate and search for items later on. Understand the character of the product so that the storage will also be more appropriate. Inventory products can be arranged based on the brand or type of product itself. Inventory categories and sizes also affect the product storage layout. Do not forget too, set the temperature of the warehouse so that it is not too moist or too dry which can have an impact on the condition of the inventory of goods stored.
• Create a Forecast for the Inventory Schedule
After the data collection and laying of the inventory have been sorted out, proceed by making inventory forecast in the required period and proceed with making inventory schedules. This inventory schedule will determine when you should make inventory purchases. The availability of inventory forecast information and inventory schedule will make it easier for you to calculate inventory budgeting for a certain period.
• Use Inventory Software
Management of goods cannot be considered trivial. Especially in a super-sophisticated era like today, fast and accurate information is needed. To meet these needs, inventory software is designed to control the inventory of warehouses owned. The use of inventory software also reduces the risk of human error when inputting data and monitoring. In addition, inventory software is also able to provide real time information and be faster in presenting reports.
This means that how to store inventory is very important not only to regulate how much inventory needs to be bought or produced. The following are steps you can take to build a good and correct warehouse management below:
• Prepare Data on Items that Need to Be Stored
The first step you need to do to build the right warehouse management is to prepare in advance what supplies will be stored in the warehouse. By preparing inventory data as accurately as possible you can calculate how much building is needed for storage.
• Determine Warehouse Location
Next you need to determine the location of the building that will be used as a storage location. Warehouse locations should be easy to access and have a spacious parking area so that vehicles can get in and out easily. The location of the warehouse should be close to the office so that it is easy to do an audit by interested parties.
• Set Inventory Layout
It doesn't stop there, but it also requires setting up inventory layout to make it easier to calculate and search for items later on. Understand the character of the product so that the storage will also be more appropriate. Inventory products can be arranged based on the brand or type of product itself. Inventory categories and sizes also affect the product storage layout. Do not forget too, set the temperature of the warehouse so that it is not too moist or too dry which can have an impact on the condition of the inventory of goods stored.
• Create a Forecast for the Inventory Schedule
After the data collection and laying of the inventory have been sorted out, proceed by making inventory forecast in the required period and proceed with making inventory schedules. This inventory schedule will determine when you should make inventory purchases. The availability of inventory forecast information and inventory schedule will make it easier for you to calculate inventory budgeting for a certain period.
• Use Inventory Software
Management of goods cannot be considered trivial. Especially in a super-sophisticated era like today, fast and accurate information is needed. To meet these needs, inventory software is designed to control the inventory of warehouses owned. The use of inventory software also reduces the risk of human error when inputting data and monitoring. In addition, inventory software is also able to provide real time information and be faster in presenting reports.
+++++++++++++++++++++++++++++++++++++++++++++++++++++++++++++++++++++++++
In an era that has been very advanced as it is today, starting a lot of emerging inventory software that can help in warehouse management in the company that you founded. You can do research first before determining which inventory software is your choice. The following are some of the advantages of inventory software that you need to know:
• Able to do automatic calculations
Inventory software has the ability to automatically calculate inventory. You can find out the amount of inventory in real time and accurately. Not only that, you can even know the history of the inventory of goods listed.
• Get Price Information in Real Time
Software inventory will help you obtain information on the price of inventory so that the company is easier to set the desired profit. In addition, recording inventory stocks can also be made easier by using this inventory software.
• Facilitate Audit
Software inventory also helps the auditor's work in auditing the company's inventory. Not only that, the inventory software also helps in controlling the movement of inventory and the needs of document documents.
• Minimizing Time and Costs
Another advantage of inventory software is being able to minimize time and costs due to human errors. The time used to calculate inventory is faster because it is done automatically so that stock taking is faster and less complicated.
• Safer and Integrated Data Storage
The use of inventory software is able to provide much greater storage space than by manual method. You can also see the history of each desired inventory and make a report faster than by manual method. Checking is also much faster and can monitor stock items online.
• Effective and Dynamic
Using inventory software makes your company work more dynamically and effectively related to inventory. The profit generated can also be more optimal and the company's performance can also be optimal. Plus customer satisfaction also increases with fast handling of their needs.
++++++++++++++++++++++++++++++++++++++++++++++++++++++++++++++++++++++++
Of course, in choosing inventory software you should not just choose it as long as you choose. The ideal inventory software is not dependent on the latest technology but conformity to the needs of the company itself. The following are some of the things you should pay attention to in choosing inventory software:
•Price
The price of an inventory software is actually diverse and there are enough choices available on the market. But you need to know that not all cheap digital products have poor quality, and vice versa. It would be better if you buy inventory software according to your needs and budget.
• Features
Each software certainly has its own advantages with each other. The usual difference lies in the features used. If your inventory has various types of inventory and is complex, use a lot of customization software.
• User Friendly
No matter how sophisticated the software is if it is not user friendly it will certainly be useless. Try to buy inventory software that is not only sophisticated and has many features, but is also user friendly so it's easy for anyone to use.
• Flexible and Integrated
An inventory software must be flexible so that it can be accessed easily. The software must also be compatible with devices in your office. Especially if you have a lot of shops, of course it's important to prioritize the flexibility and integrity of a software.
A good inventory software must certainly meet the service needs that you and the company need. One recommended inventory software is Unleashed.
Unleashed is one of the advanced inventory software that does not need to doubt its capabilities. This software is the right inventory solution for various types of companies such as manufacturing, distributors, wholesalers to e-commerce retailers.
Unleashed has many advantages as follows:
• Reporting and inventory control in real time.
• Have a mobile sales application making it easier.
• Able to calculate product costs accurately.
• Can be used for product tracking.
• Can be used to manage several warehouses at once throughout the world.
•Price
The price of an inventory software is actually diverse and there are enough choices available on the market. But you need to know that not all cheap digital products have poor quality, and vice versa. It would be better if you buy inventory software according to your needs and budget.
• Features
Each software certainly has its own advantages with each other. The usual difference lies in the features used. If your inventory has various types of inventory and is complex, use a lot of customization software.
• User Friendly
No matter how sophisticated the software is if it is not user friendly it will certainly be useless. Try to buy inventory software that is not only sophisticated and has many features, but is also user friendly so it's easy for anyone to use.
• Flexible and Integrated
An inventory software must be flexible so that it can be accessed easily. The software must also be compatible with devices in your office. Especially if you have a lot of shops, of course it's important to prioritize the flexibility and integrity of a software.
A good inventory software must certainly meet the service needs that you and the company need. One recommended inventory software is Unleashed.
Unleashed is one of the advanced inventory software that does not need to doubt its capabilities. This software is the right inventory solution for various types of companies such as manufacturing, distributors, wholesalers to e-commerce retailers.
Unleashed has many advantages as follows:
• Reporting and inventory control in real time.
• Have a mobile sales application making it easier.
• Able to calculate product costs accurately.
• Can be used for product tracking.
• Can be used to manage several warehouses at once throughout the world.

AB. WXO Modern Warehouse Management In The Era Of Customer Centricity
It is all about the customer. Whether discussing product innovation, shop floor processes or IT investments, the underlying priority is likely to be related to customer alignment. Building customer relationships is the key to repeat sales, brand loyalty and products which are immune to commoditization and price wars. This customer focus applies to warehouse priorities too. And, despite increasing complexities in inventory management, software solutions can help manufacturers optimize processes to support a customer-centric approach.
Defining the Complexities
Warehouse management is increasingly complex. Not only are manufacturers inventorying larger numbers of SKUs, those products tend to have compressed life cycles with high tech components that quickly slide into obsolescent doom. A global supply chain providing raw resources, the need for traceability of components and strict regulations around storage conditions all add to the mounting list of pressures manufacturers face. The most challenging obstacle, though, is the increased demand for highly personalized products. How can a manufacturer possibly stock all of the variations of style, dimensions, materials, finishes and accessories associated with modern product lines?
Even business-to-business manufacturers and fabricators must contend with customers who want to submit customized specifications for industrial products, machinery and electronic parts. Creating unique products which can’t be easily knocked-off by aggressive competition is often the goal. Or, the objective may be to provide major accounts with extra attention. No matter the reason, the reality is an avalanche of Engineer to Order (ETO) and Make to Order (MTO) products. And, they all need shelf space, unique IDs and a place in the system.
Setting Priorities for Change
Organizations today have to make difficult decisions about priorities and determining the projects that merit phase-one funding. Inventory management is one of the most pivotal areas impacted by innovation, yet one that is often overlooked and underestimated for its value when it is time to allocate funds. But, pausing to recognize the significance of readily available raw resources, parts and components helps managers see why investing in smart inventory management solutions is a critical part of keeping customers happy.
When picking a starting point for IT investment, manufacturing executives often automatically turn to the shop floor, concentrating on industrial machinery, workflows, sensor technology and machine maintenance for improvement initiatives. It is easy to overlook the strategic role of inventory management and make the common assumption that the warehouse is just a transitional phase where goods wait to be shipped to their destination. That is hardly the case.
When inventory management is viewed through the lens of customer centricity, the relevance of available inventory, reliable safety stock and parts availability puts a new perspective on priorities. Lack of inventory means processes are delayed, eating away at productivity. When orders cannot ship, customers become angry, eroding loyalty and repeat sales. When service level agreements cannot be met because of missing spare parts, fines are levied and contracts revoked, proving that inventory should be a topic that everyone in the plant considers high priority.
Modern Assembly Demands
Advanced inventory management receives even more emphasis when the manufacturer must manage a large percentage of highly configured, personalized products. Operational tactics, like “hub and spoke” design and late-stage assembly, allow manufacturers to take advantage of modular design concepts with mix and match components. Various systems of a product can be assembled and stored. Final assembly can be postponed until the actual order is received. Then, the right finishes, accessories and details can be added to meet the customer’s exact needs. Assembly tactics such as this are becoming increasingly common as manufacturers cope with customer expectations for specialized products.
Fortunately, advanced inventory solutions help the manufacturer manage this process of storing and staging partially assembled products, components and compatible add-ons. Without highly flexible technology that can adapt to changing situations, chaos would be the new normal. No manufacturer can afford chaos, uncertainty, delays from confusion or gaps in communications from discrepancies in paper-based spread sheets.
Innovation in Thinking
Cross-docking is a practice in modern inventory and logistics operations. Cross-docking allows products which are unloaded from incoming trucks or rail cars to be automatically dispatched to the end destination — without the waste of being put in inventory and then shortly thereafter removed. By storing the products in a staging area or simply reloading them in another transportation vehicle, time and labor can be saved. In cases of less-than-truckload (LTL) shipments, cross-docking simply moves cargo from one transport vehicle directly onto another, avoiding warehousing. In some operations, a staging area can be used to sort inbound materials and store them until the customer’s outbound shipment is complete and ready to ship.
When a manufacturer makes its own components, cross docking capabilities help sync availability and demand, automatically matching the completed goods with open jobs or purchase orders that may be waiting for that component. Such tactics speed processes, streamlining activities and allowing the manufacturer to respond to customer expectations.
Using Scanners and Sensors in the Warehouse
Technology can also be used in the warehouse to improve inventory tracking, reducing errors and speeding pick and pack processes. Barcodes, optical scanners, RFID technology and sensors with GPS tracking can all be used to help warehouse personnel find and pull products from shelves. For manufacturers with thousands of SKUs, hundreds of possible versions, and multi-part kitting requirements, saving time on each order quickly adds up to major cost impact. Even more importantly, accuracy is improved, influencing customer satisfaction.
Next generation solutions can take the advanced inventory system up yet one more level. Wearable technology, voice activated systems and automatic sensor readings all help warehouse personnel concentrate on fulfillment, rather than computer tasks. Some industries even find benefit in deploying driverless forklifts operating on tracks which can quickly move through the warehouse, automatically stopping at correct bins and using robotic arms to pull products. Speed is increased, while also reducing safety issues.
Accuracy Improves Reporting
Improved accuracy is one of the most important ways technology improves inventory systems and helps improve customer satisfaction. Customers hate errors, especially errors in availability, inventory status and projected delivery. Inventory accuracy yields more accurate reporting and analytics, including predictive analytics. The ability to predict needs with confidence means a manager can tighten safety stocks, reducing the amount of inventory kept on hand “just in case” and can practice “just in time” strategies which optimizes space, time and cash flow, while still protecting the customer’s needs.
Accurate inventory of spare parts is also critical to aftermarket service, performing preventive maintenance and fulfilling service contracts with customers. Maintenance, whether on internal equipment or on customer-owned assets, requires inventory of replacement parts and routine consumables like lubricants, ink, filters and belts. Errors in inventory can be disastrous. Planning the projected need for replacement parts can be enhanced by smart Data Science using purchase data to project when replacements will be needed.
Warehouse management may seem like the last stop on the journey toward to the customer, so not critical. This is wrong. Inventory management is a critical part of customer centricity. It is complex, fraught with obstacles, and cluttered with expectations around product personalization. At the same time, it also offers a huge opportunity. When the warehouse management exploits technology, it can be an important differentiator. Inventory management can be a strategic part of the enterprise’s strategy to improve customer loyalty. The warehouse deserves priority status when allocating funds.
+++++++++++++++++++++++++++++++++++++++++++++++++++++++++++++++++++++++++
BC. WXO Innovative Warehouse Management Technologies to Adopt
When it comes to warehouse management, constant evaluation and adoption of crucial technologies is critical so as to improve profitability and stay competitive. Today, warehouse managers have a wide array of technologies to choose from as they strive to reduce costs, improve efficiency and streamline operations. They must ensure that goods, materials and products flow effortlessly by optimizing their warehouse operations through the use of warehouse technologies. What are some of the latest technologies being used in warehouse management today?
Machine-to-Machine Technology
Over the last few years, machine-to-machine technology, or M2M, has greatly evolved into more sophisticated systems that help monitor and streamline all automation aspects of warehouse operations. When combined with warehouse management systems (WMS), the latest M2M systems are making it easier to control all equipment within the warehouse that is vital to the order fulfillment process.This technology helps collect and trade information that provides warehouse managers with actionable information that can verify operational procedures and expedite decisions.
Order Fulfillment Optimization Technology
Every warehouse should consider introducing the latest order fulfillment technology in the market. Different warehouse technology solutions are available to help maximize order picking productivity and boost accuracy. There are two main solutions: Pick-by-Light and Put-by-Light. These technologies help automate warehouse processes and offer a more efficient and lower cost solution over manual picking methods.Pick-to-Light Systems
These systems use specific light displays to direct warehouse operators to product locations. They make it easier for operators to know which to products to pick and how many. These systems are highly flexible and the technology comes with the ability to plan, control and analyze volumes of orders picked.Benefits of Pick-to-Light Systems:
- Increased picking productivity
- Better accountability
- Real-time product or order sorting
- Fewer errors
Put-to-Light Systems
This technology helps direct operators how and where to allocate products in a warehouse for orders. These systems are highly efficient when it comes to picking from bulk stock. The technology is ideal for retail warehouses that deal with apparel, sporting goods, personal care items, convenience foods, groceries and general merchandise.Benefits of Put-to-Light Systems:
- High-speed order sorting capability
- Lower cost operation
- Ideal for smaller but consistent daily orders
- Requires less floor space
Warehouse Robotics Technology
New robotics technology has become one of the most sought after technologies for warehouse management. Leading-edge manufacturers are partnering with providers of warehouse management systems to create customized software and smart robots that help manage the movement, storage and sorting of warehouse inventory.Investing in warehouse robotics technology will highly benefit you. With increasing order volumes, numerous products to navigate, highly personalized order packing and faster shipping requirements, robotics solutions will help you effectively respond to volume growth and perform more tasks with less labor and at a lower cost.
Benefits of Warehouse Robotics:
- Reduced operational and labor costs
- Improved productivity
- Higher order accuracy
- Faster cycle times
- Reduced safety incidents
Voice Tasking Technology
This is a hands-free technology that uses spoken commands for picking, putting, receiving, replenishing and warehouse shipping functions. This technology is almost similar to RF technology and is a flexible choice for order fulfillment.Benefits of Voice Tasking Technology:
- Improved picking productivity
- Increased picking accuracy
- Requires less operator training
- Improved system control
- Real-time data analysis and communications
- Higher ROI
Labor Management Systems
To effectively manage and control warehouse operational expenses, warehouse managers have to invest in labor management technologies. Measuring productivity can seem challenging, but investing in labor management systems helps take out the guesswork in this critical measurement. When combined with warehouse management systems, you can easily drive reductions in labor costs.Training is also a critical part of warehouse management. Innovative technology to consider is the use of a learning management system to train warehouse operators regularly. These training systems are designed to be easy to use and create training material and structures that suit your needs.
The Future of Warehouse Management Technology
As more advanced technology is introduced for the warehousing and logistics sectors, it is up to warehouse managers and firms to stay updated on the latest innovations. Upcoming technologies like Pick-by-Vision, Electronic Data Exchange and the use of drones will soon become mainstream in the industry. Implementation of the right technologies will be key to the smooth operations of warehouses and supply chains.+++++++++++++++++++++++++++++++++++++++++++++++++++++++++++++++++++++++++
CD. WXO The Past, Present, and Future of Technology in the Warehouse
Imagine stepping back in time to visit a large warehousing operation in 1990. If it were only possible, such an adventure would really throw today’s distribution center advances into focus.
To save you from a meltdown, let’s take a brief journey through warehouse operating developments from 1990 to 2045. While some imagination will still be required on this journey, most of the hard work has been done in the writing of this article, so you can shut down the imagination overdrive and cruise through this rundown of technology’s impact on warehouses and distribution centers.
1990: A Fine Vintage for Warehouse Operators
Welcome to our tour of a logistics warehouse in the late 20th century. Pay attention as we move through the building, because while a lot of things are different to the warehouse of today, many of them appear subtle to the eye, but have huge meaning in terms of warehouse efficiency and productivity.Perhaps the first thing you’ll notice is just how many people there are. See that supervisor over there, distinguished from the operatives by his different coloured hi-vis vest? Look! There’s another supervisor, and another over there, although you can hardly see her for all the operatives moving among the pick faces in that aisle.

That’s probably one of the first differences you’d notice between a warehouse of today and that of 25-plus years ago – and of course it’s down to technology.
Today’s warehouses need fewer operatives and hence, fewer line managers, because certain labour-reducing technologies have either made labour more efficient or eliminated it altogether. Let’s briefly consider those technologies:
WMS
Warehouse management systems have advanced considerably in the last couple of decades. In the process they have made many warehouse activities faster for people to perform and generated efficiencies to reduce labour-intensiveness. For example:- Paperwork and data entry: WMS has reduced the need for people to spend time completing paper forms or entering data from documents into spreadsheets and other data-management applications.
- Picking efficiency: Warehouse operatives can pick faster with WMS, because the technology helps to organise warehouses more efficiently and (with features such as system-guided picking) enable more efficient working practices to be followed.
- Task Interleaving: As WMS solutions have become more powerful, they have extended the concept of system-guidance across all activities, especially those performed by forklift operators.
Scanning Technologies
In 1990, picking was a task in which a warehouse operative would spend almost as much time recording activities on paper documents as performing the actual task of moving items from pick-face to pallet.Technologies such as barcode scanning and RFID have taken away much of that administration effort, by allowing operatives to simply scan a pick face and enter picked quantities on a keypad.
More advanced solutions even eliminate the data entry altogether, leaving the operative to concentrate solely on the actual picking. Scanning technologies have had a similar impact in other areas of warehouse operation, such as receiving, put-away, and dispatch.
Voice Technology
By adding voice-guidance to the range of WMS functionalities, a warehouse operation becomes even more efficient, as operatives no longer need even to look down at a display to see their work instructions.Instead warehouse staff listens to instructions and respond vocally, so the majority of their attention is always focused on “doing” without the distractions of task identification and recording.
Like other solutions already mentioned, voice technology reduces labour needs in more ways than one. In addition to helping warehouse personnel get more done in less time, it makes human error a less frequent occurrence, in turn reducing the need for labour to be expended on checking and rework.
Warehouse Automation
The mother of all warehouse technologies, warehouse automation has been responsible for more warehouse labour reduction than any other innovation and, as we’ll discuss a little later in this article, is only offering a fraction of its potential thus far.Automated solutions are pervasive, and becoming more so as the technology improves in affordability as well as sophistication. The warehouse of 1990 was typically bereft of automation though, with the exception perhaps of rudimentary (but still important) solutions such as gravity-fed racking or in companies with larger budgets, pick-to-light systems.
Now, back to the tour…
Notice how many people on the warehouse floor have paperwork in their hands? In fact, there seems to be paper everywhere… And look up there in the racking. There are rows and rows of file boxes stored on pallets, presumably containing years of paper records and documents. What a wasteful use of good warehouse cube.
The Paperless Warehouse
Fast forward to the warehouse of today, and you’ll notice far less in the way of paper about the place. WMS software, scanning solutions, and other IT applications in the warehouse have eradicated the vast majority of paper forms and documents from the warehouse environment.
As already discussed, less paperwork is less work full-stop. It also means physical space no longer has to be found for paper storage and archiving.
Warehouse technology has changed data entry processes, enabling data to be entered directly into digital storage and reducing the scope for errors caused by readability problems, lost paperwork, and other issues arising from the translation of handwritten data into electronic bits and bytes.
By removing the need for paper processes, warehouse technology has reduced operating costs (because companies don’t have to spend money on paper, related stationary, or the supply of pre-printed documents). It has also contributed to sustainability, since warehouse operations now place less demand on forestry resources.
A Summary of Our Trip Back in Time
Warehouse management systems, automation, barcode and RFID technologies, and voice guidance systems all combine to make warehouses more efficient, less impactful on the environment, and less reliant on manual labour.Of course if you’ve been involved in warehousing for some years, it’s easy to overlook the huge differences between warehouses of today and those of the late 20th century, so a quick trip back in time would likely prove quite a shock to the system.

Even now, in our less labour-intensive warehouse environments, technological progress continues to disrupt and transform the way we manage inventory storage and throughput. Having taken a look back in time, we should take some time to explore what’s happening in warehouses today before speculating about what the future will bring.
Technology’s Direct Impact on Today’s Warehouses
Now we’re back from 1990, let’s take a look around today’s warehouse, but not one of those in your own organisation. Instead we’ll visit a couple of DCs that you’re not familiar with, to get a broad view of how technology is currently impacting warehouse operations.
First let’s visit this distribution centre run by a medium-sized enterprise. Aside from an absence of people with paper, let’s see what evidence we can find of technological impact.
The Partially Automated Warehouse
This warehouse is fairly advanced in terms of technology, but clearly not at the cutting edge. How do we know that?… Well, for one thing the lights are on, so although we can see some signs of automation, this is clearly a warehouse in which people still play a substantial role.But look, here comes a forklift—without a driver?
Yes, warehouse operations are currently being disrupted by the development of advanced robotic systems, the most basic of which use digital add-on systems to transform forklifts and other types of MHE asset into robots.
A combination of sensors, cameras, lasers, and software can be used to enable forklifts to work alongside people, but without the need for human operators.
Some time ago we published a post about how brewing company Carlsberg uses these automated forklifts to move up to 500 pallets per hour around one of its Swedish distribution centres.
That’s just what we’re seeing here, a prime example of how even more people are being displaced from the warehouse environment by technology. Further examples can be seen if you look around. Over there for instance, you can see a number of pallets on turntables, spinning fast as they are cocooned in shrink-wrap ready for dispatch.
The Fully Automated Warehouse
Now let’s teleport (because we’re using our imaginations, remember?) to a large new distribution centre operated by a consumer goods brand. First let your eyes adjust to the gloom, because there are few lights on here.This is a fully automated high bay warehouse, housing an automated storage and retrieval system (AS/RS). Linked to the centre’s WMS, cranes on rails fly up and down aisles of racks that extend from the floor to giddying heights above.
The cranes extract pallets using forks and transport them at incredible speed to a conveyor system, which will carry them to a dispatch area and straight into waiting trailers.
Automated warehouses certainly seem to be the ultimate in modern distribution centres, needing very few people to operate, offering high levels of productivity (because as well as being fast, they can operate 24/7/365), and offsetting some of the power they use by operating in an unheated or un-cooled environment, with little if any need for artificial lighting.
That being said, full automation is still a big ticket item in terms of capital costs, often requiring customised warehouse construction to house high-bay storage and specialised infrastructure. That’s why it’s rare to see such advanced levels of technology in use by smaller supply chain organisations.
Automated Warehouse Benefits
For companies that can afford it, and operate in sectors compatible with automated logistics, full automation delivers a great many benefits, including:- Significant labour cost reduction
- Superior levels of productivity
- A high degree of efficiency
- Minimal risk of processing errors
- Improved inventory management
- Increased supply chain speed
The IT Impact on 21st Century Warehouses
While automation removes the need for manpower, many companies still consider it either too expensive to implement, or are concerned about the length of time to ROI, which is typically around five years. On the other hand, many software solutions offer a much faster return on investment and are affordable even for smaller businesses.We’ve already discussed WMS, but other IT applications have also been involved in making today’s warehouse operations more efficient and cost-effective.
Sophisticated analytics help operators find and eliminate process weaknesses; Inventory management software helps companies to optimise stock levels, while modeling tools do the same in construction design and warehouse layout planning.
The Indirect Impact of Technology
When considering the impact of technology on warehouses and distribution centres, it would be remiss to overlook disruptive technology in the wider commercial environment. So before moving on to visit the warehouse of the future, let’s briefly reflect on how warehouse operations have been indirectly impacted by technological advances.The biggest of these disruptions has been driven by changes in consumer behaviour, which in turn have been enabled by perhaps the most significant innovation of the last century – the Internet.
As consumers have progressed from shopping online to mobile shopping, they have driven a revolution in retail commerce, which has in turn set off a ripple effect to initiate similar changes in business-to-business trading.

Today it’s all about the omnichannel experience—and that has changed the entire supply chain profile in many industries and commercial sectors. All this transformation has led to a distinct shift in warehouse function, from being a staging point for supply chain inventory, to becoming a vital element of the value chain.
The Expanding role of the Warehouse
Few warehouses today are simply storage spaces, but instead host multiple value-adding processes, like just-in-time packaging, assembly, product customisation, and in some cases, customer collection services.Ironically, the need to add value within warehousing operations has partly slowed the rate at which human operatives become obsolete, since a lot of value-adding tasks require skills that can’t yet be replaced by automation.
The respite however, could be short-lived, as a new wave of disruptive technology emerges—one which many believe will spell the end of the warehouse as a significant source of employment and transform it into a centre of wholly automated activity.
2045 Here We Come

To understand why warehouses may soon be devoid of human presence, we should return to our tour, but instead of jumping straight to the warehouse of 2045, we’ll take a slow sojourn through the next few years to come. Along the way we’ll look at how robotics, sensors, machine-to-machine communication, and the Internet of Everything may make warehouses ever more efficient to operate, while gradually eliminating the need for a human workforce.
Rise of the Robotic Warehouse
In earlier sections of this article, we touched on some of the limitations of current automation technology. To recap, we discussed the need for specialised warehouse infrastructure and the associated cost of constructing purpose-built automated warehouses. We also discovered that some tasks being performed in today’s warehouses require human dexterity and judgment.All that may soon change, as robotics development begins to solve these problems. However, this article isn’t intended to fuel debates about whether replacing warehouse workers with robots is a good or bad thing.
Instead it’s an attempt to look objectively at future possibilities to improve warehouse operations through the use of technology. So let’s move on and do just that.
Robotics is probably the answer to many automation constraints in warehousing. For example, unlike automated storage and retrieval systems, robotic warehouse machinery (even at the current time) is able to operate in any industrial space, meaning it can be deployed in existing warehouses without expensive structural modifications.
At the same time, robotic capabilities are continually improving; with robots being developed that can perform tasks such as dressmaking, which up to now has always required a human touch. They are also becoming increasingly mobile and capable of multitasking, which means companies will need less machinery to perform more activities.
Robotic Opportunities for All?
If you need evidence of robots’ pervasiveness in warehousing, consider the examples of Amazon, which as of December 2016, had 45,000 robots employed across 20 distribution centres, and bulk grocery superstore Boxed, which replaced 75% of warehouse jobs at one fulfillment centre with robotic order pickers.By the time we get to 2045, it’s very possible that human warehouse operatives will be a rare sight indeed, as multi-functioning robots become an affordable investment for many companies. Smaller businesses may access robotic technology too, by contracting with third-party warehouse providers which thanks to robotic advances, will make outsourcing the most economically viable way to stage and store inventory.
But What About the Warehouse?
Of course there is more to a warehouse than the operation it houses, and as time goes on, technology will impact warehouse facilities by changing the way they are constructed, maintained, and powered.Take warehouse lighting for example. If we take a brief hop back to 1990, when you were looking up at all those boxes of papers in the racking, did you notice the forest of light fittings hanging from the ceiling?

Those were probably metal halide, sodium, or florescent lamps, all of which are expensive to run on an industrial level and are constructed using materials harmful to the environment.
These lighting solutions are slowly but surely disappearing from the modern warehouse environment, to be replaced by more economical and environmentally friendly light sources, such as LED and induction lamps.
The cost of lighting warehouses is considerable, since illumination must be bright enough for staff to work productively and safely, so it’s no surprise that companies are quick to take advantage of new lighting technology. LED industrial lighting consumes a fraction of the electricity needed to run conventional lamps, and when combined with management systems using sensors and timers, becomes even more economical.
No Need for Creature Comforts
Moving ahead into the near future, we’re likely to see warehouses make further savings on energy costs as automation takes over. Automated machinery and robots need no ambient lighting to operate, so while lighting may be in place for emergency situations or for service/maintenance purposes, it will seldom be switched on.The cost of artificial temperature control too, will be minimised, since temperatures will only need managing for inventory quality, not for human comfort.
It’s entirely possible that by the year 2045, the warehouse management system will be much more worthy of the title, able to control every aspect of warehouse operation, including security, receiving, put-away, storage, picking, and dispatch, as well as lighting, temperature control, indirect materials purchasing and even some, if not all, maintenance.
The Living, Sensing Warehouse
In the warehouse of 2045, sensor technology will enable everything from mechanical handling equipment, through warehouse robots and storage racks, to the very fabric of the warehouse structure, to monitor conditions and performance.Machine-to-machine communication will enable the sensors to relay data constantly to the warehouse management system, while integrated analytics and machine-learning capabilities enable that system to pass instructions back to warehouse robots (perhaps including aerial drones for certain high-level tasks).
Interpreting those instructions, the robots will respond appropriately to perform basic maintenance and repair tasks on the building, MHE, automated machines, and perhaps even themselves or each other… And so the warehouse of 2045 becomes a virtual living entity, capable of taking care of itself and the operations it houses, with minimal need for human intervention.
While a certain amount of human expertise may still be needed, there’s every chance that warehouse managers and technicians will simply monitor the operational status from their homes, using laptops or tablets, make adjustments as needed, and occasionally respond to more serious situations by riding out in their (probably driverless) cars to get hands-on with machinery or inventory.
Warehouses Get Bigger, Smaller, Fewer?
So now, with the help of this article and a little imagination, you have an idea of what the warehouse operation of 2045 might look like, but what we haven’t yet explored is the possibility that technology may impact the very existence of warehouses.Omnichannel commerce could for example, see warehouses evolve into a combination of mega-centres (hosting operations for multiple companies in shared environments) and urban mini-warehouses, used to place inventory close to target consumer markets.

On the other hand, as technological capabilities develop throughout the supply chain, and techniques such as additive manufacturing make it increasingly possible to produce items on demand, it’s possible that some supply chains may evolve in which warehouses are completely unnecessary. The result could be an overall reduction in the global warehouse footprint.
While we can probably all agree on how warehouses looked in 1985, we each have individual and unique perspectives on today’s use of warehouse technology, typically influenced by the operations that we’re most familiar with.
For example, the views in this article are influenced by the projects we get involved in as a supply chain consulting company, but your company may be using technology in different ways, and your take on future developments may be very different.
+++++++++++++++++++++++++++++++++++++++++++++++++++++++++++++++++++++++++
DE. WXO Supply Chain Management for Aviation Industry
Supply Chain Automation means managing an optimised inventory. It means having the critical equipments in stock and keeping idle items minimised. The Airline Industry are increasingly focused towards reducing their reducing the maintenance costs, keeping a high level of inventory accuracy & deliver high levels of service. Supply chain automation is a great tool to achieve that.
The aviation sector handles items, which are capital-intensive. The items also involve a huge number of components. A lot of these components are moving, creating challenges to track the inventory accurately. The value of the inventory items is in rotable parts. These issues make supply chain management all the more challenging for the aviation industry.
1. Benchmarking and planning of supply chain activities for aviation. The key measures include forecasting the customer requirements, capacity management, analyse the demand patterns, addressing key bottlenecks like hangar space, logistics, engine maintenance etc.
2. Manage Material Request Cycle with complete analysis of requests, days to fulfill the order, delays in processing, warehouse statistics and priority levels etc. The complete lifecycle management can be optimised using SCM tools.
3. Inventory Analysis is used to determine the accuracy of stock, the quantity of items and its values. The aircraft industry is capital intensive with low profit margins; hence keeping an optimised inventory is very important. The value of the stock & the volumes are analysed. The historical records are kept for analysis.
4. Maintenance Operations are scheduled and recorded to keep track of costs. The planned & unplanned maintenance are recorded. The costs for components, time, labour materials etc are taken into account. The cost of ownership also involves effective loss with unplanned maintenance.
5. Vendor & Contract Management is integrated. The supply chain management is particularly complex keeping in mind the global vendor management. Dealing with orders, contracts of vendors from different countries and managing them transparently. The integration of components, materials, structures and systems need to ensure best results to achieve operational success.
6. Track Lifecycle of Aircrafts using SCM. The components and life of the aircrafts are managed with predictive alerts. Know when the component is due for maintenance or is past its useful life with predictive notifications. The items are tracked on a regular basis for proactive replacement of critical items.
7. Invoicing, Bills and stock management can be done with high accuracy. The invoices from multiple vendors in different countries are managed on a single platform. Ensure quality checks, receiving inventory items and processing of bills using an integrated interface.
8. Track & Measure things that matter. Dashboards, key performance indicators are used for planning. The consumption history, maintenance expenses, remaining life of components etc can be used for better capital & operational expenses planning.
The SCM system ensures not only optimised inventory, stock, streamlined procurement and improvised operations. But also results in improved turnaround time from vendors, better warranty and contract managements resulting in overall performance gains for aviation companies. The turnaround time for unplanned maintenance also improves significantly. The gaps between demand & supply can be closed leading to a lean inventory with automated replenishment.
AEROSPACE INVENTORY MANAGEMENT
+++++++++++++++++++++++++++++++++++++++++++++++++++++++++++++++++++++++++
Improve Efficiency (Inventory Management)
Efficiency within the aerospace supply chain is essential in order to maintain profitability
Aerospace Inventory Management is need comprehensive inventory management system increases efficiency by ensuring the right stock is at the right place at the right time. When a more transparent view of the supply chain is available, business becomes less reactionary. Movement of stock can be closely monitored and management can focus resources on proactive inventory planning rather than putting out fires from day to day. It becomes easy to recognize in-service fleet size and location changes. The reliability rate for spare parts becomes simple to comprehend. And, large amounts of data from the Big Data revolution begin to be collected efficiently and effortlessly analyzed to create innovative, knowledge-based strategies that impact the bottom line.
Telematics tracking creates mountains of Big Data useful for inventory planning, and it is becoming increasingly more popular with aerospace manufacturers. This information can be used to drive spare part planning requirements through predictive maintenance. By having the correct parts available when maintenance is planned, aircraft spend less time on the ground. Telematics is still in its infancy but Inventory Management .
Connect Key Players (Collaborative Inventory Management)
Once the groundwork for a solid inventory management solution has been put in place, aerospace companies can continue to reap rewards by sharing future demand plans and inventory across the entire supply chain ecosystem. Similar to retail inventory management in other industries
A collaborative approach between aerospace integrators, MROs, and OEMs, helping pass inventory details seamlessly between entities without delay and allowing everyone involved to speak the same language. Instant feedback from the entire network can drive productivity, profit, and customer loyalty while reducing inventory and risk.
Merge Pricing Capabilities (Price Management)
Inventory management is extremely powerful. But those in aerospace who are even more serious about improving profits will want to take things even further by considering value-based pricing solutions as well. After all, optimum pricing strategies cannot be established without understanding the effects a price change will have on sales and, therefore, both inventory and availability.
Software as a Service (SaaS)
The historical concerns around data security and co-located data has given way to the realization that SaaS is the most cost effective way to deliver, administer and upgrade software. The web-based model not only keeps the total cost of ownership low, but also reduces complexity and aids in transparency by giving users access to real-time accurate information around the clock.
Do the math! Comprehensive inventory management solutions can produce huge advantages for those in the aerospace industry :
- Having the right parts in stock reduces aircraft on ground (AOG) incidences, and improves turnaround times. This leads to a higher customer satisfaction rating and additional revenue from repeat customers.
- Reducing excess stock frees up capital that can be put to better use growing the business.
- Forecasting can be improved making it simple to anticipate all types of demand patterns (including slow, lumpy and erratic).
- Automating day-to-day activities saves time and allows management by exception.
- By creating more predictability, warehouses become more efficient. Handling and transportation costs decrease.
- Cost reduction opportunities can be more easily identified.
- Value chain analysis improves.
- Overall profitability increases.

++++++++++++++++++++++++++++++++++++++++++++++++++++++++++++++++++++++++++
\
e- Bridge Warehouse


++++++++++++++++++++++++++++++++++++++++++++++++++++++++++++++++++++++++++
You made some decent factors there. I looked on the internet for the difficulty and found most individuals will associate with along with your website.
BalasHapusProcurement Management Software
Procurement Management System
e Procurement Management Software
Best Procurement Software
Procurement Software Companies
Thank you for this insightful post on past and present warehousing techniques. It’s fascinating to see how warehousing has evolved from manual processes to highly automated systems driven by technology. Your discussion on modern innovations like robotics and data analytics in warehousing highlights the significant strides the industry has made in improving efficiency and accuracy. I’d love to see more about the challenges businesses face when transitioning to advanced techniques and how they can overcome them. Great work!
BalasHapusEpicforce Tech