


Using Robotics In Pharmaceutical Manufacturing
Automation, including automated inspection and packaging, is becoming an increasingly important part of pharmaceutical manufacturing. The many benefits of automation include efficiency, saving workers from hazardous environments or repetitive tasks, reducing training overhead, eliminating human error, increasing repeatability and reproducibility, and in cleanrooms, removing the potential for human contamination.
A robotic system is a type of automation that has multiple axes of motion and can be programmed to perform a function. Robot types include articulated, cartesian (i.e., gantry), parallel (i.e., delta), and selective compliance assembly robot arm (SCARA). Common applications include "pick and place" operations that often use SCARA robots. There is also a new, growing use of delta-type robots for high-speed picking and packaging .
Merck, for example, is using a Fanuc delta robot on a bottling line to place dispenser caps onto bottled allergy medications. "Ten variants of the bottle can be run on the system, and the only robot line-change requirement is to select the appropriate program on the robot controller,"
"The advantages of robotics are fairly simple: greater speed and accuracy, greater flexibility and reliability than hard automation, and they are becoming ever more affordable .
Robots for filling, inspection, and packaging
Robotic technology is being used for vial-filling applications on slower speed applications. "Robotic vial manipulation transfers components from station to station both before and after filling and pack-off. The company also has experience with handling plastic and glass prefilled syringes in pre-process, buffering, and initial and end-of-line packaging. "Automated syringe assembly, inspection, and preparation for packaging is an ideal application for robotics. "The primary advantage in sterile environments is reduction of risk due to environmental contamination and contamination generated from human intervention during component transfer." In addition, productivity is increased because of the accuracy and efficiency of robots, which often perform at increased speeds and produce less scrap.
Robotic technology is being used for vial-filling applications on slower speed applications. "Robotic vial manipulation transfers components from station to station both before and after filling and pack-off. The company also has experience with handling plastic and glass prefilled syringes in pre-process, buffering, and initial and end-of-line packaging. "Automated syringe assembly, inspection, and preparation for packaging is an ideal application for robotics. "The primary advantage in sterile environments is reduction of risk due to environmental contamination and contamination generated from human intervention during component transfer." In addition, productivity is increased because of the accuracy and efficiency of robots, which often perform at increased speeds and produce less scrap.
Automatic inspection, as part of a robotic system, has the advantage of enabling 100% part inspection. Vision-sensing technology can be used in pharmaceutical packaging to verify serialization numbers for compliance with track-and-trace regulations. "Robotic dexterity and accuracy combined with current and future optical technology and serialization software is the ideal technology for an automated solution,"
An advance in vision sensors is color imaging, which, for example, allows systems to distinguish between bottle caps of different colors, noted PMMI in a trend report (3). Vision sensors have also led to advances in end-of-arm tooling design that improve the ability of robots to accurately identify and place objects.
Robots for producing personalized medicines
Custom automation and contract-manufacturing company Invetech recently partnered with biopharmaceutical company Argos Therapeutics to develop automated manufacturing systems based on Argos' Arcelis technology platform for personalized immunotherapies. "The Arcelis platform uses two, five-axis robotic arms in the production of the mRNA from a patient’s tumor, which is used as the antigen for loading into the dendritic cells produced in the cellular processing equipment. "The cellular equipment uses automation to manipulate the white blood cells throughout the manufacturing process to control their development and maturation into dendritic cells. These cells express the desired antigens, which when delivered to a patient, will trigger the patient’s immune system to produce killer T-cells that will target the metastatic tumors."
Custom automation and contract-manufacturing company Invetech recently partnered with biopharmaceutical company Argos Therapeutics to develop automated manufacturing systems based on Argos' Arcelis technology platform for personalized immunotherapies. "The Arcelis platform uses two, five-axis robotic arms in the production of the mRNA from a patient’s tumor, which is used as the antigen for loading into the dendritic cells produced in the cellular processing equipment. "The cellular equipment uses automation to manipulate the white blood cells throughout the manufacturing process to control their development and maturation into dendritic cells. These cells express the desired antigens, which when delivered to a patient, will trigger the patient’s immune system to produce killer T-cells that will target the metastatic tumors."
"The RNA robots manipulate closed disposables to perform the process within the common Class 100,000 cleanroom space . "The use of the closed disposables allows multiple patients' materials to be processed in the same manufacturing space, driving the facility capital and operating costs down significantly."
Argos' lead candidate is currently in Phase III clinical trials, and the automated technology is designed to be modular and easily scalable. Clinical processes are generally manual, skill-based processes that cannot operate practically or economically at commercial scale, notes Grant. Use of robotics, however, allows the processes to be scaled up commercially. "In addition, robotics allows new sites to be replicated around the world in a scale-out model, with minimum training for set-up and validation of new sites and minimal site-to-site variability in production processes .
Cleanroom robots
Robotic technology is ideal for cleanroom processes, such as aseptic filling, because it eliminates human contamination risk. Robotics can provide an ISO 5 environment to preclude the possibility of microbial ingress, says Langosch. ESS Technologies partners with Fanuc Robotics for secondary packaging and palletizing of pharmaceuticals, and Fanuc has several robots that will operate in an ISO 5 environment. The Fanuc M-430iA/2PV can withstand hydrogen peroxide vapor sterilization and has a waterproof rating; all wiring and cabling is routed through the robot’s hollow arm.
Robotic technology is ideal for cleanroom processes, such as aseptic filling, because it eliminates human contamination risk. Robotics can provide an ISO 5 environment to preclude the possibility of microbial ingress, says Langosch. ESS Technologies partners with Fanuc Robotics for secondary packaging and palletizing of pharmaceuticals, and Fanuc has several robots that will operate in an ISO 5 environment. The Fanuc M-430iA/2PV can withstand hydrogen peroxide vapor sterilization and has a waterproof rating; all wiring and cabling is routed through the robot’s hollow arm.
Robots designed for use in cleanrooms must minimize particulate generation to maintain cleanroom classifications, typically ISO Class 5 or 6. Cleanability, including minimizing crevices and ensuring the robot is resistant to cleaning and sterilizing agents, is also a requirement . Operator safety must be ensured by guarding or containing the robot. Another requirement is controlling the speed of robot movement to minimize impact on airflow and particle generation and to a lesser extent, managing heat generation and its impact on the heating, ventilation, and air-conditioning system of the cleanroom, explains Grant.
Robots in the laboratory
Robotics has come a long way in the pharmaceutical laboratory . Life Sciences manager at Precise Automation. In the laboratory, robots are used, for example, to transport microtiter plates between instruments. "Although the instruments can be loaded manually, a robot tied to a scheduling software system eliminates human error, maintains the quality of the experiment, and allows scientists to focus on the content of the experiment, instead of how they will execute it .
Robotics has come a long way in the pharmaceutical laboratory . Life Sciences manager at Precise Automation. In the laboratory, robots are used, for example, to transport microtiter plates between instruments. "Although the instruments can be loaded manually, a robot tied to a scheduling software system eliminates human error, maintains the quality of the experiment, and allows scientists to focus on the content of the experiment, instead of how they will execute it .
Laboratories differ from industrial applications in that, although tasks are repetitive, they are not as consistent and may change depending on the experiment . The need to access equipment near the robot quickly and the space limitations of a laboratory can be met with new collaborative robots that do not require safety guarding. In 2012, Precise Automation introduced a collaborative SCARA robot (or "cobot"), the PreciseFlex (PF)400, which handles less than 1-kg loads and is designed to allow operators to work safely next to the robot without barriers. The smaller footprint of the robot reduces cost, and the space savings is useful in benchtop laboratory applications. The robot is user friendly, and the Precise Guidance Controller inside the PF400 allows laboratory personnel to "teach" the robot using only their hands. "Because there are no barriers, instead of using a complex remote-control pendant to teach the robot, the operator can show the robot what to do by simply grasping the end of the robot arm. This accessibility is unheard of in industrial automation .
Other laboratory applications for robots include vial handling. A Fanuc robot is being used in a laboratory, for example, as a single-point handling solution for vial processing. "A handling tool was designed and attached to the end of the robot to enable it to handle ten vials at a time. A variety of components were also placed around the robot cell—including indexing tables for full rack staging, a thermostatically controlled water bath for precise sample temperature, a retrieval system for dumped vials, a washing-brushing-rinsing-drying station, a preservative spray station, and a recapping station .
In the laboratory and on the manufacturing floor, robots are increasingly used to improve quality and efficiency.
XO___XO Industrial robots in the electronics industry
Integrating robotics into electronics applications is amongst the most rewarding tasks that we face at TM Robotics. Toshiba Machine’s fast, accurate and high repeatability robots are ideal for tasks such as PCB manufacture, mobile phone assembly and hard disc production as well as other pick and place functions in electronics applications. Normally, the reason our electronics industry customers give for automating is a desire to bring down costs and compete with cheaper manufacturing economies. They are looking for the future of manufacturing in the electronics industry.
For instance, Toshiba Machine’s TH350 SCARA (Selectively Compliant Articulated Robot Arm) was the logical choice when an Irish manufacturer of MCBs (Miniature Circuit Breakers) needed to replace an existing pneumatic pick and place machine. After changes to the manufacturing process, the existing equipment was not able to perform the required task in the necessary cycle time.
With the help of a local TM Robotics’ system integrator, the TH350 was installed and now easily meets its targets.
There were two principal reasons why the TH350 was chosen. Firstly, the production line manufactures MCBs at a rate of 24 a minute, so exceptional repeatable accuracy was required for this high-speed assembly task. The TH350 is both fast and accurate – it offers repeatability and positioning to ±0.01mm and a completion time of 2.9m/s.
Size was the second important factor. The TH350 was ideal, as it is both compact and powerful, offering a 3kg maximum payload. With an arm length of 350mm and minimal footprint and head clearance, the robot’s compact design allowed the engineers to locate it inside one of the workstations on an existing automatic assembly machine. Furthermore, the TH350 is extremely flexible and offers movement of ±115º and ±145º on axes one and two respectively. The installation created very little downtime; all it took was a long weekend during which the robot was interfaced, through the robot controller, to the existing line equipment.
Small, fast and easy robots for the electronics industry
This is just one example of the way Toshiba Machine and TM Robotics have responded to fears over the ease of use of industrial robots by making our own machines ever simpler to use, install and program. We have also proactively addressed the overall needs of electronics manufacture by producing smaller, more accurate and faster robots, such as our TH180, TH250T and TH350T SCARAs. We have also taken measures such as the introduction of clean room options, essential for high level electronics work, and ceiling mount models, saving valuable floor space on the production line. We have lived by the motto, smaller, faster and easier.
A literal manifestation of this maxim is the TM Robotics-developed portable SCARA starter pack. The pack can be set up in under fifteen minutes and is sufficiently easy to use that a technician will be able to write and run a programme after only an hour of tuition. It contains a TH180 mini SCARA robot, which features an arm length of 180mm, a payload of 2kg and repeatability of ±0.01mm. The robot is ideal for use in cleanroom work or electronics manufacture and as a display tool acts as a representative of the entire Toshiba Machine range. Also included is a TS1000 controller, which offers four axis simultaneous control, absolute encoders and can be programmed in SCOL, a language similar to BASIC. The unit comes complete with a teach pendant, for easy control access, and either pneumatic or electric grippers and a number of safety cubes for use in sample applications. The entire starter pack and the specially designed work cell can fit inside two carry cases, making it extremely portable. We see the starter pack as the perfect antidote to the belief that industrial robots need to be complicated.
Easy to install automation for the electronics industry
It may well be that the best answer the European electronics industry can give to the cheaper labour costs offered in other parts of the world is this kind of easy to install automation. Not long ago I visited a factory which, as I first approached and spotted its blacked out windows, I thought was unoccupied. Thinking that what I was looking at was another empty plant; dismantled thanks to uncompetitive labour costs, I was surprised to realise that the plant was completely automated, with no human operatives at all. It occurred to me that I was looking at the most profitable future for the UK electronics industry.
Pharma Primed for Automation Investments
Despite more regulations, more global competition, more pricing pressure, more acquisitions and the need for more precision medicines—all of which could be considered obstacles to growth—the U.S. pharmaceutical market is poised for a technology transition that will aid future business.
Specifically, as the industry experiences a shift away from high-volume blockbuster drugs to more targeted and affordable treatments, there will be a manufacturing move to smaller batch runs, serialization and increasing SKUs. Collectively, these things are driving new investments in automation, according to the latest Business Intelligence report from PMMI, The Association for Packaging and Processing Technologies.
The PMMI report, titled Pharmaceutical & Medical Devices: Trends and Opportunities in Packaging Operations, reflects market conditions for the latter part of 2016. It includes feedback from 60 industry professionals from pharma, medical device and contract services companies, with about half of the respondents representing large (over $500 million) organizations.
A big takeaway from the report: Nearly half of the healthcare manufacturers interviewed continue to replace legacy equipment and buy new equipment, while two-thirds of participating companies predict spending even more on capital equipment in the next 12 to 24 months.
“Legacy equipment is a problem and causes line shutdowns at times,” said one respondent, a process engineer at a pharmaceutical company. “We continuously reinvest in equipment and look for more automation and flexibility for shorter runs.”
Operational improvements are driving new technology purchases. The top five motivators are:
- Expanding the use of automation and integration.
- Increasing throughput and advances in manufacturing processes.
- Measuring overall equipment effectiveness (OEE).
- Greater versatility during changeover due to increasing SKUs.
- Installing more robotics.
To that end, the technologies that pharma companies seem most focused on include data management, serialization and robotics.
First, the Industrial Internet of Things (IIoT) is requiring more data collection capabilities throughout manufacturing and packaging, and with that comes the need to manage and analyze the data.
Second, meeting regulatory tracking compliance in the year ahead is top of mind, which is why serialization is important. It also plays a part in anti-counterfeiting tactics. So, beyond serialized coding, companies are looking further into 2D barcodes, RFID, smart labels, water marks and holograms for track and trace capabilities.
But companies are struggling with the costs associated with meeting regulations and setting up the internal infrastructure for data collection. What they aren’t struggling so much with is where robotics factor in to the process.
Robots are a key investment moving forward, according to the report, with the majority of companies already using robotics in packaging and over 50 percent planning to install more robots in the future.
Most of the robots are being used in downstream packaging, but 12 percent of the companies expect to increase the use of robotics upstream for assembly, processing and depalletization of incoming materials. Manual procedures will still exist for some applications such as hand-filled tubes, diagnostics and custom work. But the emphasis on adding more robots into packaging is a way to increase overall productivity and worker safety.
“Robotics will continue to be used to improve product quality, reduce bottlenecks and alleviate repetitive tasks,” said a plant engineer from a contract development and manufacturing organization (CDMO).
Industrial robots are on the verge of revolutionizing manufacturing.
As they become smarter, faster and cheaper, they’re being called upon to do more. They’re taking on more “human” capabilities and traits such as sensing, dexterity, memory and trainability. As a result, they’re taking on more jobs - such as picking and packaging, testing or inspecting products, or assembling minute electronics. Also, a new generation of “collaborative” robots ushers in an era of shepherding robots out of their cages and literally hand-in-hand with human workers who train them through physical demonstration. Especially for small and mid-sized manufacturers, a question is arising sooner than most probably expected: “If prices keep declining and capabilities of robotic technologies keep expanding, is now the time to hire some automated help?” Indeed, many have already answered this question. According a PwC survey of manufacturers, 59% of are already currently using some sort of robotics technology.
Automation, robotics, and the factory of the future
industrial robots produce industrial robots, supervised by a staff of only four workers per shift. In a Philips plant producing electric razors in the Netherlands, robots outnumber the nine production workers by more than 14 to 1. Camera maker Canon began phasing out human labor at several of its factories in 2013.
This “lights out” production concept—where manufacturing activities and material flows are handled entirely automatically—is becoming an increasingly common attribute of modern manufacturing. In part, the new wave of automation will be driven by the same things that first brought robotics and automation into the workplace: to free human workers from dirty, dull, or dangerous jobs; to improve quality by eliminating errors and reducing variability; and to cut manufacturing costs by replacing increasingly expensive people with ever-cheaper machines. Today’s most advanced automation systems have additional capabilities, however, enabling their use in environments that have not been suitable for automation up to now and allowing the capture of entirely new sources of value in manufacturing.
Falling robot prices
As robot production has increased, costs have gone down. Over the past 30 years, the average robot price has fallen by half in real terms, and even further relative to labor costs (Exhibit 1). As demand from emerging economies encourages the production of robots to shift to lower-cost regions, they are likely to become cheaper still.
Exhibit 1
Accessible talent
People with the skills required to design, install, operate, and maintain robotic production systems are becoming more widely available, too. Robotics engineers were once rare and expensive specialists. Today, these subjects are widely taught in schools and colleges around the world, either in dedicated courses or as part of more general education on manufacturing technologies or engineering design for manufacture. The availability of software, such as simulation packages and offline programming systems that can test robotic applications, has reduced engineering time and risk. It’s also made the task of programming robots easier and cheaper.
Ease of integration
Advances in computing power, software-development techniques, and networking technologies have made assembling, installing, and maintaining robots faster and less costly than before. For example, while sensors and actuators once had to be individually connected to robot controllers with dedicated wiring through terminal racks, connectors, and junction boxes, they now use plug-and-play technologies in which components can be connected using simpler network wiring. The components will identify themselves automatically to the control system, greatly reducing setup time. These sensors and actuators can also monitor themselves and report their status to the control system, to aid process control and collect data for maintenance, and for continuous improvement and troubleshooting purposes. Other standards and network technologies make it similarly straightforward to link robots to wider production systems.
New capabilities
Robots are getting smarter, too. Where early robots blindly followed the same path, and later iterations used lasers or vision systems to detect the orientation of parts and materials, the latest generations of robots can integrate information from multiple sensors and adapt their movements in real time. This allows them, for example, to use force feedback to mimic the skill of a craftsman in grinding, deburring, or polishing applications. They can also make use of more powerful computer technology and big data–style analysis. For instance, they can use spectral analysis to check the quality of a weld as it is being made, dramatically reducing the amount of postmanufacture inspection required.
Robots take on new roles
Today, these factors are helping to boost robot adoption in the kinds of application they already excel at today: repetitive, high-volume production activities. As the cost and complexity of automating tasks with robots goes down, it is likely that the kinds of companies already using robots will use even more of them. In the next five to ten years, however, we expect a more fundamental change in the kinds of tasks for which robots become both technically and economically viable (Exhibit 2). Here are some examples.
Exhibit 2
Low-volume production
The inherent flexibility of a device that can be programmed quickly and easily will greatly reduce the number of times a robot needs to repeat a given task to justify the cost of buying and commissioning it. This will lower the threshold of volume and make robots an economical choice for niche tasks, where annual volumes are measured in the tens or hundreds rather than in the thousands or hundreds of thousands. It will also make them viable for companies working with small batch sizes and significant product variety. For example, flex track products now used in aerospace can “crawl” on a fuselage using vision to direct their work. The cost savings offered by this kind of low-volume automation will benefit many different kinds of organizations: small companies will be able to access robot technology for the first time, and larger ones could increase the variety of their product offerings.
Emerging technologies are likely to simplify robot programming even further. While it is already common to teach robots by leading them through a series of movements, for example, rapidly improving voice-recognition technology means it may soon be possible to give them verbal instructions, too.
Highly variable tasks
Advances in artificial intelligence and sensor technologies will allow robots to cope with a far greater degree of task-to-task variability. The ability to adapt their actions in response to changes in their environment will create opportunities for automation in areas such as the processing of agricultural products, where there is significant part-to-part variability. In Japan, trials have already demonstrated that robots can cut the time required to harvest strawberries by up to 40 percent, using a stereoscopic imaging system to identify the location of fruit and evaluate its ripeness.
These same capabilities will also drive quality improvements in all sectors. Robots will be able to compensate for potential quality issues during manufacturing. Examples here include altering the force used to assemble two parts based on the dimensional differences between them, or selecting and combining different sized components to achieve the right final dimensions.
Robot-generated data, and the advanced analysis techniques to make better use of them, will also be useful in understanding the underlying drivers of quality. If higher-than-normal torque requirements during assembly turn out to be associated with premature product failures in the field, for example, manufacturing processes can be adapted to detect and fix such issues during production.
Complex tasks
While today’s general-purpose robots can control their movement to within 0.10 millimeters, some current configurations of robots have repeatable accuracy of 0.02 millimeters. Future generations are likely to offer even higher levels of precision. Such capabilities will allow them to participate in increasingly delicate tasks, such as threading needles or assembling highly sophisticated electronic devices. Robots are also becoming better coordinated, with the availability of controllers that can simultaneously drive dozens of axes, allowing multiple robots to work together on the same task.
Finally, advanced sensor technologies, and the computer power needed to analyze the data from those sensors, will allow robots to take on tasks like cutting gemstones that previously required highly skilled craftspeople. The same technologies may even permit activities that cannot be done at all today: for example, adjusting the thickness or composition of coatings in real time as they are applied to compensate for deviations in the underlying material, or “painting” electronic circuits on the surface of structures.
Working alongside people
Companies will also have far more freedom to decide which tasks to automate with robots and which to conduct manually. Advanced safety systems mean robots can take up new positions next to their human colleagues. If sensors indicate the risk of a collision with an operator, the robot will automatically slow down or alter its path to avoid it. This technology permits the use of robots for individual tasks on otherwise manual assembly lines. And the removal of safety fences and interlocks mean lower costs—a boon for smaller companies. The ability to put robots and people side by side and to reallocate tasks between them also helps productivity, since it allows companies to rebalance production lines as demand fluctuates.
Robots that can operate safely in proximity to people will also pave the way for applications away from the tightly controlled environment of the factory floor. Internet retailers and logistics companies are already adopting forms of robotic automation in their warehouses. Imagine the productivity benefits available to a parcel courier, though, if an onboard robot could presort packages in the delivery vehicle between drops.
Agile production systems
Automation systems are becoming increasingly flexible and intelligent, adapting their behavior automatically to maximize output or minimize cost per unit. Expert systems used in beverage filling and packing lines can automatically adjust the speed of the whole production line to suit whichever activity is the critical constraint for a given batch. In automotive production, expert systems can automatically make tiny adjustments in line speed to improve the overall balance of individual lines and maximize the effectiveness of the whole manufacturing system.
While the vast majority of robots in use today still operate in high-speed, high-volume production applications, the most advanced systems can make adjustments on the fly, switching seamlessly between product types without the need to stop the line to change programs or reconfigure tooling. Many current and emerging production technologies, from computerized-numerical-control (CNC) cutting to 3-D printing, allow component geometry to be adjusted without any need for tool changes, making it possible to produce in batch sizes of one. One manufacturer of industrial components, for example, uses real-time communication from radio-frequency identification (RFID) tags to adjust components’ shapes to suit the requirements of different models.
The replacement of fixed conveyor systems with automated guided vehicles (AGVs) even lets plants reconfigure the flow of products and components seamlessly between different workstations, allowing manufacturing sequences with entirely different process steps to be completed in a fully automated fashion. This kind of flexibility delivers a host of benefits: facilitating shorter lead times and a tighter link between supply and demand, accelerating new product introduction, and simplifying the manufacture of highly customized products.
Making the right automation decisions
With so much technological potential at their fingertips, how do companies decide on the best automation strategy? It can be all too easy to get carried away with automation for its own sake, but the result of this approach is almost always projects that cost too much, take too long to implement, and fail to deliver against their business objectives.
A successful automation strategy requires good decisions on multiple levels. Companies must choose which activities to automate, what level of automation to use (from simple programmable-logic controllers to highly sophisticated robots guided by sensors and smart adaptive algorithms), and which technologies to adopt. At each of these levels, companies should ensure that their plans meet the following criteria.
Automation strategy must align with business and operations strategy. As we have noted above, automation can achieve four key objectives: improving worker safety, reducing costs, improving quality, and increasing flexibility. Done well, automation may deliver improvements in all these areas, but the balance of benefits may vary with different technologies and approaches. The right balance for any organization will depend on its overall operations strategy and its business goals.
Automation programs must start with a clear articulation of the problem. It’s also important that this includes the reasons automation is the right solution. Every project should be able to identify where and how automation can offer improvements and show how these improvements link to the company’s overall strategy.
Automation must show a clear return on investment. Companies, especially large ones, should take care not to overspecify, overcomplicate, or overspend on their automation investments. Choosing the right level of complexity to meet current and foreseeable future needs requires a deep understanding of the organization’s processes and manufacturing systems.
Platforming and integration
Companies face increasing pressure to maximize the return on their capital investments and to reduce the time required to take new products from design to full-scale production. Building automation systems that are suitable only for a single line of products runs counter to both those aims, requiring repeated, lengthy, and expensive cycles of equipment design, procurement, and commissioning. A better approach is the use of production systems, cells, lines, and factories that can be easily modified and adapted.
Just as platforming and modularization strategies have simplified and reduced the cost of managing complex product portfolios, so a platform approach will become increasingly important for manufacturers seeking to maximize flexibility and economies of scale in their automation strategies.
Process platforms, such as a robot arm equipped with a weld gun, power supply, and control electronics, can be standardized, applied, and reused in multiple applications, simplifying programming, maintenance, and product support.
Automation systems will also need to be highly integrated into the organization’s other systems. That integration starts with communication between machines on the factory floor, something that is made more straightforward by modern industrial-networking technologies. But it should also extend into the wider organization. Direct integration with computer-aided design, computer-integrated engineering, and enterprise-resource-planning systems will accelerate the design and deployment of new manufacturing configurations and allow flexible systems to respond in near real time to changes in demand or material availability. Data on process variables and manufacturing performance flowing the other way will be recorded for quality-assurance purposes and used to inform design improvements and future product generations.
Integration will also extend beyond the walls of the plant. Companies won’t just require close collaboration and seamless exchange of information with customers and suppliers; they will also need to build such relationships with the manufacturers of processing equipment, who will increasingly hold much of the know-how and intellectual property required to make automation systems perform optimally. The technology required to permit this integration is becoming increasingly accessible, thanks to the availability of open architectures and networking protocols, but changes in culture, management processes, and mind-sets will be needed in order to balance the costs, benefits, and risks.
Cheaper, smarter, and more adaptable automation systems are already transforming manufacturing in a host of different ways. While the technology will become more straightforward to implement, the business decisions will not. To capture the full value of the opportunities presented by these new systems, companies will need to take a holistic and systematic approach, aligning their automation strategy closely with the current and future needs of the business.

Outstanding solution for the pharmaceutical industry
Filling and closing syringes
A-Pack Technologies SA has in its range an outstanding solution for filling and closing syringes: the 535. This innovative system includes a Stäubli Cleanroom robot TX60 CR and achieves maximum output of up to 4000 syringes per hour.
A-Pack Technologies is a company in the Bausch Advanced Technology Group which is made up of separate companies in Switzerland, Germany, the USA and Brazil. With over 20 years in the design and manufacture of machines for the pharmaceutical industry, the group has acquired a wealth of experience. It offers solutions for complete pharmaceutical packaging lines to process syringes, carpoules, vials, bottles, ampoules and IV bags.
The company is setting process standards for dosing and closing syringes and similar objects with its 535 machine. It is intended to be used for any application involving the automation and/or validation of filling procedures. The manufacturer chose a design conducive to laminar flow and high-quality stainless steel for its machine, plus a fast and accurate six-axis TX60 CR robot from Stäubli.
Solution
Robots contribute flexibility to any process
At A-Pack Technologies, it is hoped that the use of a robot will result in a significantly more flexible standard system: “We are increasing the options offered by our standard machine substantially with the robot. The TX60 Cleanroom robot contributes a great deal of flexibility to the handling, dosing and closing processes. Thanks to the robot, it is also possible to integrate additional tasks in the cell. All in all, we are able to process a much wider range of products on the system, with enhanced work content if necessary,” said Jean-Luc Muller, CEO at A-Pack Technologies.
However, maximizing the flexibility of the system on its own is not sufficient to meet the requirements of the customers in the pharmaceutical industry completely. The productivity of the systems is also important. In this respect, the bar is constantly being set higher. With around 4000 syringes per hour, the output of the dosing and closing machine is top-class.
Customer benefits
Short cycle times with maximum process reliability
Cycle times of less than a second can only be achieved with innovative system and processing technology and with very fast and highly accurate robots. The Stäubli TX60 CR was designed for precisely these situations. The highly rigid, encapsulated mechanical structure and the compact direct-drive JCM geared motors, developed in-house by Stäubli, permit extremely fast acceleration in every axis.
The system is designed throughout for high output with maximum process reliability with an eye to impressive innovation and attention to detail. The TX60 CR automatically fills and closes syringes quickly, accurately and reliably, even under cleanroom conditions. It is equipped with a pioneering gripper system designed with the benefit of long term experience. One essential feature is that it is used simultaneously for filling and closing the syringes, drastically reducing the system’s cycle times.
Safety with accurate dosing
Accurate dosing of medication plays an essential part in filling the syringes. To ensure a precise dose, the machine has a valve-free dosing unit which achieves filling accuracy of up to ± 0.05 %. To prevent contamination and the formation of bubbles, filling and closing takes place in a vacuum. Thanks to its performance the 535 is setting standards in automatic filling and closing of syringes.
Jean-Luc Muller sums up why the company chose Stäubli robots: “We endeavor not only to fulfill the expectations of our customers in the pharmaceutical industry, but to surpass them. We achieve this with fast, economical and reliable systems in which we use only the best components available on the market. Stäubli was chosen to supply the robots, because in terms of cleanroom suitability, precision, speed and reliability, Stäubli robots are state-of-the-art in pharmaceutical and medical technology.
Electronic skins for soft, compact, reversible assembly of wirelessly activated fully soft robots
Designing softness into robots holds great potential for augmenting robotic compliance in dynamic, unstructured environments. However, despite the body’s softness, existing models mostly carry inherent hardness in their driving parts, such as pressure-regulating components and rigid circuit boards. This compliance gap can frequently interfere with the robot motion and makes soft robotic design dependent on rigid assembly of each robot component. We present a skin-like electronic system that enables a class of wirelessly activated fully soft robots whose driving part can be softly, compactly, and reversibly assembled. The proposed system consists of two-part electronic skins (e-skins) that are designed to perform wireless communication of the robot control signal, namely, “wireless inter-skin communication,” for untethered, reversible assembly of driving capability. The physical design of each e-skin features minimized inherent hardness in terms of thickness (<1 millimeter), weight (~0.8 gram), and fragmented circuit configuration. The developed e-skin pair can be softly integrated into separate soft body frames (robot and human), wirelessly interact with each other, and then activate and control the robot. The e-skin–integrated robotic design is highly compact and shows that the embedded e-skin can equally share the fine soft motions of the robot frame. Our results also highlight the effectiveness of the wireless inter-skin communication in providing universality for robotic actuation based on reversible assembly.
Robotics is a disruptive technology that is playing an increasingly important role in the manufacturing industry. We have the right environment – an ideal blend of industrial and consumer markets, supply chain clusters, and academia and research institutions – for robotics and automation companies to flourish.
++++++++++++++++++++++++++++++++++++++++++++++++++++++++++++++++++++++
e - Pharmaceuticals + e- Robotics = e - Manufacturing + e - Works system

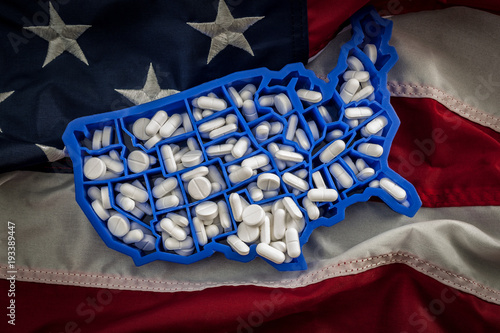
electronics vision and automation of industries:
- health sciences
- energy
- transportation
- mining
- industrial
- consumer
- food and beverage
- pulp and paper
- oil and gas
- chemical
- electronics Learn + Gain + Control
- telecommunications
+++++++++++++++++++++++++++++++++++++++++++++++++++++++++++++++++++++++++++++
This is truly a very good post. Precimotion is the best solution for Cobot in delhi. Our engineering facilities are state-of-the-art and our team of professionals is in demand for their capability to existing gears and gearboxes for diverse applications and other services such as Servo planetary, Strainwave gearboxes, Six axis, Pick & place robots, AGV.
BalasHapusCobot in delhi